As its name suggests, the purpose of “Hybrid Manufacturing” is relatively easy to understand: taking the advantages of both additive and subtractive technologies within the same machine. The concept is relatively new as first hybrid manufacturing (HM) machines were launched in the 2000s. And like any new technology, there is a set of challenges, there is a learning curve and there are several concerns it raises within industries.
Unlike most scenarios where we used to highlight the advantages of additive manufacturing over conventional manufacturing processes, this article will look at the way they complement each other within the same platform. The concept becomes intriguing when one knows that additive processes start from the ground up while subtractive processes start from the top down – or when AM processes consist in adding raw materials, layer-by-layer to form a product while subtractive manufacturing consists in removing raw materials until the desired dimensions are met. Given the variety of additive and subtractive technologies that exist, what type of technologies can be combined to form a hybrid technology? What can we expect from a manufacturing process that involves the use of a hybrid manufacturing system? And what are the investments and implementation costs?
As we saw with AM, the potential benefits of HM have convinced some early adopters on the market. As a matter of fact, in the exhaustive list of companies that developed HM processes, one counts DMG MORI, ELB-Schliff, Matsuura, Mazak, Mitsui Seiki, Okuma, Meltio, 3D-Hybrid Solutions, Inc., Hermle, Siemens, Sodick, Diversified Machine Systems, Fabrisonic, Optomec, Thermwood, Weber Additive, Sulzer, and Hybrid Manufacturing Technologies, Imperial Machine & Tool Co. to name a few.
However, to tackle this topic, we have invited Hybrid Manufacturing Technologies’ Co-founder and CEO Dr. Jason Jones as well as Hans Weber Maschinenfabrik GmbH’s Commercial Director Additive Manufacturing Manuel Kolb to share the manufacturer’s perspective. CGTECH’s Product Manager, Gene Granata will touch on the software aspect of this topic.
The combination of additive and subtractive processes
As you may know, the AM portfolio covers various types of technology processes, which can be divided into three main categories: AM technologies that process powders, liquid and solid – each of them requiring a wide range of materials.
Traditional subtractive manufacturing on the other hand, is first intended for metals. Over time, this portfolio has included other processes that are compatible with a wider range of materials. They include electric discharge machining, CNC machining, water jet cutting, electrochemical machining and laser cutting. Directed Energy Deposition (DED)* is often mentioned as the main AM process that can be hybridized but it turns out it is not the only one.
“Any type of additive process that uses a nozzle for deposition can be combined with milling, grinding, or even laser cutting/ablation. The most common combination is Directed Energy Deposition (DED) with CNC milling of metal parts. Material Extrusion (ME) with CNC milling for polymer composites is also a growing adoption path, particularly for making fixtures and tooling”, Jason Jones from Hybrid Manufacturing Technologies states.
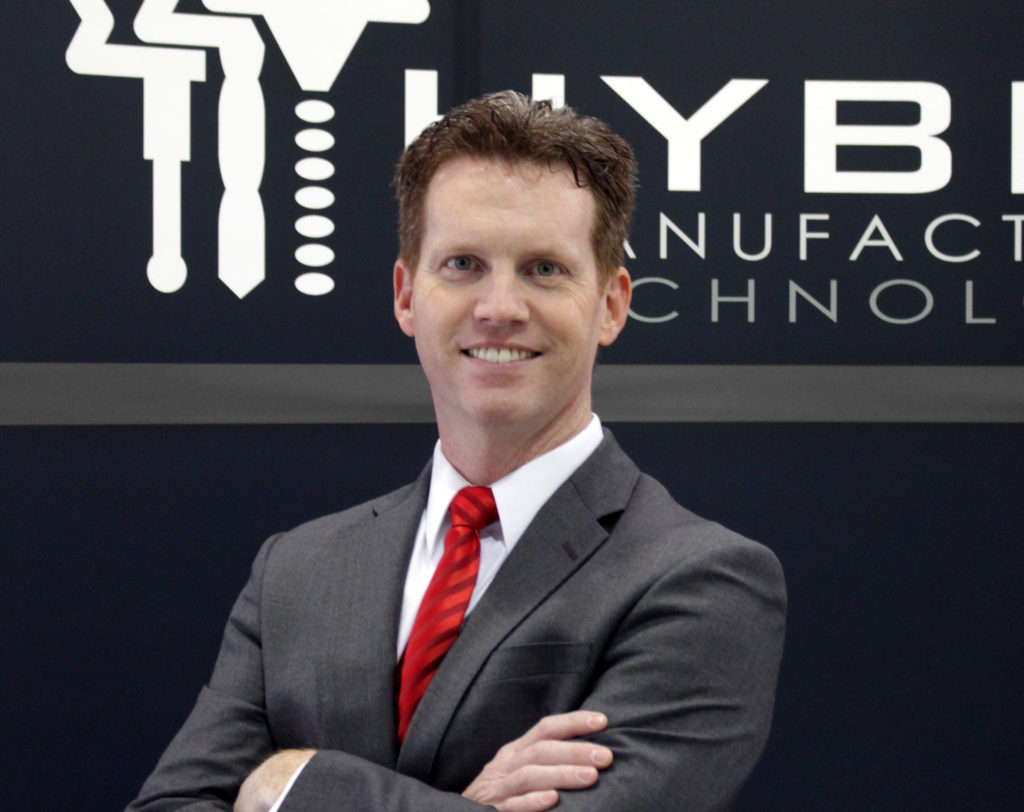
The truth is, while in the end, one only talks about hybrid manufacturing, it should be noted that manufacturers can either develop off-the-shelf hybrid machines or modify existing additive or conventional manufacturing machines to form a HM process. In this vein, in addition to DED, AM processes like sheet lamination and powder-bed fusion can be used in various forms with CNC machining. For instance, Beam-directed technologies, such as laser cladding can be integrated with computer numerically controlled (CNC) milling machines by mounting the cladding head to the z-axis of the milling machine.
