Although end-users in the consumer goods industry do not always ask themselves what technology was used for the manufacturing of their products, applications of additive manufacturing in this field of activity are the ones that will further foster the growth of this technology. The latest example that we saw in this industry is the skiing goggles that have been shared by OECHSLER.
Known for manufacturing automotive and medical parts, the company has been supplying 3D printed parts since 2017. It relies on HP and Rösler’s AM technologies at the production level, and it is also known for its partnership with AREVO.
OECHSLER believes that the multiplicity of parts leads to a higher failure potential during production, higher risk of product failure, and ultimately higher costs. That’s why, at the beginning of the winter season, they decided to explore a technique that would provide more comfort and functionality to one of the most used sporting goods product of this season: skiing goggles.
The company wanted to simplify the manufacturing process of goggles and that’s something that was easily achievable in a low volume production. Using AM lattice technology, the product development process required a start-to-finish product timeline of around four weeks.
The manufacturing process
Normally, 13 parts are used to manufacture a single pair of skiing goggles. That’s pretty high for such a standard sporting goods article, right?
Using AM could enable to reduce this number of parts but also require to rethink the manufacturing process. According to the team at OECHSLER, “the used PU foam should be replaced by an additively manufactured lattice structure, the number of parts should be minimized to the bare minimum and the wearing comfort increased.”
The company needed to take a reverse-engineering approach to achieve this goal. In this vein, the team first disassembled the lens swap including the rotatable element for lens removal. This rotatable element is crucial as it facilitates the change of lenses during certain weather conditions or when they are no longer functional. The next part that was disassembled was the outer frame, which is held by clips, and in the end, the buckets holding the elastic band.
During the redesign process, the design team of the German manufacturer had two possibilities: either create an all-in-one product and eliminate all mounting steps or reduce elements so that the foams would be replaced with a 3D-printed lattice.
The team went for the first path and decided to scan all parts via CT to gain deeper insights into the component dimensions. Thereafter, they reconstructed each of these parts in a vector-based program to generate a suitable print file for the solid and lattice parts.
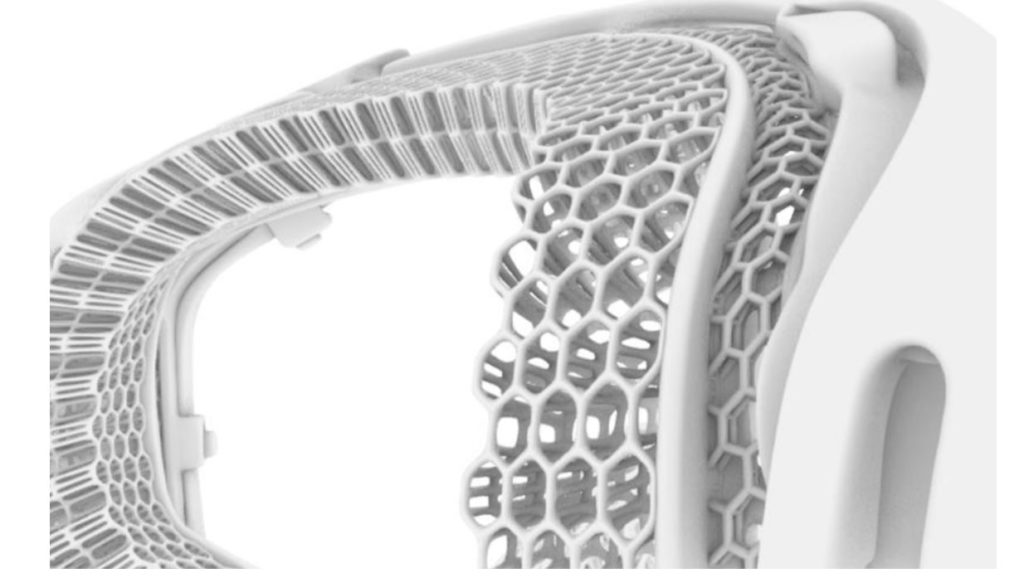
Despite their experience, like many companies, the team also faced a failure in the first attempt in creating the print files. They explain that the first prints were too stiff, therefore, the handles were not flexible enough. “Contrary to the initial assumption, this was not caused by the print file but by the post-processing steps in production. The lattice structure needed a different and more intense cleaning of the lattice structures to remove more of the printing residue. Even though optimizing the print file has been quite fast, the adjustment of the post-processing to increase the flexibility of the lattice structure was challenging.”
In the end, results demonstrate the following advantages by applying AM to the fabrication of these skiing goggles:
- Increased wearing comfort and integrated damping function in case of an accidents
- Combination of rigid and soft elements in one component
- Movable joints instead of extra parts like clips
- Reduction of material variety leading to easier recycling at the end of the product life cycle
- Reduction of production costs due to the elimination of mounting steps
- Foam replaced by 3D printed lattice structure: adjustable hardness – the existing multi-layer foams can be replaced
Remember, you can post job opportunities in the AM Industry on 3D ADEPT Media free of charge or look for a job via our job board. Make sure to follow us on our social networks and subscribe to our weekly newsletter : Facebook, Twitter, LinkedIn & Instagram ! If you want to be featured in the next issue of our digital magazine or if you hear a story that needs to be heard, make sure to send it to contact@3dadept.com