Although it operates in a critical market often subject to confidentiality when it comes to revealing how it uses AM, we know Pratt & Whitney has built up expertise in using AM for the MRO of commercial engines. History shows that Pratt started using AM in the late 1980s long before the technology became mainstream. Today, the RTX Additive Manufacturing Process and Capability Center – the company is part of – focuses on developing additive tools and integrating them into production.
The company recently shared how it has been advancing AM for the development of the TJ150 engine. By relying on an AM technique called unitization, Pratt & Whitney engineers have reduced the total part count from over 50 to just a handful.
Unitization naturally results in a lower part count, decreased weight and volume, quicker and more efficient assembly processes, reduced quality control costs, and a more streamlined supply chain. This technique drove many benefits a few years ago during the development of this RF passive hardware design.
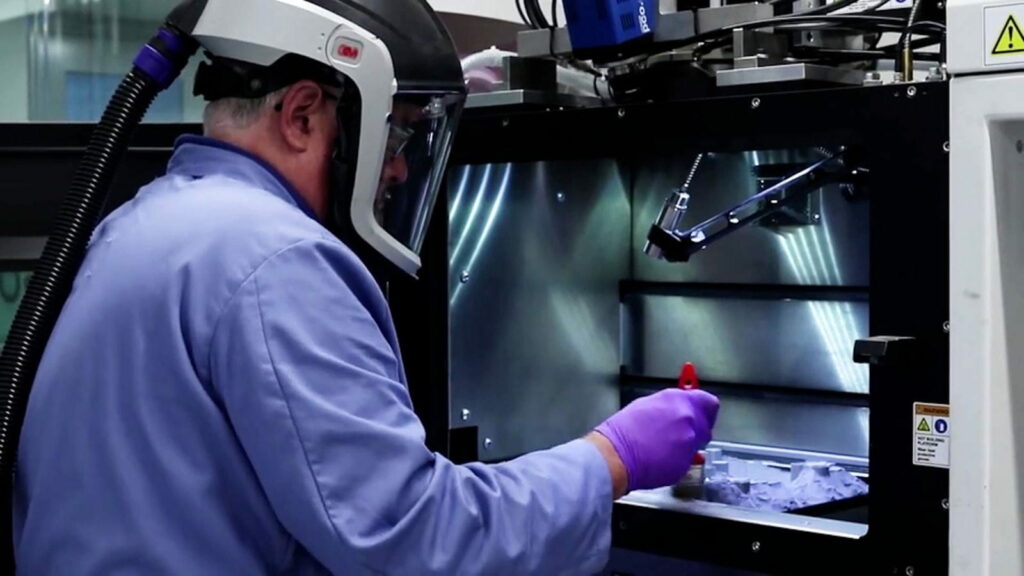
A technician operates a 3D printing machine. The face shield protects from the materials used, which can come in the form of fine powders.
For the redesign of this engine, the Pratt team worked with GATORWORKS, a newly formed prototyping arm within the company that focuses on the rapid and agile development of lower-cost military engines.
The teams tested two generations of additive hardware in military engines and are now additively manufacture other TJ150 components. The project also involved the development of TJ150 turbojet via Additive Manufacturing and this process would involve reducing the number of parts from fifty to fewer than five.
“Pratt & Whitney is [also] upgrading the F135 engine with technology from multiple development programmes to deliver increased capability and performance for the warfighter,” stated Chris Johnson, vice president of the company’s F135 programme. “Upgrading the F-35’s propulsion system to ECU is a critical step toward ensuring the F-35 remains the world’s premier air dominance fighter.”
Remember, you can post job opportunities in the AM Industry on 3D ADEPT Media free of charge or look for a job via our job board. Make sure to follow us on our social networks and subscribe to our weekly newsletter: Facebook, Twitter, LinkedIn & Instagram! If you want to be featured in the next issue of our digital magazine or if you hear a story that needs to be heard, make sure to send it to contact@3dadept.com