Swedish industrial design partner Splitvision delivers its services to medtech and automotive companies. The company distinguishes itself from others of the same range through a focus on manufacturing and logistics.
To provide much more than just competence to its clients, above all, to evaluate fitting and assembly before moving into serial production, Splitvision installed 3D Systems’ Figure 4 Standalone 3D printer in-house.
Launched last year, the Figure 4 Standalone is a SLA 3D Printing system. It has already convinced more than one company in the industry. ACS Custom, for instance, quadrupled the production of custom hearing protection with Figure 4™ Standalone 3D Printers. Other companies that leveraged this 3D printer from 3D Systems include Rapid Application Group and Nokia.
In this specific case, Splitvision’s goal was to go beyond simple prototyping. Before harnessing 3D printing, prototyping tasks were performed manually. The Swedish company worked with materials in foam and plastics to explore geometries and ergonomics, sometimes in full scale. Prototypes for functional tests or for customer review were bought from a third-party supplier, either from Sweden or China.
“Then, all of a sudden, there was this period when we had a massive amount of products under development, and everything basically piled up as we waited around for our 3D printed prototypes,” said Lukass Legzdins, R&D manager at Splitvision Design. “That’s the moment we decided to invest in an inhouse 3D printer, and luckily, it coincided with us discovering the Figure 4.”
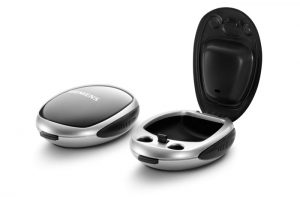
With no prior experience with 3D Systems’ technology, Splitvision discovered a few samples later, a technology that completely matches their requirements.
“After receiving a number of print samples from PLM Group, we realized that 3D Systems’ Figure 4 ELAST-BLK 10 material had the same properties as rubber. It was beyond our expectations,” Legzdins. “The material enables well-defined surfaces. We can see detailed shapes and facets. But most importantly, it allows us to evaluate the assembly process to identify potential challenges. Overall, it’s an excellent way for us to get confirmation of the geometry, while at the same time enabling our customers to do their own user tests.”
“One could say that our Figure 4 takes us one step closer to reality,”saidLegzdins. “Previously, we added more margin to our CAD files before ordering tools. Now, we can skip one or two steps in the development phase, as we have much more geometrical data from the 3D printed prototypes. The result is fewer incremental changes and adjustments to the tool.”
You can now post free of charge job opportunities in the AM Industry on 3D ADEPT Media.For further information about 3D Printing, follow us on our social networks and subscribe to our newsletter : Facebook, Twitter, LinkedIn & Instagram !Would you like to be featured in the next issue of our digital magazine? Send us an email at contact@3dadept.com
https://pagead2.googlesyndication.com/pagead/js/adsbygoogle.js
(adsbygoogle = window.adsbygoogle || []).push({});