In its continuous efforts to develop new materials for the energy industry, AM company BeamIT Group unveils the latest superalloy it has been working on: René 80 RAM1. With a name partially similar to that of a real person, René 80 RAM1 will serve applications in Aerospace and most importantly, in the Energy industry where AM can ensure better combustion efficiency and reduce environmental impact.
René 80 belongs to the family of Nickel-based superalloys which are structured with a high melting point and excellent oxidation resistance at high temperatures. The material better performs at ambient temperatures when it is processed by AM technologies.
To qualify the material for AM, BeamIT relied on Elementum 3D’s material expertise that modified it using its patented RAM technology. Once the alloy’s chemical composition had been modified, BEAMIT Group technicians developed and optimized the LPBF process to achieve good density and a crack-free microstructure.
Furthermore, as heat treatments are essential to ensure performance in an AM production, the team conducted a deep research to identify the most suitable treatment and also to eliminate any cracks in the parts.
“René 80 is proving that our one-stop shop strategy succeeds throughout the entire value chain, including when researching and developing new materials. Integrating special processes enables us to devise an otherwise unattainable solution with extraordinary results. The tougher the technological challenges, the more process integration and the innovation of post-processing, made available to highly skilled metallurgists, not only make the difference but become the only way forward. René 80 is one of our first demonstrations of this concept. And we are not done yet because other new advances are already in the developmental phase,” says BEAMIT Group General Manager Andrea Scanavini.
The parameters for René 80 RAM1 treated with HIPing and HIP quenching were characterized and compared with as-built René 80. With the optimized HIP-Q cycle, we recorded a 20% increase in the mechanical properties compared with the aged condition of René 80 produced with conventional technologies. Furthermore, elongation up to 8% was achieved with a 37% increase compared to casting, the company explains in a press release.
The advantage of the process parameterized by BEAMIT Group lies in the HIP-Q phase. The treatment can be performed with Quintus technology and enables HIPing to be followed by rapid quenching in Argon to produce a high-performance material with just a one-step heat treatment and ensure a shorter lead-time than treatments using conventional methods.
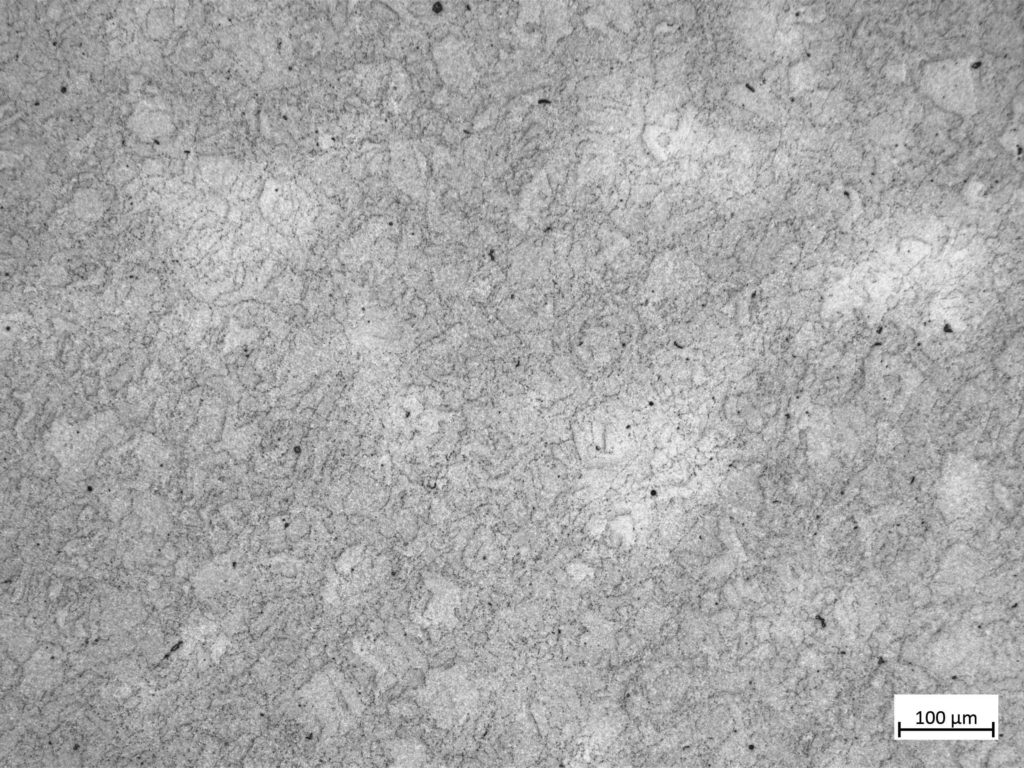
Finally, tests were conducted at high temperatures and to gage cracking resistance which
confirmed a yield strength of 750 MPa at around 900°C.
Jacopo Sisti, BEAMIT Group Materials and Special Processes Manager says, “It was a challenge to actually print an alloy that performs so well at high temperatures, but we fine-tuned the AM process and succeeded – plus we achieved high density. The turning point came with the innovative HIP-quenching heat treatment: we avoided the formation of cracks in the material which meant that we delivered better static mechanical properties than the alloy produced with conventional technologies.”
Remember, you can post job opportunities in the AM Industry on 3D ADEPT Media free of charge or look for a job via our job board. Make sure to follow us on our social networks and subscribe to our weekly newsletter : Facebook, Twitter, LinkedIn & Instagram ! If you want to be featured in the next issue of our digital magazine or if you hear a story that needs to be heard, make sure you send it to contact@3dadept.com