A couple of years ago, I took part in a MedTech conference in Eindhoven (The Netherlands) where I accidentally stumbled upon a book that read: “modern medicine was no accident, except when it was. The history of medical innovation, which spans centuries, is filled with killer diseases, scientific inquiry, accidental discoveries, and brilliant machines.” It was true, sad, and kind of heroic. Don’t ask me why, that’s what I thought. So yes, during the past decades, medical technology advances have changed the practice of medicine. Whether we talk about mind-reading exoskeletons, 3D-printed drugs or implants, those innovations are coming to healthcare almost every day and it turns out – they ultimately want to address a challenge that stands the test of time: the need for more personalized care.
Needless to say that the timeline of milestones achieved in medical technology will vary from one expert to another, and most importantly, will depend on everyone’s field of expertise and/or area of interest. When we look at AM/3D printing for instance, one realizes that the technology was first used for medical purposes as dental implants and custom prosthetics in the 1990s but we had to wait until the 2000s when patents related to the technologies, started expiring to see a growing exploration of the technologies across medical applications and other fields of activity.
“In the 90s, 3D printed anatomical models gave the first opportunity to better plan surgeries. As an example, conventionally manufactured jaw plates for tumor treatments were adapted to the anatomy using 3D-printed plastic models. This resulted in more efficient surgery for the patient“, Nicolas Bouduban, CEO of medical technology company Swiss m4m Center, comments.
Fast forward to today: the healthcare segment is shaping up with advances in digital healthcare technologies, such as artificial intelligence, VR/AR, 3D printing, robotics or nanotechnology, and among these technologies, the strides made in AM often outshine the limitations that still needed to be addressed by medical device manufacturers.
This article aims to highlight what enables AM to stand out from the crowd on a market cluttered with various digital healthcare technologies. With a key focus on depowdering equipment, it will discuss how these “brilliant machines” fit into this evolution, as well as the limitations that are still raising concerns among medical device manufacturers.
It’s about the small steps
We don’t often realize how far we have evolved until a milestone is celebrated. Remember, six years ago, when we first discussed with automated powder removal expert Solukon, they made us realize that post-processing was considered a modest priority by manufacturers, yet it was the stage that often increased the final cost of the 3D-printed part. Over the years that followed, we dedicated time to understanding the ins and outs of this process; we shed light on the reasons why we believed post-processing in additive manufacturing of medical parts is a matter of liability, but we eventually failed to understand why this awareness process took a little longer in the medical field.
For Andreas Hartmann, CEO/CTO of Solukon, the reason is first and foremost a question of size and complexity. While he recognized that medical device manufacturers are increasingly aware of the importance of automated powder removal, “the fact that this learning process took a little longer than in other industries (e.g., aviation) is because, at a first glimpse, medical devices seem not that challenging to depowder compared to complex, heavy and huge heat exchangers or rocket propulsion components.”
For our expert, three main reasons have truly fostered the need for automated depowdering solutions:
- The numbers of additively manufactured parts and the cost pressure in the medical industry that require an automated instead of a manual depowdering solution are steadily rising.
- In the medical industry, production needs to be on demand and fast. Automated depowdering ensures leaner and faster postprocessing which contributes to a faster overall manufacturing process.
- MedTech is a strictly regulated industry. This results in high requirements for transparency and traceability of the entire manufacturing process, including the depowdering process. Not to mention that manual powder removal procedures are not at all sufficient here.
If you wondered what automated powder removal solution was trending at the time, let me tell you now, it was the SFM-AT200 – an affordable system developed by Solukon. Like any technology developer, Solukon has upgraded and diversified its portfolio. Today, a machine called SFM-AT350 is also suitable for medical 3D printed parts.
