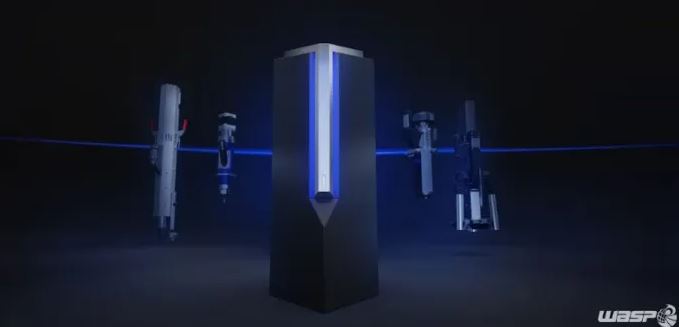
Italian 3D printer maker WASP- World’s Advanced Saving Project took Formnext by storm with their new range of 3D printing technologies which stresses on sustainability and accessibility, keeping up with the theme of the Frankfurt event.
The Italian company showcased new advancements in the Liquid Deposition Modelling (LDM) and Fused Granulate Fabrication (FGF) 3D printing. This included products like CEREBRO – an integration of robotic arms and WASP extruders, METAMORFOSI – a multi-material pellet extrusion system and the WASP App – software for customized serial production.
CEREBRO System integrated 3D printers
Through the CEREBRO system, WASP has transformed robotic arms into a 3D printer compliant with Industry 4.0. The system is integrated with WASP extruders and printing tools to produce 3D-printed parts. There are many combinations of using the robot arms and WASP extrusion technologies including the FIRECAP heated chamber and the Vacuum Buildplate System which allows the use of different types of printing planes compatible with different 3D printing materials.
New pellet extrusion system
This year at Formnext, WASP displayed a new multi-material pellet extrusion system building on the success of the large scale pellet 3D printer they launched 8 years ago. METAMORFOSI with WASP High Definition Pellet (HDP) can control and modify the position, quantity and properties of the 3D printing material at different points in the 3D printing process. This helps to make the AM parts stiffer in some areas and flexible in others based on the needs of the industry.
CEREBRO makes it possible to use WASP HDP XL METAMORFOSI on any robotic arm or 3D printer. This was displayed at Formnext, where WASP and Sekisai created a 3D printed part using METAMORFOSI and 3MT HDP.
The WASP App
On the software front, WASP launched the WASP App building on the success of the Vase Generator developed by Tommaso Casucci in 2014 for specialized ceramic 3D printing modeling and the successive development of parametric 3D modeling software, created to enhance clay 3D printing. The new app transitions from prototyping to mass production of ceramic 3D printed parts by customized serial production. The AM industry manufacturers can set the shape, dimensions, texture and slicing settings according to their needs to make their own ceramic 3D printed parts.
The combination of WASP 40100 LDM, Continuous Feeding System, and Automated Production System can lead to 24/7 customized serial production where the G-code export mode enables countless number of copies production.
Remember, you can post job opportunities in the AM Industry on 3D ADEPT Media free of charge or look for a job via our job board. Make sure to follow us on our social networks and subscribe to our weekly newsletter : Facebook, Twitter, LinkedIn & Instagram ! If you want to be featured in the next issue of our digital magazine or if you hear a story that needs to be heard, make sure to send it to contact@3dadept.com