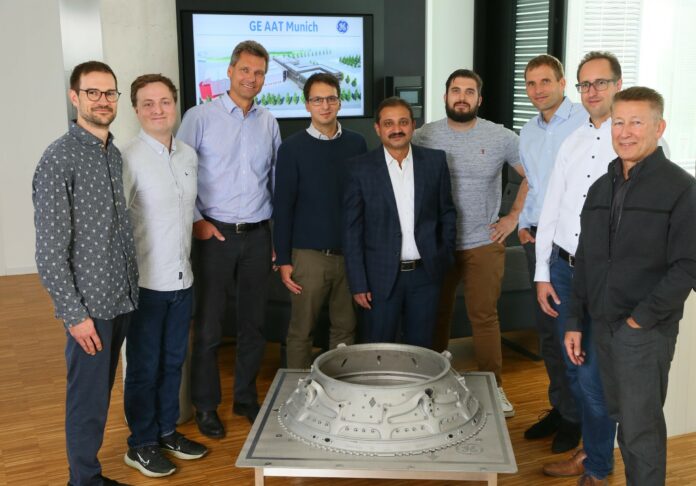
The EU’s European Green Deal sets out the need to reduce transport emissions by 90% by 2050, compared to 1990 levels, with the aviation sector playing its part. Policy actions and industry efforts since 2005 have led to greater fuel efficiency per passenger. Priorities going forward include financial and regulatory measures to drive low-emissions aviation and the urgent development of clean sheet frames, new aircraft engines and propulsion systems and Sustainable Aviation Fuel.
One significant research initiative underway to develop these types of more fuel efficient air transport technologies for the earliest possible deployment is the European Commission and European aerospace industry-funded Clean Sky 2 Programme, now entering its final phase. Its successor Clean Aviation was launched in December 2021.
The Clean Sky 2 program is made up of key industry players and subject matter experts along with academic research bodies across Europe. The program is integrating, demonstrating, and validating technologies capable of reducing CO2 emissions as well as nitrous oxide (NOx) and noise emissions by up to 30% compared to 2014 “state-of-the-art” aircraft. Another goal is to develop a strong and globally competitive aeronautical industry and supply chain in Europe.
Based in Munich, Germany, GE Aerospace Advanced Technology (GE AAT) Munich team leads three core partnerships in the Clean Sky 2 program to identify engine hardware, benefits, design, manufacturing process and, connected to the program’s goals, collaborate closely with GE Aerospace’s sites in Italy, Czech Republic, Poland and Turkey, as well as external partners.
Changing the Game for Large Metal Additive Parts
One of the GE AAT Munich-led partnerships is the Turbine Technology Project (TURN), which was set up to accelerate technology maturation for future aero engines.
And in response to a Clean Sky 2 call for proposals, in 2018 a consortium of Hamburg University of Technology (TUHH), TU Dresden (TUD) and technology company Autodesk, was selected to support GE AAT Munich for the design and manufacturing of a large-scale metal additive manufacturing component – the Advanced Additive Integrated Turbine Centre Frame (TCF) casing – the MONACO project. This also included the design and production of coupons and critical parts, validation and qualification, and the final delivery of the full-sized metal 3D-printed casing.
After almost six years in R&D and engineering, the large-format TCF casing design using GE Additive’s Direct Metal Laser Melting (DMLM) technology in nickel alloy 718 was recently unveiled by the consortium. The TCF casing is one of largest additively manufactured parts produced for the aerospace industry.
The additively manufactured TCF casing is designed for narrow-body engines in which the part is approximately one meter or more in diameter. Having this single-piece design solution to produce this kind of large format engine hardware with reduced cost, weight and manufacturing lead time gives a competitive business advantage.
“We wanted to reduce the weight of the part by 25% but also improve the pressure losses of the secondary air flow as well as a strong reduction in part count to improve maintenance,” said Dr. Günter Wilfert, GE AAT Munich’s technology and operations manager.
“The team can be proud of the results. With the final print of the full casing, they were able to prove the values. Those targets were achieved and surpassed. We were able to reduce the weight by ~30% in the end. The team also reduced the manufacturing lead time from nine months to two and a half months, by approximately 75%. Over 150 separate parts that make up a conventional turbine center frame casing have been consolidated into one single piece design,” he added.
To ensure that all the engineering requirements were met, including a performance benefit of 0.2% in specific fuel consumption, the design was reviewed by experts from across the team for Technology Readiness Level (TRL) and Manufacturing Readiness Level (MRL) 4 and multiple manufacturing trials were performed to meet hardware quality and incorporate the manufacturability of MRL4.
Reducing Reliance on Castings and Future Applications
Outside the environmental, performance, weight, cost benefits and reduction of waste material of this new part, perhaps the biggest impact will be supply chain disruption in all industries facing challenges with their casting in conventional manufacturing.