Speaking of hybrid machines his company develops and commercializes, Jones explains:
“The part shape and material(s) determine the processes required and the required accuracy for the machine. We choose the best combination of machine and processing heads/tools for our customers. We integrate the modules into existing machines or supply new turnkey systems.When budgets are tight, often customers will opt for field integration into machines that they already own. However, additional capabilities come with one of our fully optimized turnkey solutions. We have solutions running on CNC machines (verticals, universals, mill-turns, etc.), gantries, grinders, robots, and parallel kinematic machines (hexapods, etc.).”
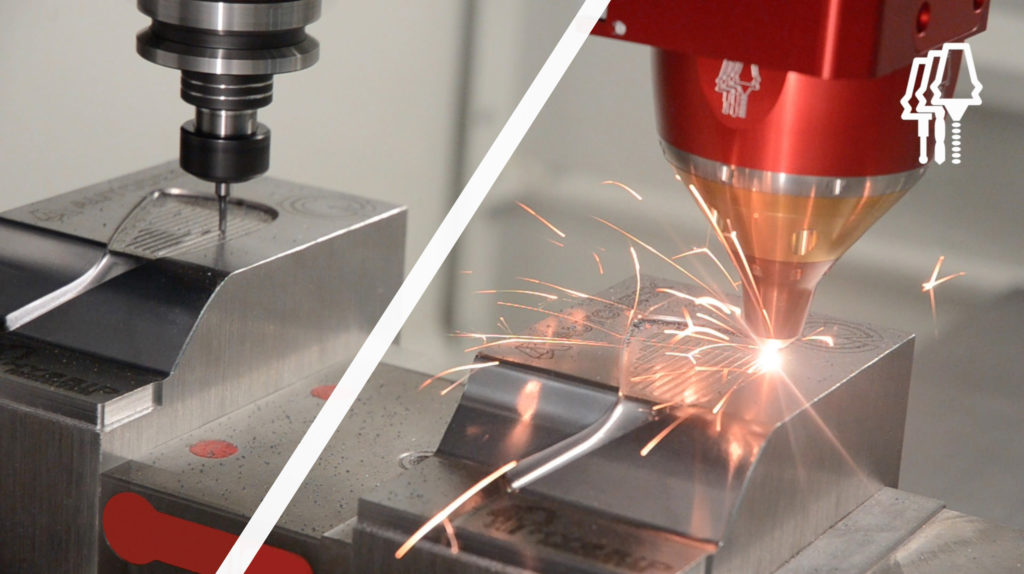
In the quest for the ideal system that will disrupt advanced manufacturing technologies, manufacturers have explored the combination of Wire-Arc Additive Manufacturing* with milling. Due to the deposition rate of WAAM that can reach up to 50–130 g/min with almost no limitations of the build volume, compared to 2–10 g/min in laser- or electron beam-based processes, the combination with milling[1] is acknowledged for delivering high productivity, low cost, high material utilization, and high energy efficiency.
Furthermore, researchers have also found out that new capabilities can be reached in a newly developed hybrid form of manufacture: Ultrasonic Additive Manufacturing (UAM), or Ultrasonic Consolidation[2]. Designed for metal components, the manufacturing process – which is classified in the category of sheet lamination – would raise the interest of those who are looking to produce multi-material structures with embedded componentry.
Also, cold spray processes that keep the metal powders in a solid state instead of melting them as seen in thermal processes have been explored in hybrid processes due to the deficiency in ductility/plasticity of cold spray additive manufacturing materials which limit the applications with this process. – An exclusive feature has been dedicated to “Cold Spray” in the January-February Issue of 3D ADEPT Mag.
Another example of hybrid manufacturing technology can be seen with the extrusion of plastic pellets. “We can combine fused granular fabrication with 5-axis milling to fabricate large, complex parts, with high surface quality and minimum material use. The additive process is a planar layer-by-layer melt deposition process, as known from fused filament fabrication. The milling process follows the same CNC machining concept Reichenbacher Hamuel is implementing in their classical subtractive machining centers. The two processes can be carried out sequentially: first the mentioned additive process, then the conventional milling process” Hans Weber Maschinenfabrik GmbH’s Manuek Kolb explains.
The manufacturing process of hybrid machines
Given the wide range of possibilities that exist in the HM portfolio, it won’t be possible to have a closer look at each process developed by market players. With examples provided by Hybrid Manufacturing Technologies, Weber Additive and CGTech, we will have a look at what to expect from the manufacturing process at the software, and post-processing levels.
The software perspective
If AM processes require engineers to apply DfAM methods, it turns out that engineers who leverage HM should design for HM in a certain way. As a matter of fact, design software advances are pivotal to capitalize on the advantages of a hybrid manufacturing platform.
