In an industry where one of the major issues consists in reducing “product-time-to-market” cycles, additive manufacturing is often directly categorised as a technology that enables faster production compared to conventional manufacturing processes. Yet, for certain applications such as mould tooling – which is pivotal for the development of many products -, certain AM processes are not only costly, but are as long as conventional machining, not to mention that they will still require the operator to perform some machining before obtaining the final 3D printed part.
Interestingly, another alternative recently came onto the market, an alternative that would provide a more interesting bet in terms of tool lead times and product-time-to-market; an alternative that is based on metal pastes.
Mantle, a San-Francisco based-startup that recently turned stealth mode off, following a secret fundraising of $13 M, brings this intriguing concept onto the market. With a technology solution named TrueShape, the company decided to solely focus on the tooling market (for now); a specific interest, that is perfectly understandable when one knows the background and expertise of the founders. At the end of the day, your experience often determines how you will shape the future, right?
Well, Mantle has been founded by Ted Sorom (CEO) & Steve Connor who are respectively mechanical design engineer and chemist by training. Although the company officially made entered the market on February 2021, it should be noted that Sorom and Connor have founded it over five years ago.
Their respective professional experiences led to the development of TrueShape to the extent that from the very beginning of his career, Connor built up expertise and decided to specialize in nanoparticles and metal pastes. He has even developed a successful “lower-cost replacement for the expensive silver metal pastes used in the solar industry.” “He then shifted gears to see if similar technology could be used for additive manufacturing”, Sorom told 3D ADEPT Media.
The focus on the tooling market can be explained by the fact that its size was valued at $212,500.0 million in 2020, and is projected to reach $439,994.9 million by 2030, registering a CAGR of 7.5% from 2021 to 2030. Beyond these figures, let’s note that Sorom has also gained extensive experience in the field. Indeed, right after he obtained his degree, he “joined a vertically integrated company that made high-end equipment using CNC machined metal and injection molded plastic parts.”
“I designed the parts and molds upstairs and then went downstairs and made the molds before putting them into full production. I saw first-hand how time-consuming and expensive the toolmaking process was for even a simple plastic part. Our new product launch schedules were gated by tooling. Unfortunately, my experience is not unique; almost every manufacturing company struggles with these same challenges. At Mantle, we’ve focused our efforts on addressing these challenges”, he recalls.
Understanding the backbone of the manufacturing industry
Often considered as the backbone of the manufacturing industry, tooling involves the designing and manufacturing of tools required for bulk production of parts, parts that may involve the fabrication of moulds and dies (presses), forging, gauging, jigs & fixtures, and cutting tools, all of which are useful to produce other parts for cars, turbines, propellers, to name a few.
As the design and fabrication of these tools directly affects the production quality of the end-user industry, the choice of the manufacturing process leveraged here is of paramount importance. “Tooling applications require outstanding surface finish and a high degree of accuracy”, Sorom points out. To deliver such rendering, Mantle decided to combine the best of both worlds: traditional machining and additive manufacturing.
Most importantly, as far as AM is concerned, the founders see an opportunity here for this technology to make a big impact on high-volume production of products.
TrueShape
Historically, fabricating tools using a traditional manufacturing method often requires a multi-step process that includes programming, cutting, and finishing the tools – a process in the end that can take several months rather than just a few days with the dedicated AM technology.
Mantle’s hybrid bound metal printing works by extruding a proprietary metal paste before refining the part surface via traditional subtractive machining. For those who are not familiar with them, please note that metal pastes are often used to fill the dent over any metallic and solid surface and also for fixations of granites and other allied industries. Usually, a resin and hardener are combined to create a durable, high-strength bond that dries in minutes and can be used for repairing, filling, and rebuilding all metal and concrete surfaces.
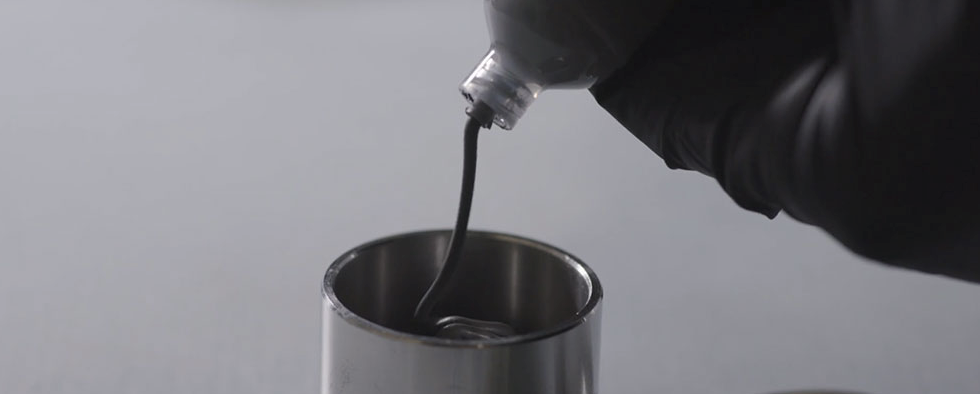
In Mantle’s case, the paste consists of metal particles and liquid carriers, which one extrudes to build up the parts layer-by-layer.
