With key examples on medical 3D printing.
Most of the time when we talk to an additive manufacturing user, one of the challenges that keeps coming back when using additive manufacturing is the post-processing stage – powder removal in particular. Whether they are in the aerospace, consumer goods or medical industry, users want to be able to perform powder removal easily and perfectly. The irony here is that when additive manufacturing was not mature enough, users complained about the fact that they performed this task manually – which in the end took too much time and was expensive – but with the current maturity of the technology, users have understood the need for a machine that can do it for them, yet continue to complain. Does the current challenge lie in the lack of the right technical features within these machines? Let’s put it like this: what are the technical features that will enable a powder removal machine to do the job well?
Powder removal is probably the most critical first step in the post-process chain of a finished part, especially for metals. This is because metal AM parts will frequently have heat treatment, and any residual powder will either be sintered to the outside, or worst still inside the part itself. Once that happens it’s virtually impossible to remedy the part and it would be scrapped. For medical parts especially, and other critical use parts, the very last thing anyone wants, is residual sintered powder anywhere on the parts.
As you may guess, this stage of the manufacturing has raised a number of challengesthat OEMs have done (and are doing) their best to overcome. Interestingly, as these are increasingly being addressed, the solutions found contribute to position AM as a serious manufacturing process for industrialization, and regulators, quality assurance managers and legal units are more eager to pay attention to other risks that may arise.
These challenges are mostly highlighted in laser powder bed fusion machines which are also the most widely used metal AM processes across industries. Let’s remember that, although they are often mentioned across other manufacturing steps of the AM production, safety and health issues cause the greatest concerns during the “depowdering” process where operators might be in direct contact with the powders. Risks of explosion, costs, powder recovery, cleaning quality and process repeatability complete this list and explain the shift towards regulation and standardization. That being said, we have to recognize that human exposure to metal powders is a risk that most organizations cannot handle yet. Standards currently available do not always address all safety concerns. Most of the time, it is the responsibility of the user of this standard to establish appropriate safety, health, and environmental practices and determine the applicability of regulatory limitations prior to the use of a powder removal machine.
So, what are the technical features that will enable a powder removal machine to do the job well?
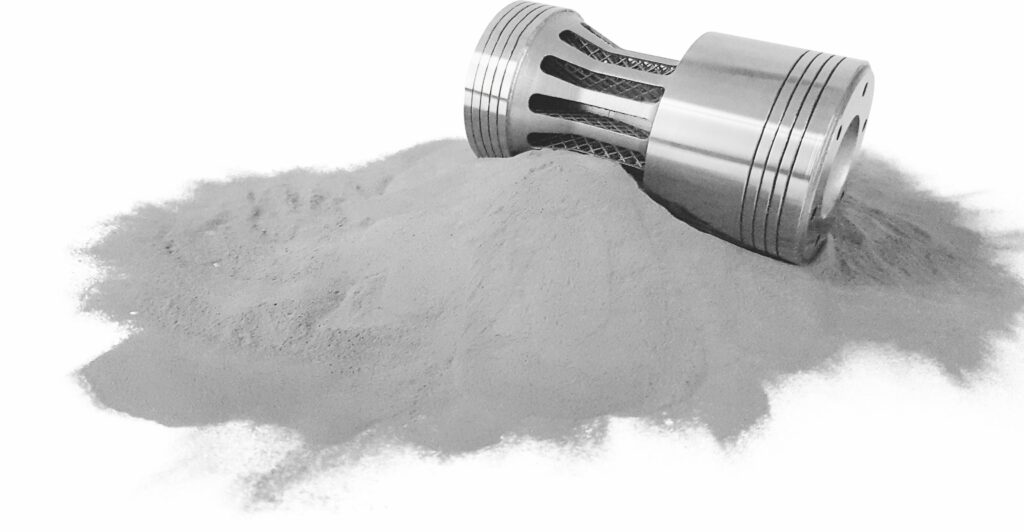
The first thing that one should understand here is that powder removal can be a very meticulous task, and when carried out manually, it can involve multiple steps to continuously check and inspect the part.
Automating powder removal can provide many advantages in this respect. As a matter of fact, an automated process is a very good support towards the possibility to validate a depowdering process. It provides consistency and greater control.
This is especially a need for regulated industries such as the medical device sector. By having a supply chain step allowing an operational reproducibility, you will get a good base to assess your powder removal performance accurately.
At the end of the day, once a process has been defined for a particular part this can be reliably repeated over and over again with a high level of confidence that the result will be the same.
As far as features are concerned, it’s interesting to assess the powder removal machine’s ability to not only remove residues in an effective way, but to also apply different strategies if and when required. A clear depowering parametrization should allow to get optimal results in the long term.
We can never stress this enough: powder removal systems must be able to adhere to strict health and safety guidelines associated with handling fine powders. In this regard, they should be equipped with an enclosed working chamber. The addition of using inert gases for atmosphere control is also an important feature.