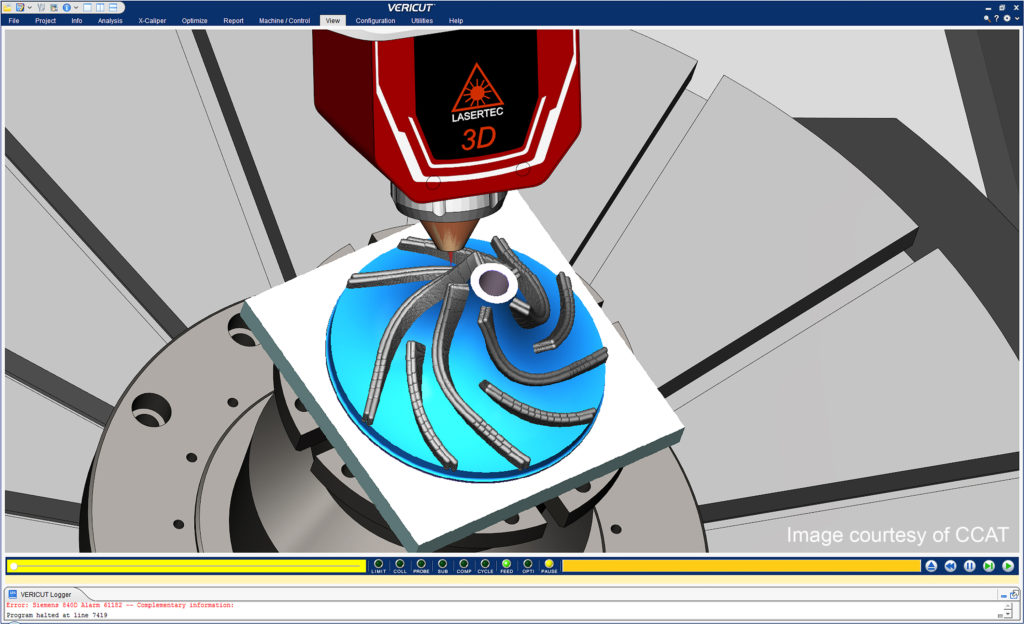
“Dedicated CAD/CAM and verification software is HIGHLY recommended to facilitate efficient and SAFE hybrid manufacturing. Every aspect of hybrid part manufacturing is more challenging, more expensive, and often unfamiliar to many companies breaking into this exploding field. Software dedicated to hybrid manufacturing helps by optimizing part designs for Additive Manufacturing (AM), offering unique operations not available in “subtractive-only” CAM software, and by verifying that the entire hybrid manufacturing process (sometimes involving multiple CNC setups and machines) will work as expected to produce the designed part.
Some manufacturers avoided investing in dedicated hybrid manufacturing software, and instead opted to use less efficient combinations of traditional subtractive CAD/CAM design and toolpath technology. They even resorted to manual editing/merging NC programs to create programs for hybrid CNC manufacturing. However, this approach is extremely inefficient and error prone, and sometimes led to expensive incidents in the shop with costly downtimes that followed”, CGTECH’s Gene Granata points out.
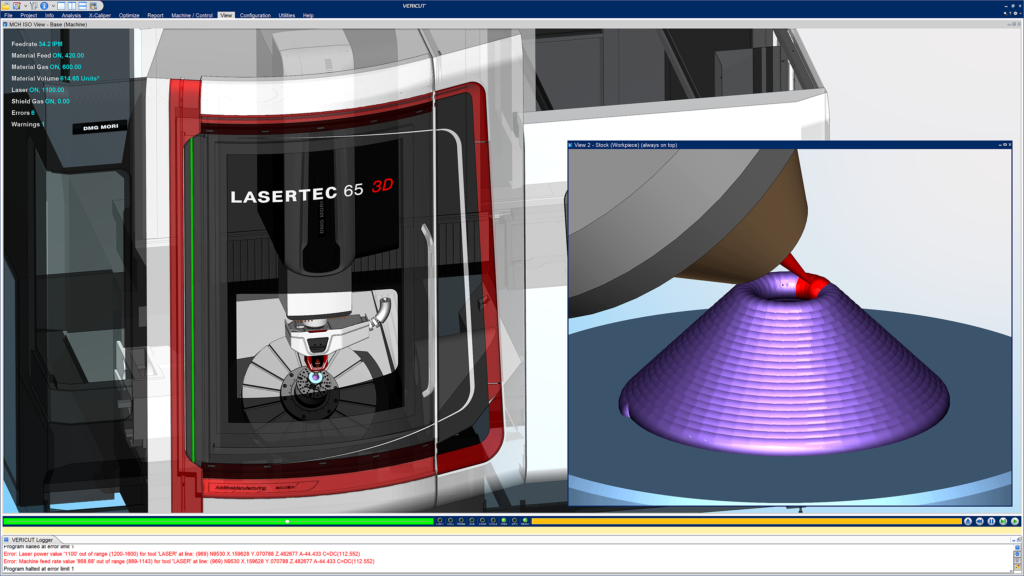
While Hans Weber Maschinenfabrik GmbH’s commercial director of AM believes in the importance of design software advances, he lays emphasis on three important aspects: the necessity to have an excellent 3D model quality or resolution, the calculation of the necessary printing offset of the contours as well as the thermally induced intrinsic bulk stress. Taking the example of a HM process based on plastic pellets and milling, he states:
“One important aspect is the 3D model quality or resolution. It is highly recommended to avoid meshed formats like .stl, because the precise milling process can make these artefacts visible. If it cannot be avoided, then a proper mesh resolution is important.
Another aspect is the calculation of the necessary printing offset of the contours, so that the milling process has enough material to remove and guarantee a homogeneous and void free surface finish. The offsetting can be very individual depending on the exact geometric requirements.The third aspect is the thermally induced intrinsic bulk stress in the printed material. During the milling process and removal of eventual support structures, the part can be deformed by the bulk stress and the release of fine structures by material removal. This must be respected during the planning of the milling process, to avoid excessive material removal at respective surfaces.”
