Desktop Metal has reported a total of $277 million in financing to develop it rapid growth and foster the adoption of its metal 3D printing system. The amount of 65M $ in this financing has been led by Ford Motor Company whose CTO, Dr. Ken Washington joins DM’s board of Directors.
Desktop Metal is one of those companies that have demonstrated a rapid growth within the industry on the one hand, on the other hand, that attracted a lot of investors. Since its first financing, the company has been able to develop an international expansion. We can recall the first time its Studio System, its flagship product, was shipped to Google’s Advanced Technology and Products (ATAP) group. Furthermore, it has already been granted patent for its technology.
However, as far as this partnership is concerned, Ford and Desktop Metal will work together to achieve Dektop’s goal vis-à-vis its strategy, especially with the integration of Dr. Ken Washington in the company’s board of directors.
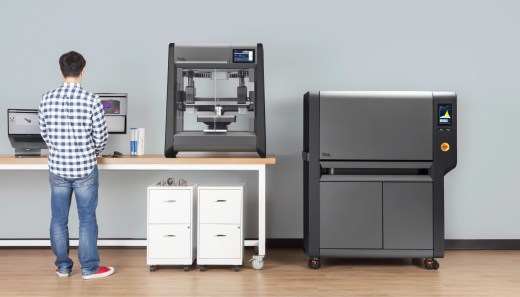
“The age of metal 3D manufacturing is here and this strategic partnership with Ford, along with our portfolio of investors, validates our vision to transform the way metal parts will be designed and mass produced,” said Fulop. “The continued support of our investors underscores the power of our metal 3D printing solutions to help engineers and manufacturers, for the first time, apply metal 3D printing for the entire product development lifecycle – from prototyping to mass producing complex, high performance metal parts in a cost-effective way.”
Changes that accompany this new funding are the increase of employees (more than 225 committed people); about 100 channel partners and resellers, more than 40 countries that can distribute its flagship product, a portfolio of 100+ pending patent applications covering more than 200 inventions, as well as the granting of two patents for its Separable Supports™ and last, the development of R&D including Live Parts™. The latter is a generative design tool that applies morphogenetic principles and advanced simulation to shape strong, lightweight parts in minutes.
For further information, follow us on our social media and subscribe to our newsletter!
Would you like to be featured in the next issue of our digital magazine? Send us an email at contact@3dadept.com
//pagead2.googlesyndication.com/pagead/js/adsbygoogle.js
(adsbygoogle = window.adsbygoogle || []).push({});