Le pressage isostatique à chaud (en anglais Hot isostatic pressing = HIP) est un procédé utilisé pour réduire la porosité et augmenter la densité des poudres, des pièces coulées et frittées dans un four à haute pression (100-200 MPa) et à des températures comprises entre 900 et 1250°C (1652°F et 2282°F). Pour garantir les propriétés des matériaux dans des environnements exigeants, le procédé a été un élément clé des processus de production en amont tels que le moulage, le MIM et, ces dernières années, la fabrication additive (FA). Dans le cas de la fabrication additive, le procédé a prouvé son efficacité dans l’élimination des défauts et l’amélioration des propriétés mécaniques des matériaux pour les composants critiques imprimés en 3D. Le dossier ci-dessous vise à comprendre comment et où exactement le procédé HIP peut influencer le processus de fabrication additive afin d’en tirer le meilleur parti.
Ce dossier fait partie de notre série d’articles sur le « post-traitement », qui vise à démystifier chaque tâche de post-traitement pouvant être utilisée à la fin de la production additive. Rappelons que le post-traitement est un terme générique qui recouvre une variété d’étapes que les pièces imprimées en 3D doivent subir avant d’être utilisées pour leur usage final. Il va sans dire que l’utilisation de chaque tâche de post-traitement dépend de plusieurs facteurs, notamment du processus de fabrication additive et des matériaux utilisés, ainsi que de l’objectif final à atteindre pour une pièce imprimée en 3D donnée.
Le procédé HIP est considéré comme un type de solution de traitement thermique qui peut être appliqué à des pièces fabriquées à la fois par FA et par des processus de fabrication traditionnels. Pour rappel, dans un dossier précédent, nous avons abordé le traitement thermique des pièces fabriquées de manière additive. Dans ce dossier, nous nous attacherons à aider les utilisateurs de la FA à comprendre :
- Les différences dans l’utilisation du HIP pour le moulage, le MIM et la FA
- Comment ce processus est réalisé pour les pièces imprimées en 3D en particulier
- Les décisions qui peuvent conduire à l’utilisation du procédé HIP
Les différences dans l’utilisation du HIP pour le moulage, le MIM et la FA
Même si le procédé HIP est principalement associé aux pièces métalliques, il convient de noter qu’il peut également être utilisé pour réduire la porosité et augmenter la densité des céramiques, des polymères et des matériaux composites. Si les métaux et les céramiques sont les matériaux les plus couramment utilisés avec le procédé HIP, Greg Lane, Key Account Manager chez Aalberts Surface Technologies, note que les alliages à base de Fe, Ni- et Ti (super-) sont quelques-uns des métaux typiques qui peuvent être traités par HIP, ainsi que l’aluminium (AlSi10Mg et A357), le Cu, le SS, les aciers à outils, les alliages de Co, le MCrAlY. C’est pourquoi, dans cet article, la plupart des exemples et des idées seront donnés en tenant compte des pièces métalliques imprimées en 3D.
Greg Lane explique comment la porosité et les défauts se produisent : « La porosité est générée au cours de la solidification dans les moulages à la cire perdue et la FA, ainsi qu’au cours du frittage. Un pore restant est toujours un point faible et peut servir de site d’initiation d’une fissure, limitant ainsi la durée de vie d’une pièce. Même un petit réseau de pores à l’intérieur d’une pièce facilite l’apparition et la propagation de fissures, en particulier lorsqu’elle est soumise à une charge cyclique. »
Si L’objectif du HIP reste le même – améliorer les propriétés des matériaux et éliminer les défauts – quel que soit le processus de fabrication utilisé, il y a quelques considérations spécifiques au moulage, au moulage par injection de métal (MIM) ou à la fabrication additive (AM).
Dans le cas du moulage, la tâche HIP vise principalement à résoudre les problèmes de porosité, tandis que dans le cas du MIM, elle permet d’améliorer la densité du produit final. En ce qui concerne la fabrication additive, la tâche HIP permet de résoudre les problèmes liés aux défauts et aux pores apparaissant au cours du processus de fabrication.
