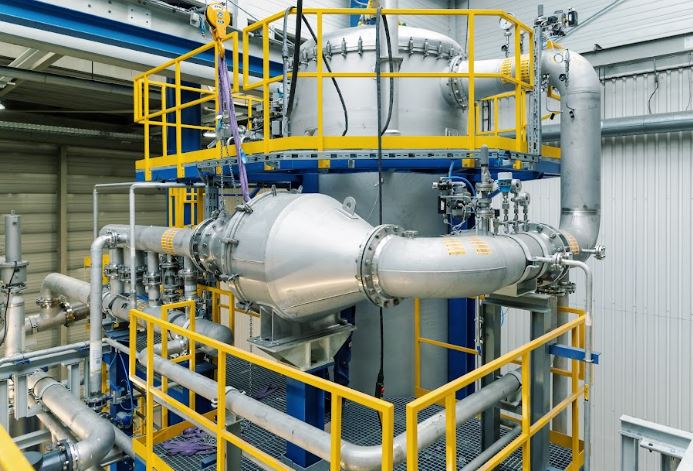
Il existe un certain nombre de raisons pour lesquelles on peut choisir l’acier inoxydable pour les processus de fabrication additive (FA), notamment ses propriétés mécaniques et de corrosion supérieures à celles d’autres types d’acier (ce qui signifie que le composant durera plus longtemps), et son caractère durable. Dans l’article ci-dessous, Andoni Sanchez-Valverde Erice, ingénieur commercial/R&D chez le producteur de poudres métalliques Outokumpu, explique certaines des considérations techniques clés dans la production de poudres d’acier inoxydable sphériques.
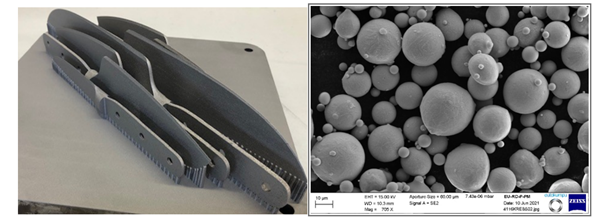
Actuellement, l’acier inoxydable est la troisième matière première préférée des industries de FA, derrière les alliages de titane et les alliages de nickel. Toutefois, selon le cabinet de consultance AMPOWER, d’ici à la fin de 2027, l’acier inoxydable sera la matière première la plus utilisée, avec une part de marché de 33 %.
Production de poudre d’acier inoxydable
La poudre d’acier inoxydable est produite par le procédé d’induction sous vide et d’atomisation par gaz inerte (VIGA) illustré à la figure 2. Ce procédé permet d’obtenir des poudres métalliques hautement sphériques d’un diamètre compris entre 0 et 300 µm.
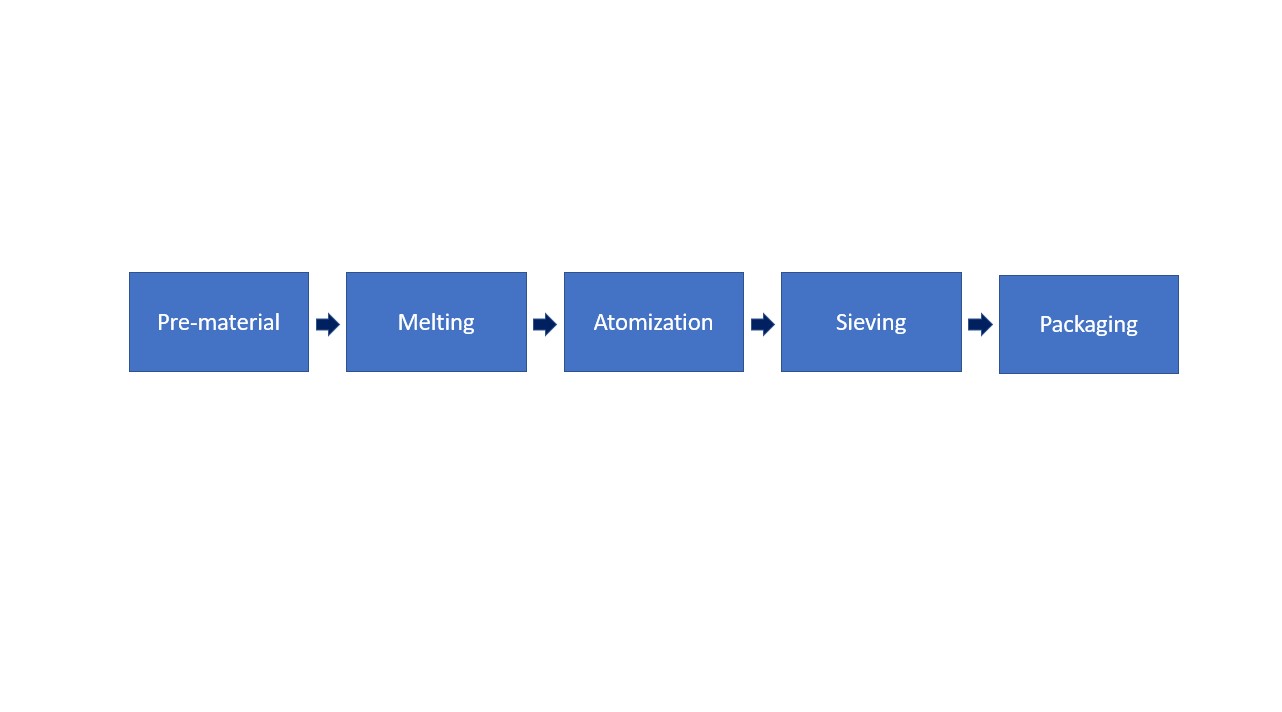
Les détails de l’équipement du procédé sont présentés dans la figure 3.
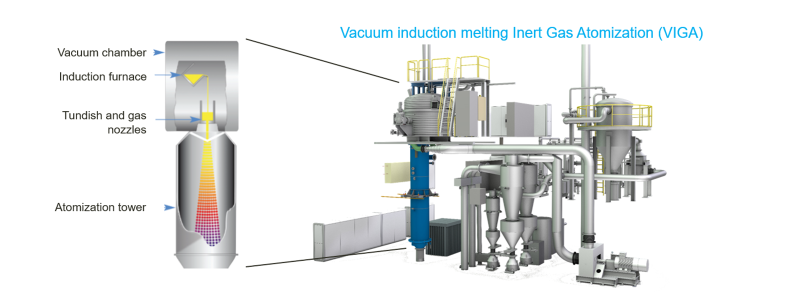
Prématériau : Dans la plupart des cas, le pré-matériau est constitué de déchets provenant de la transformation de produits plats. Le matériau est ensuite découpé en petits morceaux adaptés au processus – généralement 25 x 25 x 1~4 mm. Ces petits morceaux sont ensuite placés dans le creuset du four.
