There are so many additive manufacturing technologies which promise a lot and deliver little that sometimes, it’s hard to perceive their effective role in manufacturing. However, a relatively new technology called volumetric 3D printing is increasingly gaining traction for good reason: not only does it intrigue by a process that is way different from the well-established layer-by-layer processes, but it promises a lot more: the ability to print an entire object in one go. Wouldn’t that be a dream come true?
To make it easier for us, we call it “volumetric 3D printing”. Note that this new technology has more than one fancy names: tomographic 3D printing, xolography (named this way by XOLO), volumetric additive manufacturing – for those who would like to point out the industrial perspective of the technology – or even “system and method for a three-dimensional optical switch display (OSD) device”. This latter is an invention of Dallas-based Southern Methodist University that was granted a patent by the US Patent Office.
However, a company that commercializes a holography technology has often called volumetric printing “Hologram 2.0“. Volumetric prints however are not produced in the same manner as holograms, in that there is no interference pattern generated or used in basic volumetric prints.
Anyway, it’s already been five years that volumetric 3D printing has been in the research stages but the process receives even more credibility last year when some experts in the field announced the commercialization of their technology.
First, let’s find out what volumetric 3D printing is
Volumetric 3D Printing (V3DP) is quite complex to define. In this process, a pattern is projected into a vat of transparent photopolymer liquid repeatedly from all angles. This resin-based technology is often compared to SLA printing. However, what makes it outstanding is the fact that rather than curing the resin by projecting a 2D image of the current layer into the container, V3DP uses several lasers to create intersecting points within the liquid. Moreover, whereas resin-based 3D printers cannot withstand oxygen, the latter can be used as an additive in VI3DP as the operator must slow down the solidification, as the light patterns must pass through resin freely for some distance.
Among the scientists that have reflected on the topic, three are quite interesting to follow:
- Brett E. Kelly, Indrasen Bhattacharya, Hossein Heidari, Maxim Shusteff, Christopher M. Spadaccini, Hayden K. Taylor, researchers from the University of Berkeley reported on the technology they developed via tomographic reconstruction. Their report reads:
“We developed a method, computed axial lithography (CAL), that allowed us to synthesize arbitrary geometries volumetrically through photopolymerization. The CAL approach has several advantages over conventional layer-based printing methods. Our method may be used to circumvent support structures, as it can print into high-viscosity fluids or even solids. Printing 3D structures around preexisting solid components is also possible with our approach. CAL is scalable to larger print volumes and is several orders of magnitude faster, under a wider range of conditions, than layer-by-layer methods”.
- Researchers from the Ecole Polytechnique Fédérale de Lausanne and founders of Readily3D, Damien Loterie, Paul Delrot, and Christophe Moser. They explain how the project started:
“During our Ph.D. studies, we discussed on multiple occasions new concepts for photopolymerization that involved shaping light beams in 3D to create the desired object. Our project really took off when, in 2017, we decided to test experimentally whether we could make a 3D object by illuminating a photosensitive resin from multiple angles, which was the basis for tomographic printing. These initial experiments were surprisingly successful, and we realized that we were onto something”.
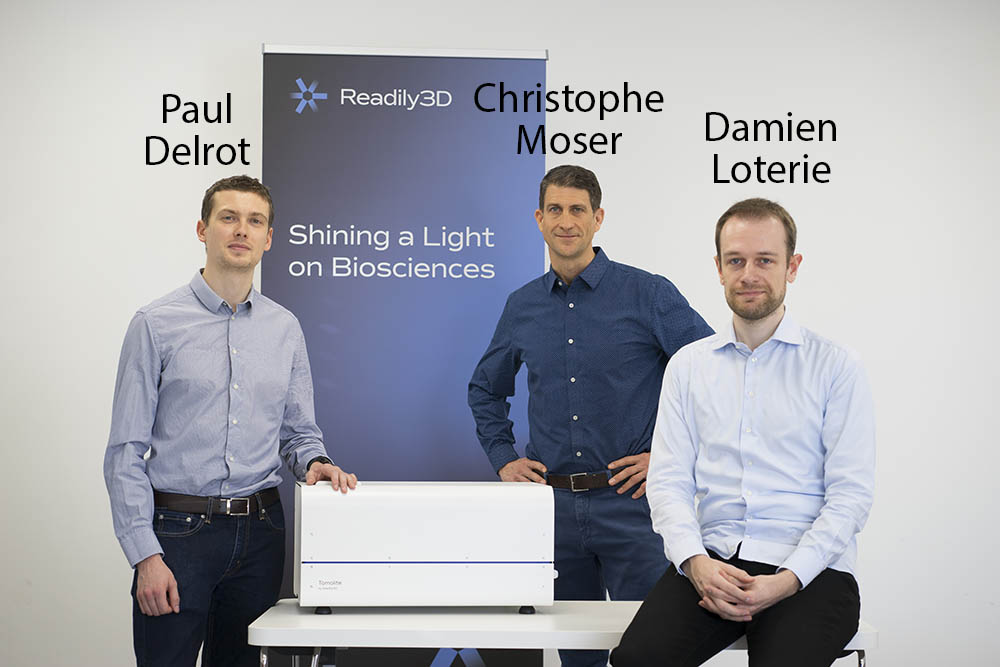
Readily3D’s technique is also based on the principles of tomography. Their process works by sending a laser through a translucent gel – either a biological gel or liquid plastic.
