En septembre 2015, les chercheurs du MIT ont démontré la possibilité d’imprimer en 3D des objets en verre optiquement transparents. Le principal défi à l’époque était la température élevée nécessaire pour faire fondre le matériau, température qui ne permettait pas à l’objet d’avoir deux attributs souhaités : la solidité et la transparence.
Cet obstacle avait été surmonté par un système qui a pu conserver ces propriétés, permettant ainsi d’obtenir des objets en verre imprimés 3D qui sont à la fois solides et totalement transparents à la lumière. Aujourd’hui, Chikara Inamura, Michael Stern, Daniel Lizardo, Peter Houk et Neri Oxman, les chercheurs de ce projet discutent de l’évolution de cette imprimante 3D.
Pour mettre à niveau l’imprimante 3D de verre G3DP2, les principaux objectifs des chercheurs étaient de :
– Développer une imprimante 3D à base de verre fondu à l’échelle industrielle en prolongeant les recherches précédemment menées au MIT et en améliorant les propriétés des matériaux et la gamme de produits qui pourraient être fabriqués.
– Développer une structure de verre imprimée en 3D à l’échelle architecturale pour évaluer les capacités pratiques du nouveau système dans une production industrielle.
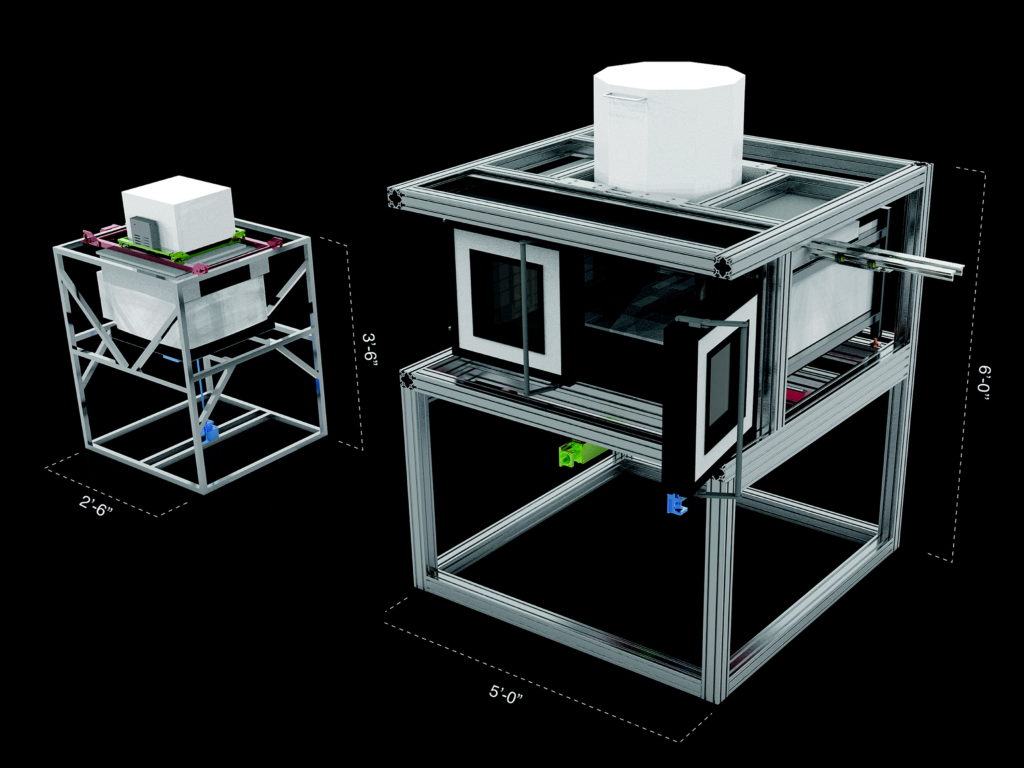
Dans l’architecture de la nouvelle imprimante 3D, l’énergie thermique appliquée au système de chauffage permet à la charge mécanique du système de mouvement de fonctionner de manière indépendante. Même s’il en résulte une certaine durabilité des systèmes, les propriétés des matériaux et l’analyse des pièces constitutives ont tout de même nécessité un examen attentif. De plus, « l’accent a été mis sur la tête d’impression elle-même, située à l’interface entre les modules et exigeant les performances thermiques et mécaniques les plus élevées de son choix de matériaux ».
Comprendre le comportement des matériaux dans une large gamme de températures a donc été un défi majeur dans ce développement. L’équipe a démontré comment elle a trouvé une solution en imprimant en 3D des colonnes de verre de trois mètres de haut pour l’exposition Lexus « Yet » à la Milan Design Week 2017.
En effet, 15 composants en verre imprimé 3D ont été assemblés de manière verticale avec « des systèmes de menuiserie à film mince en silicone et de poteaux en acier pour assurer la stabilité verticale ». Les colonnes intégraient un module d’éclairage LED mobile fixé sur un système de mouvement. Les rayons lumineux en mouvement et la forme des structures vitrées ont créé un beau spectacle.
« A l’avenir, en combinant les avantages de cette technologie de FA avec la multitude de propriétés matérielles uniques du verre telles que la transparence, la résistance et la stabilité chimique, nous pourrions voir apparaître de nouveaux archétypes d’éléments de construction multifonctionnels », concluent les chercheurs. « Les tubes de verre transparents et à section creuse agissent simultanément comme un système de chauffage, de ventilation et de climatisation (CVC), jouant à la fois le rôle de structure à l’échelle du bâtiment, à travers lesquelles les milieux synthétiques et biologiques circulent et réagissent à la lumière solaire et à la température ambiante, régulant passivement le bâtiment et éclairant l’espace intérieur. ».
Pour des informations exclusives sur l’impression 3D, abonnez-vous à notre newsletter et suivez-nous sur les réseaux sociaux !
Vous souhaitez-vous abonner à 3D ADEPT Mag ? Ou vous voulez figurer dans le prochain numéro de notre magazine numérique ? Envoyez-nous un email à contact@3dadept.com
//pagead2.googlesyndication.com/pagead/js/adsbygoogle.js
(adsbygoogle = window.adsbygoogle || []).push({});