Over 75% of the 118 elements on the periodic table are made of metals. There are so many different types of metals, all of which depend on whether they are elements, compounds or alloys. In the non-exhaustive list of these materials, only a short group has the luxury to be processed by additive manufacturing technologies. Amid them, hardmetals seem to struggle to carve out a place in this niche market.
Often called cemented carbides or sintered carbides, – often written “hard metals”, hardmetals are simply composite materials that are made up of a hard phase embedded in a metal matrix. Their development within the additive manufacturing sphere is a hot topic right now and before we delve into its technical advancements, it feels right to clarify that their appellation often varies from one region to another. “In the US, the wording “cemented carbides” and “cermets” are often the most-widely used ones while hard metals or hardmetals are the preferred wording in Europe”, Dr. Johannes Pötschke, Group leader hardmetals and cermets at Fraunhofer IKTS told us from the outset.
However, with the goal of remaining faithful to its origins, we would keep the wording “hardmetals” in this feature – which comes from the German word “Hartmetall”.
Anyway, these pioneering powder metallurgical materials refer to a category of materials that are sintered, hard, and wear-resisting. They are based on the carbides of one or more of the elements tungsten, tantalum, titanium, molybdenum, niobium and vanadium, bonded with a metal of lower melting point usually cobalt. Here, Tungsten carbide-cobalt (WC-Co) remains the most widely used hardmetal. “It is an alloy of a hard ceramic phase, tungsten carbide (WC) and a ductile metallic phase, cobalt (Co). In other words, this metal matrix composite is made up of cobalt particles embedded in a tungsten carbide matrix”, Pötschke adds.
As their word implies, what might raise the interest in a specific hardmetal over another one is the level of hardness that it integrates – unlike soft metals that are characterized by their low hardness and ductility, becoming therefore the materials of choice for reducing friction and improving anti-wear ability as well as increasing equipment service lifetime.
Hardness is a vital property of hardmetals. It defines their ability to withstand localized permanent or plastic deformation, penetration, scratching or bending. This means that, a material with a high level of hardness will deliver a part that will present a strong resistance to wear. Other key properties for which they are known for, include toughness and strength. Research reveals that high hardness can reach up to 20 GPa, high bending strength up to 5000 MPa and high fracture toughness values up to 20 MPa*m1/2. Also, it should be noted that those properties can be attained if the three elements (tungsten, carbon and cobalt) are present in the two-phase state of tungsten carbide and cobalt alloy (WC-Co) and not in any possible the phase state. The route to achieve this, is therefore an entirely different matter.
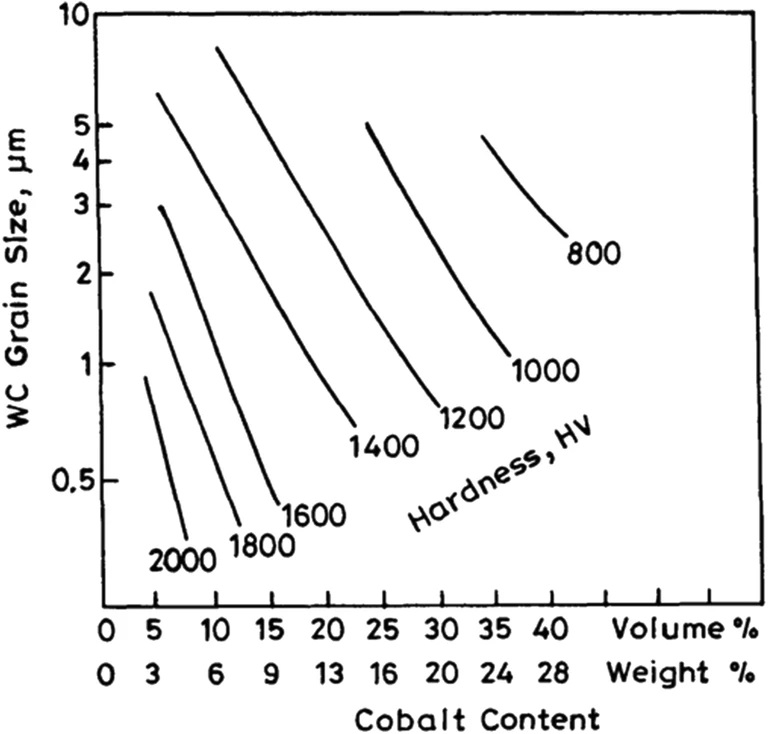
That being said, hardmetals have often been the way to go in traditional manufacturing. They are used to be processed by a standard Powder Metallurgy shaping process which delivers green parts first, that should undergo some post-processing before getting the desired part. (The manufacturing process is similar for some technical ceramics leveraged in AM).