- And xolo. Founded in January 2019, the majority of the team works on xolography throughout 2019. With a key focus on their technology, the team explained:
“The xolography technology can very well be described as a process in which a planar printing zone is continuously – and with high speed – moving through a photopolymer tank rather than photopolymer slowly moving from a tank into the print zone of a conventional SLA/DLP printer.”
Despite the uniqueness of each of these volumetric 3D printing approaches, we might be tempted to think that this approach is no longer 3D printing as it does not meet the layer-by-layer principle. The truth is, although we do not see the well-known “Z-axis” operate, in these approaches, the process works simultaneously in three dimensions at the same time.
“Most 3D printing technologies rely on an additive layer-by-layer process. Volumetric printing, however, relies on a photopolymer-filled vat in which each voxel (3D analogue of a pixel) can be selectively addressed to convert it from the liquid (uncured) state to the desired hard (cured) material state”, xolo explains.
Furthermore, at the level of materials, the viscous resin can allow for the integration of much more additives than common resin-based 3D printers could contain, which opens up more opportunities for the development of new materials.
In this vein, the process which is quite similar to SLA/DLP 3D printing (- and where there are no layers -) can be seen as a new generation of additive manufacturing technologies as parts solidify instantly in three dimensions.
Addressing one urgent issue in manufacturing
The most significant advantage of V3DP is speed. So far, AM technologies deliver an entire part in a few days or hours depending on the technology used. VI3DP promises the fastest printing speed we have ever seen in the AM industry as it can print an entire object in seconds or minutes.
“The most spectacular aspect of our technology is speed: because the whole volume is solidified at the same time and not layer-by-layer, objects can be printed in just a few tens of seconds. This is revolutionizing as it is unmatched by any other method at similar scale and resolution”.
Xolo could not agree more as for the startup, the V3DP technology is the basis for unprecedented speed and design freedom “as printed parts do not need to be attached to a platform anymore.”
And there are other advantages as well:
“Printing directly within the resin volume also solves additional challenges of traditional AM systems. For example, we do not require temporary supports to print hollow structures or overhangs, because the object is held in place by the resin during the relatively short print time. The lack of mechanical contact between printer and resin also means that we can print within sealed, sterile containers. Finally, we are able to print soft and deformable materials, which tend to be challenging or impossible to make on AM systems based on deposition or recoating operations”.
“Volumetric 3D printing will challenge the state-of-the-art only where customers are unhappy with existing solutions. Think of time-sensitive applications or manual removal of support structures, the staircase effect, etc. With the release of the xube, we hope to inspire creative minds for applications that were not realizable before. We want to enable products that were unimaginable before’’, the team at xolo explained to us.
Volumetric 3D printing technologies and their specifications
The buzz around V3DP might be hard to ignore but reality shows that the list of companies that are moving from lab to markets is still very short.
In the research field, in addition to the aforementioned researchers from Berkeley University, a group of researchers of the University of Michigan tackled the issue. Still in the research arena, Siemens Energy filed a patent for “Systems And Methods Of Volumetric 3d Printing” in 2018 that describes a process similar to the one developed by T3DP, a California-based startup developing 3D printing technology. The latter relies on a resin comprising an “optical molecular switch molecule, wherein the optical molecular switch molecule has a non-fluorescent state and a fluorescent state, wherein at one wavelength of optical excitation the molecule has a first state, and at a second state the optical molecular switch molecule fluoresces at a second wavelength of excitation.”
Also, for reasons that are currently unknown, we have discovered that Disney also holds a patent for “near instantaneous object printing using a photo-curing liquid”. Apparently, this would be a form of volumetric 3D printing.
For now, companies that are making V3DP a reality in the field by commercializing their technology are xolo and Readily3D.
