
C’est toujours une découverte agréable de voir ce qu’une entreprise qui débute dans l’impression 3D a produit pour la première fois. MAHLE, fournisseur de l’industrie automobile et expert en mobilité, a choisi de produire des pistons en aluminium de haute performance. Une production qui a été réalisée dans le cadre d’une collaboration avec le constructeur automobile Porsche et l’entreprise de construction mécanique Trumpf.
En quoi cela diffère-t-il d’un processus de fabrication conventionnel de pistons ?
Selon les spécialistes, les pistons qui sont généralement produits par forgeage atteignent facilement leur potentiel de performance. Porsche a notamment prouvé que la puissance du moteur de 700 CV de sa voiture de sport pouvait être augmentée de 30 CV avec une augmentation associée de l’efficacité.

C’est pourquoi, dans sa nouvelle approche de la fabrication, l’équipe a opté pour une conception bionique qui reproduit exactement les structures naturelles de la pièce. En effet, l’expérience de MAHLE en matière de procédés thermiques a permis à l’équipe de concevoir un piston qui ne peut être produit qu’à l’aide des technologies d’impression 3D.
Un alliage d’aluminium spécial développé par MAHLE est ensuite ajouté dans les zones chargées, ce qui facilite l’adaptation de la structure du piston à la charge. Il convient de noter que l’alliage est atomisé en une fine poudre avant d’être imprimé sur la technologie de fusion laser des métaux de Trumpf.
Ce procédé permet à l’équipe d’économiser du matériau et de produire un piston imprimé en 3D plus rigide, qui est jusqu’à 20% plus léger que son homologue fabriqué de manière conventionnelle. Sans compter que la technologie de Trumpf permet de produire des ébauches de piston composées d’environ 1 200 couches en 12 heures environ.
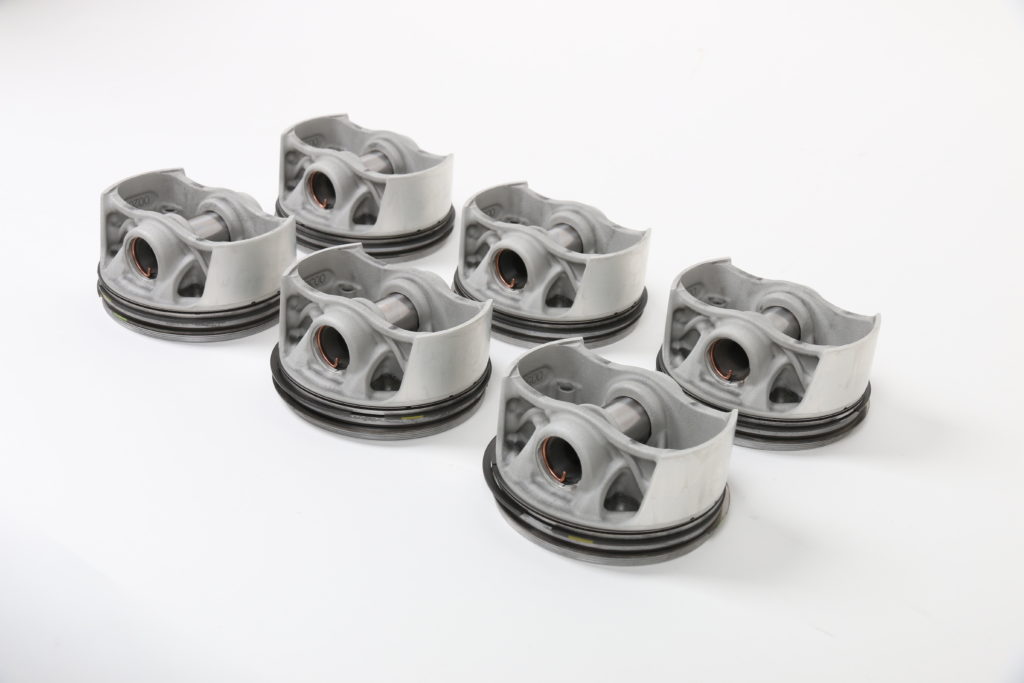
« Ce projet comportait de multiples défis. De la conception du piston à la spécification du matériau et au développement des paramètres d’impression appropriés, nous avons dû procéder à de nombreux ajustements fins pour obtenir un résultat optimal », explique Volker Schall, responsable de la conception des produits dans le domaine de l’ingénierie avancée chez MAHLE. « Nous avons maintenant non seulement maîtrisé l’aspect technique des choses, mais nous pouvons également évaluer comment la méthode peut être intégrée dans les processus de fabrication existants ».