Furthermore, when they process hardmetals by conventional pressing, operators cannot achieve parts with complex geometries, and the manufacturing process will still require some post-processing such as machining. In any case, there is often a chance that the operator ends up with a part that delivers low porosity. In AM on the other hand, the potential has yet to be unleashed, but given the capabilities that the technology enables across various fields of activity, organizations are currently exploring various routes that may lead to viable applications of hardmetals.
Types of AM processes that can process hardmetals – tungsten carbide-cobalt in particular.
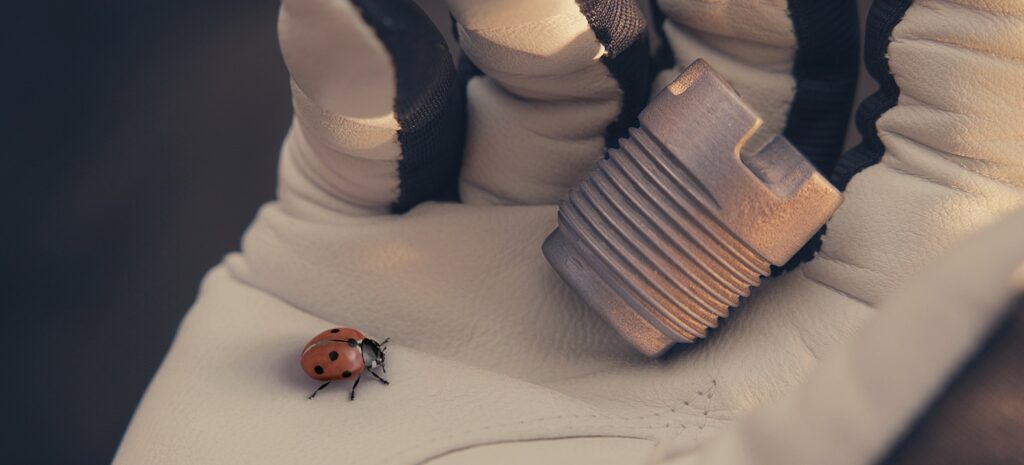
It’s easy to talk about AM in general because the same advantages tend to come back. What makes the conversation about AM captivating, is the nuances that may occur during the use of a specific AM process with a certain material, or for a given application.
Metals in general, are usually processed by selective laser melting (SLM), selective electron beam melting, laser powder deposition, binder jet 3D printing, and wire arc additive manufacturing (WAAM) to name a few. While stainless steels, Ni alloys, Ti alloys and some refractory metals & Al alloys are often the most highlighted in metal AM applications, it should be noted that tungsten carbide-cobalt still remains very challenging to be processed by AM technologies due to its very high melting temperature.
According to Dr. Johannes Pötschke, there are a lot of projects that are being conducted on the topic right now, and most of them involve the use of WC-Co hard metals on binder jet 3D printing and sinter-based AM processes in general.
Interestingly, with binder jet 3D printing, the “green part” obtained right after the manufacturing process can have enough strength to withstand the debinding step during which the polymer binder material will be removed before going on to a sintering process that will form a stronger and dense part. The only thing is that, given the fact that the manufacturing process requires a powder spreading step, the flowability is critical to the success of the printing operation.
Other additive manufacturing processes have been explored to process WC-Co hardmetals as well. They include SLM, Electron Beam Melting, 3D gel printing and FFF. While each of them presents its share of advantages and disadvantages, one thing we will keep in mind is that there are still a wide range of mechanical properties issues to address to deliver viable WC-Co 3D printed parts.
Indeed, in an AM production that involves WC-Co, density is a primary indicator for quality. Other indicators are related to the aforementioned main properties of hardmetals: hardness, fracture toughness and bending strength.
“The almost unavoidable defects, such as micro-cracks and porosities, and lack of dimensional accuracy, prevent AM processes from being widely used for producing WC-Co parts in the industry. Post-processing, such as heat treatment, hot isostatic pressing (HIP), infiltration, and machining, are often required, resulting in additional time and cost”, a research on “Additive manufacturing of WC-Co hardmetals” reads.
Currently, several material producers & OEMs have developed proprietary solutions that addressed these mechanical issues. Material producer Sandvik is one of them. The expert in hard materials has recently introduced 3D printed cemented carbide developed with a patented process. On the other hand, the company is also involved in GE Additive’s Binder Jet Beta program to advance the manufacturer’s beta H2 system into pilot lines. In the same vein, the latest company that joined this program is industrial technology provider Kennametal that will further advance the Binder Jet printing capabilities in cemented tungsten carbide. While waiting for these announcements to lead to fruitful results, we can already share the various advantages and disadvantages we might deal with, when processing WC-Co hardmetals with other AM processes.