“The SFM-AT200 is still an ideal candidate for the medical industry. The system has a very small footprint and therefore also a small process chamber that is filled up with inert gas in under two minutes. It can depowder parts with dimensions up to 300 x 300 x 230 mm and is equipped with one automated rotation axis and manually adjustable frequency excitation. The SFM-AT200 is the right system to depowder rather small, medium-complex parts and a very cost-effective automated depowdering solution.
In comparison, the SFM-AT350 offers enhanced freedom of motion with a two-axis rotation (endless on the rotation plate, 250 degrees on the horizontal axis), a bigger process chamber (for parts up to 350 x 350 x 420 mm) and -even more importantly- all features for process monitoring (Digital-Factory-Tool) and automation integration (OPC UA)“, Hartmann outlines.
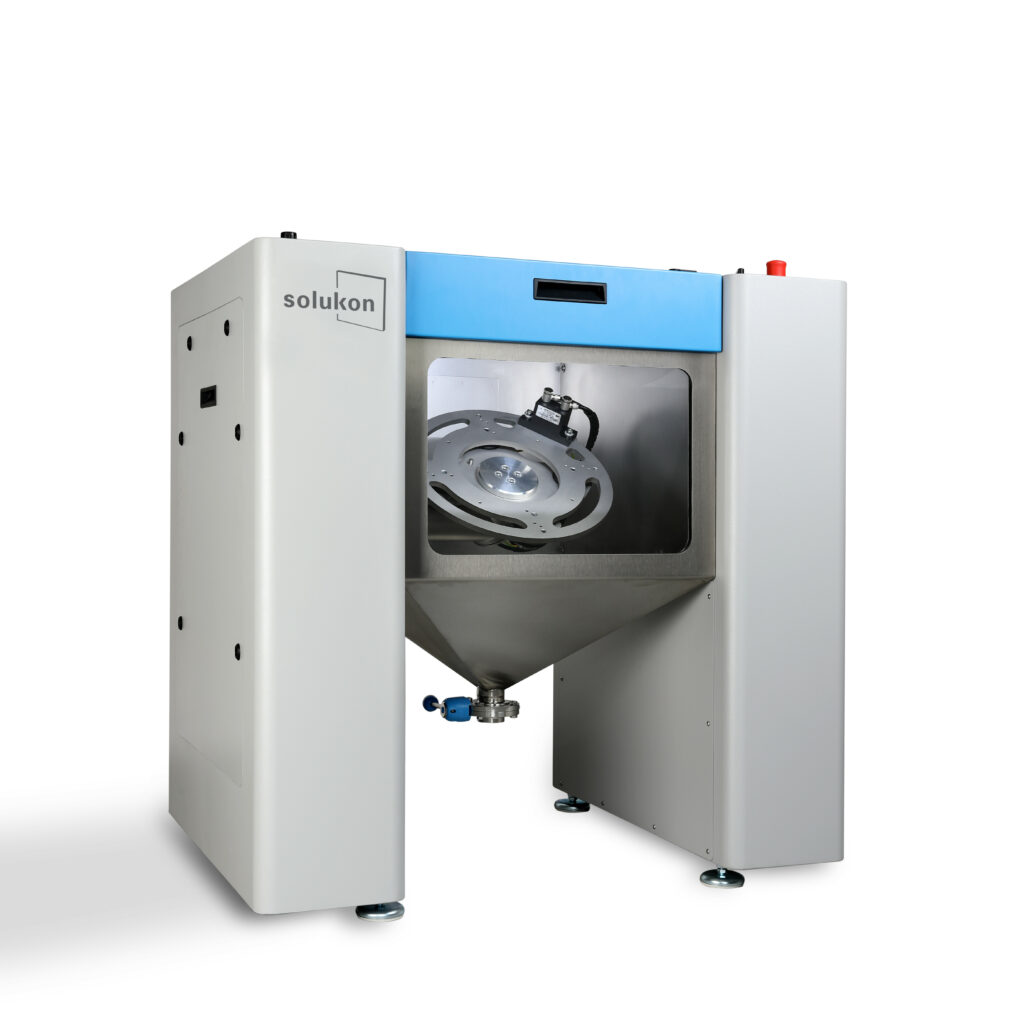
