Il peut être facile pour les ingénieurs ou les concepteurs de penser que, parce qu’ils ne sont pas directement impliqués dans la fabrication des pièces, ils ne devraient pas être au courant de certaines complexités entourant le fonctionnement pratique des machines. Ce n’est pas le cas. Connaître les variables et les complexités liées au fonctionnement pratique des machines permet d’assurer une communication claire avec les opérateurs et, surtout, de faire en sorte que les objectifs de conception répondent parfaitement aux attentes de la fabrication. L’une de ces complexités consiste à comprendre l’importance des dispositifs de recouvrement (souvent appelés ‘lames’) pour la fabrication additive métal.
En termes simples, un dispositif de recouvrement (plus connu sous le nom de recoater en anglais) est une barre horizontale qui étale et lisse le matériau pendant le processus de fabrication, afin de créer une couche uniforme et plane avant que le matériau de construction ne soit solidifié, fritté, fondu ou collé. Comme l’ont confirmé Michael Wohlfart, expert en FA chez EOS, et Thomas Spears, PhD, directeur d’AAMT, il est généralement admis que seuls les procédés à base de poudre nécessitent un dispositif de recouvrement.
Néanmoins, la recherche montre que les recycleurs peuvent également être utilisés dans la photopolymérisation pour étaler le polymère liquide. Dans ces machines, la machine de photopolymérisation se compose d’une cuve de résine, d’une lame de repositionnement, d’une plate-forme de construction, d’une source lumineuse et de systèmes de contrôle. La résine photopolymère liquide est placée dans la cuve. Le dispositif de recouvrement est utilisé pour distribuer et balayer la résine liquide lorsqu’une couche est durcie. La plate-forme de fabrication fixée à un élévateur se déplace à l’envers et la pièce est fabriquée dessus.
Parlant d’exemples de machines de FA qui intègrent un dispositif de recouvrement, Thomas Spears, directeur d’AAMT, cite la fusion par faisceau d’électrons (comme Arcam) ou la projection de liant (comme ExOne). « Les nouvelles modalités que j’ai vues à Rapid+TCT étaient l’épandage d’un matériau à matrice céramique, les machines de photolithographie comme celles de 3D Systems, et les machines de frittage de plastique comme celles d’EOS », ajoute-t-il.
Cela dit, cet article se focalisera sur l’utilisation des dispositifs de recouvrement dans les procédés de fusion laser sur lit de poudre.
Dispositifs de recouvrement
Si vous ne connaissez pas encore la Fabrication Additive (FA), sachez que les procédés de fusion laser sur lit de poudre (abrégé LPBF – soit laser powder bed fusion en anglais) reposent sur un principe de base : l’utilisation d’un laser ou d’un faisceau d’électrons pour faire fondre et fusionner les matériaux en poudre. Plus précisément, une couche de matériau d’une épaisseur typique de 0,1 mm est étalée sur la plate-forme de fabrication. Un laser fusionne la première couche ou la première section du modèle. Une nouvelle couche de poudre est étalée sur la couche précédente à l’aide d’un dispositif de recouvrement ou d’un rouleau. Le processus se répète jusqu’à ce que la pièce entière soit fabriquée.
Outre le fait qu’il dépose la poudre de manière uniforme, un dispositif de recouvrement permet de contrôler l’épaisseur de la couche de poudre déposée. La vitesse de recouvrement joue un rôle important dans ce processus, car elle peut influencer la morphologie de la surface du lit de poudre, ce qui peut compromettre la réussite de la fabrication de la pièce et la fiabilité de la production.
Le choix du bon dispositif de recouvrement devient donc crucial, car les opérateurs peuvent faire fonctionner leurs machines LPBF 24 heures sur 24, 7 jours sur 7, avec des changements de couche toutes les minutes. C’est la raison pour laquelle les fabricants de machines font de plus en plus de leur dispositif de recouvrement un avantage concurrentiel.
Types de dispositif de recouvrement
« Il existe de multiples variantes de technologies pour répandre la poudre dans les systèmes commerciaux à base de poudre, mais elles sont toutes désignées sous le nom de « recoaters« , » précise d’emblée Michael Wohlfart.
