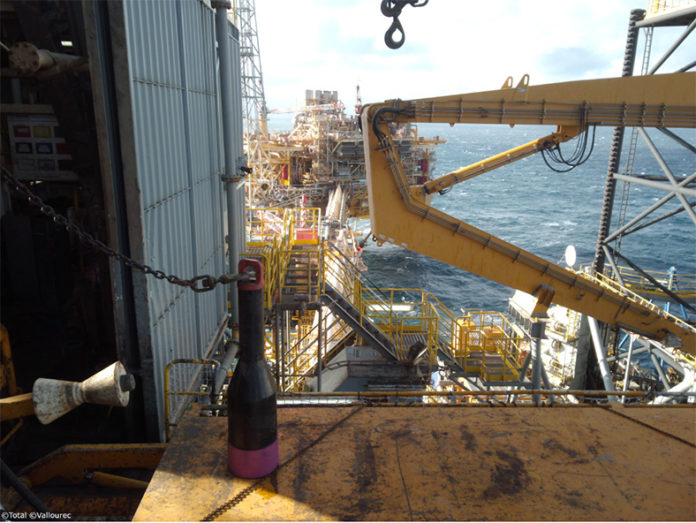
Vallourec, a multinational manufacturing company headquartered in Boulogne-Billancourt (France) has provided energy company Total with an additively manufactured waterbushing for the EIG Elgin-Franklin rig in the North Sea.
The production of this 3D printed waterbushing is a premiere for Vallourec and for the entire offshore energy equipment; a great application example that is worth mentioning as we are just one-day way from the Additive Talks panel dedicated to the use of AM in the energy industry. Produced using Wire Arc Additive Manufacturing technology (WAAM), the component has successfully passed usability tests on Total’s EIG Elgin-Franklin rig in the North Sea.
“This is the first time that a safety-critical component has been created using additive manufacturing in the Energy industry. It was essential for us to have the right partner and a good business case. Vallourec, as a longstanding partner, provided us with that confidence”, Edwige Ravry, Additive Manufacturing (3D Printing) Lead at Total Manufacturing notes.
Why is the choice of a reliable technology of paramount importance for this application?
To understand the reasons that led to Additive Manufacturing, and especially WAAM, we should first understand how waterbushings are utilized. According to experts, there are safety-critical components used in the oil and gas drilling industry to counter hydrocarbon kicks from wells in construction. Therefore, the components should deliver enough strength and reliability to avoid any failures that might result in equipment destruction.
To achieve this project, both teams have been working together for about a year. They performed intense testing of the part before its effective installation in February.
“The project came out of an open innovation collaboration with RAMLAB, a Rotterdam-based startup”, explains Bertrand Maillon, Additive Manufacturing Business Development manager at Vallourec. “The aim of this project was to go beyond Proof of Concept to successfully develop the Quality Assurance and Quality Control frame of supply for components using WAAM technology.”
As explained, WAAM technology is the metal AM technology that was leveraged as part of this production. This variation of Direct Energy Deposition technology uses an arc welding process to 3D print metal parts. Vallourec’s decades of expertise in welding, metallurgy and non-destructive examination as well as experience in threading, coating and pressure testing makes the company an ideal partner for such productions.
Among the many advantages that the technology allows, four main benefits have been highlighted for the production of this waterbushing: supply chain agility, lead time efficiency, lighter parts as well as low carbon footprint.
“Additive manufacturing enables us to move one step closer to the industry goal of a digital warehouse, increasing availability of crucial parts and reducing waste”, Bertrand Maillon, Additive Manufacturing Business Development manager.
While the part is around half the weight of components manufactured using conventional manufacturing processes, it should be noted that it also generated 45% lower emissions than those created through the regular forged and machining process, complying this way with Total’s sustainability goals. Indeed, Total aims to reduce by 60% or more the carbon intensity across its worldwide operations by 2050 or sooner (scope 1, 2 and 3, hence its investments in all sorts of innovation that may help reducing emissions and supporting the energy transition.
Remember, you can post job opportunities in the AM Industry on 3D ADEPT Media free of charge or look for a job via our job board. Make sure to follow us on our social networks and subscribe to our weekly newsletter: Facebook, Twitter, LinkedIn & Instagram ! If you want to be featured in the next issue of our digital magazine or if you hear a story that needs to be heard, make sure you send it to contact@3dadept.com