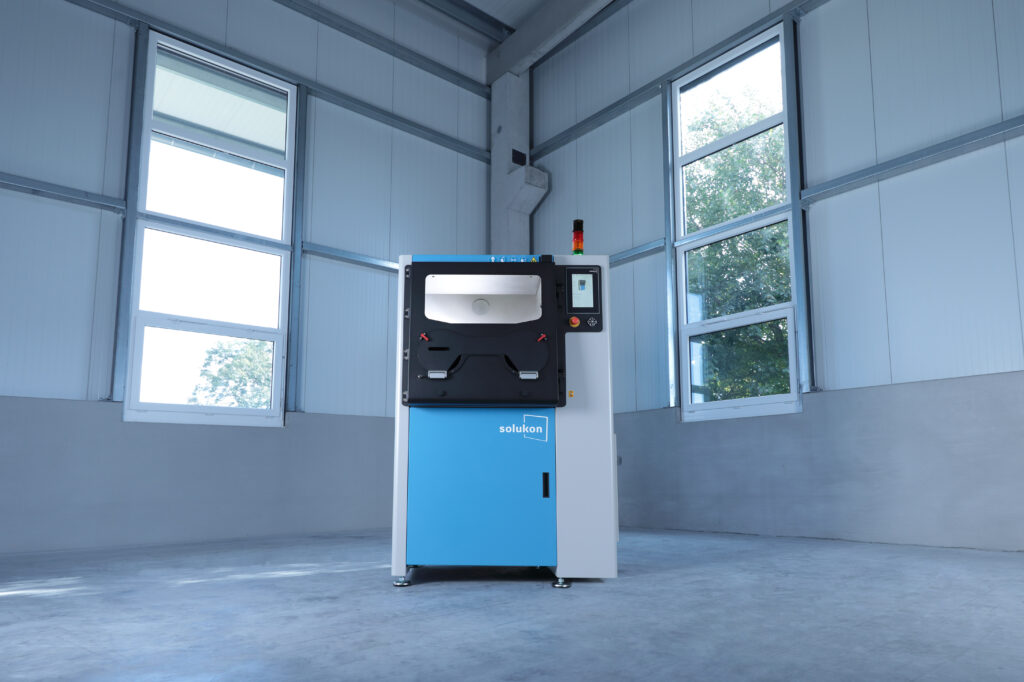
By highlighting the digital factory tool and automation integration as key features of the SFM-AT350, Solukon’s CEO refocuses the debate on a key item that enables AM to stand out from the crowd in a market already full of various digital healthcare technologies.
For the sake of humanity
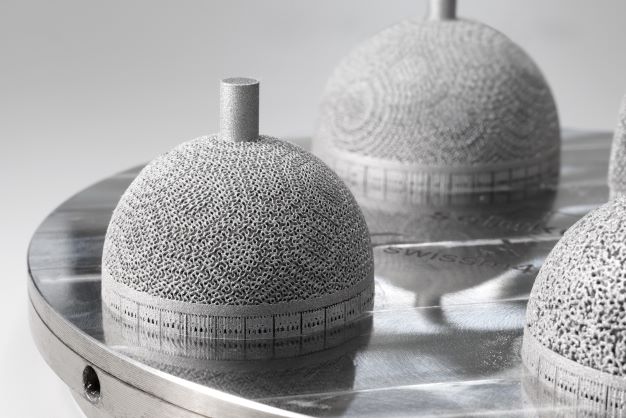
Orthopedics, traumatology, cardiology, ophthalmology are a few examples of sectors of activity that have already benefited from Additive Manufacturing. According to Bouduban, when we look at serial production, prosthetic parts with lattice structures for hip, knee or shoulder endoprosthetics are examples of parts that may require the use of AM in fabrication. Individualized parts for craniomaxillofacial surgery (orbita or jaw plates), semi-finished dental products such as metal frameworks or bridges and orthodontic products are other examples worth mentioning.
