A conversation with Joseph Crabtree
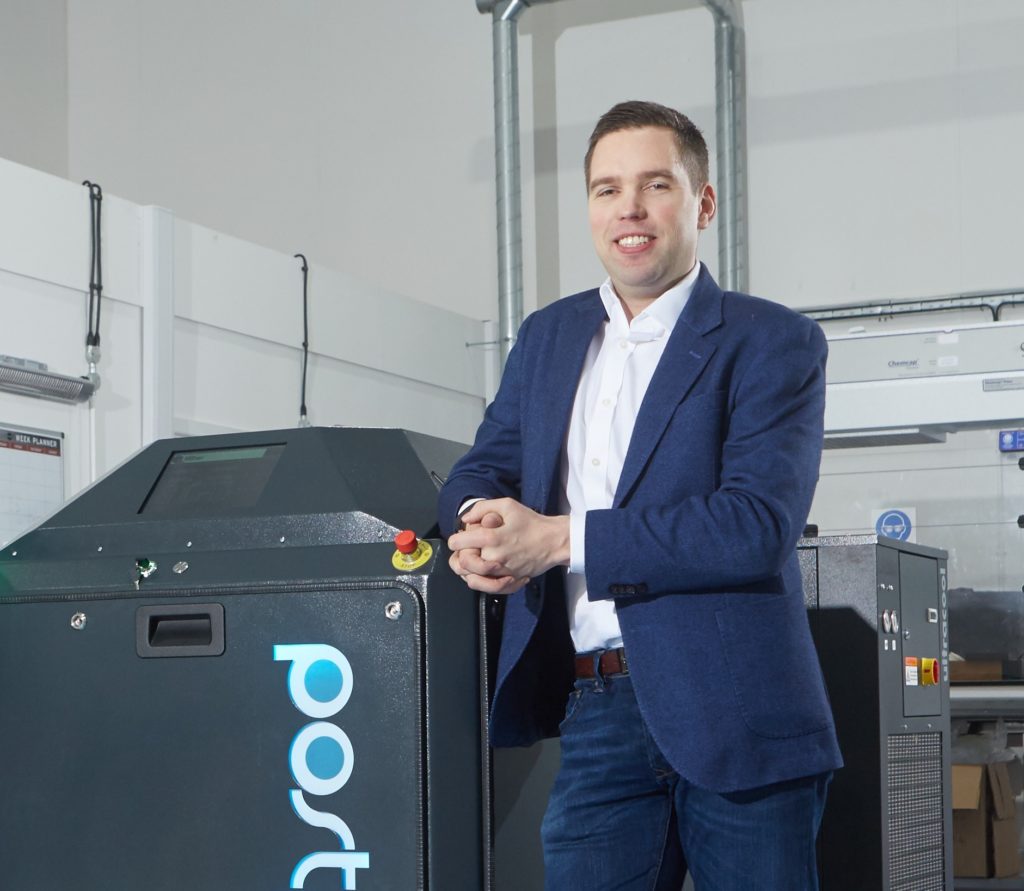
This story is about seeing “the bigger picture”. Those who have been in this industry for decades have only focused their efforts on developing their 3D printing technologies. They tend to forget that to make it profitable in the long run, they should also demonstrate possible applications that could result from these technologies.
It takes a few outsiders to look at the bigger picture, to discover the part nobody was looking at: post-processing. In the short list of companies that have decided to address this issue, there is Additive Manufacturing Technologies (AMT), a UK-based company that develops automated post-processing solutions called PostPro.
In the midst of Formnext Connect, we caught up with Joseph Crabtree, CEO at AMT, todiscuss some of the company’s latest developments, as well as the impact of their Vapor Smoothing technology on various materials such as TPU and PP.
Five years ago, Crabtree knew nothing about AM. Engineer by trade, he graduated in materials science. 3D printing came into play when he was looking for other opportunities. This timing was perfect for those who were interested in developing metal AM as patents for several technologies including binder jetting began to expire, allowing new companies into the market. But Crabtree was not interested in developing a metal AM technology. He realized that even if companies might invest extra miles to develop low-cost production 3D printers, 80% of the overall price of a 3D printed part still depended on the post-processing. The rest of the story became obvious: AMT should solve that missing link.
“This was the next problem we had to solve. If you don’t have the materials, the printers, and the post-processing, then you can’t say AM is a viable technology. With a background in traditional manufacturing, I looked at the obvious problems in traditional manufacturing and applied them to AM. The result was a whole range of automated post-processing solutions that allows [any industry] to produce an end-to-end ecosystem”, Crabtree says.