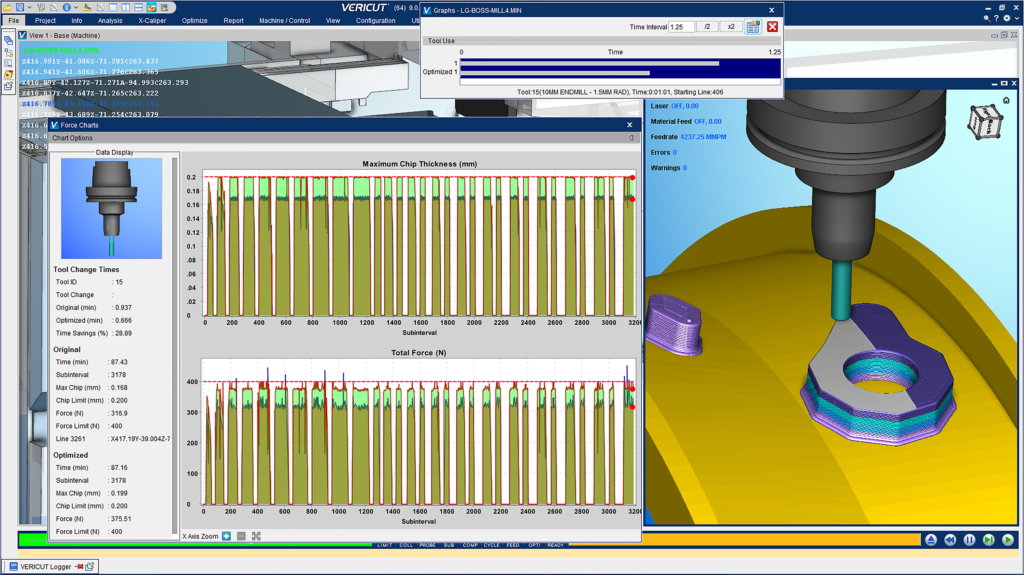
In a hybrid DED+CNC machine on the other hand, Hybrid Manufacturing Technologies’ CEO observes that “the deposition paths and the machining tool paths both need preparation. Fortunately, the digital workflow for both of these processes is nearly identical. In fact, both can be generated from the same computer model and often in the same CADCAM software.”
Several software providers currently offer solutions to do this in the same user environment. However, as part of this topic, we have asked CGTech’s specific questions to understand the compatibility of their software with hybrid manufacturing. CGTech first appeared on our radar after a collaboration with Thermwood, but the company has been active in the AM industry since the mid-2000’s. Three years ago, the software provider introduced to the market VERICUT 8.1, a simulation software designed for additive and hybrid-AM processes including direct metal laser sintering (DMLS), wire-arc additive manufacturing (WAAM), and big area/large-scale composites additive manufacturing (BAAM/LSAM) methods.
First, “an important and valuable aspect of hybrid manufacturing is optimizing the subtractive machining paths. With VERICUT Force optimization, this can be done while verifying NC programs, ensuring the final NC programs are not only free from errors, but the overall process is efficient as possible.”
“As we do with all of VERICUT’s digital twin CNC machine simulations, we worked closely with the folks at Thermwood to simulate their LSAM machines, including the NC machine codes that control the additive functions: dispensing and monitoring of material, roller tangential following that presses the composites material onto the layer beneath it, and ensuring each layer builds on top of previously deposited material or some other build surface.
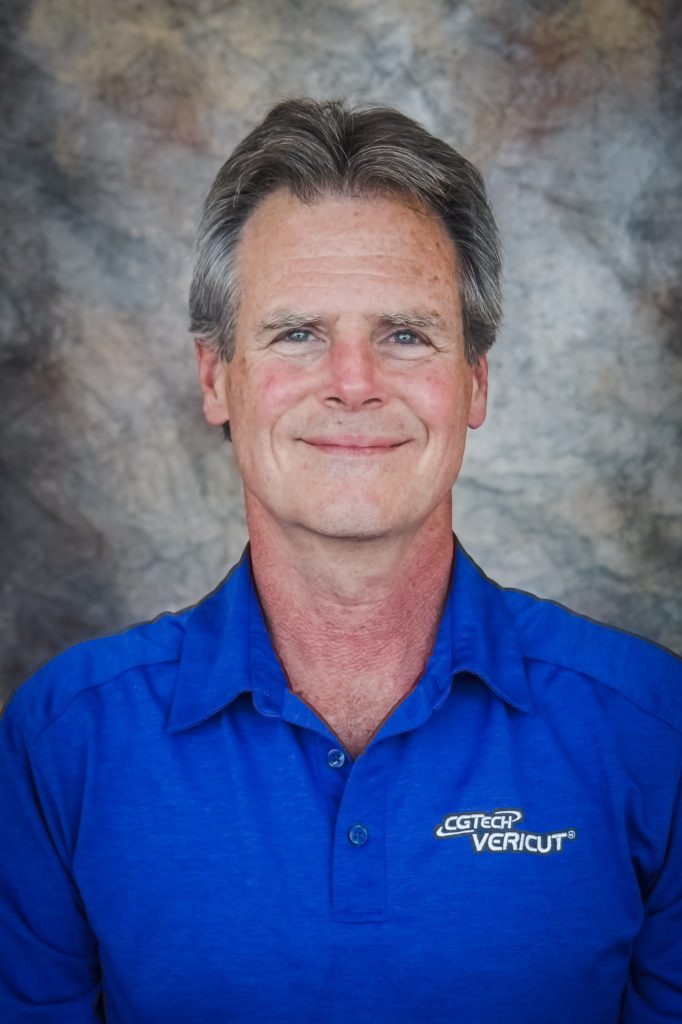
A simulation that runs in minutes can inform users when conditions are not suitable for additive deposition on their LSAM machine, detect when expensive collisions could occur with work holding fixtures or the part being built, optimize machining, and check that the final hybrid manufactured part matches the intended design”, Granata notes.
For engineers, combining hybrid manufacturing solutions, new topology optimization and generative design software facilitates the redesign of assemblies as single parts, eliminates the need to create interfaces between components and allows for the lightweight and parts reduction strategies that are very demanded in product development lifecycle.
Taking the example of VERICUT, Granata sheds light on software specifications related to AM, subtractive processes and hybrid technologies: “Users can add then cut, or cut then add in any order. On hybrid CNC machines, the choices about the order in which additive versus subtractive process are applied to produce the part are controlled by the order of NC programs, and the specific NC codes and parameter values they contain. By processing NC programs in the same order as they will be used on the hybrid CNC machine users see exactly how the part will be built, and machined, to achieve the final shape. Multiple operations that are performed on different CNC machines can also be simulated via multiple “setups” in VERICUT. For example, consider a turbine impeller type of part that is created by first turning the shaft/hub on a CNC lathe, then is moved to a hybrid 5-axis machine to deposit the blades on the hub, and perform the 5-axis blade and finish machining. VERICUT users verify the entire manufacturing process end to end, so they know it will work as expected to make the finished part.”