The xube volumetric 3D Printer
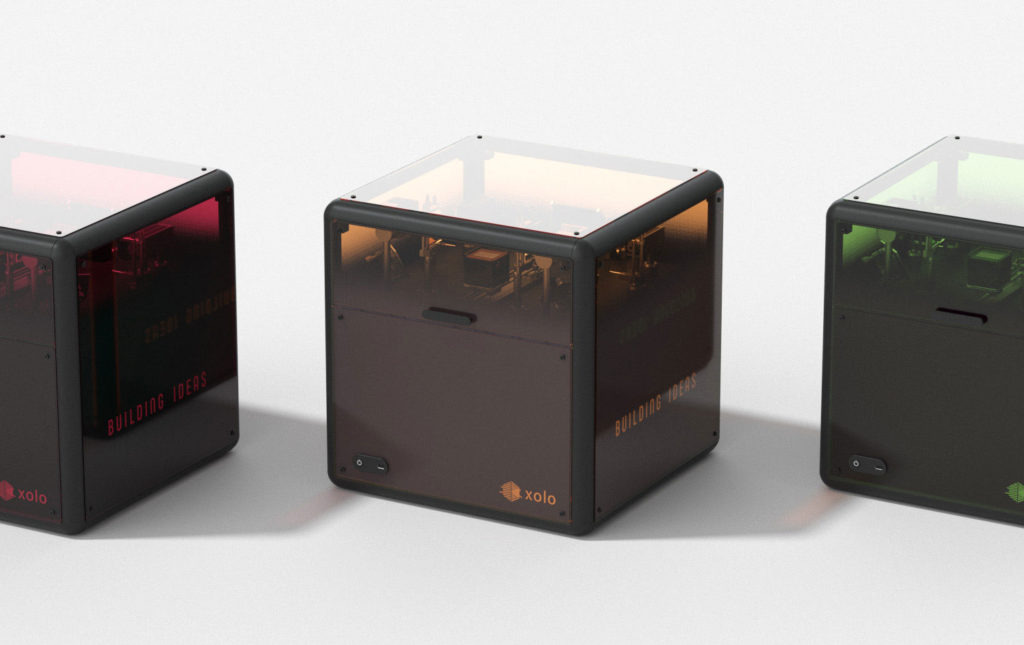
German startup Xolo unveiled its new 3D printer at the end of 2020. Called xube, the system is based on a technology Xolo called Xolography (obviously!). The xube 3D printer is capable of fabricating small parts in about 20 seconds and large parts in 5 minutes.
“The xube is specially designed for curious researchers: While standard protocols are available for printing acrylics, it is open to individualization, all printing parameters can be chosen freely and any self-made material can be employed. The customer loads the printer with a photopolymer vat with dimensions spanning from >50 mm to 10 mm along with the space coordinates. Within seconds to about a few minutes (depending on the print size), the object is solidified with high accuracy based on a standard STL input file”, xolo told 3D ADEPT Media.
According to the company, once the printed part – or the “solidified object” as per the words of xolo – is removed from the vat, “residual resin is washed off and depending on the material used, final material properties can be attained by photo/thermal processing”.
xolo is currently making its technology available to research organizations.
The Readily3D’s Tomolite printer
Readily3D’s flagship product is named Tomolite. With a compact unit of 30cm x 40cm x 60cm and a build volume of 10mm in diameter and 27.5mm in height, the CE marked can find its place on any or laboratory bench.
Described as ultra-fast and user-friendly by its inventors, the unit cant print “centimetre scale object, out of soft and hard materials, in a few tens of seconds with 40 um optical resolution.”
Valve, stained, Bone, stained, – images via Readily3D
Unlike the xube 3D printer that may require an additional photo/thermal processing stage, Readily3D claims that no post-processing is required beyond washing.
Speaking of the printing process, the company explains: “the resin is first poured into a cylindrical vial, which is then hand loaded in the printer. The STL file of the object to print is generated by a CAD program. The printer comes with the Apparite software, which allows for the loading and handling of STL files, as well as the configuration of dose settings and printing monitoring.”
To point out an application, the founders add: “our printer can shape light-sensitive bioresins into complex living constructs featuring vasculatures, pores and cavities that cannot be done with any other printers on the market with the same speed and resolution.”
The 3D printer can be purchased by companies and public institutions. As a matter of fact, some units are already installed in several research centres in Europe.
Main applications of volumetric 3D printing
Our exchange with experts reveals that main applications of volumetric 3D printing can be found in optics, dentistry, audiology, bioengineering, microfluidics and prototyping. In a nutshell, sectors of activity that will require rapid and scalable methods to create centimetre-scale cell laden 3D constructs.
Currently, Readily3D believes that the market is already ready for dentistry and audiology applications as they increasingly decentralize manufacturing by customizing directly the products in shops or in the practitioner’s office.
Although it is still at its infancy, the promise of volumetric 3D printing is obvious. The commercialization and possible applications shared by Readily3D and xolo show that the technology is ready to be put in action.
This exclusive feature has originally been published in the January/February issue of 3D ADEPT Mag.