Il va sans dire que les particularités de certaines imprimantes 3D peuvent se manifester sous la forme d’outils différents utilisés pour étaler uniformément les couches de poudre pour chaque couche d’une construction. « Certains fabricants utilisent un rouleau pour compacter la poudre et créer une densité plus importante et plus cohérente sur la surface active. Velo3D utilise un recycleur sans contact qui utilise le vide pour garantir une épaisseur de couche correcte », explique Spears.
Il existe quatre grands types de dispositifs de recouvrement. Selon Wohlfart, il y a :
- Les dispositifs de recouvrement durs : HSS (acier rapide), lames en céramique
- Les dispositifs de recouvrement souples : Différents types de brosses (fibre de carbone, métal), différents types de lames en polymère (silicone, caoutchouc NBR, autres types de polymères).
- Les dispositifs de recouvrement à rouleaux : ce sont des technologies de niche principalement utilisés dans les imprimantes 3D LPBF pour polymères, mais également dans des imprimantes 3D métal spécifiques qui traitent les poudres fines difficiles à étaler.
- Les dispositifs de recouvrement sans contact : il s’agit d’une technologie de niche dans les imprimantes 3D métal qui permet une croissance hors plan de l’application sans interruption de la fabrication, mais elle est généralement lente et limitée en termes de flexibilité (par exemple, une seule hauteur de couche spécifique). En outre, la croissance hors plan n’est pas acceptable pour de nombreuses applications en raison des tolérances dimensionnelles serrées.
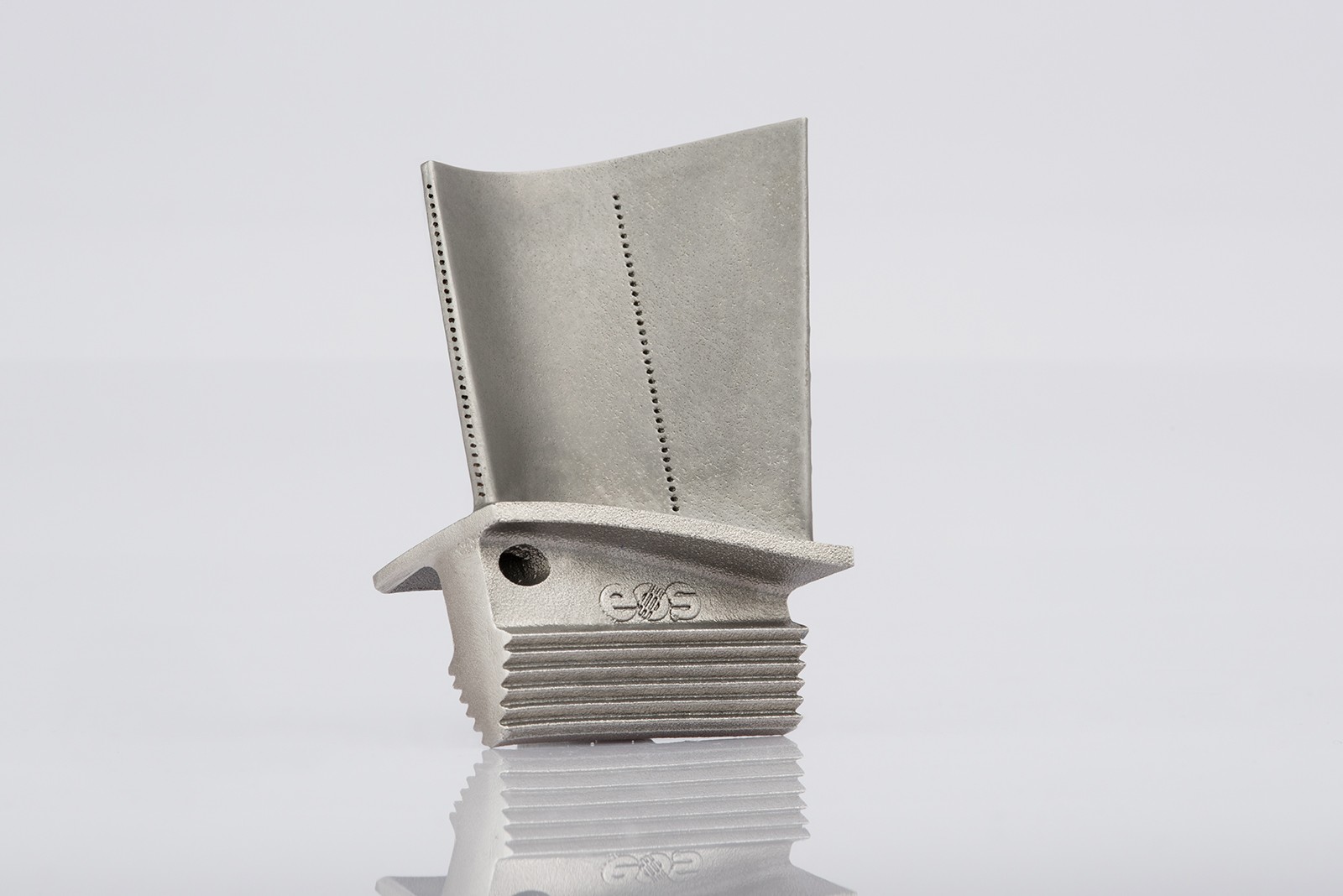