Il est cependant important de comprendre comment ce procédé fonctionne pour évaluer les considérations spécifiques liées aux pièces métalliques imprimées en 3D.
Comment ce processus est mis en œuvre pour les pièces imprimées en 3D.

En général, le processus HIP se déroule dans une cuve sous pression à l’intérieur d’un four chaud. Les pièces sont placées dans la chambre, qui est ensuite chauffée, remplie d’un gaz inerte comme l’argon pour la mettre sous pression, et maintenue à cette température pendant une durée déterminée. La chaleur et la pression sont appliquées uniformément à la pièce pour éliminer les trous. Parfois, le refroidissement rapide sous pression est également utilisé comme bain de refroidissement rapide. L’ensemble du processus peut durer de 8 à 12 heures, voire plus.
Le procédé HIP peut être utilisé avec des pièces produites par presque tous les procédés de FA des métaux. Dans sa liste des procédés les plus utilisés, Lane cite la fusion de lit de poudre par faisceau laser (PBF-LB), la fusion de lit de poudre par faisceau d’électrons (PBF-EB), la fabrication additive par arc de fil (WAAM), ainsi que le jet de liant.
En ce qui concerne le traitement HIP des pièces imprimées en 3D, Lane rappelle tout d’abord que la plupart des traitements HIP commerciaux appliqués aux pièces AM sont les mêmes que pour les pièces moulées, mais qu’ils ne sont pas optimisés.
« Toutefois, la nature du processus de FA est très différente de celle des procédés de fabrication susmentionnés. La solidification rapide pendant la fabrication produit une microstructure très fine aux propriétés uniques. Cette structure peut être jusqu’à deux ordres de grandeur plus fine que celle des pièces coulées à la cire perdue, même pour le même type d’alliage. C’est pourquoi un cycle HIP adapté peut avoir un impact positif considérable sur les propriétés d’une pièce obtenue par FA et sur la chaîne de production de FA elle-même », ajoute-t-il.
« Un cycle HIP typique commence par un chauffage où la pression et la température sont augmentées. Pendant le maintien/trempage, la combinaison d’une température élevée et d’une pression allant jusqu’à 200 MPa ferme les pores et les fissures du matériau. Les matériaux sont virtuellement fusionnés jusqu’à ce qu’ils soient exempts de défauts. Après un certain temps, le cycle se termine par un refroidissement. Les équipements HIP modernes permettent de régler les vitesses de chauffage et de refroidissement, car certains matériaux traités nécessitent des vitesses de refroidissement rapides ou fixes », poursuit-il.
Lane nous a appris que la température, la pression et le temps de maintien sont les trois principaux paramètres d’un cycle HIP qui déterminent la densification. Par ailleurs, même si les matériaux d’impression 3D à base de poudre sont généralement très denses, ils peuvent toujours présenter des défauts tels que des pores et des fissures internes. Ces défauts, y compris leur taille et leur occurrence, dépendent du type de poudre et de la manière dont elle est imprimée. Ils peuvent donc altérer les propriétés mécaniques du matériau, en particulier son comportement à la fatigue. Le processus HIP peut contribuer à relever ces défis et à produire un matériau relativement dense.
