Phase3D, an expert in-situ monitoring for additive manufacturing, correlates measurable metal powder bed fusion build anomalies to final part defects in real-time. This work was done for the United States Air Force and NASA, two well-known aerospace part producers who rely on AM, and validated with two materials on two different laser powder bed fusion (PBF) machines.
Phase3D has worked closely with the U.S. Air Force and NASA to develop Fringe Research, an in-situ monitoring product which measures, in microns, every layer of a powder-based AM build. As a reminder, the system automatically identifies anomalies from the build process to help improve the AM process. Leveraging Phase3D’s expertise in repeatable, calibratable, and unit-based measurements and analytics, Fringe Research can be used on most powder-based AM systems and employs structured light, a well-known and understood metrology technology, to create the measurements used for this correlation.
The company explains that its measurement technology, Fringe Research, does not use artificial intelligence (AI) or machine learning (ML) to create measurements or identify anomalies. It gathers objective data to reduce project lead time, increase machine utilization, and ensure build quality.
Materials leveraged
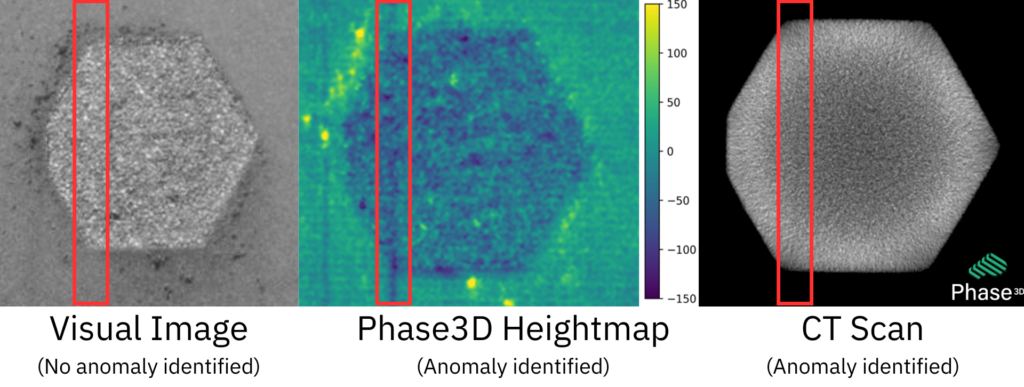
Phase3D printed with Ti64 for the U.S. Air Force and GRCop-42 for NASA to determine the effect of detectable build variation on part quality. The builds included an anomaly generator, which created realistic, geometry-based powder and melted anomalies, including hops and streaks patterns seen in most AM builds. While measuring the build, Fringe Research automatically identified hops and streaks that were later correlated to porosity in the final part. Parts were inspected using CT scanning and correlation was done in Fringe Research and a commercial CT inspection software.
For Ti64 printed on an EOS M290 for the U.S. Air Force:
- 81% of Fringe Research identified anomalies correlated to part defects detected by CT
- 100% of Fringe Research identified anomalies ≥47um depressions correlated to defects detected by CT
For GRCop-64 on a Colibrium Additive (previously GE Additive) M2 for NASA:
- 83% of test specimen identified defects were correlated to layers with Fringe Research identified anomalies
- 100% of Fringe Research identified anomalies ≥42um depressions correlated to defects detected by CT
“Providing our customers a high correlation of measurable build anomalies to part defects is changing what is possible for AM,” says Niall O’Dowd, Founder and CEO of Phase3D. “Our customers continue to request objective data that can identify part defects when they occur. With the data Fringe Research collects, we predict our aerospace customers will be able to increase machine throughput by more than 10% every year by stopping parts that will fail inspection early.”
Fringe Research is shifting the paradigm of in-situ monitoring by measuring the entire build surface three times during every layer. Engineers, designers, quality assurance staff, and managers will no longer guess why a part failed. Fringe Research provides its users with the tools to identify the cause of failure and improve the process quickly. Historically, Phase3D customers relied on visual images from the machine to either identify anomalies using AI/ML or an engineer to watch a video of the visual images or scroll through them. This is not reliable, effective, or smart. Phase3D’s heightmaps and Fringe Research allow everyone the opportunity to identify how to build anomalies impact part quality, including CT-identified defects, fatigue life, tensile strength, and more.
Phase3D will be showcasing the correlation data for the U.S. Air Force and NASA during RAPID + TCT 2024 in Los Angeles, California from June 25-27, 2024. You can visit Phase3D at Booth 1063.
Remember, you can post job opportunities in the AM Industry on 3D ADEPT Media free of charge or look for a job via our job board. Make sure to follow us on our social networks and subscribe to our weekly newsletter : Facebook, Twitter, LinkedIn & Instagram ! If you want to be featured in the next issue of our digital magazine or if you hear a story that needs to be heard, make sure to send it to contact@3dadept.com