Interestingly, one common thread that surrounds the use of AM across these sectors is digitalization – a “catch all” term that the Gartner Glossary defines as “the use of digital technologies to change a business model and provide new revenue and value-producing opportunities.” A term that is often used interchangeably with digitization which refers to the process of converting information into a digital (i.e. computer-readable) format.
In the medical field, “data acquisition is the starting point for being able to perform fully digitized “”workflows“”, Bouduban points out. As medical technology aims to be more and more personalized, this should be reflected in the design and production decisions that medical device manufacturers make.
At every step of the manufacturing value chain (design, fabrication process, post-processing), collecting and maintaining complete data about how a medical device is fabricated and inspected is of paramount importance. In their production facility – and depending on the volumes of production to achieve, a medical device manufacturer will use a wide range of equipment to track the progress of projects, for production scheduling and for quality control.
The information gathered about the whole process then becomes very fragmented, hence the use of a manufacturing execution system (MES) that will digitize and centralize AM production data from beginning to end. This is just one example that reflects the need to acquire data across the entire value chain, data that can be traceable.
This need for transparency and traceability is also pivotal at the depowdering stage. As a matter of fact, these are features that make “the SFM-AT350 the machine of choice for medical AM manufacturers that need full process transparency (even to get a certified production environment)”, Hartmann recalls.
The truth is, “MedTech, together with aerospace and space, is the industry with the highest demand for process traceability and repeatability. This is where our Digital-Factory-Tool comes into play. The [latter is] a sensor and interface kit that records all relevant depowdering process data and summarizes the values in a protocol file. Critical limits can be set for relevant data so that deviations can be directly displayed and assessed. The DFT monitors data in the parts, such as residual oxygen, humidity, chamber pressure, temperature and frequencies. Information on the selected cleaning program is also available. The user can add specific information manually such as the type, batch, customer job and material used so that, in the end, a PDF-format protocol file is created”, he adds.
To date, Solukon’s collaboration with AM users has enabled the team to identify other pain points to address – which will lead to an upgraded version of the Digital-Factory-Tool. Hartmann shares for instance, that thanks to these collaborations, they know, users “need some more numbers from the depowdering process with respect to part quality and energy consumption during depowdering.” “In the medical field, more than in other industries, one comprising digital job ticket of the whole build and post-process must be the goal. We do everything to make the depowdering process transparent and are also contributing to work on a digital protocol for the whole process”, he completes.
Moving forward…
While digitalization has been mentioned as the common thread that surrounds the use of AM across the aforementioned medical sectors, the increasing adoption of these technologies comes with a growing number of pain points that require the attention of both technology providers like Solukon and technology users like Swiss m4m Center. Those pain points seem even more crucial when discussed in a vital industry like the medical one.
To those mentioned earlier – and with regards to depowdering, Solukon added the need for developing a sort of catalog that spells out the complex and resulting limitations of the depowdering process. This would mean actively matching part complexities (e.g. section of openings, length of channels, spread of openings on the part, structure depth) with their depowdering process.
“With a depowdering guide that aligns with relevant norms such as ASTM F3335, we will optimize the postprocessing process of our medical customers even further”, Hartmann concludes.
This content has been produced in collaboration with Solukon Maschinenbau GmbH.
This article was first published in the March/April edition of 3D ADEPT Mag.
Remember, you can post job opportunities in the AM Industry on 3D ADEPT Media free of charge or look for a job via our job board. Make sure to follow us on our social networks and subscribe to our weekly newsletter: Facebook, Twitter, LinkedIn & Instagram ! If you want to be featured in the next issue of our digital magazine or if you hear a story that needs to be heard, make sure you send it to contact@3dadept.com