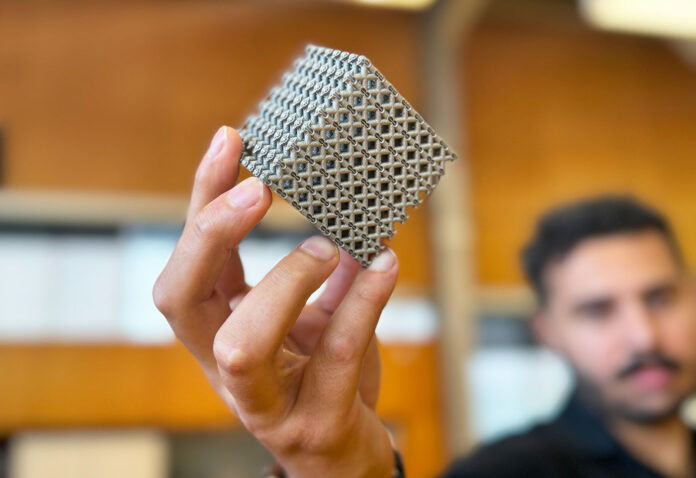
Ce titre ressemble au début d’un livre de science-fiction, mais ce n’est pas le cas. Des chercheurs de l’institut australien RMIT ont mis au point un nouveau métamatériau – terme utilisé pour décrire un matériau artificiel doté de propriétés uniques non observées dans la nature – à partir d’un alliage de titane ordinaire.
Les tests montrent qu’il est 50 % plus résistant que l’alliage le plus solide de densité similaire utilisé dans les applications aérospatiales.
La clé réside dans la conception unique de la structure en treillis du matériau.
Ce développement rappelle à quel point la nature peut inspirer les progrès de l’impression 3D. Dans ce cas précis, les structures en treillis constituées d’entretoises creuses ont été inspirées par des plantes robustes à tige creuse comme le nénuphar de Victoria ou le corail en tuyaux d’orgue (Tubipora musica) qui combinent légèreté et solidité.
Pour adapter ce matériau à la FA, le défi résidait dans la reproduction de ces « structures cellulaires » creuses dans les métaux. Ma Qian, professeur émérite au RMIT, explique que la contrainte dans tous les matériaux cellulaires complexes devrait être uniformément répartie. « Cependant, pour la plupart des topologies, il est courant que moins de la moitié du matériau supporte principalement la charge de compression, tandis que le volume plus important du matériau est structurellement insignifiant. »
C’est là que l’impression 3D métal entre en jeu.
« Nous avons conçu une structure tubulaire creuse en treillis à l’intérieur de laquelle court une fine bande. Ces deux éléments combinés présentent une force et une légèreté jamais vues ensemble dans la nature », a déclaré M. Qian. « En fusionnant efficacement deux structures en treillis complémentaires pour répartir uniformément les contraintes, nous évitons les points faibles où les contraintes se concentrent normalement. »
Les chercheurs ont imprimé un cube en 3D en utilisant la fusion laser sur lit de poudre. Les tests ont montré que le modèle imprimé – un cube en treillis de titane – était 50 % plus résistant que l’alliage de magnésium WE54 coulé, l’alliage le plus solide de densité similaire utilisé dans les applications aérospatiales. La nouvelle structure a effectivement réduit de moitié la quantité de contraintes concentrées sur les fameux points faibles du treillis. La conception en double treillis signifie également que toute fissure est déviée le long de la structure, ce qui améliore encore la résistance.
L’équipe prévoit d’affiner encore le matériau pour une efficacité maximale et d’explorer des applications dans des environnements à plus haute température.
Même s’il résiste actuellement à des températures de 350 °C, l’équipe pense qu’il pourrait être fabriqué pour résister à des températures allant jusqu’à 600 °C en utilisant des alliages de titane plus résistants à la chaleur, pour des applications dans l’aérospatiale ou les drones de lutte contre les incendies. La technologie permettant de fabriquer ce nouveau matériau n’étant pas encore largement disponible, son adoption par l’industrie pourrait prendre un certain temps, conclut le RMIT.
N’oubliez pas que vous pouvez poster gratuitement les offres d’emploi de l’industrie de la FA sur 3D ADEPT Media ou rechercher un emploi via notre tableau d’offres d’emploi. N’hésitez pas à nous suivre sur nos réseaux sociaux et à vous inscrire à notre newsletter hebdomadaire : Facebook, Twitter, LinkedIn & Instagram ! Si vous avez une innovation à partager pour le prochain numéro de notre magazine numérique ou si vous avez un article à faire connaître, n’hésitez pas à nous envoyer un email à contact@3dadept.com