One thing fans of Star Wars and fans of laser games would likely agree with, is that lasers are super cool. Why? You could ask. Because of speed. More lasers mean more agility and more speed. In the AM industry, the possibility to have more lasers in an industrial 3D printer also seems cool to a bunch of users. But, does it necessarily mean more agility and more speed?
Whether they are 2, 4 or 12, lasers remain the most effective energy source in a 3D printer since they can transfer a large amount of energy into micro-scale focal region instantaneously to solidify or cure materials in air, therefore enabling high-precision and high-throughput manufacturing for a wide range of materials. As AM increasingly embraces (mass) production, part manufacturers are eyeing the integration of multiple lasers within a 3D printer with great interest. To facilitate their decision-making process, it’s important to understand why and how multi-laser AM machines make sense.
While the focus is usually (and will be) made on powder-bed fusion processes (as part of this dossier), it should be noted that AM processes that are based on SLS, DED (Directed Energy Deposition) and VAT photopolymerisation can also be equipped with multiple lasers.
“In polymer AM there is selective laser sintering (SLS) that is also available with more than one laser source. There are some stereolithography machines with multiple lasers as well, however the required energy density for photopolymerization is low, so there are other methods that expose more than one area at a time”, Dr. Ing. Dominik Schmid, Sr. Engineer, at Kennametal comments.
According to Kartik Rao, Strategic Marketing Director at Additive Industries, the industry that probably shows us a path where we are going to head down is the laser cladding industry. “There are a lot of people that work with laser cladding in the oil and gas industries; so, they take big, long shafts and they are cladding the whole thing in wear-resistant materials with multiple robots working on a part. Ultimately, that’s probably where AM is headed”.
While each of the aforementioned technologies uses different types of laser and laser power and requires different beam sizes on the build plate, the ultimate goal for part producers is the same: enhance productivity while eventually reducing the cost per part. Here is the thing, a number of technical challenges may arise when working with multiple lasers in a powder-bed fusion process.
When does “more” mean “better”?
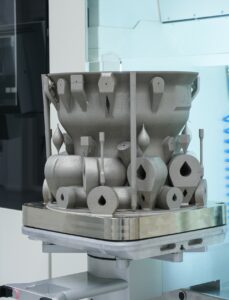
First of all, if you are looking to support R&D efforts or achieve prototypes, a single-laser 3D printer might remain your best option.
However, if you are looking to enhance the throughput of your 3D printer, or lower cost per part, there is a great chance that exploring multi-laser 3D printers is a great idea. For others, it often comes down to answering a couple of questions: how many parts can we achieve within a single batch – at one time? How large can a part be in the build envelope?
“Multi-laser systems have a higher build rate meaning the production capacity is higher compared to single-laser systems. On the other hand, they are more expensive than single laser systems. So, it is important to make usage of that additional capacity the systems provide. In short, the most vital factor in whether it makes sense to use multi laser systems is the demand for additive products”, Kennametal’s expert points out.
Emphasizing on the technical reasons why it makes sense to use multiple lasers in powder-bed fusion processes, Additive Industries’ speaker notes:
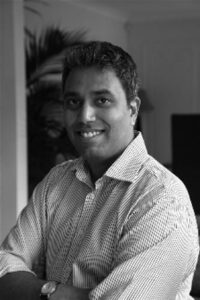
“In the powder-bed area, it makes more sense to have multiple lasers because ultimately, you want as much of the powder bed to be active as possible. The cost of the part may be a reason worth considering as well as the size of the parts you will be able to build. Very large parts for instance may require to have multiple lasers working on them, otherwise it may take up to 30 days to build, which is clearly a very long time and it will not be scalable for your business. It also makes sense if you have smaller parts on a large build tray.”
Rao’s example on large parts comes from the fact that, in powder-bed fusion processes with multiple lasers, lasers are spatially separate to expand coverage or to enable the lasers to reach a larger area.
On another note, even if productivity is advocated, quality should also be part of the equation and that’s something that can be challenging when one is aware of the implications surrounding material properties, build strategies and other laser parameters relevant to additive manufacturing.