Remember, post-processing is the last step in the manufacturing process. It is also an umbrella term that covers a variety of stages that 3D printed parts have to undergo before being used for the final purpose. PostPro technology, on the other hand, focuses on automated cleaning and depowdering. The biggest challenge with this stage is that many manufacturers do not know how to unpack and “depowder” their parts without any human intervention.
In the three years of its existence, AMT has worked hard to provide a fully automated depowdering solution that can help operators overcome this challenge. Furthermore, despite the Covid-19 pandemic, this year has remained a busy one for the AMT team. It saw the launch of two new de-powdering systems developed in collaboration with Leering Hengelo and the grant of several patents for its Chemical Vapor Smoothing. It also marked a collaboration with HP to deliver industrial Post-processing for 3D printing applications with Chemical Vapor Smoothing technology.
““We started this year with great aspirations, however after Q1 2020 the pandemic hit. At the time, No one knew what was going on, but upon reflection, we need to recognize what it did for us: it has expedited the adoption of 3D printing. Whereby traditionally the adoption might take five to ten years to be adopted at a large scale, that timeline has been reduced”, the CEO adds.
For the founder of AMT, the pandemic has made them evolve from the state of “uncertainty” to a wealth of opportunities. The aforementioned developments are just a few examples that illustrate this range of opportunities but there can be more.
“As we progress, we are looking for more partnerships with material producers including BASF, DSM, Lubrizol and Evonik – to name a few of them. We have also been working on a lot of new projects. The pandemic has caused the acceleration of technology. Next year, we are going to see a bunch of applications in aerospace, automotive but I see the medical sector as a key vertical industry. Interestingly, this acceleration/adoption of technologies is not just about AM but all manufacturing technologies”, Crabtree outlines.
The Vapor Smoothing technology and its impact on various materials
PostPro Chemical Vapor Smoothing technology is AMT’s core technology. The company has more patents granted for this technology. Most importantly, the technology would allow for sustainable manufacturing due to its multitude of purposes.
The technology can turn a 3D printed rough part into an aesthetically pleasing part. However, for the expert, the most important is not only about making the parts visually acceptable, “it’s about making a part functionally performant and adding inherent value. It’s only when the parts perform better, that you can unlock those applications across automotive, medical, and other industries that you couldn’t have done previously.”
So, how does the PostPro Vapor Smoothing technology enable to seal the surface, and offer the “injection molding look and feel” Crabtree is talking about? Through matching of chemicals and polymers.
For example, flexible polymers do not have the same properties as composite polymers. To process the parts manufactured with these materials, different consumables must be used during this post-processing stage. The expert explains that those consumables are then vaporized – in other terms, transformed from liquid to vapour. Under the right temperature conditions, that vapor is used to process the plastic or the polymer part –with respect to regulatory requirements.
As far as flexible polymers are concerned, operators that read these lines will certainly agree with the fact that it’s a real “Holy Grail” to post-process parts made of these materials manually. The Vapor Smoothing technology would not only achieve it automatically, but it would do so by increasing mechanical properties such as elongation break and fatigue resistance – in a nutshell, properties that are crucial to increase parts performance.
Another key takeaway we get from our conversation with Crabtree is that unlike other automated post-processing equipment that is designed for a certain type of materials, AMT’s PostPro technology can work with any materials but also any powder-based technologies. Indeed, due to its modularity, the system can be adapted to other industrial 3D printer configurations.
With 100 systems at customers’ facilities across the globe, it is fair to say that PostPro technology is gaining momentum. Moreover, the fact that everything the company does, every project it carries out, or every company it partners with is underpinned by sustainability, contributes to national and global recognition of its potential. In this vein, it has recently been awarded two hundred thousand euros by the UK government for that commitment to sustainability.
While waiting for our next physical rendez-vous at Formnext 2021, where AMT will hold a live demonstration of how its end-to-end system can achieve automated post-processing of a 3D printed part, the upcoming months will certainly see more real-life applications, more partnerships and a more mature AMT that will continue to raise awareness on this “dirty little secret.”
Remember, you can post free of charge job opportunities in the AM Industry on 3D ADEPT Media or look for a job via our job board. Make sure to follow us on our social networks and subscribe to our weekly newsletter : Facebook, Twitter, LinkedIn & Instagram ! If you want to be featured in the next issue of our digital magazine or if you hear a story that needs to be heard, make sure to send it to contact@3dadept.com