
It’s always a pleasant discovery to see what a company that debuts in 3D Printing has produced for the first time. MAHLE, a supplier to the automotive industry and expert in mobility, chose to produce high-performance aluminum pistons. A production that was achieved as part of a collaboration with car manufacturer Porsche and mechanical engineering company Trumpf.
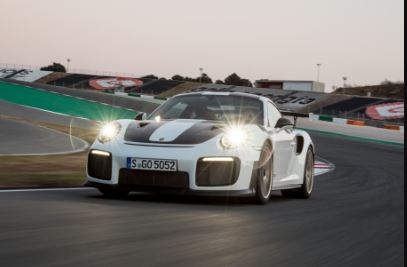
How is it different from a conventional manufacturing process of pistons?
According to specialists, pistons that are usually produced by forging easily reach their performance potential. Porsche has proved out that the power of its 700 HP engine could be boosted by 30 HP with an associated increase in efficiency.
That’s why, in their new approach to manufacturing, the team has opted for a bionic design which exactly reproduces natural structures of the part. Indeed, MAHLE’s experience in thermal processes has enabled the team to design a piston which can only be produced using 3D Printing technologies.
A special aluminum alloy developed by MAHLE is thereafter added in loaded areas, which facilitates the facilitates the adaptation of the piston structure to the load. It should be noted that the alloy is atomized into a fine powder before being printed on Trumpf’s laser metal fusion technology.
Proceeding this way enables the team to save material and to produce a more rigid 3D printed piston which is up to 20% lighter than its conventionally manufactured counterpart. Not to mention that Trumpf’s technology can produce piston blanks made up of approximately 1,200 layers in around 12 hours.
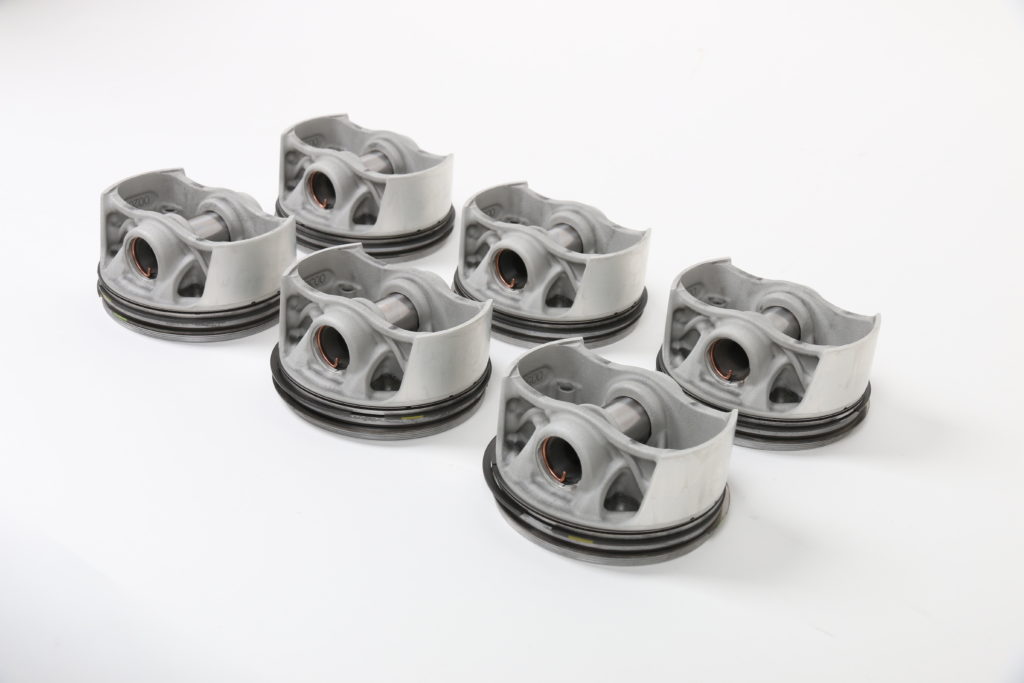
“This project involved multiple challenges. From the design of the piston through the specification of the material and the development of the appropriate printing parameters, we had to make many fine adjustments to achieve the optimum result,” explains Volker Schall, Head of Product Design in Advanced Engineering at MAHLE. “We have now not only mastered the technical side of things, but can also assess how the method can be embedded into existing manufacturing processes.”
