By its very nature, additive manufacturing is considered a sustainable technology. The sustainable advantages of 3D printing could play an important, even decisive role for producers and manufacturers towards series applications. For material manufacturers like Evonik, living sustainability might not be so self-evident for everyone. But the more aware and transparent the sustainable journey becomes at the beginning of the additive value chain, the more impact these effects will have in the final application.
With a growing emphasis on environmentally friendly manufacturing, the evaluation of the environmental performance of additive manufacturing processes has gained attention. Additive manufacturing offers several sustainable advantages over other processing technologies: The design freedom of 3D components offers enormous potential for novel product developments and improvements in component efficiency and performance. New bionic lightweight structures enable the best possible design of functional elements, which are used as lightweight components primarily in the aerospace and automotive industries. Due to the general principle of all additive technologies of depositing material in a structured way instead of removing it, as in some other processes such as machining, 3D printing materials are used very efficiently. In the recent past, which unfortunately has been characterized by collapsed global supply chains for several reasons, additive manufacturing has been particularly effective: on-demand production of parts organized in a decentralized manner, is now a reality. That’s why 3D printing is often regarded as a sustainable processing technology.
“In our specialty chemicals business with high-performance materials, we don’t see the various processing technologies in any sustainability competition,” explains Sylvia Monsheimer, who heads the Industrial 3D Printing market segment t at Evonik. “People often tend to compare injection molding and 3D printing. But there is room for both on the market, and there are good reasons to rely on one or the other technology depending on the application, such as 3D printing for shorter product life cycles or injection molding for high-volume specialty parts.” In addition to the economic arguments, it is impossible to imagine parts production today without ecological aspects. When deciding for or against a processing technology, ecological influences such as sustainability in its many aspects or the various options for recyclability are considered in addition to costs per part.
For many market players like material manufacturers or technology providers, living sustainability might not be so self-evident for everyone. But the more aware and transparent the sustainable journey becomes at the beginning of the additive value chain, the more impact these effects will have in the final application.
As a specialty chemicals company with a presence throughout the world, Evonik, sees sustainability and long-term business success as two sides of the same coin. That is reflected in the rising demand from customers for products and services that demonstrate a good balance of economic, ecological and social factors. Sustainability has long since developed into a growth driver for Evonik.
Sustainable 3D printing starts with the right material
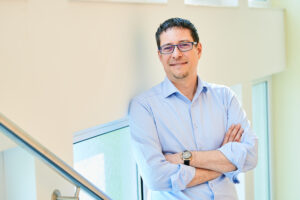
Yet material manufacturers bear a great responsibility here because the sustainable result of an application stands or falls with the sustainable performance of the materials used. “Sustainability is the core element for being successful in the future. We understand sustainability as a key growth driver and the cornerstone of our product portfolio, investments and innovation management. Sustainability is therefore an integral part of Evonik’s strategy.”, says Dr. Dominic Störkle, Head of the Additive Manufacturing Innovation Growth Field at Evonik.
At Evonik, the polymer experts take a holistic view on sustainability based on four main cornerstones:
- Improving reusability rates
- Reducing carbon footprint
- Saving fossil resources
- Recycling
Alongside factors such as production efficiency or the reusability of materials, their sustainability approach includes the total life cycle assessments of materials and their consistent improvement. The specialty chemicals company looks not only at carbon footprint but also at other important factors such as water consumption and land use. Using green energy and renewable or recycled feedstocks for production, Evonik significantly improves the overall eco-balance of their materials and work on end-of-life opportunities for the group’s polymers.
Improving reusability rates
Evonik already offers its first new PA12 grades which can be reused by only replacing the powder needed for the parts of the previous job which avoids material waste in production according to the group’s ZERO WASTE approach. Furthermore new powder materials are being developed to increase their reusability rate during a 3D printing process.
Reducing carbon footprint
In October, last year, Evonik introduced a new grade of PA12 powders with significantly reduced CO2 emissions. The new PA12 powders will replace the previous INFINAM® polyamide 12 materials for all common powder-based 3D technologies such as SLS, HSS or MJF. The new sustainable INFINAM® PA12 powders are produced using renewable energies at the Marl Chemical Park in Germany. TÜV Rheinland has certified the associated life cycle assessments, confirming an improvement in the company’s own carbon footprint of almost 50 percent. In the overall life cycle assessment, the comparison of the new sustainable material grade is positive even compared with the castor oil-based polyamides of Evonik’s own Terra range.
Saving fossil resources
Evonik is also working to expand its range of sustainable PA12 powders to include the INFINAM® eCO product line. “eCO” stands for the company’s goal of avoiding the greenhouse gas carbon dioxide by using renewable or circular raw materials via the mass balance approach. Mass balance involves mixing virgin fossil and renewable or circular raw materials into existing systems and production processes. The renewable amount is then allocated mathematically to specific products and is certified by a neutral third party to verify the use of renewable or circular resources across all stages of production. Mass balance is a way to keep track of the renewable or circular quantities throughout the process and allocating them to specific products. It allows for large-scale production and enables cost-effective solutions that meet more stringent environmental and sustainability targets. The market launch of INFINAM® eCO is planned for this year.
Recycling
In addition, Evonik also work on end-of-life opportunities for polymer-based 3D applications.
Additive manufacturing is an emerging manufacturing technology for parts. With a growing emphasis on environmentally friendly manufacturing, the evaluation of the environmental impact of additive manufacturing processes is crucial for choosing case by case the most efficient and sustainable technology for parts production. Life cycle assessment is an important tool to compute the environmental impacts of 3D printing processes. By developing new sustainable high-performance materials, Evonik wants to drive 3D printing as another important manufacturing technology for series production to coexist with injection molding, extrusion and machining in the future. For this, the right materials must be used from the start.