Comme vous pouvez le constater dans l’industrie, les dispositifs de recouvrement durs et les dispositifs de recouvrement souples sont souvent mentionnés comme les principales technologies utilisées. C’est la raison pour laquelle l’expert AM d’EOS qualifie les deux autres de technologie de niche.
D’après ce que nous savons, les dispositifs de recouvrement durs sont une bonne solution pour la fabrication de pièces identiques sur la même plate-forme de fabrication. Ils entraînent souvent une faible déformation des pièces. Il est évident que si une pièce se déforme, il y a de fortes chances que d’autres pièces se déforment également.
Par ailleurs, si vous fabriquez des pièces délicates ou différentes à la fois, il est préférable d’opter pour un dispositif de recouvrement souple. Cela semble évident, non ? Dans ce cas précis, si vous manipulez un lot de pièces différentes, la déformation d’une pièce n’entraîne pas nécessairement la déformation des autres – par conséquent, la construction ne s’interrompt pas.
Il est intéressant de noter que, parfois, ces différences ne sont pas suffisantes pour choisir entre un dispositif de recouvrement dur et un dispositif de recouvrement souple.
Certains fabricants recommanderont un dispositif de recouvrement dur pour les pièces les plus exigeantes en raison de leur capacité à obtenir une qualité reproductible, tandis qu’ils opteront pour un dispositif de recouvrement souple pour les pièces présentant des rapports d’aspect élevés et pour les productions où le délai d’exécution est plus important que le risque d’imperfections.
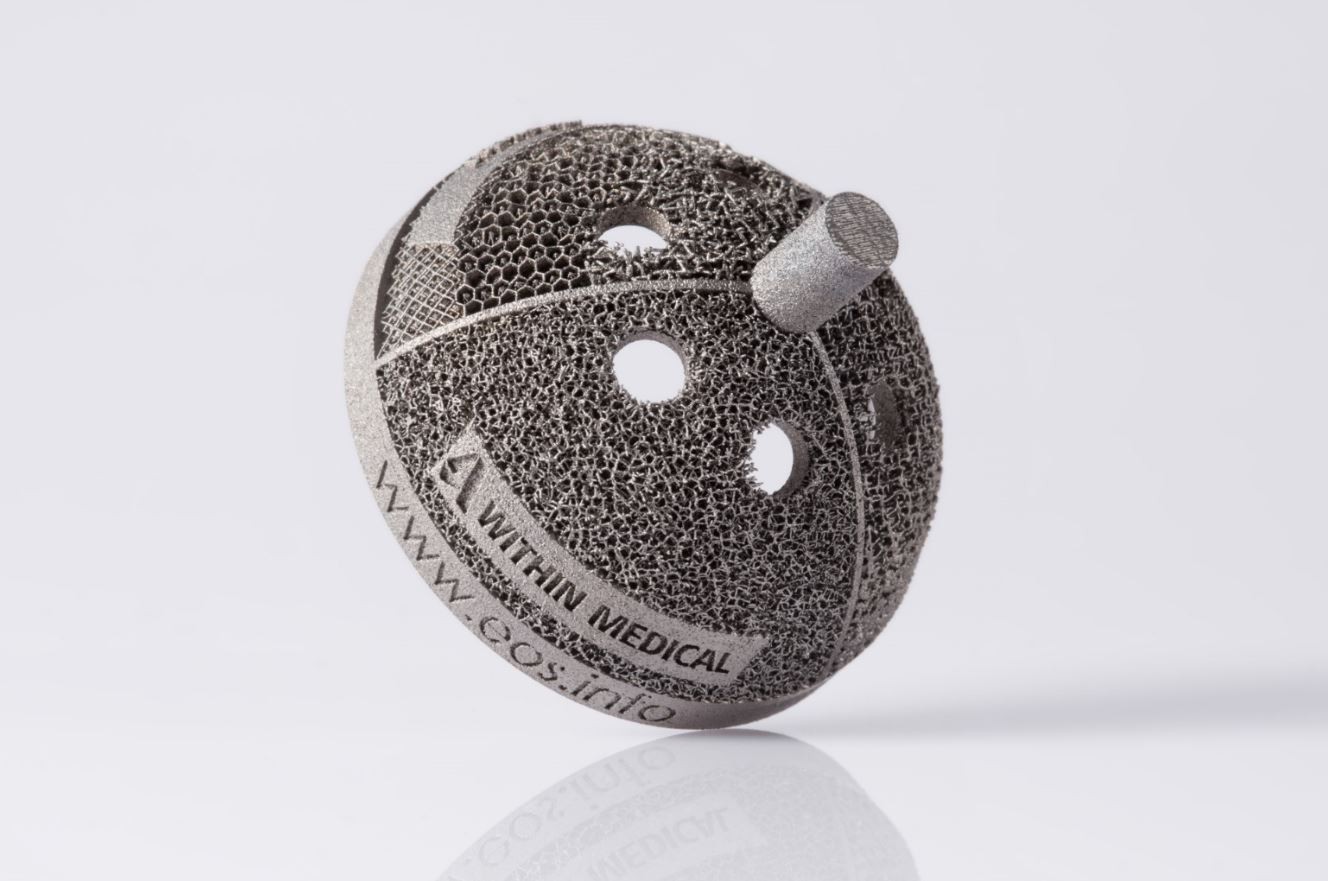