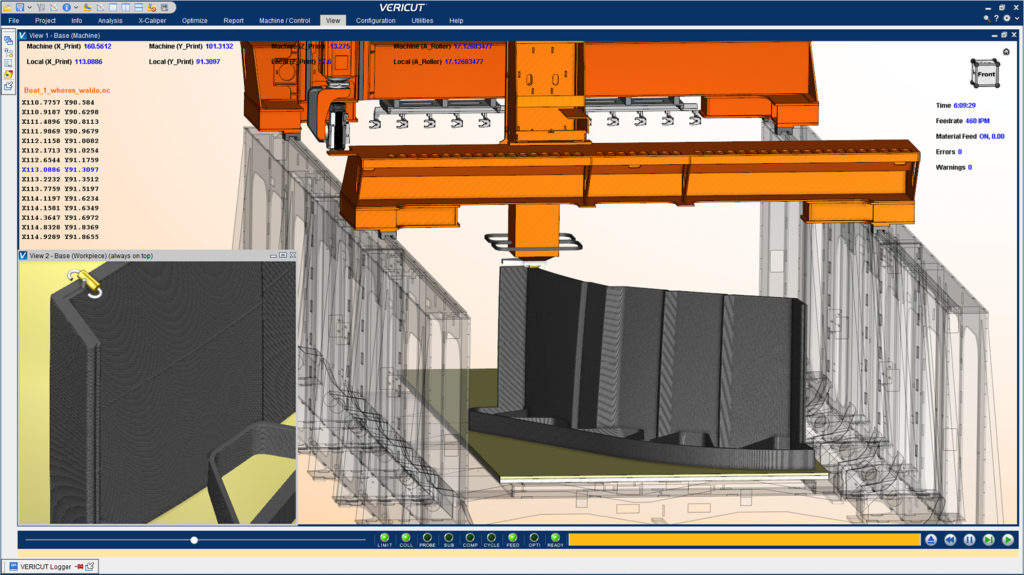
Manufacturing and post-processing
As far as manufacturing is concerned, it is worth noting that some processes for producing metal parts are not usually that different from processes that are used to produce polymer parts.
Imagine a machine that adds some material through a type of deposition process and then requires a tool change. Rather than using a deposition head, the operator will bring in a CNC milling tool that will remove some of the material. If desired, the operator can change the tool to use the additive process. While the two processes can be used interchangeably depending on the production needs, the difference is that for polymers everything happens at much lower temperatures. But that’s just one machine. We invite you to look at the specifications of manufacturing processes developed by other players. In this dossier, we have given a closer look at Hybrid Manufacturing Technologies’ process as well as Hans Weber Maschinenfabrik GmbH’s HM process.
The company provides “a wide variety of additive (DED, ME, Jetting, Direct Write, etc.), subtractive, and inspection (probing, laser scanning, eddy current, and ultrasound) technologies integrated together”. “Our AMBIT™ processing heads are automatically interchangeable so a customer can choose the combination of processes that best addresses their application needs. These technologies are controlled using edge computing and closed loop feedback to enable robust, optimized, and traceable performance” Jones points out.
Interestingly, while the AMBIT platform is acknowledged for surface inspection, the manufacturer develops a tool head that can verify quality post-deposition, detect cracks and void beneath the surface of the part. Not only does this enable CNC users to get quality assurance with their 3D printed part, but it also allows for an all-in-one manufacturing process in which an object is produced, finished and inspected in a single step.
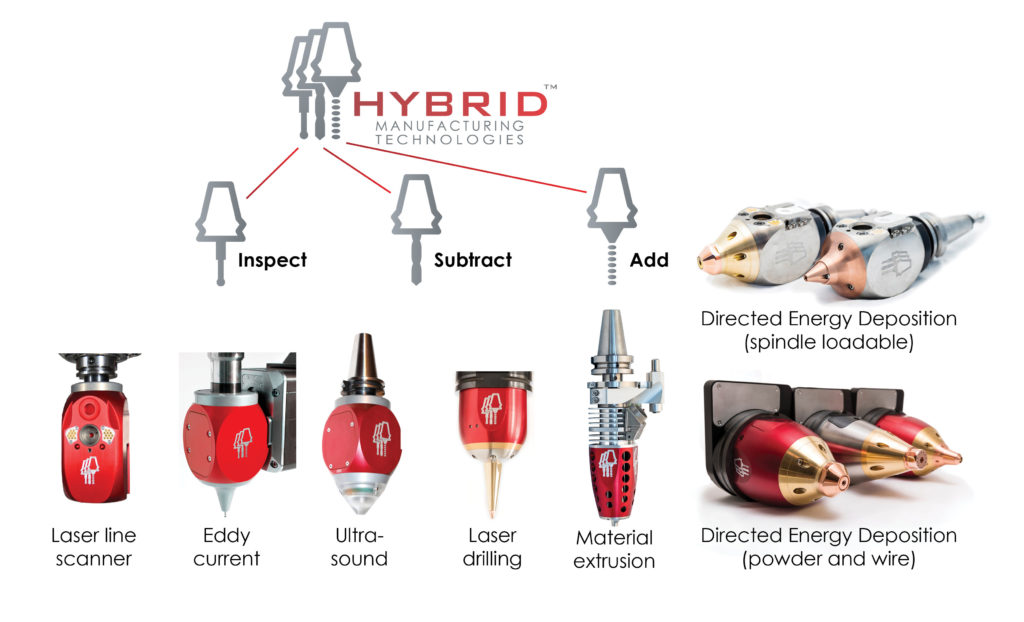
That’s certainly the reason why, when he was asked the main stages operators should perform after the manufacturing process, he enthuses: “The beauty of hybrid manufacturing is that often the post-processing can be fully automated. For metal parts, this routinely reduces the total cost of AM part production by 25-30% or more.”