Essai de la voiture de sport 911 GT2 RS de Porsche
Il était crucial pour l’équipe de vérifier que le piston imprimé en 3D réponde aux mêmes exigences que celui fabriqué de manière conventionnelle. En outre, l’accent a été mis sur la zone centrale du piston, la jupe, et l’endroit où il se connecte avec la bielle, l’alésage de l’axe. Comme ils sont soumis à des tests de pulsation et d’arrachement de la jupe, l’équipe doit simuler les charges qui se produiraient lors d’autres opérations.
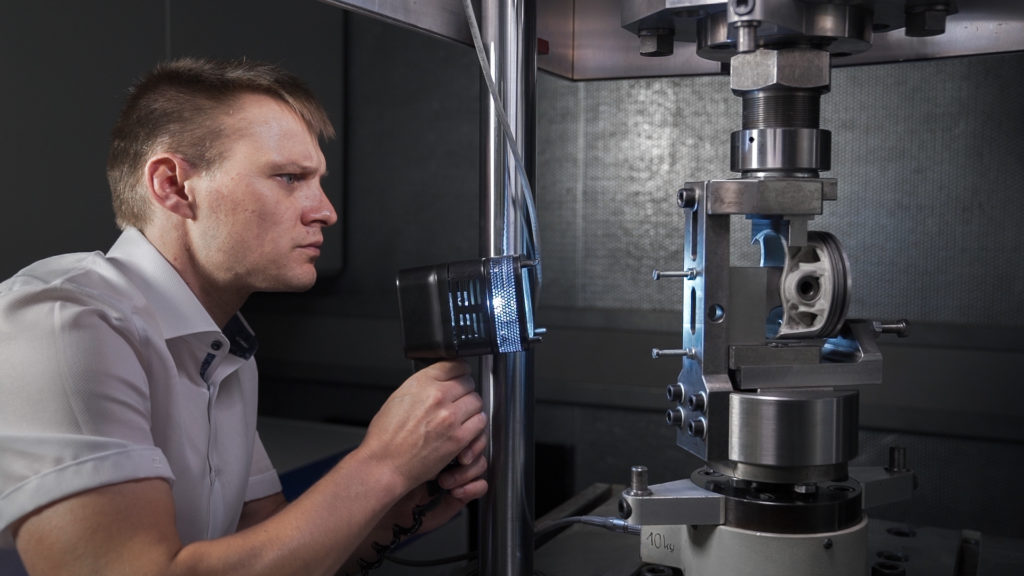
De nombreux tests non destructifs ont donc été effectués par Zeiss à l’aide de la tomodensitométrie, de la numérisation 3D et de la microscopie. Non seulement le piston imprimé en 3D répondait aux exigences, mais les essais pratiques ont démontré que six pistons étaient montés dans le moteur de la Porsche 911 GT2 RS.
MAHLE a expliqué dans un communiqué de presse que le groupe motopropulseur avait réussi 200 heures de tests d’endurance dans les conditions les plus difficiles du banc d’essai. Cela a représenté environ 6 000 kilomètres à une vitesse moyenne de 250 km/h, arrêts de ravitaillement compris, et environ 135 heures à pleine charge. Le parcours d’essai comprenait également 25 heures de charge moteur, c’est-à-dire le mode de dépassement simulé d’un véhicule.
Frank Ickinger, chef de projet chez Porsche, commente : « Grâce à l’étroite collaboration de toutes les personnes impliquées, nous avons pu démontrer le potentiel de la fabrication additive dans notre voiture de sport de haute performance haut de gamme, la Porsche 911 GT2 RS, ouvrant ainsi la voie à son utilisation dans les futurs entraînements. En termes de technologie, c’est le début d’un nouveau chapitre pour nous, qui ouvre des possibilités totalement nouvelles en matière de conception et de production ».
N’oubliez pas que vous pouvez poster gratuitement les offres d’emploi de l’industrie de la FA sur 3D ADEPT Media ou rechercher un emploi via notre tableau d’offres d’emploi. N’hésitez pas à nous suivre sur nos réseaux sociaux et à vous inscrire à notre newsletter hebdomadaire : Facebook, Twitter, LinkedIn & Instagram ! Si vous avez une innovation à partager pour le prochain numéro de notre magazine numérique ou si vous avez un article à faire connaître, n’hésitez pas à nous envoyer un email à contact@3dadept.com.