Fusion : Elle s’effectue sous vide afin d’éviter une éventuelle contamination par l’oxygène et la combustion d’éléments importants de la matière fondue. Il est possible de mesurer et de contrôler tous les paramètres importants du processus, tels que la température, la pression et le vide. La matière fondue peut également être analysée chimiquement pour vérifier si un alliage supplémentaire est nécessaire pour obtenir la bonne composition. Lorsque la matière fondue est prête, le four est rincé à l’argon ou à l’azote et le processus de coulée commence.
Atomisation : La matière fondue s’écoule à travers le répartiteur et est atomisée en très petites gouttelettes par de l’azote ou de l’argon à haute pression et à haute température (jusqu’à 32 bars et 450 °C). Les petites gouttelettes se solidifient en forme de sphère et volent à travers les tuyaux jusqu’au cyclone. La poudre solidifiée y est séparée du gaz et recueillie dans les bacs de collecte.
Tamisage : La poudre est séparée en différentes fractions par un tamisage mécanique et un classificateur à air afin de cibler différentes technologies de métallurgie des poudres. Si, par exemple, un client ne souhaite pas que plus de 5 % de sa poudre ait une taille inférieure à 20 µm, le classificateur à air peut être utilisé pour séparer les poudres les plus petites du lot.
Pourquoi le choix du gaz d’atomisation est-il important ?
Il y a quatre raisons principales pour lesquelles un client peut choisir l’azote (N) ou l’argon (Ar) comme gaz d’atomisation de ses poudres :
Le prix : L’azote est moins cher que l’argon. Cela a un impact sur le prix de la poudre finie. La poudre atomisée avec de l’argon sera plus chère.