Même si les machines qu’ils construisent sont compatibles à la fois avec les dispositifs de recouvrement durs et souples, le directeur d’AAMT reconnaît qu’« il y a une part de subjectivité [lorsqu’il s’agit de choisir le dispositif de recouvrement idéal] ». Certains utilisateurs préfèrent la tolérance de la couche du dispositif de recouvrement souple, tandis que d’autres préfèrent la consistance de la couche du dispositif de recouvrement dur, même si elle est plus susceptible de s’écraser en raison d’anomalies de la surface supérieure ou d’un décollement de la pièce. D’autres considérations liées au processus peuvent également dicter le type de vernis : le silicone, les brosses en fibre de carbone et les râteaux métalliques sont plus appropriés pour les applications nécessitant des caractéristiques très fines qui pourraient être physiquement détruites par un vernis dur entrant en contact, même de façon modeste, avec ces caractéristiques ».
Wohlfart, quant à lui, apporte des précisions sur le sujet :
« Les procédés des imprimantes LPBF pour métaux et polymères sont fondamentalement différents et il n’existe pas de machines sur le marché qui puissent traiter les deux matériaux dans le même système. Cependant, il existe encore des différences entre les systèmes de réapprovisionnement qui peuvent s’expliquer par les différentes exigences en matière de matériaux/processus, mais aussi par la géométrie à imprimer qui peut avoir une influence sur le type de réapprovisionnement.
Les systèmes de polymères utilisent généralement des dispositifs de recouvrement durs ou des dispositifs de recouvrement à rouleaux, en raison de la température élevée du lit de poudre et de la nature différente des processus. La forme de la lame du dispositif de recouvrement dur est également différente de celle des dispositifs de recouvrement pour métaux, car le compactage du lit de poudre est plus essentiel pour le processus.