“Then we heat and dry the paste inside the printer, which removes the liquid carrier and leaves a “green body” that is relatively soft and can be machined quickly and easily. The machining creates the accuracy, surface finish, and fine features needed for precision parts like moulds. The final step is a sintering step, which is important because it fuses the metal particles and establishes the final material properties. We sinter in a high-temperature furnace that brings the parts’ temperature to just below the material’s melting point, and then cools it off. When the parts come out of the furnace, they are high-hardness tool steels with extraordinarily smooth surfaces that can go directly into injection mould tooling applications with no post-processing of the mould surfaces”, the CEO told 3D ADEPT.
Based on the company’s explanations, the main difference with other AM processes lies in the post-processing stage. It is no secret that this stage of the production cycle often takes more time than the manufacturing stage itself, and is even more expensive than manufacturing a part. TrueShape ambitions to drastically reduce or even remove this stage, when necessary.
There is not much to say if we compare it to conventional manufacturing processes. However, we do know that this technique seems advantageous to some AM processes which highlight design advantages such as conformal cooling. Indeed, Mantle’s process seems to go beyond these advantages, as it can also provide some sort of material uniformity during the process which is pivotal to achieve reproducibility of parts.
This is mainly due to the way the Flowable Metal Paste is distributed, to create stronger microstructures directly in the end-3D printed part. So far, Mantle has developed two steel materials that are comparable to very common tool steels, P20 and H13, for the specific needs of the tooling industry.
To illustrate the capabilities of their technology, Sorom mentioned the example of a global medical device manufacturer that used TrueShape to fabricate cavity and core tool-steel mould inserts. Using the hybrid metal printing process, this company successfully moved its production from 7 weeks to 8 days, and reduced costs by over 50%.
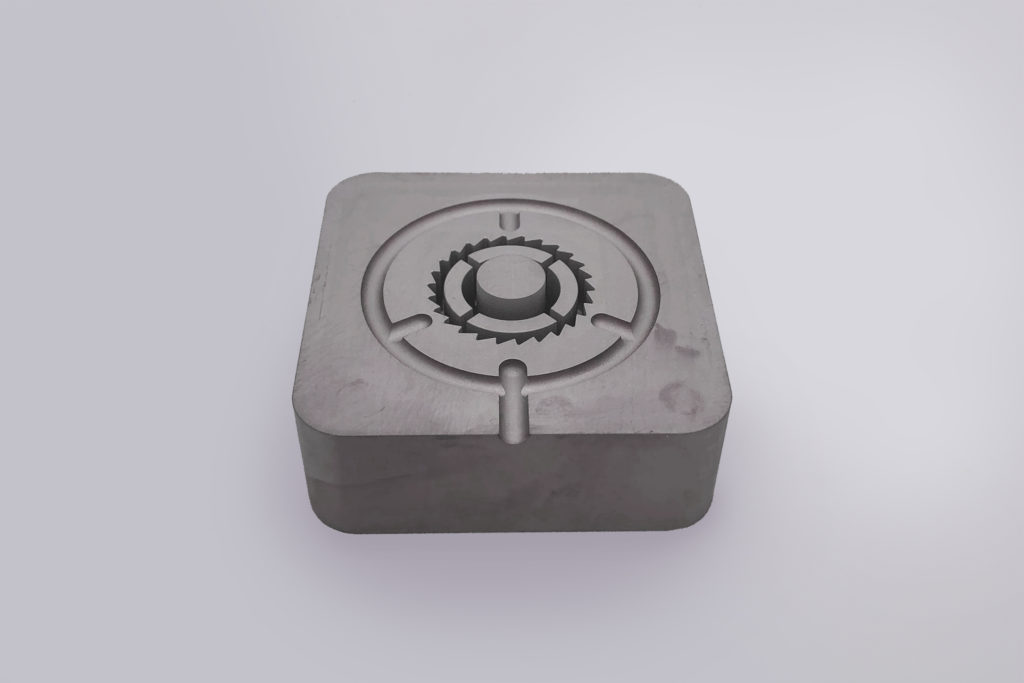
The next step in the pipeline
Mantle’s first goal is to demonstrate how TrueShape is capable of making precision components with a key focus on tooling as first application. Moving forward, the company expects their customers to find all sorts of uses for this technology.
“Other application areas include precision jigs and fixtures and low volume / spare parts for industrial applications”, the CEO notes. “We also anticipate that, several years from now, our technology will be qualified for end-use medical, aerospace, and automotive applications”, he completes.
Lastly, as a young machine manufacturer, we might expect Mantle to develop new materials, faster printing processes, and larger build envelopes but what we can’t wait to see right now, is the shipment of their first systems, as it often marks a real positioning on the international stage of the industry.
This exclusive feature has first been published in the July/August edition of 3D ADEPT Mag.
Remember, you can post job opportunities in the AM Industry on 3D ADEPT Media free of charge or look for a job via our job board. Make sure to follow us on our social networks and subscribe to our weekly newsletter : Facebook, Twitter, LinkedIn & Instagram ! If you want to be featured in the next issue of our digital magazine or if you hear a story that needs to be heard, make sure you send it to contact@3dadept.com