Au printemps de l'année dernière, le Composites Manufacturing Simulation Center (CMSC) de l'université de Purdue et Thermwood Corporation ont annoncé la création d'un laboratoire de fabrication additive à grande échelle pour mener des recherches financées par l'industrie sur la fabrication additive thermoplastique composite à grande échelle.
Le CMSC concentre essentiellement ses domaines de recherche sur la simulation et la validation de la fabrication des composites, la fabrication additive des composites ainsi que la mécanique du génome des structures. Le centre de recherche est soutenu par une communauté de composites en ligne (le cdmHUB – qui signifie Composites Design and Manufacturing HUB -) qui contribue à la certification par l'analyse en développant et en diffusant les meilleures pratiques de simulation et par l'éducation et l'évaluation des outils de simulation des composites.
Thermwood, quant à lui, est un fabricant de machines CNC diversifié, multinational et basé aux États-Unis, qui est devenu l'une des principales références en matière de systèmes de fabrication additive à grande échelle pour les moules, les outils et les modèles en composite thermoplastique.
Un an plus tard, les partenaires partagent les résultats de l'un des projets qui les a occupés depuis l'annonce. Le projet consistait à concevoir, prototyper, tester et fabriquer des structures de support en composite pour les expériences CMS et ATLAS du Grand collisionneur de hadrons (LHC) du CERN. Ce projet s'inscrirait dans le cadre de la mise à niveau de la haute luminosité du collisionneur de particules, dont la mise en place des parties finales est prévue pour 2026-27.
Comme annoncé l'année dernière, les partenaires ont utilisé l'imprimante additive LSAM 105 de Thermwood et à la toupie LSAM Trim à cinq axes pour l'impression et l'usinage rapides à grande échelle de dispositifs de réglage pour les structures tubulaires composites de haute précision.
L'imprimante additive LSAM 105 est composée d'une table mobile et d'un portique fixe unique (10'x 5' Moving = 25 x 12 cm) qui peut fabriquer des composants avec une hauteur d'impression maximale de 4' (10 cm). Compatible avec des têtes d'impression de 40mm, la machine peut atteindre une température maximale de 450°C avec une cadence d'impression de ≈ 100 lbs/hr (45kg/hr).
Le portique de découpe ou soustractif est un système de toupie CNC à cinq axes équipé d'une broche à changement d'outil automatique de 12HP (3 000 à 24 000 tr/min) et d'un changeur d'outil automatique à dix positions.
L'équipe du projet a imprimé en 3D le dispositif d'ébarbage d'un mètre de long et d'un rayon de 208 mm sur le LSAM en utilisant de l'acrylonitrile-butadiène-styrène (ABS) renforcé par 20 % en poids de fibre de carbone. Avec l'achèvement réussi de ce prototype de 914 mm de long du tube de support interne du tracker de mise à niveau du CMS, l'équipe est suffisamment confiante pour effectuer les tests de ses composants structurels et de détection.
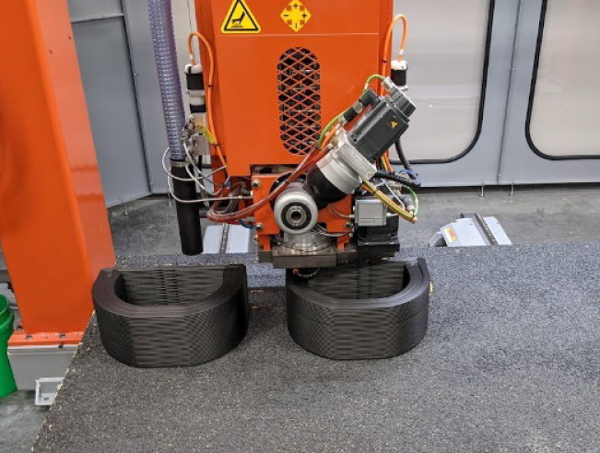
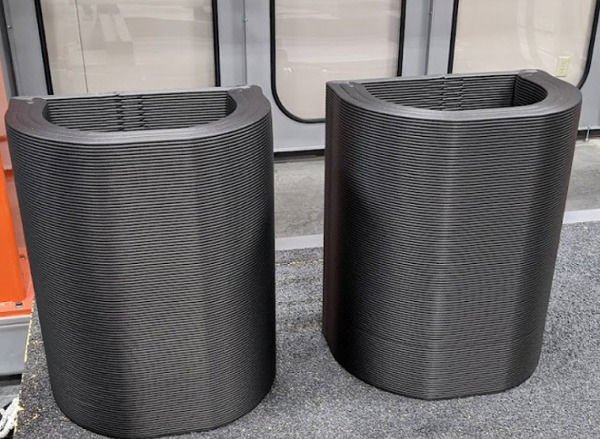
Selon Thermwood, les composants individuels installés dans ce tube de support doivent être positionnés avec une précision de +/- 0,5 mm ou moins, de sorte que l'usinage précis des caractéristiques d'interface est essentiel. Ce type de précision à grande échelle est rendu possible, économique et pratique à l'aide de systèmes comme le LSAM.