Les décisions qui peuvent conduire à l’utilisation du HIP plutôt que d’un autre procédé de post-traitement alternatif
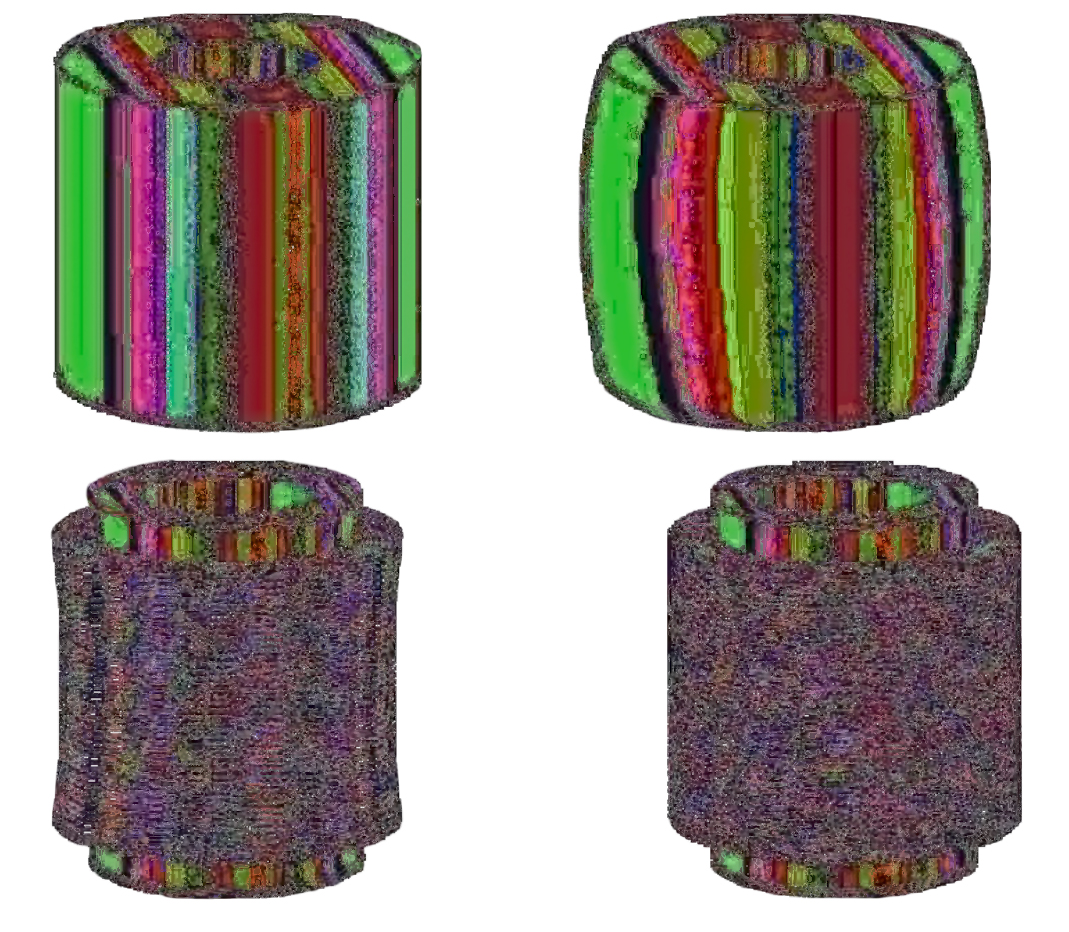
précontrainte (en bas). Sans pression (à gauche) et avec pression (à droite).
(à droite). Source : « Heat treatment of PM parts by Hot Isostatic Pressing par Anders Eklund »
Nombreux sont ceux qui connaissent l’utilisation du HIP pour la densification des pièces moulées dans les industries ayant des exigences très élevées en matière de résistance à la fatigue, telles que l’industrie aérospatiale et l’industrie des turbines à gaz. Il est intéressant de noter que la FA génère une demande croissante de HIP au-delà de ces industries.
Le procédé HIP a déjà permis la fabrication de différents types de composants tels que les pièces métalliques de grande taille et massives de forme quasi nette utilisées dans l’industrie pétrolière et gazière, pesant jusqu’à 30 tonnes, ou les roues de forme nette d’un diamètre pouvant atteindre un mètre – toutes ces pièces pouvant être produites par le biais de processus de FA. D’autres applications vont des implants orthopédiques aux voitures de course et aux moteurs de fusée.
