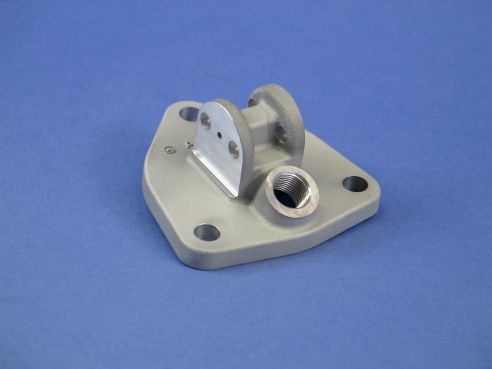
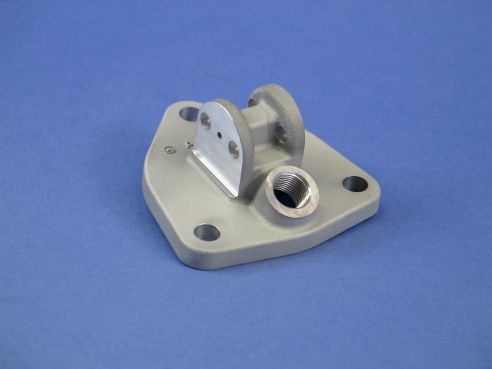
En mai 2017, Premium AEROTEC, EOS et Daimler ont lancé le projet NextGenAM. Leur idée était de développer la base d’un futur système de production en série à l’aide des technologies d’impression 3D. Ce système devrait être capable de produire des composants en aluminium pour les secteurs de l’automobile et de l’aérospatiale de façon beaucoup plus rentable qu’avec les méthodes actuelles.
Jusqu’ici, les trois collaborateurs semblent satisfaits de leur partenariat : pour l’ensemble de son processus de production, Premium AEROTEC a déjà pu réduire ses coûts de fabrication de 50% par rapport aux systèmes d’impression 3D existants.
Les principaux points qui ont été améliorés sont la production entièrement automatisée, la capacité extensible, les opportunités pour les petites séries ainsi que la qualité des produits.
L’automatisation de la fabrication
Pour ce qui est de la production automatisée, les partenaires expliquent que toutes les machines utilisées dans le cadre de ce projet sont connectées entre elles. Les données de fabrication sont transmises au centre de contrôle, qui hiérarchise ensuite les différentes requêtes et les attribue au système de fabrication additive.
Durant la fabrication, il est également possible de consulter le statut du processus sur un appareil mobile donc à distance et à tout moment. Une fois la production terminée, les rapports qualité sont centralisés au niveau du centre de contrôle. Toutes les données nécessaires à la production d’un « jumeau » numérique y sont accessibles, ce qui permet notamment une traçabilité totale.
Un flux continu de données 3D
Les équipes ont amélioré la gestion des données. Les lignes de production peuvent être facilement dupliquées pour étendre la capacité de l’usine. Cela permet d’espérer des économies encore plus substantielles à terme, avec l’augmentation des volumes.
Petites séries et qualité des produits
Le procédé d’impression 3D est particulièrement utile dans le secteur des pièces de rechange car, en cas de problème avec un outil, les pièces rarement demandées peuvent souvent être reproduites de façon plus économique.
« La fabrication additive se prête également à la production de nouveaux véhicules en petite série (éditions limitées). Le développement systématique de pièces spécialement conçues pour l’impression 3D permet de réduire encore les coûts de production et d’optimiser la qualité », explique Jasmin Eichler, responsable des technologies du futur chez Daimler AG. « L’impression 3D est également particulièrement intéressante durant la phase de développement avancé des véhicules. La fabrication additive permet souvent de produire à moindre coût le faible nombre d’unités requises et plus rapidement qu’avec des processus de production conventionnels. »
Enfin, parlant de la qualité des produits, les collaborateurs expliquent qu’il s’agit de la norme dans l’installation pilote. Il est également prévu d’employer un alliage d’aluminium, de magnésium et de scandium très résistant (appelé Scalmalloy®) pour les pièces utilisées dans les secteurs de l’aviation et de l’aérospatiale.
Pour le secteur automobile, on utilise un alliage d’aluminium classique (AlSi10Mg) dont les propriétés matérielles ont été améliorées tout au long du projet pilote. La résistance et la qualité de finition du matériau, entre autres, sont nettement meilleures qu’elles ne l’étaient il y a deux ans, au début de la coopération.
Pour des informations exclusives sur l’impression 3D, abonnez-vous à notre newsletter et suivez-nous sur les réseaux sociaux ! –
Vous souhaitez-vous abonner à 3D ADEPT Mag ? Ou vous voulez figurer dans le prochain numéro de notre magazine numérique ? Envoyez-nous un email à contact@3dadept.com
//pagead2.googlesyndication.com/pagead/js/adsbygoogle.js (adsbygoogle = window.adsbygoogle || []).push({});