Comme les surfaces critiques seraient usinées ultérieurement, et pour augmenter la vitesse de production de la géométrie prismatique, l'outil a été divisé en deux segments imprimés verticalement. Les moitiés ont été collées avec de l'adhésif et des goujons pour assurer la solidité et la stabilité des joints, explique l'entreprise sur son site Web.
Il est intéressant de noter que le projet révèle l'importance de combiner la FA et l'usinage pour obtenir les meilleurs résultats possibles.
En effet, après avoir usiné les faces qui allaient devenir la base du dispositif d'ajustage, ils ont utilisé le dispositif imprimé et usiné pour ajuster les bords de la pièce composite, percer des trous d'interface et, avec les surfaces d'accouplement usinées à plat, ils ont fabriqué un joint en écharpe pour joindre les deux demi-cylindres. Les moitiés de composite découpées avec précision ont ensuite pu être collées ensemble.
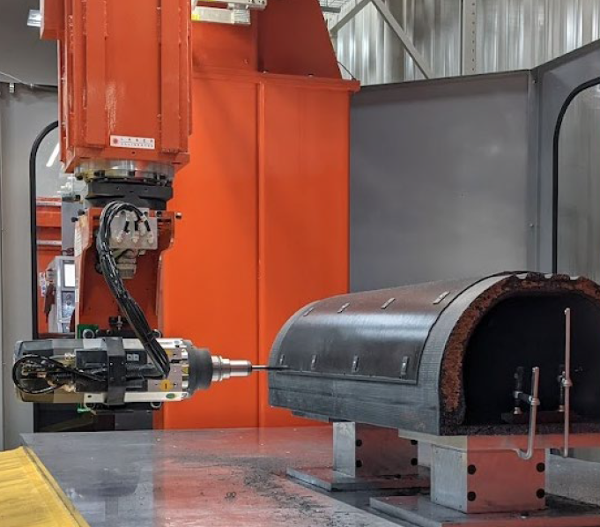
Le résultat final révèle un tube de 3,2 m de long capable de supporter une masse de 140 kg tout en ne permettant que des déviations inférieures au millimètre.
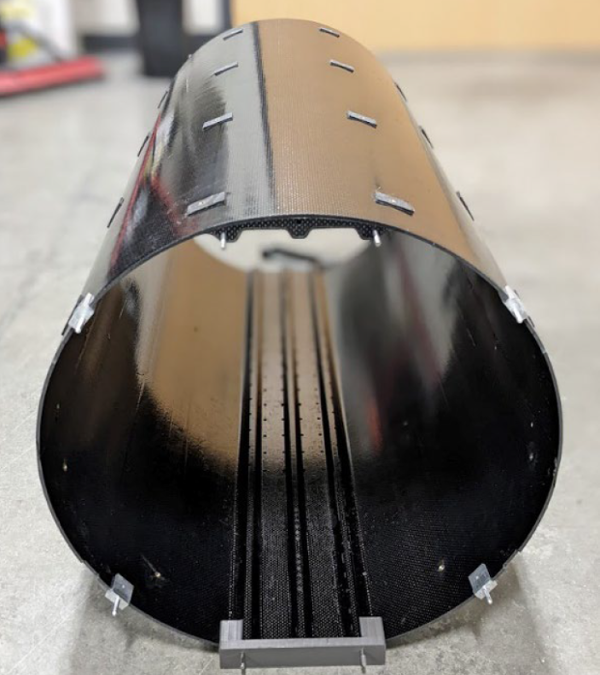
On peut s'attendre à ce que l'équipe Purdue CMSC/PSDL conçoive, fabrique et teste d'autres structures de support composites pour la mise à niveau du LHC du CERN, des structures aussi petites que des feuilles de 0,5 mm et aussi grandes que des tubes de 2,4 m x 5 m en panneaux sandwich. Espérons que la fabrication additive à grande échelle fera toujours partie des projets, car c'est un bon moyen d'explorer les diverses capacités des solutions de Thermwood.
N’oubliez pas que vous pouvez poster gratuitement les offres d’emploi de l’industrie de la FA sur 3D ADEPT Media ou rechercher un emploi via notre tableau d’offres d’emploi. N’hésitez pas à nous suivre sur nos réseaux sociaux et à vous inscrire à notre newsletter hebdomadaire : Facebook, Twitter, LinkedIn & Instagram !