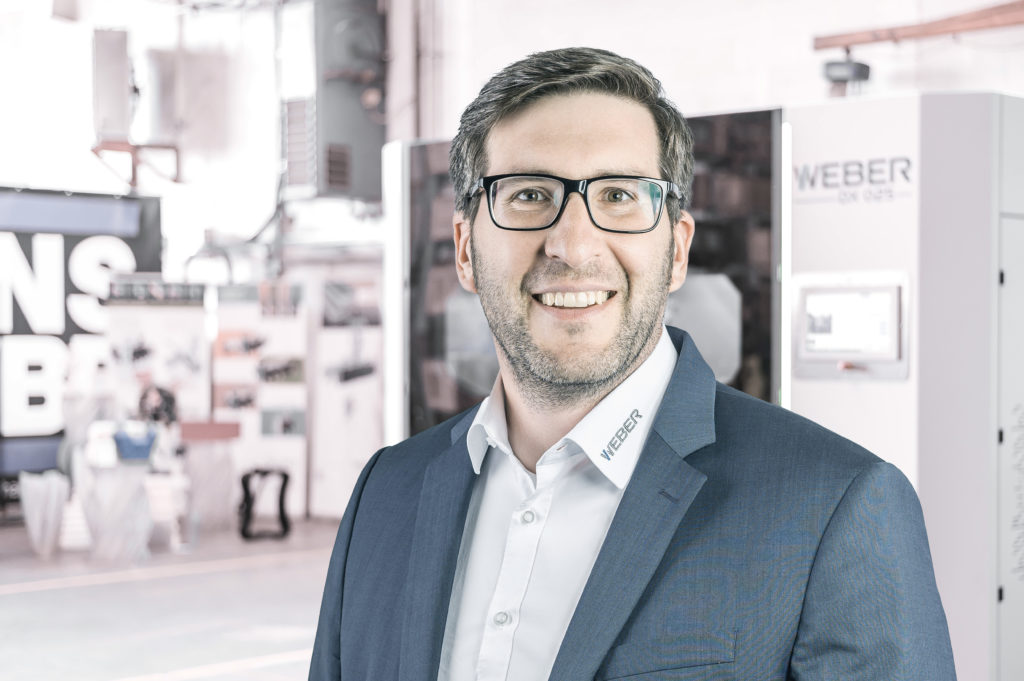
On the flip side, a look at the combination of fused granular fabrication and 5-axis milling from Hans Weber Maschinenfabrik GmbH reveals that it provides engineers with increased geometric design freedom as well as various extended component functions. Moreover, one item that can raise the interest in this process is the uniqueness of materials and their optimization.
While hybrid metal systems can process dissimilar metals to the same part – for instance, cladding with Inconel -, hybrid polymer systems can use injection moulding pellets and composite reinforced polymers. Multiple materials and new hybrid materials can be created and used to achieve an overmolding effect. Speaking of Hans Weber Maschinenfabrik GmbH’s HM process, Kolb outlines that hybrid materials “consider the synergy effects of the know-how in the field of mechanical engineering (machine construction) and extrusion technology of the two companies Reichenbacher Hamuel GmbH and Weber Additive. These support the emergence of a variety of options for machine configurations and of the production of a wide range of component sizes.”
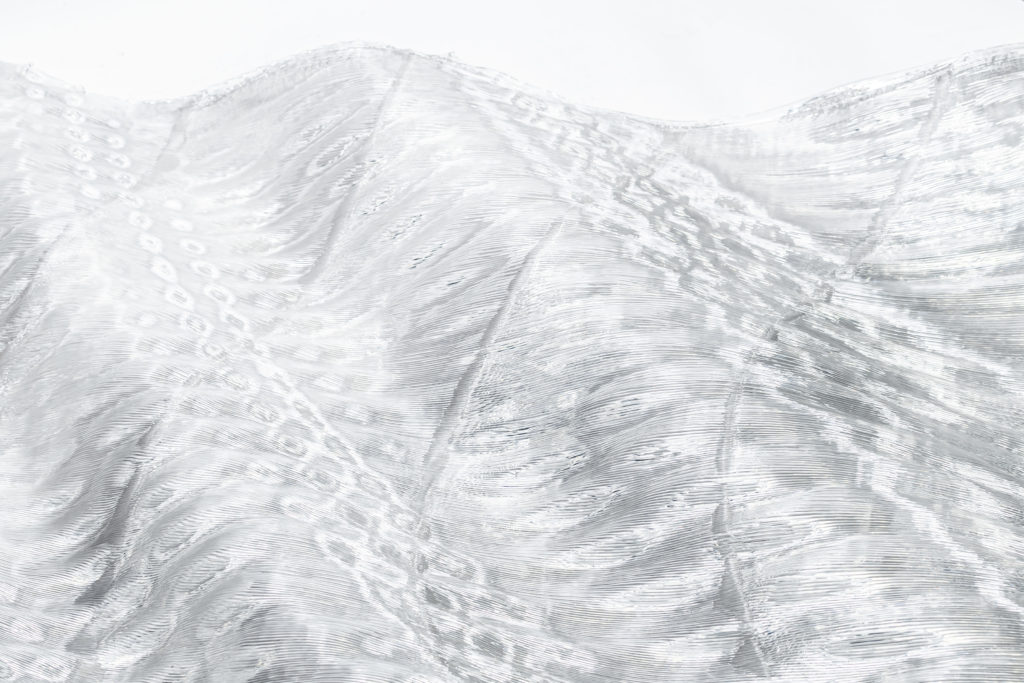
For the Commercial Director Additive Manufacturing, the hybrid solution is an ideal production candidate for operators who are looking to achieve better accuracy and ideal properties of the given part, and to reduce post-processing stages in the manufacturing.
