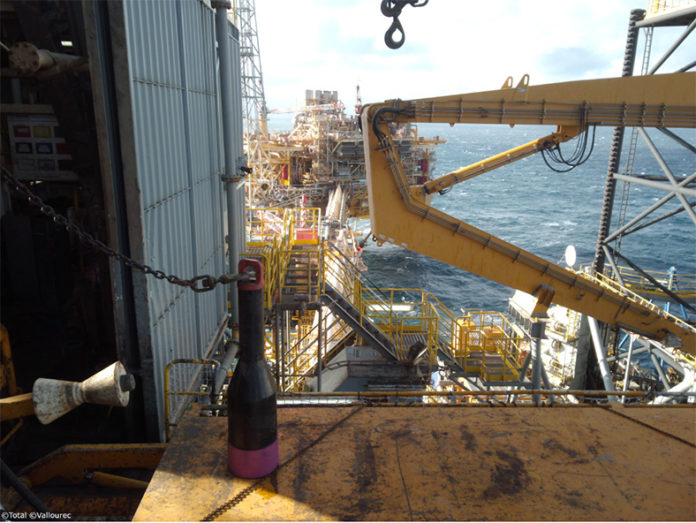
Vallourec, multinationale de l’industrie manufacturière dont le siège social est à Boulogne-Billancourt (France), a fourni à l’entreprise énergétique Total un waterbushing (composant sous pression) fabriqué de manière additive pour la plate-forme EIG Elgin-Franklin en mer du Nord.
La production de ce waterbushing imprimé en 3D est une première pour Vallourec et pour l’ensemble des équipements énergétiques offshore, un exemple important de noter alors que nous sommes à un jour du panel Additive Talks dédié à l’utilisation de la FA dans l’industrie de l’énergie. Produit à l’aide de la technologie de fabrication additive par arc électrique (WAAM), le composant a passé avec succès les tests d’utilisation sur la plate-forme EIG Elgin-Franklin de Total en mer du Nord.
« C’est la première fois qu’un composant critique pour la sécurité est créé par fabrication additive dans le secteur de l’énergie. Il était essentiel pour nous d’avoir le bon partenaire et une bonne analyse de rentabilité. Vallourec, en tant que partenaire de longue date, nous a apporté cette confiance« , note Edwige Ravry, responsable de la fabrication additive (impression 3D) chez Total Manufacturing.
Pourquoi le choix d’une technologie fiable est-il primordial pour cette application ?
Pour comprendre les raisons qui ont conduit à la fabrication additive, et plus particulièrement à WAAM, il faut d’abord comprendre comment sont utilisés les waterbushings. Selon les experts, certains composants critiques pour la sécurité sont utilisés dans l’industrie du forage pétrolier et gazier pour contrer les émanations d’hydrocarbures des puits en construction. Par conséquent, les composants doivent offrir suffisamment de résistance et de fiabilité pour éviter toute défaillance qui pourrait entraîner la destruction de l’équipement.
Pour réaliser ce projet, les deux équipes ont travaillé ensemble pendant environ un an. Elles ont effectué des tests intensifs de la pièce avant son installation effective en février.
» Le projet est né d’une collaboration d’innovation ouverte avec RAMLAB, une startup basée à Rotterdam « , explique Bertrand Maillon, responsable du développement de l’activité de fabrication additive chez Vallourec. « L’objectif de ce projet était de dépasser la preuve de concept pour développer avec succès le cadre d’approvisionnement en assurance et contrôle qualité pour les composants utilisant la technologie WAAM. »
Comme expliqué, la technologie WAAM est la technologie de FA métal qui a été exploitée dans le cadre de cette production. Cette variante de la technologie de dépôt par énergie directe utilise un procédé de soudage à l’arc pour imprimer en 3D des pièces métalliques. Les décennies d’expertise de Vallourec en matière de soudage, de métallurgie et de contrôle non destructif, ainsi que son expérience en matière de filetage, de revêtement et d’essais sous pression font de l’entreprise un partenaire idéal pour ce type de production.
Parmi les nombreux avantages que permet cette technologie, quatre avantages principaux ont été mis en avant pour la production de ce waterbushing : l’agilité de la chaîne d’approvisionnement, l’efficacité des délais, l’allègement des pièces ainsi qu’une faible empreinte carbone.
« La fabrication additive nous permet de nous rapprocher de l’objectif industriel d’un entrepôt numérique, en augmentant la disponibilité des pièces cruciales et en réduisant les déchets », Bertrand Maillon, responsable du développement commercial de la fabrication additive.
Alors que la pièce pèse environ deux fois moins que les composants fabriqués à l’aide de procédés de fabrication conventionnels, il convient de noter qu’elle a également généré 45% d’émissions en moins que celles créées par le processus habituel de forgeage et d’usinage, se conformant ainsi aux objectifs de durabilité de Total. En effet, Total vise à réduire de 60% ou plus l’intensité de carbone de ses activités mondiales d’ici 2050 ou plus tôt (scope 1, 2 et 3), d’où ses investissements dans toutes sortes d’innovations susceptibles de contribuer à la réduction des émissions et à la transition énergétique.
N’oubliez pas que vous pouvez poster gratuitement les offres d’emploi de l’industrie de la FA sur 3D ADEPT Media ou rechercher un emploi via notre tableau d’offres d’emploi. N’hésitez pas à nous suivre sur nos réseaux sociaux et à vous inscrire à notre newsletter hebdomadaire : Facebook, Twitter, LinkedIn & Instagram ! Si vous avez une innovation à partager pour le prochain numéro de notre magazine numérique ou si vous avez un article à faire connaître, n’hésitez pas à nous envoyer un email à contact@3dadept.com.