Il existe un vieux dicton dans le monde des affaires selon lequel « être précoce est la même chose qu’avoir tort ». En effet, lorsque vous êtes précoce, votre start-up a plus de chances d’échouer parce qu’elle est en avance sur son temps. Ça a été le cas de nombreuses entreprises de l’industrie de la FA, excepté voxeljet.
Le fait d’avoir traversé les différentes crises qui ont marqué ce marché de l’ingénierie et de rester fort aujourd’hui fait de voxeljet une licorne que nous avons voulu découvrir davantage. Pour nous aider à raconter cette histoire, nous avons invité dans cette Opinion de la Semaine, Tobias King, directeur du marketing et des applications de la société.
Cela fait déjà deux décennies que le Dr. Ingo Ederer a fondé voxeljet. Le fabricant de machines s’est alors concentré sur le développement de la technologie d’impression 3D pour les applications de moulage de métaux. En quelques mots, leur technologie permet de fabriquer des moules de coulée en sable et des modèles en plastique pour le moulage à la cire perdue. C’était assez fou car, comme vous le savez déjà, à l’époque, les procédés de moulage et de fraisage étaient principalement utilisés pour la production d’outils et de moules. Sans compter que ces technologies ne permettent pas vraiment d’atteindre une certaine complexité géométrique.
Ainsi, lorsque voxeljet a fait ses débuts sur ce marché, elle a établi un nouveau standard de fabrication, qui s’est avéré être une mission d’innovation continue et de stimulation d’une « nouvelle pensée industrielle et constructive », une mission qui s’est affinée au fil du temps puisqu’aujourd’hui la société vise à redéfinir la fabrication additive de masse.
King par contre, a rejoint le pionnier de l’impression 3D en 2008. D’ingénieur de projet à directeur du marketing et des ventes, il fait partie des collaborateurs qui ont contribué à définir et à mettre en œuvre des objectifs stratégiques et des mesures de marketing opérationnel, pour l’expansion du portefeuille de produits et d’applications de l’entreprise. Selon ses propres termes, son rôle comprend, sans s’y limiter, les marchés de la construction, du laminage et des polymères dont les produits peuvent être utilisés comme coffrages pour le coulage du béton, outils de laminage et pièces polymères fonctionnelles pour des applications finales.
Quoi qu’il en soit, voxeljet s’est efforcé de rester centré sur sa mission. Comme l’indique le représentant de la société :
« Lorsque nous avons commencé, nos imprimantes avaient un volume de bâtiment de 1.500 x 700 x 750 mm. C’était déjà assez grand pour des imprimantes lancées en 2003. Aujourd’hui, notre plus grand système d’impression 3D a un volume de 4.000 x 2.000 x 1.000 mm. Cela laisse beaucoup de place pour de très grands moules ou un très grand nombre de petites pièces. En 2011, nous avons également développé un concept d’imprimante 3D continue qui pourrait être capable de créer un nombre infini de pièces. D’une manière générale, nous nous efforçons continuellement de repenser et de redéfinir nos produits dans une optique d’avenir. Aujourd’hui, l’impression 3D est devenue une technologie de fabrication qui trouve des applications bien au-delà du prototypage et de la production de pièces de rechange ».
Néanmoins, voxeljet a ouvert de nouvelles portes aux fondeurs, aux ingénieurs et aux outilleurs qui souhaitaient maintenir la fonte des métaux au cœur de leur environnement de production. Le fabricant est désormais reconnu pour soutenir les fonderies dans la réalisation de formes de moulage qu’il serait impossible d’obtenir avec les procédés traditionnels. Rappelez-vous de l’histoire de la fonderie d’acier indienne qui a investi dans l’imprimante industrielle VX4000 pour fabriquer et fournir des pièces moulées en acier.

