Acknowledged as one of the most effective energy sources, lasers play a crucial role in different fields and Additive Manufacturing is no exception to that. If for many users, lasers are directly associated with more speed, the key to achieving product quality and increased productivity in manufacturing often comes down to the type of lasers the 3D printer is equipped with. Interestingly, different AM processes require different types of lasers. The article below aims to shed light on important laser parameters relevant to AM and highlights specific considerations for selecting the ideal lasers for one’s AM equipment.
As you may guess, a laser beam can deliver a large amount of energy into a micro-scale focal area, allowing for a high degree of precision and speed for a wide range of materials.
Before diving into the most-widely used lasers in AM equipment, it’s important to remember that a laser is usually made up of a gain medium, a pumping energy source, and an optical resonator. The gain medium within the optical resonator amplifies the light beam through stimulated emission, utilizing the external energy provided by a pumping source. The gain medium in use is therefore very important as it also permits to easily categorize lasers: gas, solid state, and fiber lasers.
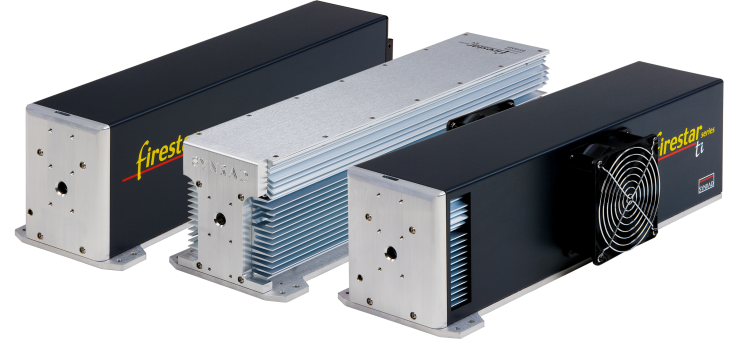
That being said, CO2 laser, Nd:YAG laser, Yb-fiber laser, and excimer laser are often mentioned as the main representative lasers across the AM industry due to their widespread use within specific AM processes and other precision manufacturing processes.
For those who are new to this space, please note that the CO2 laser is one of the first gas lasers that has been developed in the industry. In CO2 lasers, the gas-state gain medium fills the discharge tube and is electrically pumped by a DC or AC current to achieve population inversion for lasing.
Nd:YAG lasers (neodymium-doped yttrium aluminum garnet laser; Nd3+:Y3Al5O12 laser) are a type of solid-state laser using rod-shaped Nd:YAG crystals as a solid gain medium.
A fiber laser is a type of laser where the active gain medium is an optical fiber doped with rare-earth elements whereas excimer lasers use ‘excimers’ as the gain medium and are pumped by pulsed electrical discharge to produce nanosecond pulses in ultraviolet (UV) region.
“CO2 lasers used to be used in both metal and polymer, but they really didn’t have enough power to properly melt and fuse metal, so the metal AM industry moved to fiber lasers as requirements for higher powers and quality parts increased. Lasers also come in different power levels, and they can be turned up or down according to the parameter settings chosen for any given material or print feature desired. However, the design in power cannot be exceeded. For instance, a 500W laser will operate only up to 500W,” Alex Kingsbury, Market Development Manager – Additive Manufacturing at nLIGHT points out.