La morphologie : La capacité thermique de l’argon est inférieure à celle de l’azote. Par conséquent, la poudre atomisée avec de l’argon a plus de temps pour atteindre la morphologie sphérique souhaitée avant de se solidifier. Les poudres atomisées avec de l’azote se solidifient plus rapidement et prennent une forme plus irrégulière, même si elles sont encore très sphériques.
La proportion de poudres fines : Lors de l’atomisation d’un lot dans les mêmes conditions de température et de pression, la proportion de poudres fines – qui sont intéressantes pour certaines technologies de FA – est plus élevée lorsque l’on utilise de l’azote. L’explication complète de ce phénomène est assez technique. La raison en est simple : les atomes d’azote sont plus petits et, à température et pression égales, il faut donc moins d’énergie pour diviser le métal en un plus grand nombre de petites gouttelettes.
Les propriétés des poudres : Les propriétés mécaniques et de corrosion des poudres peuvent être influencées par le gaz d’atomisation. Par exemple, l’azote peut augmenter à la fois l’usinabilité et les propriétés de corrosion des pièces imprimées.
Le système antisatellite fait une différence cruciale
Le système anti-satellite est une caractéristique essentielle de la production de poudres. Les satellites sont de petites gouttelettes qui adhèrent aux grosses particules sphériques (voir figure 4). Pour éviter cela, de l’argon ou de l’azote est recirculé dans la tour d’atomisation. Ce gaz pousse les très petites gouttelettes vers le bas, ce qui réduit la probabilité de présence de satellites dans les particules en cours de solidification.
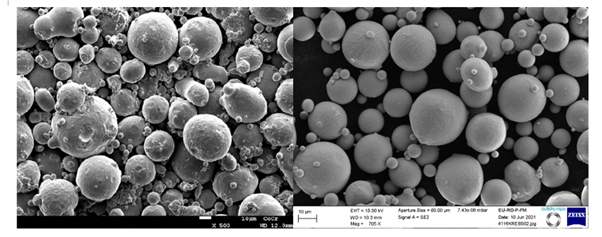
La présence de satellites plutôt que d’une poudre lisse et ronde aura un impact sur la qualité des composants imprimés 3D de deux manières :
L’étalement : L’étalement de la poudre est réduit si elle présente des satellites plutôt que des poudres parfaitement sphériques. Ceci est important pour la partie du processus où la couche de poudre suivante est étalée sur la couche de poudre existante par le recouvreur.
La morphologie : Les satellites réduisent la densité apparente et le tassement de la poudre. Si la densité de la poudre est réduite, le risque d’échec dans le processus de FA est plus élevé, en raison des pores ou des espaces d’air entre les particules.
La nécessité de disposer d’une gamme de tailles de poudre
Chaque technologie de métallurgie des poudres nécessite des poudres de tailles différentes. C’est pourquoi les poudres se différencient non seulement par leur qualité et le gaz utilisé pour l’atomisation, mais aussi par leur taille. Les poudres jusqu’à 300 µm conviennent aux technologies d FA et de métallurgie de poudres :
- Technologie de projection de liant (BJT) : <20 µm
- Fusion laser sur lit de poudre (PBF-LB) : 15 à 45 µm et 20 à 63 µm
- Fusion sur lit de poudre par faisceau d’électrons (PBF-EB) : 20 à 150 µm
- Dépôt direct d’énergie (DED) : 20~45 à 150 µm
- Moulage par injection de métal (MIM) : <20 µm
- Pressage isostatique à chaud (HIP) : 0-300 µm
Extension du champ d’application des nuances d’acier inoxydable
À l’heure actuelle, les nuances d’acier inoxydable les plus largement utilisées dans le cadre de la FA et d’autres technologies des poudres sont le 316L et le 17-4PH. Toutefois, un certain nombre de nouvelles nuances d’acier deviennent disponibles pour le secteur de la FA et répondent mieux aux exigences des applications de haute performance.
Les aciers inoxydables « de base » utilisés dans les technologies de FA sont les suivants :
- 316L (1.4404) : une alternative à faible teneur en carbone à l’acier 316. Cela minimise la précipitation de carbure à la suite d’un apport de chaleur, par exemple pendant le soudage, ce qui améliore la résistance à la corrosion intergranulaire. Le 316L/4404 convient à une grande variété d’applications dans les industries automobile, chimique, pétrochimique et médicale. Les produits typiques comprennent les brides, les vannes et les appareils médicaux.