En ce qui concerne les dispositifs de recouvrement durs pour les systèmes LPBF pour métaux, une lame en céramique est nécessaire si le matériau est facilement magnétisable (par exemple les aciers maraging), sinon des lames HSS sont utilisées. Alors que les dispositifs de recouvrement durs assurent la meilleure répétabilité de la hauteur de couche, les dispositifs de recouvrement souples sont recommandées pour les pièces présentant un rapport d’aspect élevé. »
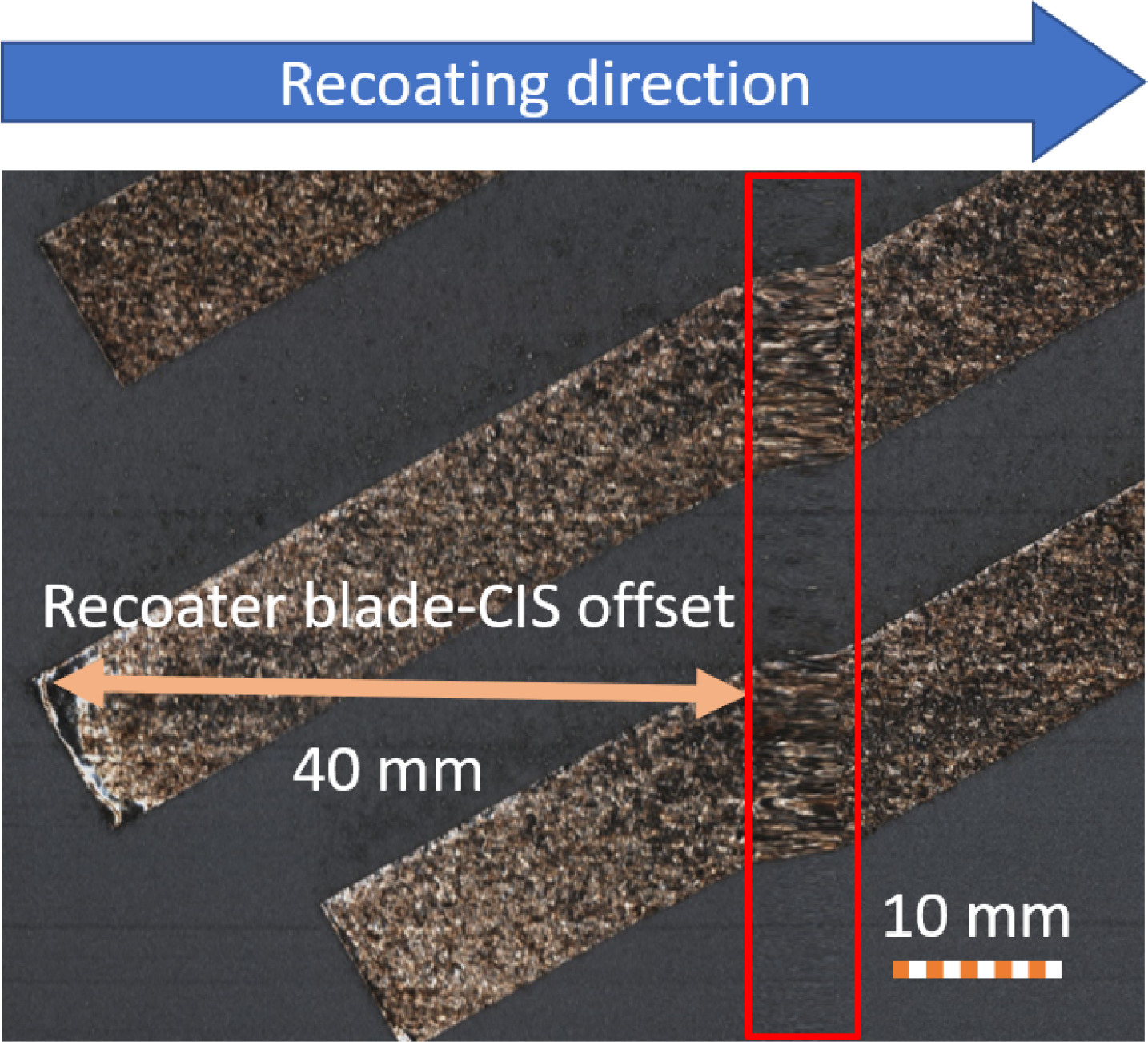
Quelques conseils sur le positionnement des pièces
Pour minimiser les déformations ou les échecs de fabrication et, dans une certaine mesure, garantir l’efficacité de la lame de rechargement à long terme, l’opérateur doit prêter attention au positionnement des pièces.