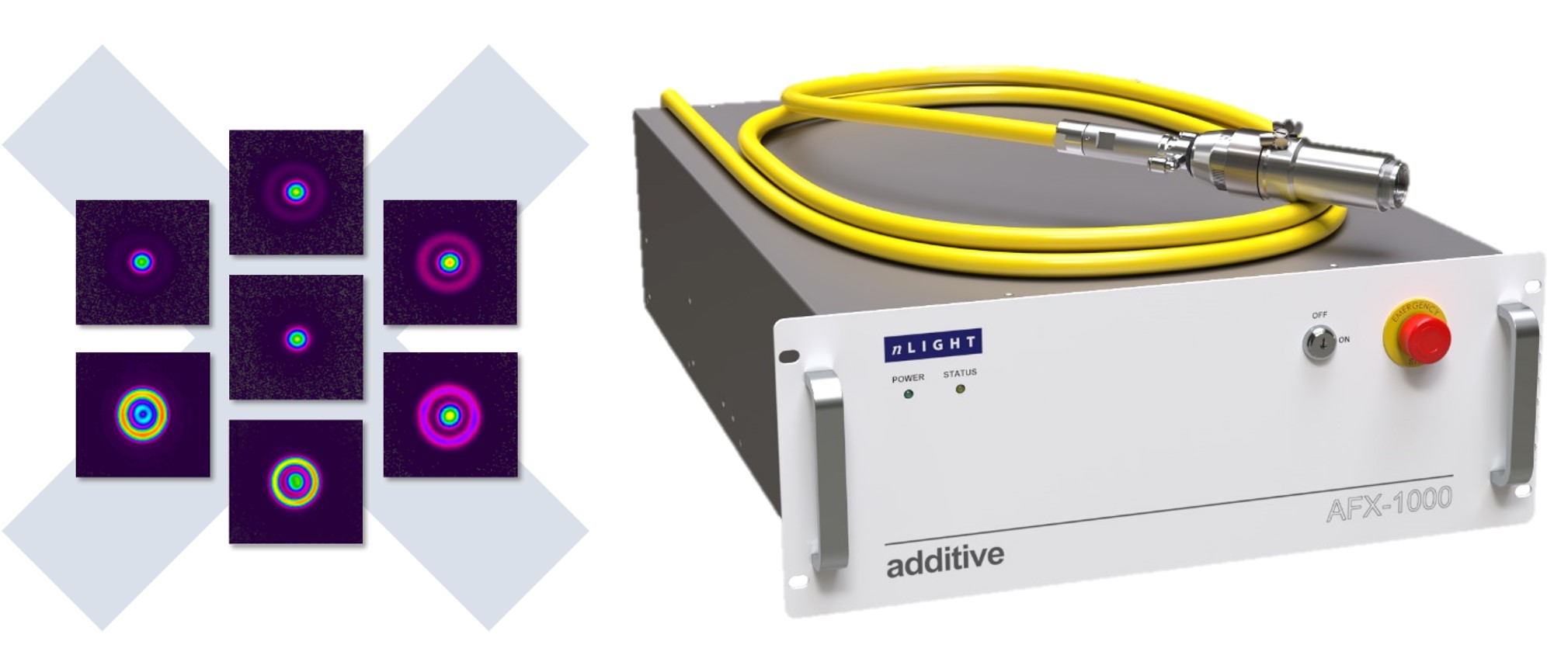
So far, we note that 3D printers based on Stereolithography (SLA), selective laser sintering (SLS), Directed Energy Deposition, and selective laser melting (SLM) can all be equipped with specific lasers.
Michael Rath, Inside sales representative at Novanta explains the differences in the use of lasers within these processes :
“The lasers used in Laser Additive Manufacturing (LAM) machines are primarily defined by the laser-material interaction of the base printing material. The central wavelength of the laser must align with the absorption spectrum of the 3D printing material. UV lasers (around 355 nm) are required for machines that use photo-polymer resins, CO2 lasers (around 10 µm) are required for SLS machines that use polymer powders, and IR lasers (around 1 µm) are required SLM machines that use metal powders.
Photo-polymer resin machines typically use frequency-tripled UV solid-state lasers with 500 mW to 1.5 W output power. The polymer powder bed machines typically use RF-excited, enclosed, metal tube CO2 lasers that are optimized for CW emission with 30 W to 150 W output power. The metal powder bed machines use single-mode and ring mode YB-fiber lasers with 200 W to 3000 W output power.”
What are therefore the essential criteria for choosing lasers?
“The central wavelength of the laser is the most [important] criteria for selecting a laser. As described above, the central wavelength of the laser must align with the absorption spectrum of the 3D printing material. In addition to wavelength optimization, lasers are qualified based on several performance characteristics including power stability, divergence stability, wavelength stability, output power, and beam quality (M²). The pulse-to-pulse stability for pulsed lasers or average power stability for CW lasers directly affects the width of the printed material, and thus the quality of the part to be built. Divergence stability and wavelength stability can have a similar impact. The output power of the laser typically dictates the print speed and throughput. Wavelength, beam quality (typically expressed as M²), and choice of scan head will affect the size of the beam focus, and therefore define the minimal feature size of the printed part,” Rath states from the outset.
Based on these criteria, one can identify these specifications for the lasers often integrated into AM machines:
Laser | CO2 laser | Nd:YAG laser | Yb-fiber laser | Excimer laser |
Application | SLA, SLM, SLS, LENS | SLM, SLS, LENS | SLM, SLS, LENS | SLA |
Operation wavelength | 9.4 & 10.6 μm | 1.06 μm | 1.07 μm | 193, 248, and 308 nm |
Output power (CW) | Up to 20 kW | Up to 16 kW | Up to 10 kW | Average power 300 W |
Pump source | Electrical discharge | Flashlamp or laser diode |
Laser diode | Excimer recombination via electrical discharge |
Operation mode | CW & Pulse | CW & Pulse | CW & Pulse | Pulse |
Pulse duration | Hundreds ns-tens μs | Few ns – tens ms | Tens ns – tens ms | Tens ns |
Beam quality factor
|
3 – 5 | 0.4 – 20 | 0.3 – 4 | 160 x 20
(Vertical x Horizontal) |
*Please note that these specifications may slightly vary from one provider to another. Source: Lasers in AM: A review.