Laser parameters relevant to multi-laser AM systems
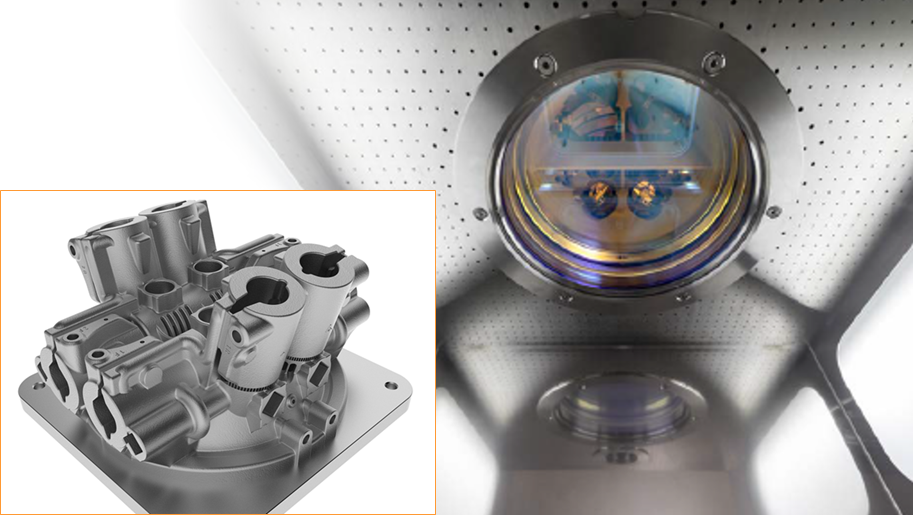
It’s legitimate to question the material properties of parts achieved with multi-laser AM systems – with the hope that they have the same properties achieved with single-laser systems. Most of the time, you might hear that multi-laser AM systems can achieve the same homogenous material properties in areas of the part as the ones delivered by single-laser AM systems. However, a couple of items that are inter-dependent should be considered.
Schmid explains that the scale with more laser sources is not linear. “A machine with four lasers might only be three times as fast as a single laser machine because the recoating time basically remains the same. Whether it is possible to reduce manufacturing costs with multi-laser systems depends on the specific application as well as the required investment in the machines themselves. Multi-laser manufacturing brings additional challenges, such as laser alignment or more complex design of the inert gas flow, so the ideal result is when quality can be achieved equal to a single laser machine”, he outlines.
Rao completes this explanation by laying emphasis on the fact that, more lasers necessarily do not necessarily mean faster production or quality production. As a matter of fact, shops should take into account a number of issues that are likely to occur with multi-laser AM systems – quality issues caused by:
- zoning/stitching of parts
- interaction of lasers with condensate from another active laser
- gas flow (heat management and waste removal)
- calibration of lasers (absolute and relative)
Producing with multiple lasers can often lead to lots of spatter which is important to handle effectively. Indeed, when there is not enough space between several lasers, they might “stitch” on the part, thus giving unpredictable results. To address this issue, some machine manufacturers have developed systems with reasonable overlap coverage. This enables operators to assign lasers to build individual parts.
Furthermore, the relative position of lasers with regard to the gas flow is pivotal, governed by laser assignment choices made during build preparation. Needless to say that gas flow configurations vary from one machine to another.
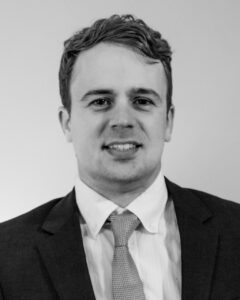
“In most cases some sort of attribution of the lasers to the parts has to be done by the operator. This means if you have multiple pieces on the build plate you need to assign which laser should work on which part. Because multi-laser machines are more expensive and build times are shorter, the scheduling of builds and planning of shifts becomes even more important to minimize unproductive time and maximize productivity and efficiency.”, Kennametal’s representative comments. Speaking of gas flow and thermal stability consideration, he adds: “When using more than one laser simultaneously, the fumes from one process zone should not interfere with the laser beam(s) active in another area. This needs to be resolved by the inert gas flow direction in combination with timing and local attribution of lasers. At the same time multiple lasers bring more energy and thus heat to the building chamber. A part of that heat goes into the gas flow, the other into the machine frame. This has to be taken into account at the machine design. The powder management is virtually independent of the number of lasers sources/optics.”
So, how do you determine your build strategy?