Dans l’idéal, une fois que le dispositif de recouvrement a étalé une couche de poudre, la zone du composant construit ne devrait pas bouger. Dans la pratique, en fonction de nombreuses variables, la pièce peut bouger, entraînant une distorsion qui peut exercer une pression sur le dispositif de recouvrement. Cette pression peut plier ou casser le composant, ou dans le pire des cas, endommager la lame du dispositif de recouvrement.
Un positionnement correct de la pièce peut contribuer à éviter ces problèmes. Par exemple, il est possible d’éviter que le dispositif de recouvrement entre en contact avec plusieurs composants imprimés en 3D à la fois. L’opérateur peut échelonner les pièces sur la plateforme de construction pour réduire ce risque.
Un autre exemple consiste à placer les pièces les plus hautes le plus près de la machine à recouvrir. En effet, certaines imprimantes 3D peuvent nécessiter une pause dans la fabrication et l’ajout de poudre pour fabriquer des pièces de grande taille.
Par ailleurs, vous ne voudrez peut-être pas placer vos composants imprimés en 3D directement l’un derrière l’autre. La raison en est que la fabrication peut continuer si la pièce ou le réceptacle est endommagé.
Enfin, certains fabricants de pièces explorent de plus en plus l’idée d’un contrôle in situ des défauts géométriques et de surface dans la fusion sur lit de poudre afin de surveiller le processus de recouvrement et de prévenir les problèmes susceptibles d’entraîner un échec de la fabrication.
Quelques mots sur les entreprises participantes
Open Additive est un fabricant de systèmes de fabrication additive métal (FA), de solutions de contrôle des processus et de produits et services connexes. L’entreprise fait partie du groupe Arctos, une société de R&D appliquée de premier plan qui définit la trajectoire de la prochaine génération de technologies de l’aérospatiale et de la défense. La société a récemment lancé AMSENSE Chimera with Recoat+ pour résoudre les problèmes liés au recouvrement pendant le processus de fabrication. La nouvelle offre AMSENSE Chimera with Recoat+ est spécialement conçue et réglée pour identifier les problèmes liés au processus de recouvrement sur les machines EOS M400 et M290. Elle constitue une plate-forme de détection tierce abordable qui augmentera le rendement et réduira les échecs de fabrication sur les machines LPBF les plus critiques et les plus répandues sur le marché de l’aérospatiale.
EOS fabrique des systèmes de FA pour les polymères et les métaux. L’entreprise propose une large gamme de dispositifs de recouvrement durs et souples. En fonction de la magnétisabilité, une lame HSS (standard) ou une lame en céramique (poudres magnétisables) sera utilisée. Même si elle offre à ses clients un maximum de flexibilité et d’ouverture, l’entreprise indique que la configuration du dispositif de recouvrement dur est, dans la plupart des cas, l’option préférée. Les dispositifs de recouvrement souples sont les suivants :
- Deux types de lames pour polymères : Silicone et NBR pour différentes plages de température et exigences de rigidité.
- Une brosse en fibre de carbone, qui est encore plus indulgente pour les pièces fragiles et à rapport d’aspect élevé qu’un dispositif de recouvrement souple pour polymères. Toutefois, si la brosse est endommagée par des arêtes saillantes ou une croissance hors plan due à des contraintes internes, il est également plus coûteux de remplacer ce type de dispositif.
Sur la base d’études détaillées des différents types de dispositifs de recouvrement, l’entreprise recommande la bonne configuration en fonction du cas d’utilisation.