If all of these specifications seem a lot to you, we recommend keeping in mind Kingsbury’s advice to assess a good laser:
“For starters, there are some simple quality parameters you can check to quickly gauge the quality of a laser. The first is the beam parameter product (BPP). The BPP gives you information on how well a beam can be focused to a small spot size. This is relevant for AM as the laser spot size will determine your melt pool width.
Another good measure of beam quality for Gaussian-shaped beams, i.e. most laser beams used in additive manufacturing, is the M2 value. The lower the number and the closer to 1, the better the quality of the beam, and the more tightly you can control it.
An OEM that builds 3D printers will also consider other factors relating to the laser such as how much ‘overhead’, i.e. spare power, the laser has built in.
As we move increasingly to multi-laser systems, we also need to consider how well synchronized those lasers are.”
The impact of lasers on 3D printer cost
While the focus has been made on 3D printers in this article, it should be noted that in AM, it’s possible to use CO2 lasers to polish the surfaces of 3D printed polymer parts and make them smoother. According to Novanta’s team of experts, this is a common procedure when printing customized shoe insoles.
On another note, it’s no secret that one of the limitations that slow down the purchase of industrial 3D printers (metal 3D printers especially) is the expensive cost one must invest in these machines. To reduce these costs, several OEMs on the market (such as ONE Click Metal) that pride themselves on delivering affordable metal 3D printers, focus the development of their machine on one of the most expensive parts: lasers.
It’s therefore important to keep in mind that even the price of these lasers vary from one category to another.
According to Novanta’s team of experts, “The type of laser (i.e. CO2 versus fiber) and output power will impact the total cost of the printer. For example, for fiber lasers, there are roughly three categories:
- Low-cost air-cooled continuous wave single mode fiber lasers up to 500 Watts
- Mid-cost water-cooled continuous wave single mode fiber laser above 500 Watts
- High-cost water-cooled continuous wave ring mode lasers
For CO2 lasers, there are similar categories:
- Low-cost glass tube CO2 lasers with under 100W output power
- Mid-cost RF-sealed CO2 lasers with under 100 W output power
- High-cost RF-sealed CO2 lasers with more than 100W output power”
To that, nLIGHT’s expert notes that “lasers, or the ‘light engine’, i.e. the whole optical train including the scanner, form the very heart of a 3D printer, and typically the light engine consists of a reasonable portion of the total bill of materials for a 3D printer. CO2 lasers, as mentioned above, are cheaper than fiber lasers, so in cases where they work well, i.e. for polymer systems, they are the laser of choice.” However, there is always the scanner choice as an option.
