Shell International B.V. et GE Additive ont dévoilé les résultats d’un projet commun de conception et d’ingénierie – un micromélangeur oxygène-hydrogène fabriqué de manière additive. Cette pièce de démonstration complexe et non fonctionnelle a été imprimée en alliage de nickel 718 sur un système GE Additive Concept Laser M Line, installé au CoE et à l’atelier d’impression 3D de Shell, qui font partie de l’Energy Transition Campus Amsterdam (ETCA), aux Pays-Bas.
Shell dispose d’une installation d’impression 3D de pointe à l’ETCA, à proximité de ses scientifiques et de ses entreprises partenaires, afin de tirer parti de la fabrication additive pour créer des prototypes et imprimer des pièces fonctionnelles. Le fait de disposer de sa propre capacité d’impression donne au département R&D de Shell la liberté et la rapidité nécessaires pour créer des pièces inédites qui ne sont pas disponibles sur le marché, et pour résoudre de nouveaux défis techniques afin de soutenir la transition énergétique.
Joost Kroon, expert en technologie additive chez Shell, explique : « Nous voulions vraiment mettre la M Line à l’épreuve et la tester jusqu’à ses limites. En collaboration avec l’équipe GE Additive, nous avons convenu d’appliquer la technologie additive pour réimaginer une pièce complexe de grande taille, en y incorporant des canaux qui seraient difficiles à fabriquer de manière conventionnelle. Travailler sur un micro-mélangeur oxygène-hydrogène s’aligne bien sur les stratégies de nos entreprises pour jouer un rôle positif dans la transition énergétique. »
S’inspirer de la géométrie dans la nature
Sonali Sonawane Thakker, ingénieur concepteur en chef au sein de l’équipe AddWorks de GE Additive basée à Munich, a été chargée de rechercher, de concevoir et d’itérer la conception finale. Son mandat consistait à concevoir une pièce de grande taille, complexe et dotée de canaux pour l’hydrogène et l’oxygène comprimé. Sonawane Thakker a pu profiter des libertés de conception offertes par la technologie additive pour repenser la structure et la forme de la pièce.
« Une fois que nous nous sommes mis d’accord sur une pièce, nos recherches préliminaires ont montré que les micromélangeurs existants – également connus sous le nom de brûleurs hydrogène-oxygène – sont généralement cylindriques, lorsqu’ils sont fabriqués de manière conventionnelle, pour s’adapter à la disposition complexe des réservoirs, des tuyaux et des buses. Pour plus de complexité, nous avons opté pour une conception conique de grande taille et sommes également passés d’une structure plate à une structure incurvée avec une grille ISO pour augmenter la résistance globale, plutôt qu’une structure plate habituelle. »
Sonawane Thakker a cherché à s’inspirer des géométries et de la symétrie dans le monde naturel, en particulier de la séquence Fibonnaci reproduite dans les fleurs et les pétales.