“We can extremely reduce the time to print large parts by printing fast with high material output and consequently with rough tolerances with high layer thicknesses. To achieve better geometric tolerances and a high-quality surface finish, the milling process is necessary to be carried out on the cooled down part. Therefore, applications for large parts will be much more economical in contrast to only additive technologies, where the build time would be extremely high. The thermally induced geometrical deformation gets worse with bigger parts. Whereas only AM processes will suffer from high deviations from the original geometry, the milling process solves this issue in a very straightforward way. Additionally, the automated removal of support structures can be also directly implemented in the milling process and saves valuable time for the part manufacturer”, Kolb continues.
That being said, it should be noted that printed parts produced with Hans Weber’s solution deliver properties similar to milled plastic parts. “If these properties are not fulfilling the technical requirements, appropriate further post processing steps can be carried out. In some cases, the removal of support structures, a brim can take place first after the part was taken off from the build plate”, Kolb adds.
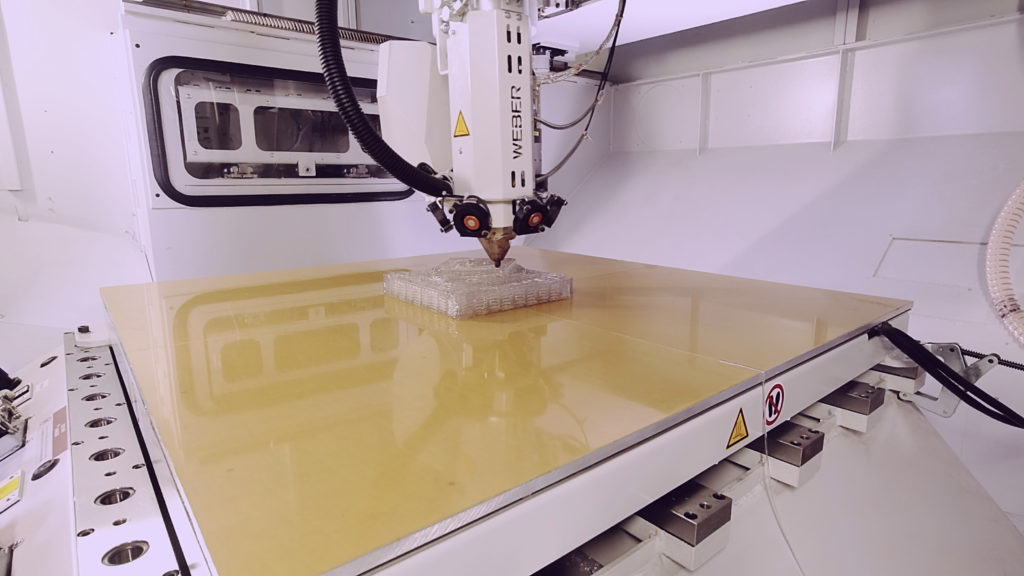
Applications & Costs
Applications. All this literature would not be interesting if there was no proof of concept, right? Experts and researches we carried out reveal that hybrid manufacturing enables applications in aerospace and automotive industries, repair and maintenance operations as well as mold and dye. Even though, real use cases have not been largely shared yet, professionals also believe in the potential of the technology for medical parts, given the fact that 3D printing and machining are already widely used separately within this segment.
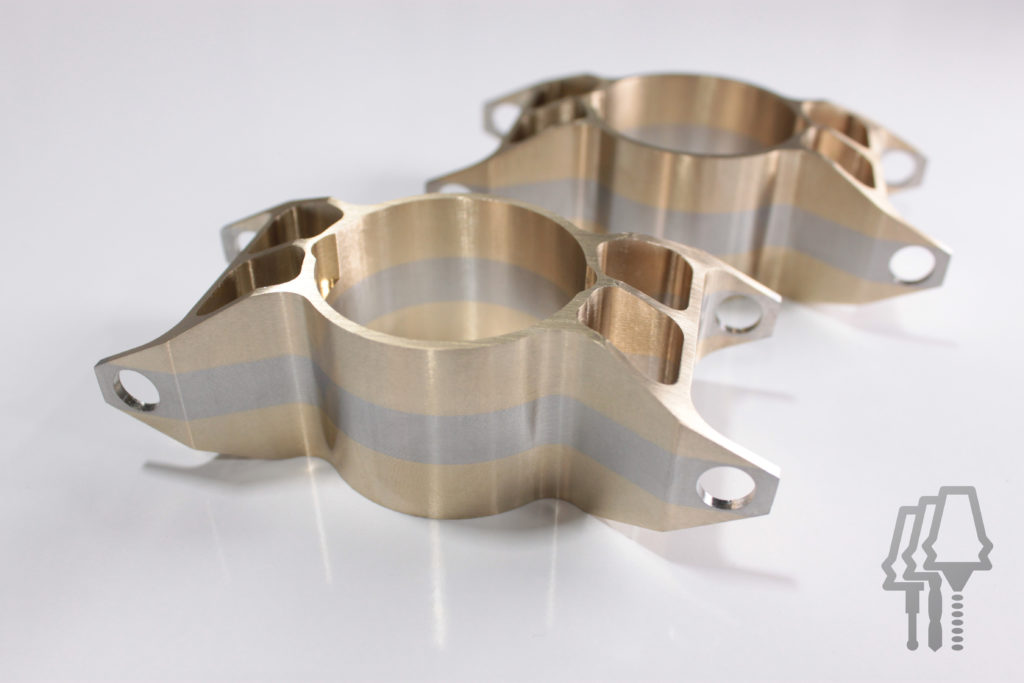
Compared to additive manufacturing technologies, three benefits we would keep from Hybrid Manufacturing Technologies’ CEO are:
“Hybrid machines bring three compelling capabilities. First, in-process finishing can create smooth surfaces on parts. This encourages faster deposition rates since the stair-step effect can quickly and easily be removed using machining. Second, in-process inspection enables assurance that the part produced is good inside and out before it leaves the machine. Lastly, interchangeable AMBIT™ brand heads mean that the most optimized tool or head can be used for each feature. This is a practical step that optimizes feedstock usage and cycle times.”