In terms of the actual operation, a very simple technique that has been used to great effect during manual powder removal involves simply weighing the part. So the ability to monitor the weight of the part by comparing the calculated weight with that in the equipment would be a key function.
However, any automated equipment must have a flexible configuration since they will be required to work with many different part geometries. The ability to add tools to end of arm robotics, and the ability to program the movement of the part inside the chamber are also essential.
With the possibility of trapped powder inside parts, it is very important to study the optimized path inside the movement space of the equipment that will enable that powder to flow freely and find an exit point. For this, systems that are able to interact with 3D CAD models and interpret the optimum path would provide excellent solutions. Sometimes, extra effort is required and the use of fine point tools, gas injectors and other implements that attach to robotic arms would be very desirable, especially when dealing with medical parts that may have bone ingrowth enhancing mesh structures on their surfaces.
With only a handful of companies offering automated powder removal machines, we came to realize that some functions are increasingly demanded by operators.
The most-sought after features in a powder removal system | Description/remarks |
Table size | Varies from one system to another |
Vibration of the build plate | Adjustable and/or programmable vibration frequency |
Access to large parts (optional) | Easy crane loading from the top of the machine/back entry for robot-loading system integration |
Rotation of the build plate | Freedom of rotation allows for reaching and cleaning stuck powder inside support structures or internal channels; |
Inert gas capability | Prevents explosion risks |
Programmability & automation | Allows for predictable & repeatable cleaning results |
Compressed air or gas | ventilator system | This helps avoid ejecting particulate matter into the atmosphere. Prevents windows from getting dusty |
Glove access/ blow off gun | |
Ionization unit | Reduces static electricity |
Cyclone | Blasts media cleaning |
Sealed dust bin | Collects dust from the filter |
Needless to say that each application is unique, and may therefore have its own requirements; which is why we recommend to look at the ins- and outs of your project: the environment, the appropriate equipment and even the final purpose after the removal of powders.
What about savings?
The question of savings increasingly becomes of paramount importance in a context of sustainability. This raises several other considerations regarding production, purchase, and the viability of the powder that we have addressed in a previous feature.
As of today, it’s difficult to put an actual value on savings because it depends on whether one is considering the reduced time to process a set number of parts, in a consistent and reliable way, compared to the equivalent manual operation, or whether one also wants to factor in the reduced likelihood of having any reject parts further down the process chain. A single scrap part due to unseen trapped powders could have associated costs that run into the tens of thousands of pounds/euros/dollars. Furthermore, an automated system would actually introduce cost to any operations from the capital investment, running costs, and overheads including maintenance, and these need to be factored into any cost saving analysis.
When we look at medical 3D printed parts for example, we might quickly observe that a performant depowdering will avoid issues along the subsequent supply chain steps such as heat treatment, post machining or surface treatment. This will also decrease risks related to powder contamination on final devices. Moreover, quantifying the savings of a patient infection due to powder residues on implants is not an easy task. It is however clear that we should do everything we can to reduce this risk.
Concluding thoughts
Powder removal solutions remain relatively new hence the small number of OEMs that currently deliver solutions in this regard. (You may have a look at the 2022 International Catalogue of AM Solutions to discover some of the latest solutions available on the market for this task). Anyway, one thing we can easily agree on is that there is not yet a defined guideline to the use of depowdering. The reason for that is that holistic experiences are often the way the industry learns the most about this stage of manufacturing. This means, every project should be assessed separately to get an optimal result.
The most important consideration has to be whether it makes sense or not to employ these solutions, since using automation for some parts may just be overkill, and may end up providing no real benefit to the business.
As for specifications, the AM world is a fast moving sector right now and there are an ever growing list of draft and approved specifications to govern everything from selection of powders, qualification of equipment, and certification of final parts. In the medical industry especially, the ASTM F 3335-20 standard gives a good guidance for residue removal. Lastly, all aspects of biocompatibility should be assessed according to the ISO 10993 standards.
This dossier has first been published in the May/June edition of 3D ADEPT Mag.
Authors The writing of this exclusive feature has been led by Kety Sindze, Managing Editor at 3D ADEPT Media. Two other experts with different backgrounds assist in the preparation and writing of this article. Nicolas Bouduban, CEO & Founder of Swiss m4m Center AG, an additive manufacturing center for medical applications that promote the development and usage of 3D printing by focusing on all process know-how in a validated environment. Email: nicolas.bouduban@swissm4m.ch / Tel: +41 79 601 32 38 Dr. Martin McMahon, Additive Manufacturing Consultant that brings over a decade of experience in nearly all aspects of the metal AM sector from the supply chain through to full production parts manufacturing. Tel: +44 7923 475565 / Email: Martin.McMahon@MAMSolutions.uk