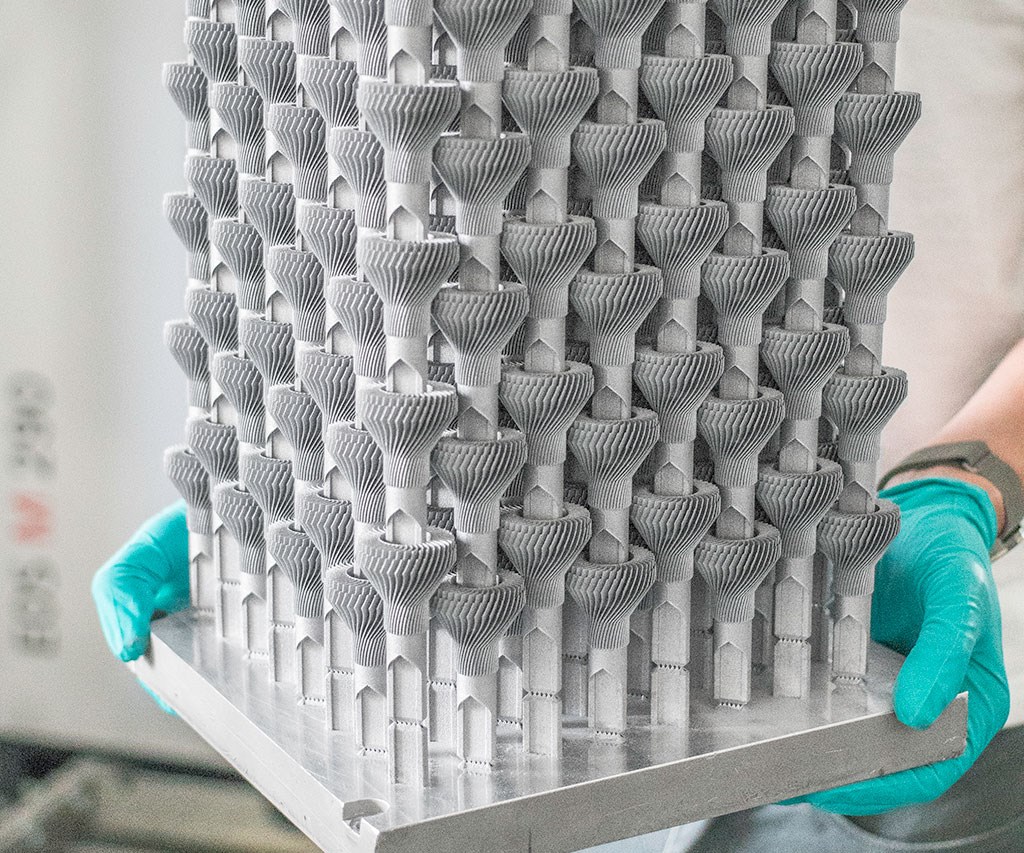
While manufacturers often use multiple lasers, either to build simultaneously a single component or to build individual parts with each laser, they should assess the turnaround time on the 3D printer, “as the goal remains to maximize laser utilization”, Rao highlights.
“What’s the point of having more than four lasers if you only take advantage of one or two? In the end, the more lasers you have, the more expensive the system is. The rise in capex needs to be offset by higher productivity. However, productivity is also influenced significantly by build time and shift patterns [and this depends a lot on the application you want to achieve]”, he continues.
Lastly, one item that is often overlooked in this assessment is software while, as per Rao’s explanations, it plays a big role in optimizing the process and thus achieving quality parts. As a matter of fact, engineers perform and determine all laser operations through software tools. Sometimes, achieving quality parts is often hampered by the lack of the right software tools. Taking the example of Additive Industries, he said their team has been working on developing dedicated software solutions for dynamic laser assignment, qualification and multi-beam tool calibration and they also invested in CFD and real-world analysis solutions.
Conclusion
Surprisingly, lasers hold a major role in a variety of industries such as telecommunications, instrumentation, medicine, computing and entertainment. In conventional manufacturing, one has observed their applications in processes such as cutting, drilling, welding, bending, cladding, cleaning, marking and heat-treatment. For such a versatile tool with an outstanding portfolio of applications, its ability to scale up in a technology sector like AM depends on the user ability to better define their requirements. In fine, a thoughtful analysis of the “why” and “how” of multiple laser AM systems, can definitely lead to increased productivity, fabrication of large size parts and reduced cost per part.
A few notes on the contributing companies:
Kennametal works across multiple types of additive technologies to drive improvements in both the solutions they make and how they make them. For example, multi laser powder bed fusion is the right choice for their hot work tool steel products because they achieve the desired material properties in combination with high accuracy and a simple process chain. At the same time, Kennametal applies binder jet printing to produce high quality solid carbide tools and wear components because they can leverage powder and sintering capabilities in conjunction with this additive technology. Every 3D printing technology comes with unique considerations; the challenge is to match the right technology to the right application to unlock the full benefits of AM and drive the biggest benefits for them and their customers.
Additive Industries is a 3D metal printer manufacturer for high-quality metal parts. It offers a system specifically aimed at high-end and demanding industrial markets. With class-leading build volume, robustness as well as productivity, Additive Industries redefines the business case for aerospace, automotive, energy and high-tech equipment. Headquartered in the Netherlands, Additive Industries has demo and service centres in the USA and UK and is a global key player in large volume metal printing systems.
This dossier has first been published in the January/February edition of 3D ADEPT Mag.