- 17-4PH (1.4548) : l’acier martensitique bien connu à durcissement par précipitation (PH) avec des éléments d’alliage tels que le chrome ou le nickel. Il possède de bonnes propriétés de corrosion et d’excellentes propriétés mécaniques jusqu’à 300°C. Il est utilisé dans les industries aérospatiale, papetière et nucléaire pour des produits tels que les garnitures mécaniques, les pompes ou les pales de turbines.
Les nuances d’aciers inoxydables spéciaux à valeur ajoutée sont les suivantes :
- 904L (1.4539) : Nuance spéciale pour les environnements à forte corrosion. Il s’agit d’un acier inoxydable austénitique à forte teneur en nickel et en molybdène qui présente une très grande résistance à la corrosion. Développé à l’origine pour la manipulation de l’acide sulfurique à température ambiante, il est aujourd’hui utilisé dans une large gamme d’applications dans les industries pétrolières, gazières et chimiques. Les pièces typiques produites en 904L sont les pompes, les vannes et les brides.
- 253MA (1.4835) : Nuance spéciale pour les applications à haute température. Il s’agit d’un acier inoxydable austénitique doté d’une excellente résistance à l’oxydation et au fluage dans des conditions cycliques, qui est le mieux adapté aux températures allant jusqu’à 1150°C. Il est utilisé dans les industries du pétrole et du gaz, de l’aérospatiale et du sport automobile pour des pièces telles que les raccords et les échangeurs de chaleur.
- 4116 : Nuance spéciale qui est un acier inoxydable martensitique à haute dureté offrant une meilleure résistance à la corrosion et à l’usure que les autres aciers inoxydables martensitiques. Elle est utilisée dans les secteurs de la santé et des biens de consommation pour des produits tels que les appareils médicaux et les couteaux.
- La poudre d’acier inoxydable austénitique sans nickel (modifié 1.4678) : Cette poudre d’acier inoxydable sans nickel spécialement développée est un substitut idéal aux alliages 316L ou Co-Cr. C’est également une qualité parfaite pour éviter les réactions allergiques au nickel dans les applications de santé ou les applications de biens de consommation pour des produits tels que les montres et autres articles portés près du corps.
Des alliages à base de nickel (Ni) sont également disponibles :
- Alliage 625 : Pour une utilisation dans des environnements très difficiles et corrosifs à des températures élevées. L’alliage 625 combine du nickel, du chrome, du molybdène et du niobium qui lui confèrent d’excellentes propriétés de corrosion et d’excellentes propriétés mécaniques. Comparé à l’alliage 718, l’alliage 625 présente une plus grande résistance globale à l’oxydation. Il est utilisé dans les industries du pétrole et du gaz, de l’aérospatiale et de la défense pour des composants tels que les raccords, les pièces de fusée, les échangeurs de chaleur et les cuves.
- Alliage 718 : cet alliage à base de nickel est également utilisé dans des environnements à forte corrosion et à des températures élevées. Il contient du molybdène, du tantale, de l’aluminium et du titane qui lui confèrent une plus grande résistance et une meilleure soudabilité, ainsi qu’une meilleure résistance à la fissuration par corrosion sous contrainte (FCC) que l’alliage 625. Il est utilisé dans les industries du pétrole et du gaz, de l’aérospatiale et de la défense pour des composants tels que les raccords, les pièces de fusée, les échangeurs de chaleur et les cuves.
Faire passer la FA au niveau supérieur :
La disponibilité accrue des poudres d’acier inoxydable ouvrira de nouvelles possibilités aux concepteurs qui souhaitent créer des pièces par FA qui offrent une résistance à la corrosion, une durabilité et une longue durée de vie.
En tant que fabricant d’acier inoxydable, Outokumpu apporte ses connaissances à l’industrie en lançant une nouvelle activité pour soutenir la FA. Cela comprend la mise en service d’une usine d’atomisation dans notre usine de Krefeld, en Allemagne. Cette usine de poudre est en fait une grande unité de recyclage qui utilise les déchets issus des processus de production existants.
Cet article a été initialement publié dans le numéro de Mai/Juin de 3D ADEPT Mag