Running a test on Porsche’s 911 GT2 RS sports car
It was crucial for the team to verify that the 3D Printed piston meets the same requirements than the conventionally manufactured one. Furthermore, a key focus was made on the central area of the piston, the skirt, and the place where it connects with the conrod, the pin bore. Since they are subjected to skirt pulsing and tear-off tests, the team should simulate the loads that would occur during other operations.
Numerous non-destructive tests were therefore performed by Zeiss using CT scanning, 3D scanning, and microscopy. Not only did the 3D Printed piston meet the requirements, but practical testing demonstrates that six pistons were fitted in the engine of the Porsche 911 GT2 RS.
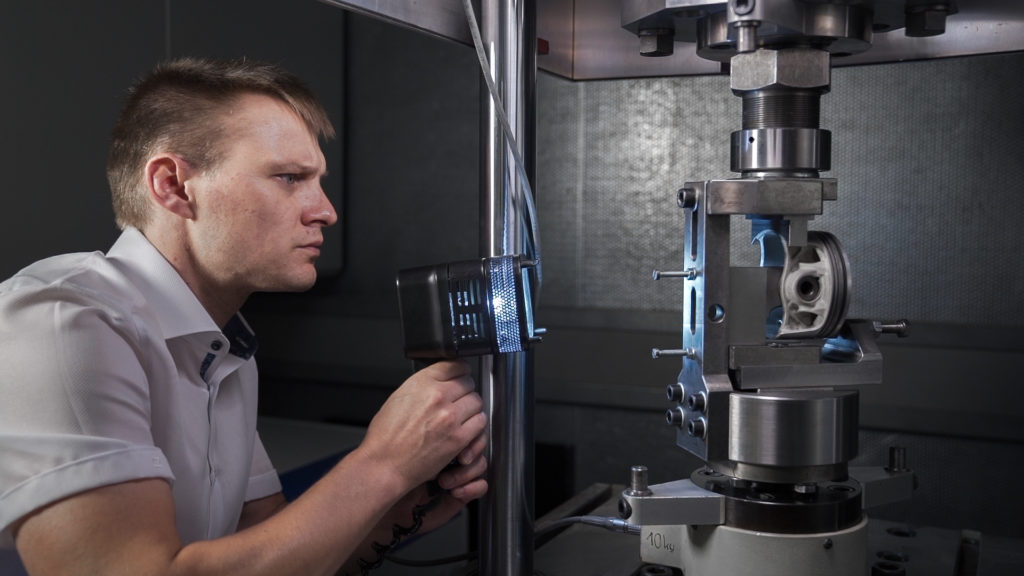
MAHLE explained in a press communication that the drive unit successfully completed 200 hours of endurance testing under the toughest conditions on the test bench. This comprised around 6,000 kilometers at an average speed of 250 km/h including refueling stops, and around 135 hours at full load. The test run also included 25 hours of motoring load, i.e., the simulated overrun mode of a vehicle.
Frank Ickinger, project manager at Porsche, comments: “Thanks to the close cooperation of everyone involved, we were able to demonstrate the potential of additive manufacturing in our top-of-the-line high-performance sports car, the Porsche 911 GT2 RS, thus clearing the way for its use in future drives. In terms of technology, this is the start of a new chapter for us, which opens up completely new possibilities in design and production.”
Remember, you can post AM job opportunities for free on 3D ADEPT Media or look for a job via our job board. Make sure to follow us on our social networks and subscribe to our weekly newsletter: Facebook, Twitter, LinkedIn & Instagram! If you want to be featured in the next issue of our digital magazine or if you hear a story that needs to be heard, make sure to send it to contact@3dadept.com