Alors, quand et comment sait-on que le procédé HIP est l’étape de post-traitement qu’il convient d’utiliser pour une application donnée ? Pour Lane, tout dépend de la porosité :
« Un travail de fabrication bien contrôlé peut réduire la tendance à introduire des défauts internes tels que la porosité dans les pièces imprimées 3D à un niveau acceptable pour certaines applications non exigeantes. Cependant, pour des applications critiques dans des industries exigeantes telles que l’énergie, l’aérospatiale, la défense et la médecine, où la performance et la sécurité sont essentielles, la porosité doit être éliminée. En l’état, car sans HIP, la porosité résiduelle peut entraîner des différences de résistance mécanique (dispersion des propriétés), soit entre les pièces d’une même plaque construite, soit entre les différentes sections transversales de pièces plus grandes. Un réseau résiduel de pores facilite la propagation des fissures lorsqu’il est soumis à des charges cycliques dans les moteurs à réaction (pales) ou dans le corps humain (implants HIP) ».
Pour expliquer comment le procédé HIP peut généralement améliorer la productivité et la qualité des pièces critiques imprimées en 3D, il ajoute :
« Le procédé HIP n’est souvent qu’une partie de l’ensemble du processus de traitement. Un itinéraire traditionnel comprendrait un traitement de détente avant le traitement HIP et un recuit en solution et/ou un durcissement par précipitation après le traitement HIP, effectués dans un four sous vide. L’équipement HIP de pointe offre la possibilité d’incorporer la détente et le recuit/durcissement en solution dans le cycle HIP, car il est possible de réaliser des vitesses de chauffage définies avec des plateaux de maintien intermédiaires ainsi que des vitesses de refroidissement rapides. Cela permet de rationaliser la chaîne de post-traitement par FA, d’augmenter la productivité des imprimeurs et, en fin de compte, d’améliorer les propriétés mécaniques et la durée de vie des pièces imprimées 3D».
Le tableau ci-dessous résume les avantages du HIP capturé lorsqu’il est appliqué aux pièces AM et les domaines auxquels les opérateurs doivent encore prêter attention :
Principaux avantages | Faire attention à |
Élimination des défauts d’impression, quel que soit leur nombre | Des contraintes résiduelles peuvent apparaître dans le matériau introduit au cours du processus de FA |
Amélioration des propriétés de fatigue | En raison de leurs différences, les propriétés des métaux imprimés peuvent poser des problèmes au cours de la phase HIP. |
Aucune déformation de la forme nette des pièces imprimées 3D n’est à prévoir pendant la phase HIP | |
Une méthode de fabrication allégée, conduisant à des délais de production plus courts | |
Réduction de l’impact sur l’environnement (dans le cas de pièces de forme nette ou proche de la forme nette) |
Conclusion
Alors que les processus de HIP sont bien établis et compris pour des processus tels que les moulages, un livre entier reste à écrire pour documenter les spécifications de ces processus pour les pièces imprimées 3D. Si l’article ci-dessus constitue une première introduction au HIP, il est essentiel de garder à l’esprit que la diversité des propriétés des matériaux dans les pièces métalliques imprimées en 3D modifie continuellement la manière dont le procédé HIP peut être appliqué.
Néanmoins, comme le dit Lane, le HIP reste une étape de post-traitement qui améliore considérablement les performances du produit tout en offrant la possibilité de raccourcir les temps d’impression et de réduire les coûts finaux pour les entreprises utilisant la FA.
Notes de l’éditeur
Pour discuter de ce sujet, nous avons invité une entreprise dont l’expertise dans ce domaine a été reconnue dans plusieurs secteurs adoptant les technologies de FA et au-delà :
Aalberts surface technologies, un fournisseur mondial de services de technologie de surface. En tant que fournisseur de services complets de solutions spécialisées de traitement thermique, les systèmes HIP de pointe ont été ajoutés aux capacités existantes de traitement thermique (traitement thermique sous vide) de l’entreprise dans son installation Nadcap de Greenville (S.C.) afin de répondre aux besoins spécifiques des industries aérospatiales et de production d’énergie. Selon le fournisseur de services, les avantages de la logistique et de la manutention en termes de réduction des coûts, ainsi que l’amélioration des délais d’exécution par rapport aux normes de référence de l’industrie, confèrent à ses clients un avantage sur leurs concurrents. Cet avantage leur permet d’augmenter leur trésorerie grâce à des délais d’exécution plus courts et de commercialiser leurs produits plus rapidement.