D’un point de vue technique, ces applications de moulage à la cire perdue et d’impression 3D en sable sont rendues possibles grâce à la technologie du jet de liant de l’entreprise. King explique que chez voxeljet, ils lient les matériaux en poudre avec des têtes d’impression haute performance et créent des pièces dans un lit de poudre. Ce procédé permet donc d’imprimer tout ce qui se présente à l’état de poudre, d’où l’accent mis sur le sable pour « les applications de moulage en sable, et la poudre acrylique pour les applications de moulage à la cire perdue au départ ». Lorsqu’on lui demande ce qui fait de sa technologie un bon candidat pour ces applications, le directeur du marketing et des ventes souligne l’importance d’utiliser des matériaux de fonderie standardisés abordables tels que le sable de silice et diverses résines, et de réaliser des économies de temps et d’argent.
« La création d’un outil traditionnel peut prendre jusqu’à 8-12 semaines et coûte très cher. Cela représente beaucoup de temps et de ressources pour créer un prototype qui, dans le pire des cas, ne pourra pas être produit. Grâce à notre technologie de Jet de liant, les moules peuvent être imprimés, livrés et coulés en une semaine seulement, pour un coût bien inférieur à celui de l’outillage classique. Et la manipulation pour le fondeur lui-même ne change pas du tout, les moules ou les modèles de moulage à la cire perdue peuvent être intégrés dans le processus de moulage traditionnel. C’est ce qui rend la fabrication additive si attrayante.
De plus, les matériaux que nous utilisons ne sont pas si chers. Avec les taux de construction les plus rapides en FA qu’offre le Jet de Liant, combinés aux coûts totaux de possession d’un système d’impression 3D, ou la production à la demande dans nos centres de service est plutôt faible. C’est pourquoi nous pouvons cibler des marchés à fort taux de production, comme l’industrie automobile. Si les clients n’ont pas besoin d’un système d’impression complet, par exemple parce que la quantité de pièces nécessaires est trop faible, les clients peuvent toujours passer commande dans nos centres de service et se faire livrer les pièces en quelques jours ».
Les choses sont devenues passionnantes il y a trois ans, lorsqu’ils ont lancé le frittage à grande vitesse (HSS), ouvrant ainsi de nouvelles portes à la création de pièces en polymère dont les propriétés peuvent être similaires à celles du SLS ou des pièces moulées par injection.
L’industrialisation de l’impression 3D au cœur de leurs activités
C’est également à cette époque que voxeljet s’est réveillée de son mode furtif et a décidé de répondre aux questions spécifiques soulevées par les industries verticales adoptant la FA, notamment l’automobile. En plus d’être un secteur vertical crucial pour tout fabricant de systèmes De FA, l’industrie automobile est également une cible clé pour les volumes de production.
Le développeur de la technologie HSS a exprimé le besoin de se positionner sur de tels marchés dans le cadre du projet ICP, abréviation de « Industrialization of core printing » ; un projet qui a vu le développement de la série d’imprimantes 3D VJET X, réalisée en collaboration avec l’expert en fonderie Loramendi et le spécialiste des matériaux ASK Chemicals. Alors que les trois entreprises visaient à réaliser une production additive en série pour les noyaux de chemises d’eau, le projet lui-même a aidé voxeljet à atteindre une étape importante dans sa vision de redéfinir la production additive en série. Mettant l’accent sur les spécifications techniques, King souligne l’utilisation de leur imprimante 3D VX1300 X dans le cadre de cette chaîne de production. « C’est une imprimante 3D haute performance, plus de 10 fois plus rapide que nos imprimantes habituelles. L’imprimante utilise un liant inorganique, développé par ASK Chemicals, pour lier le sable. L’avantage du liant inorganique est que lors du moulage, seule de la vapeur d’eau est créée, ce qui améliore considérablement les conditions de travail dans la fonderie et a un impact positif sur l’empreinte écologique. Loramendi a développé l’ensemble du post-traitement entièrement automatisé de cette ligne de production. Cette ligne de production est installée chez un client du secteur automobile en Allemagne ».