Additive Manufacturing techniques involving lasers are used in several industries, including electronics, medical, automotive, and aerospace. With the growing need for industrial applications, lasers will continue to play a crucial role in the pursuit of target performances. Their choice should therefore always take into account their operating principles, optical configurations, and comparative analysis of their respective advantages and limitations.
Firefly 3D scan head: Compact solution designed to boost performance in the product line thanks to multiheaded machine capability that can achieve up to 100% overlap. Credit: Novanta
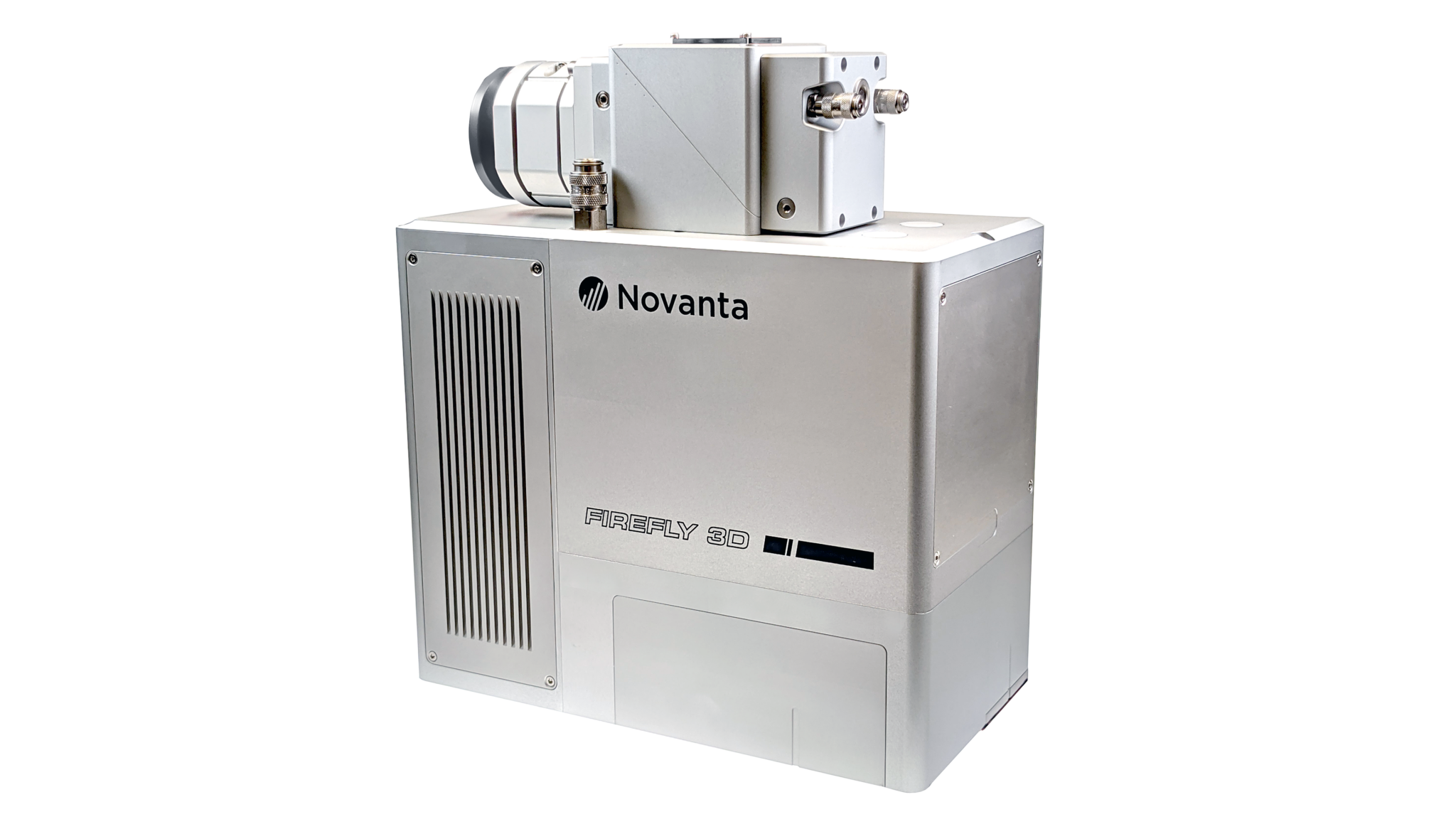
Editor’s notes
To discuss this topic, we invited two companies with key expertise on laser technologies.
nLIGHT is a company founded in 2000 that develops, designs and produces laser technologies and products. The company provides the AM industry with high power industrial fiber lasers for L-PBF systems. They have ‘standard’ Guassian-shaped lasers starting at 500W and up to 1kW, and ‘shaped’ lasers, the AFX, that start at 1kW and currently go up to 1.5 kW. Lasers can be shaped through free-space optics, but the AFX is shaped in the fiber, which is unique to nLIGHT. In-fiber beam shaping allows for precise control of the beam, and therefore the melt pool. The AFX has six different ring beam shapes that can be selected, and each may be more suitable than the other depending on the material, geometry, and desired microstructure. According to the company’s Market Development Manager – AM, with an increased understanding of the power bed, the metal AM industry has been able to successfully move towards ever higher powers in lasers. The current standard is 1kW. However, beyond 1 kW, the melt pool becomes unstable leading to excess porosity and poor quality parts. Ring-shaped lasers are the only shape of laser that enables higher powers to be applied to the powder bed while keeping a stable melt pool. Additionally, melt pool widths can be up to 300 microns wide; unleashing new levels of productivity in metal AM machines.
Through its Synrad brand, Novanta offers high-performance CO2 lasers from 10 W to over 200 W for polymer SLS 3D printing machines. Novanta also offers OEMs and system architects a broad range of high precision laser beam delivery systems and beam steering components for SLA, SLS and SLM applications. FIREFLY3D is Novanta’s next generation 3-axis scan head designed for Laser Powder Based Fusion (LPBF) machines in additive manufacturing applications. The FIREFLY3D is an enclosed, compact solution designed to boost performance in the product line thanks to multiheaded machine capability that can achieve up to 100% overlap. Incorporated within the design are features to simplify installation and operation including automated scan field calibration and advanced features such as precise monitoring of the additive manufacturing process.
This dossier has first been published in the May/June 2024 edition of 3D ADEPT Mag.