« Avec plus de 330 buses individuelles à incorporer dans un motif circulaire, je me suis inspirée de la façon dont les grains de pollen se forment dans une tête de fleur. La paroi incurvée et la forme conique reflètent également la forme d’un pétale« , a-t-elle ajouté.
Fabrication et post-traitement
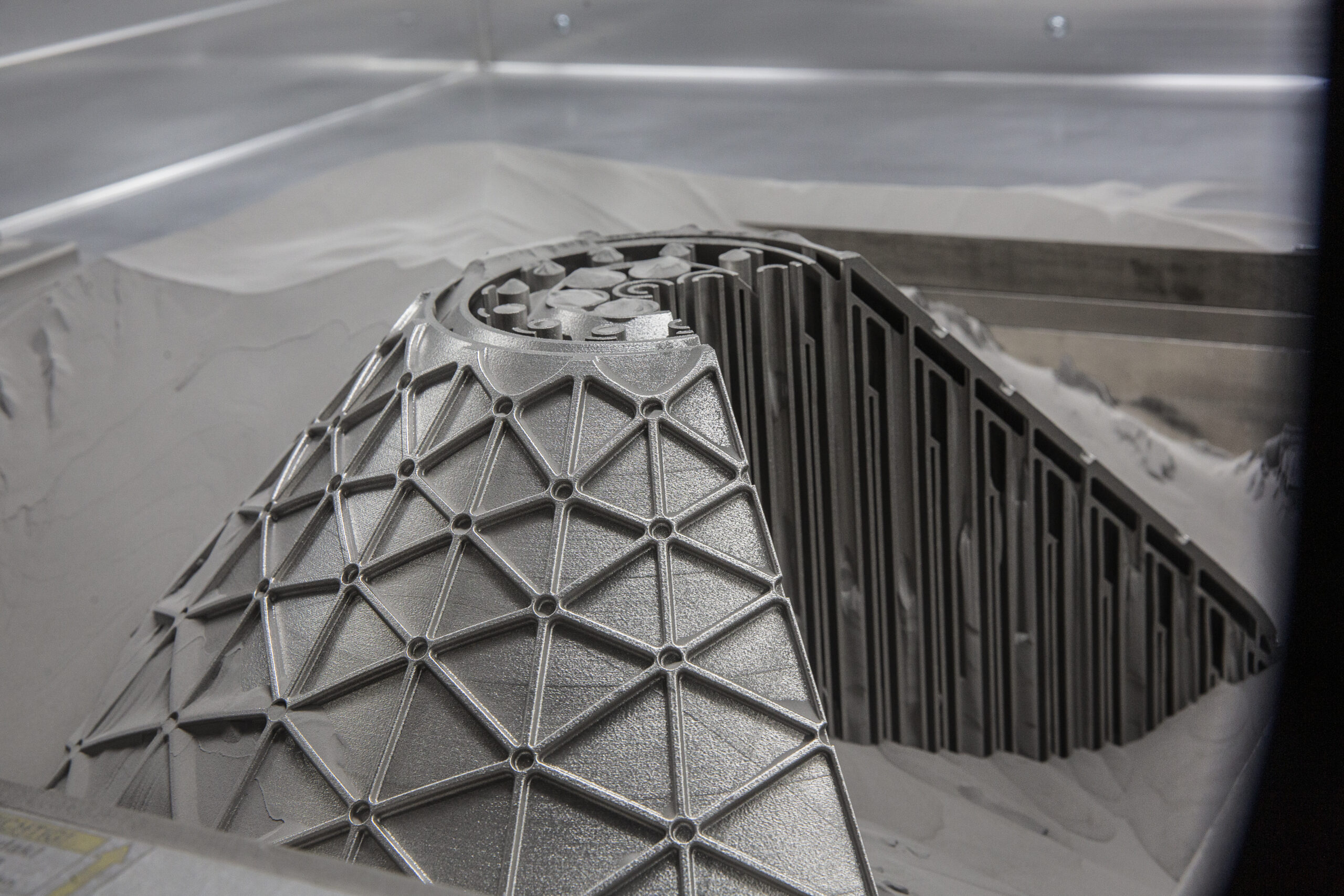
Après des examens de faisabilité et des itérations par les équipes de Shell et de GE Additive, la conception et les dimensions de la pièce réimaginée ont été finalisées et l’alliage de nickel 718 a été choisi comme matériau pour la fabrication.
Dimensions de la pièce :
- Hauteur : ~296 mm
- Diamètre : 484 mm
- Autres : X ~ 429 mm Y ~490 mm
La préparation de la construction et l’impression de la pièce sur la ligne M ont été supervisées par Lisa Kieft-Lenders, chef d’équipe, et Dennis Boon, technicien au Centre d’excellence et atelier d’impression 3D de Shell.
« Nous avons été impliqués dans le projet dès le début et avons donc été particulièrement proches de cette construction et investis dans sa réussite. Étant donné qu’il s’agit de l’une des pièces les plus grandes et les plus complexes construites sur une ligne M jusqu’à présent, si ce n’est la plus grande, nous sommes restés en contact étroit avec l’équipe GE Additive à Munich et avons été soutenus, sur le terrain ici à Amsterdam, par leurs ingénieurs de service locaux. Après quelques adaptations au début, la construction s’est déroulée sans problème pendant neuf jours« , a déclaré Kieft-Leenders.
Le post-traitement a également été réalisé dans les installations de Shell, et cela a été facilité par l’inclusion de trous de retrait de la poudre, incorporés par Sonawane Thakker pendant la phase de conception. La pièce a été achevée début novembre et envoyée au stand de GE Additive au salon Formnext. Après l’événement, le micromélangeur sera retourné et exposé à l’ECTA de Shell.
« Nous sommes confiants dans la capacité de la M Line à être performante. En effet, nous saisissons chaque occasion de la tester à ses limites à deux mains. Je ne peux sous-estimer le pouvoir de la collaboration et de la résolution de problèmes au cours de ce projet. Il a rassemblé de grands esprits de la FA et le résultat final n’est pas seulement époustouflant visuellement, mais il est également de taille substantielle, complexe et tout aussi solide« , a déclaré Rob Dean, responsable AddWorks de GE Additive pour la région EMEA.
N’oubliez pas que vous pouvez poster gratuitement les offres d’emploi de l’industrie de la FA sur 3D ADEPT Media ou rechercher un emploi via notre tableau d’offres d’emploi. N’hésitez pas à nous suivre sur nos réseaux sociaux et à vous inscrire à notre newsletter hebdomadaire : Facebook, Twitter, LinkedIn & Instagram !