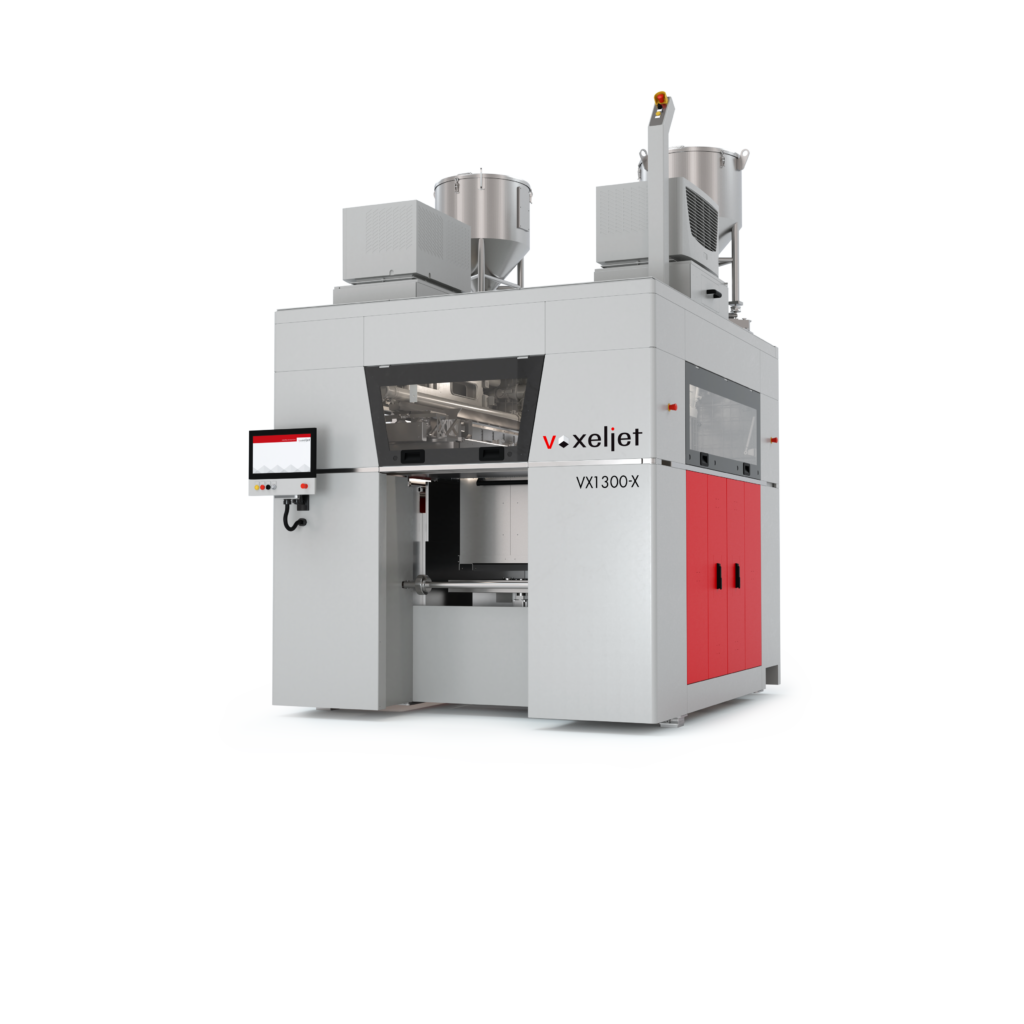
Les prochaines étapes pour voxeljet ?
Forte de ses années d’expérience, voxeljet cherche maintenant à améliorer les goulets d’étranglement actuels du processus de fabrication, comme l’automatisation au stade du post-traitement, et à développer une nouvelle gamme de produits. Après le lancement du premier prototype de son système VX1000 HSS à Formnext 2019, l’équipe de voxeljet gardera le développement de l’imprimante 3D polymère à grande échelle comme l’une de ses priorités pour les mois à venir.