Although, very little information is spread on use cases that required the use of HM, we would like to mention the hybrid manufacturing of impellers by Sulzer, as a tangible example of this technology’s capabilities.
Operators often opt for casting technologies to produce closed pump impellers.
The company explained that the high wrapping angle and twist of the blades often lead to high performance when pumping common fluids like water or oil. This optimized geometry does not allow the internals of an impeller to be machined from a forged material. Furthermore, this restricted accessibility for the tools does not enable the use of subtractive manufacturing technologies like milling or electric discharge machining (EDM) without compromising the original impeller geometry.
The team at Sulzer therefore used a hybrid manufacturing process that combines a laser metal deposition and a 5-axis milling. “With a hybrid process, the amount of additive build-up can be limited. This helps to keep costs of the process reasonable. Additive build-ups quite often need support structures – but with hybrid manufacturing, these structures are often not necessary due to the variable build direction. Thanks to the final 5-axis milling, the material surface quality complies with the accepted industry standards. Because of the high geometrical precision, these hybrid-manufactured parts require less post-processing efforts”, the company explains.
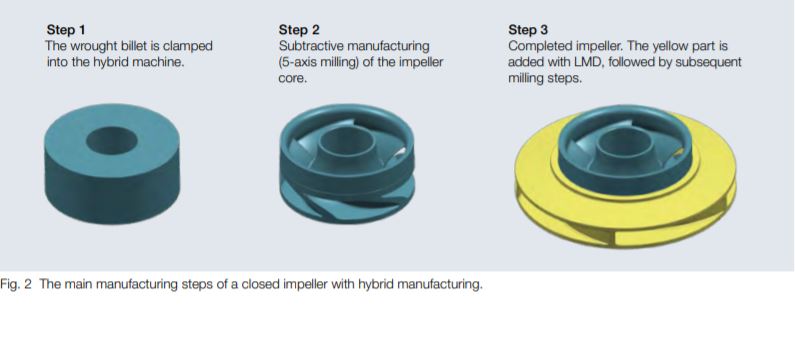
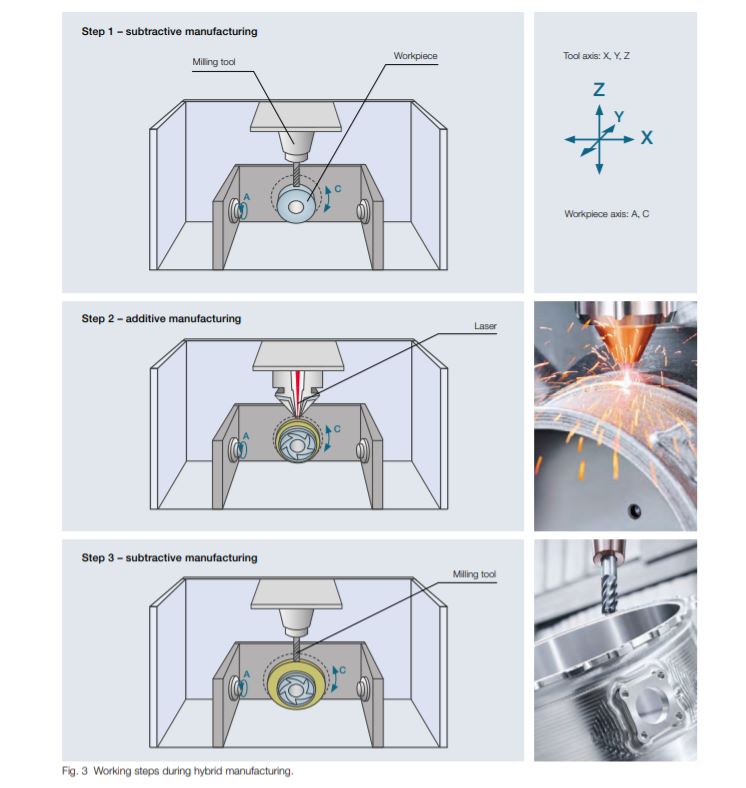
Thereafter comes the question of costs. Investments and implementation costs are often a challenge associated with each new manufacturing equipment. Currently, all companies cannot afford the costs of getting in-house AM capabilities. But, the decreasing costs of laser makes HM another alternative for companies that would like to transform their CNC machines into HM platforms. Furthermore, the flexibility and the ease of access are other arguments that work in favour of HM.
Companies that do not see the necessity to acquire a system, can always turn to service bureaus:
“Our in-house service bureau (hybridam.com) lets people use this technology without needing to invest in their own equipment. Next, AM can be added to their existing CNC and robotic equipment. This reduces implementation costs and allows for easy operator training and adoption. Also, hybrid machines generally reduce the amount of capital equipment needed to do AM by as much as 45%. This decisively contributes to the lowest total cost for each kilogram (or pound) of printed and finished material” Jones concludes. At Hans Weber Maschinenfabrik GmbH, leasing or solutions such as instalment purchase can be envisioned when it comes to acquisition. The company is open to alternative financial solutions to support investment decisions and give customers the possibility to explore how relevant and efficient their solution is during a trial use phase.
Advantages and areas for improvement of hybrid manufacturing platforms
The table below summarizes the main advantages and areas for improvement of HM platforms:
Advantages | Areas for improvement |
Achieve higher accuracy or better surface finish | |
Less need to focus on placement of support structures – as it is the case with AM | Important work to be done when it comes to optimizing the part to add materials or to mill away |
Allow for different materials in a single process, which means that parts that require different material combinations can easily be designed | The number of parts produced via hybrid manufacturing may be relatively small |
Less or no post-processing work: in-process finishing, in-process inspection & interchangeable heads |
This dossier has first been published in the March/April issue of 3D ADEPT Mag.