AM Process | Advantages | Disadvantages |
Selective Laser Melting (SLM), also known as Laser Powder Bed Fusion (L-PBF) | High dimensional Accuracy High geometric freedom Less steps High hardness |
High residual stress Uneven microstructure Carbon loss and evaporation of Co. |
Selective Electron Beam Melting (SEBM) also known as Electron Beam Powder Bed Fusion (E-PBF) | High dimensional accuracy High geometric freedom Less steps High hardness High scan speed |
High residual stress Uneven microstructure Needs vacuum |
Binder Jet 3D Printing | Uniform microstructure High toughness Low cost Low residual stress No raw material loss |
High shrinkage Low hardness |
3D gel-printing | Low residual stress Uniform microstructure Low powder requirements No raw material loss |
Large shrinkage Low hardness |
Fused Filament Fabrication | Low residual stress Uniform microstructure Low powder requirements No raw material loss |
Large shrinkage Rough surface |
“In summary, the above five additive manufacturing processes can be divided into two types: selective melting process and shaping-debonding-sintering (SDS) process. Selective melting processes include SLM and SEBM, which make parts by melting powder with a heat source. This type of process is very simple and enables one-step molding. But sometimes post-processing is needed to eliminate stress and defects. The SDS process includes Binder Jet 3D printing, 3DGP, and FFF. The SDS type processes are characterized by forming a green part with organic compounds as binder and then sintering. Compared with the selective melting process, the SDS process is more complicated. Because SLM, SEBM, and BJT all contain a powder spreading step, all three processes require the powder to have good flowability. While 3DGP and FFF prepare powders as slurry and filament for printing, there is no need for powder flowability. The application of SEBM is limited by its very high equipment cost. SLM suffers from uneven microstructure, carbon loss, and evaporation of Co”, the research lays emphasis on.
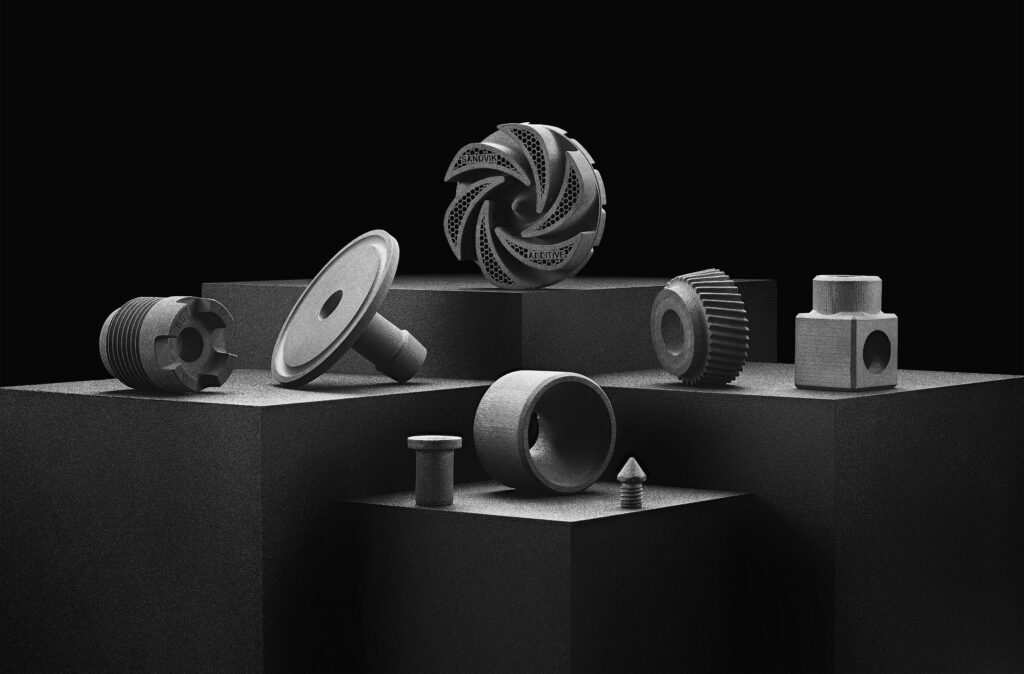
What about applications?
“There are currently no commercial applications made possible via AM and hardmetals. Most projects are being conducted right now for prototyping or research purpose. One notable advancement is that sinter-based AM processes are ahead of the curve since they can meet the stringent requirements of hardmetals [assuming that the operators know how to deal with concerns raised by material composition, production speed, accuracy and desired part size]”, Pötschke told 3D ADEPT Media.
That being said, the current lack of applications is indicative of the long route ahead to make tungsten carbide-cobalta viable commercial application with AM. This is all the more important given the fact that when used with conventional manufacturing processes, hardmetals are pivotal to various sectors such as agricultural, textile, metallurgical, mechanical, mining, aeronautical and aerospace and medical. They are often the best choice for fabricating valves, rollers, cylinders, plates, pins, blades, nozzles, or gears, etc.