Cependant, pour l’année prochaine, « nous nous concentrons pleinement sur notre vision d’amener la fabrication additive de polymères en production de série avec le lancement de la version bêta du VX1000 HSS. 2020 a été une année particulière, avec de nombreux défis énormes auxquels nous avons tous dû faire face. Mais pour l’industrie de la fabrication additive, ce fut très intéressant. Le manque soudain et la demande excédentaire pour de nombreux produits pouvaient être satisfaits grâce aux technologies de FA. Cela a montré au monde ce dont cette technologie est déjà capable. Nous allons poursuivre notre mission et travailler sur nos solutions d’impression 3D afin d’ouvrir la voie à une nouvelle norme de fabrication », conclut King.
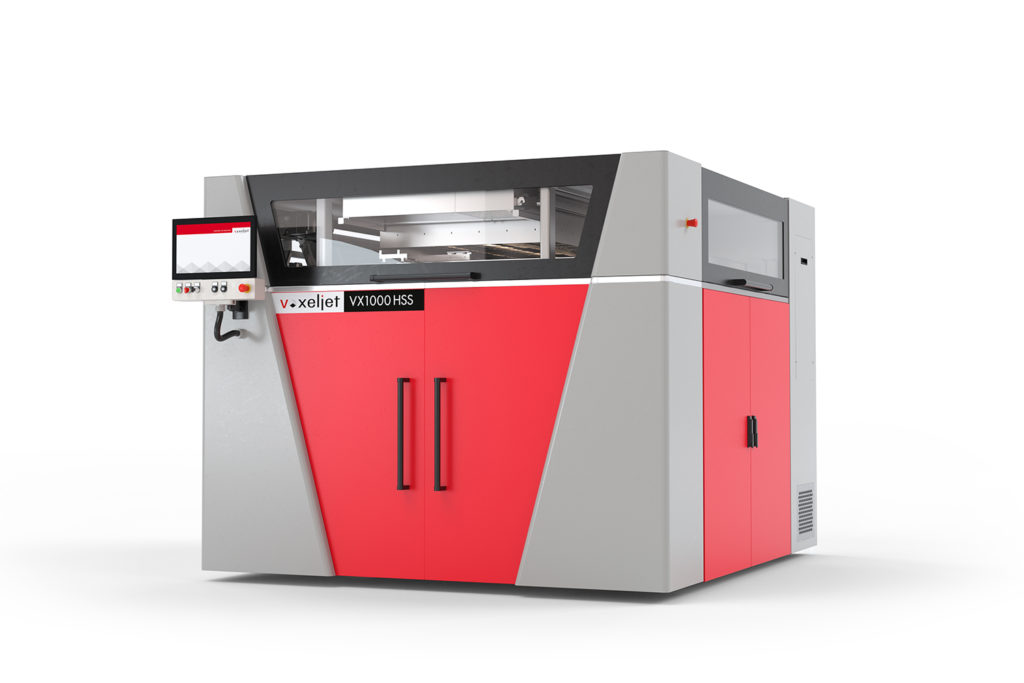
En attendant, si vous souhaitez interagir avec les experts de l’entreprise lors d’un salon, n’hésitez pas à les rencontrer lors du prochain Formnext Connect.
N’oubliez pas que vous pouvez poster gratuitement les offres d’emploi de l’industrie de la FA sur 3D ADEPT Media ou rechercher un emploi via notre tableau d’offres d’emploi. N’hésitez pas à nous suivre sur nos réseaux sociaux et à vous inscrire à notre newsletter hebdomadaire : Facebook, Twitter, LinkedIn & Instagram ! Si vous avez une innovation à partager pour le prochain numéro de notre magazine numérique ou si vous avez un article à faire connaître, n’hésitez pas à nous envoyer un email à contact@3dadept.com