Early at the beginning of the year, Dr Johannes Homa told 3D ADEPT Media that we could expect the company to launch a new 3D printer in addition to the LCM technology. For us here at 3D ADEPT Media, it was just a matter of time before the reveal happens. And here we are, 6 months later, we are about to give you the most important details of this new family member in the Austrian machine manufacturer’s portfolio.
Named CeraMax Vario V900 3D printer, the new ceramic 3D printer features a build envelope of up to 250 x 250 x 290 mm, and can apply up to 1.000 µm slurry per layer in less than a minute. It has been designed for the production of large ceramic parts with thick walls and full densities using oxide and non-oxide ceramics. (If you need a fresh reminder about the capabilities of oxide and non-oxide ceramics in AM, I would recommend you check this article on the key factors to consider when exploring technical ceramics in (medical) 3D printing applications.)
In addition to the aforementioned two main groups of materials, the Austrian expert in ceramic 3D printing has also added to the 3D printer the capability to process dark ceramics such as silicon carbide (SiC). Acknowledged as one of the most important advanced ceramics in contemporary usage, those black, high-strength materials deliver higher hardness and better thermal shock resistance than alumina.
The ability to process SiC marks a new chapter in the AM industry, which has never experienced applications with this material. Yet, the superior properties of dark ceramics are ideal production features to achieve power devices and do marvels in the power electronics industry. If you’ve used SiC before, then you probably know that in traditional manufacturing processes, processing SiC to manufacture products often requires batches of sand (SiO2 or silicon dioxide) and carbon to be heated and to react in an electric furnace. But that’s now a thing of the past.
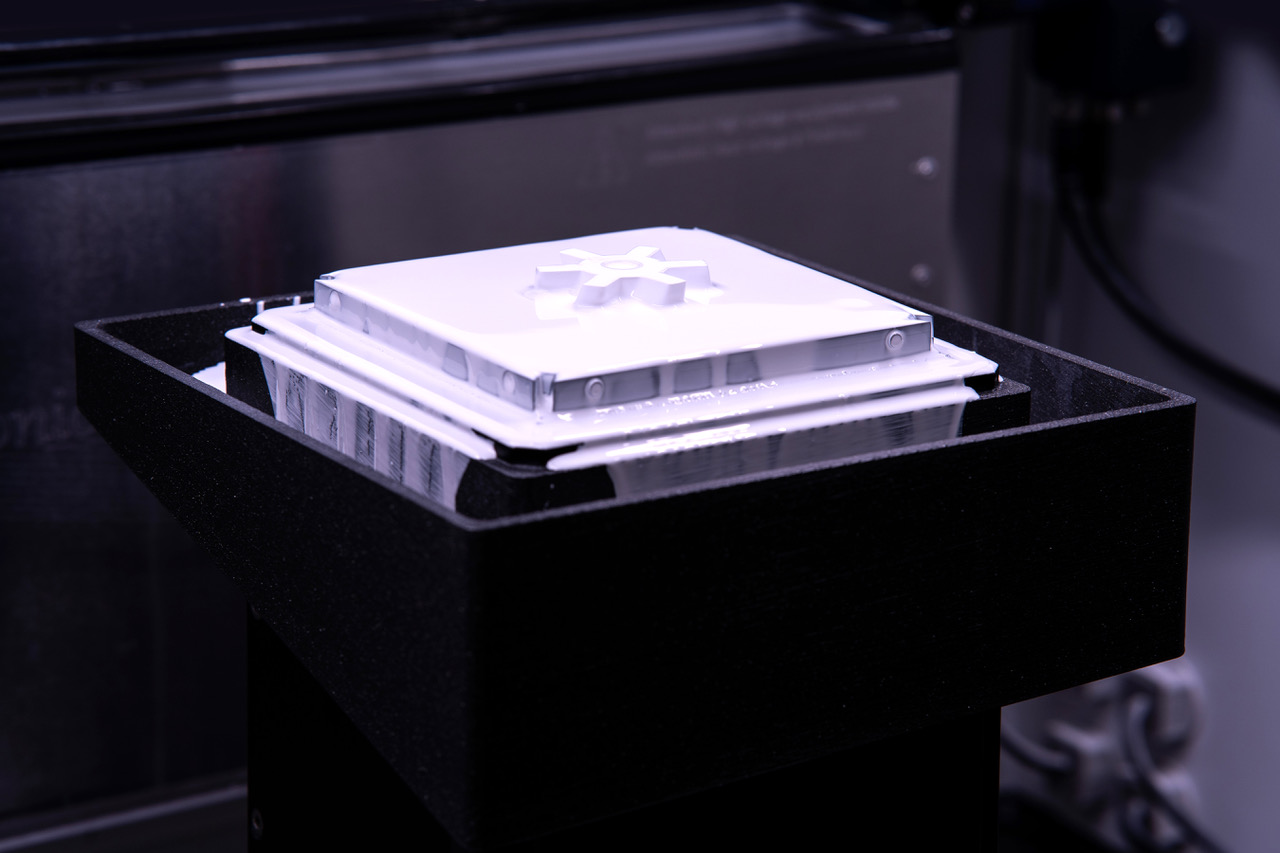
With an innovative Laser-Induced Slipcasting (LIS) technology, the CeraMax Vario V900 fabricates parts using industrial water-based suspensions with very low organic binder contents. Lithoz assures that the debinding process has been simplified to enable wall thicknesses that we previously did not see in other ceramic 3D printing solutions.
Green parts printed with the CeraMax Vario V900 are machineable without any restrictions, meaning they can therefore be easily reintroduced into the traditional ceramic process chain. This water-based slurry solution completely absorbs the laser beam. Due to treatment being purely heat-induced, even dark ceramics such as silicon carbide can be processed without issues or loss of desired properties, we learn.
The best part of this new machine is certainly the database-supported storage and management of all process data, which enables seamless documentation of print jobs. Obviously, optional software upgrades allow for even better parameter control or adjustment, as well as the structuring of your production data and the possibility of real-time process monitoring via remote video transmission.
Apart from the build envelope and layer thicknesses, other technical specifications of CeraMax Vario V900 include:
- Precision optics: F-Theta lens and high-speed scanner
- Light source: CO2 Laser
- CO2 Laser Spot Diameter (1/E2) ca. 0.5mm
- Scanning speed: up to 8m/s, flexibly adjustable to part design
- Dimensions (L x W x H): 1.85 x 0.95 x 2.20m
- IIoT & Industry 4.0 ready
LIS technology seems to be the ideal production candidate for anyone looking to explore ceramic 3D printing for the first time. Indeed, as per the words of Lithoz, it perfectly combines the full 3D design flexibility plus a considerably accelerated ceramic shaping process with economical water-based suspensions which stay very close to familiar standard slurries.
At Ceramitec – one of the events supported by 3D ADEPT Media –, the company will showcase some 3D printed parts that demonstrate the CeraMax Vario V900’s potential. While I look forward to seeing the machine and the parts in person, I do not doubt that these features and capabilities are the first step that enables any ceramic producer to envision what’s possible to achieve with “𝐓𝐡𝐞 𝐋𝐢𝐭𝐡𝐨𝐳 𝐖𝐚𝐲 𝐨𝐟 𝐁𝐈𝐆”.
Remember, you can post job opportunities in the AM Industry on 3D ADEPT Media free of charge or look for a job via our job board. Make sure to follow us on our social networks and subscribe to our weekly newsletter : Facebook, Twitter, LinkedIn & Instagram ! If you want to be featured in the next issue of our digital magazine or if you hear a story that needs to be heard, make sure you send it to contact@3dadept.com