Most importantly, in the medical and healthcare industries, Pötschke told us that hardmetals are mostly used with conventional manufacturing processes:
“Given the fact that they deliver the ideal [compromise between toughness and hardness], hardmetals are ideal for the fabrication of cutting tools. In the medical industry, they can serve applications in dentistry and bone tissue machining.” This might not be tungsten carbide-cobalt (WC-Co) buta few number of companies are using pure tungsten for medical 3D printing applications. DUNLEE is one of them.
If you are a regular reader of 3D ADEPT Media, you may have already discovered the company through our Opinion of the Week segment. In this exclusive feature, we have asked Jan Philippe Grage, Product & Business Development Manager 3D Printing at DUNLEE to answer a short list of questions that may help us understand how (fast/slow) this niche market evolves.
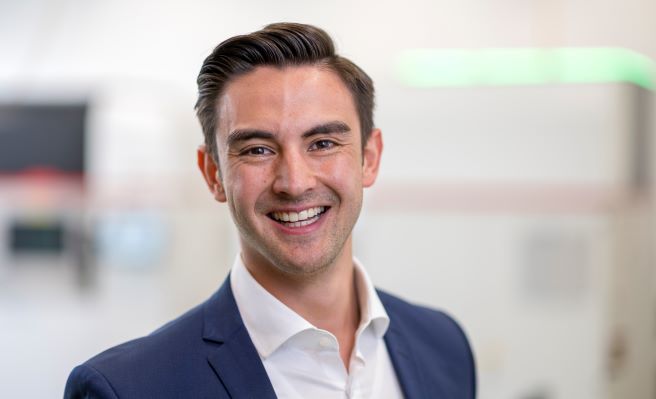
3DA: Has Dunlee only explored the use of tungsten for anti-scatter grids (ASGs)? (Are there any other applications?)
Our core business is anti-scatter grids and that is also what will be a driving force of our developments in the future. However, Dunlee is also actively providing components for other medical applications such as shielding windows or collimators for X-ray tubes. Going further we are also working on new applications outside of medicine, such as nuclear fusion, aerospace, automotive or even the mining industry. This is due to tungsten:
- high melting point making it ideal for extreme temperature environments
- High density making it ideal for radiation absorption or as a counterweight in small or complex geometries
- Long lifetime and resistance to corrosion
3DA: While there are many advantages to additive manufacturing with tungsten, there are obstacles to scaling the technology for mass production. In most cases it takes longer and is more expensive to make parts. How can we address this issue?
Indeed, there are cases where additive manufacturing is just not a fit in terms of price, scalability or even performance. Yet, there are still so many untapped opportunities where additive manufacturing can support production of components at volume, the right mix starting with part evaluation and design all the way to post processing need to be found. This takes time and effort but as can be seen with our major application, ASGs, is worth the development. Therefore, for companies entering these kinds of developments, they need to set the right expectations and understand that delays or even an unsuccessful investigation could be the result. When it comes to scaling, I believe a big element is finding the right partners. Partnering up within the AM field is key as many developments and potentials have not been unlocked yet, therefore you need partners across your value chain that constantly look to develop and invest the time required in order to continuously improve.
3DA: Are there any other hard metals the company has explored for medical 3D printing applications?
Till today, our strategy is to focus on pure tungsten and develop this niche metal industry. Of course, we receive requests for other refractory metals but we either managed to develop the application with tungsten or deemed the relation between that application and our capabilities a no match. We do however have it on our agenda to assess every new material opportunity that comes our way to see if there is a match.
3DA: Is there anything else you would like to share regarding the use of tungsten with AM?
For those looking into AM tungsten parts for the first time, do understand it is still not an easy task. We may be producing hundreds of thousands of parts a year but every new application has its challenges and for those new developments may be required. So do not shy away at hearing what needs to be developed first, the potential for tungsten in AM can save you costs, increase system performance or even a combination of both. What is increasingly being seen as well in the market is the opportunity to become more sustainable than with traditional manufacturing. With AM it’s possible to have much smaller supply chains and can close the loop on material usage/wastage. Especially in these times, where supply chain pressure is high and everyone is facing material shortages, recycling and circular economies are becoming that more important.
The dossier below has first been published in the May/June edition of 3D ADEPT Mag.
Remember, you can post job opportunities in the AM Industry on 3D ADEPT Media free of charge or look for a job via our job board. Make sure to follow us on our social networks and subscribe to our weekly newsletter : Facebook, Twitter, LinkedIn & Instagram ! If you want to be featured in the next issue of our digital magazine or if you hear a story that needs to be heard, make sure you send it to contact@3dadept.com.