The turbine center frame, an inherent component of modern, turbofan aircraft engines, serves as a duct for the hot gas that flows from the high-pressure turbine into the low-pressure turbine. Conventionally, they are manufactured by casting and/or forging, followed by additional machining steps.
Due to stringent requirements on airworthy hardware in the highly regulated aerospace industry, the number of approved vendors for casting and forging parts is very limited. This creates long lead times and high costs. These challenges, and the fact that a turbine center frame isn’t a rotating part, made it an ideal candidate for additive manufacturing.
This new additive manufacturing design solution on engine frames is not limited to turbine center frames for future engines; it can be leveraged to existing and legacy engine center frames. The proposed design features can also be transferred and/or scaled to turbine rear frames (TRF), low pressure turbine casings and turbine mid frames (TMF).
“People already want to know how this part has been made and how the design and technology could translate to their industries. Our strategy all along was to make sure that the component design meets aerospace engineering requirements and Clean Sky 2 goals, but it could be easily translated to other similar segment engines, and adjacent businesses and sectors,” said Ashish Sharma, an advanced lead engineer on the GE AAT team.
“The Clean Aviation program, in line with the EU Green Deal objective of carbon neutrality by 2050, supports the launch of disruptive new products by 2035, with the aim to replace 75% of the operating fleet by 2050. Faster time to market and increased production rates will therefore be crucial to reaching these ambitious environmental targets,” said Christina-Maria Margariti, project officer for hydrogen-powered aircraft for Clean Aviation.
Industry-Academic Collaboration
The consortium team regards its work, and the part itself, as potential game-changer in the use of metal additive manufacturing for the future production of large parts for commercial aircraft engines.
The involvement of academia has been critical to the overall success of the project, enabling them to become part of a large European technology program by collaborating closely with industry, using their infrastructure and maturing different technologies.
Everybody, Sharma said, had their part to play. “Hamburg University of Technology has a GE Additive M2 machine installed on campus, and their expertise with prototyping was invaluable, while the team at TU Dresden was responsible for validation and building a dedicated test rig. Autodesk optimized the Design for Additive Manufacturing process, and finally GE Additive supported us by printing the part using its A.T.L.A.S machine. Having such a talented, additive-experienced team brought a lot of new ideas and concepts in fundamentals that we wouldn’t necessarily have thought about if we were working in our individual teams. There was a lot of ingenuity”, he added.
The project employed a multi-disciplinary iteration loop setup to design the hardware and leveraged Lean manufacturing concepts, processes and tools to reduce design iteration time. Many innovative and creative design features and solutions were considered and introduced to reduce pressure, thermal gradient and stress.
Dr. Dirk Herzog, interim professor at TUHH’s Institut für Laser- und Anlagensystemtechnik, said, “Due to the size of the part, it was necessary to evaluate design concepts by manufacturing segments at first, validate their performance and from there learn how to transfer to full scale. A lot of effort has been invested from all of the team members over the course of the last three-and-a-half years to advance us to the point where we were fully confident to have the design and the DMLM process ready for the final print. To finally see the physical part being built successfully is very rewarding.”
At the beginning of the TURN program GE AAT Munich explored the design space and performed multiple trade studies leveraging advanced technologies such as additive manufacturing. The GE AAT Munich team was able to lay down a technology maturation plan to advance the art of making TCF cases.
Finally, when the consortium started to support the technology maturation plan, AutoDesk brought advanced tools to optimize additive design, TUHH added additive machine for initial print trials and TUD’s experts built an aero/thermal rig with state-of-the-art instrumentation devices for validation – which blends to give satisfying results at the very first attempt to deliver a successful 3600 single-piece additive TCF case.
“The biggest challenges to validating additively manufactured hardware is that we are not allowed to scale up or down, as this changes the surface finish, which reflects in measurement data translated to product. We contributed our unique experience in testing print trials for mechanical strength, thermal emissivity and aero/thermal validation,” said Thomas IIzig, Eike Dohmen and Sarah Korb, TUD’s team of scientists.
“The team went ahead and designed and manufactured a novel three-hole probe to measure pressure loss on the additive TCF casing, which demonstrated a reduction of around 90% in pressure drop compared to a conventional design. The TCF casing underwent extensive aero/thermal and mechanical testing to meet engineering requirements,” they added.
Autodesk’s role in this research was to develop a lightweight, high performance turbine center frame casing by optimizing the structural and fluid performance while contributing to consolidate over 150 parts into a single component. Team Autodesk were instrumental in taking challenges to design component utilizing their software tools to meet program requirements.
Remember, you can post job opportunities in the AM Industry on 3D ADEPT Media free of charge or look for a job via our job board. Make sure to follow us on our social networks and subscribe to our weekly newsletter : Facebook, Twitter, LinkedIn & Instagram ! If you want to be featured in the next issue of our digital magazine or if you hear a story that needs to be heard, make sure you send it to contact@3dadept.com