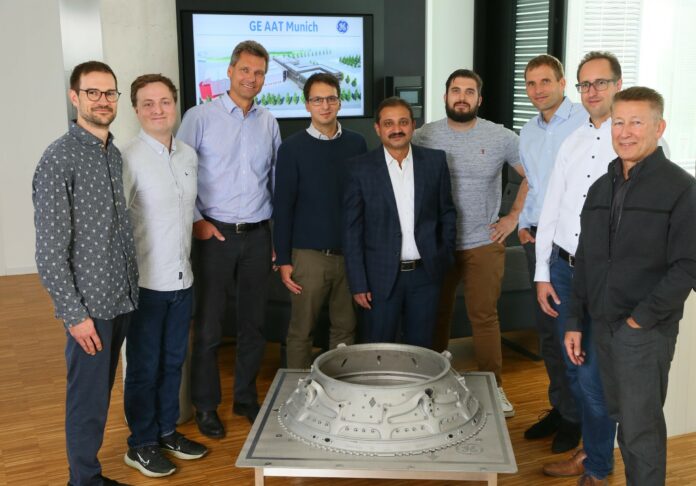
Le « pacte vert » européen de l’UE prévoit la nécessité de réduire les émissions du secteur des transports de 90 % d’ici à 2050, par rapport aux niveaux de 1990, le secteur de l’aviation jouant son rôle. Les mesures politiques et les efforts du secteur depuis 2005 ont permis d’améliorer le rendement énergétique par passager. Les priorités pour l’avenir comprennent des mesures financières et réglementaires pour favoriser une aviation à faibles émissions et le développement urgent de cadres de tôles propres, de nouveaux moteurs d’avion et systèmes de propulsion et de carburant d’aviation durable.
Le programme Clean Sky 2, financé par la Commission européenne et l’industrie aérospatiale européenne, qui entre maintenant dans sa phase finale, est une initiative de recherche en cours pour développer ces types de technologies de transport aérien plus économes en carburant en vue d’un déploiement le plus tôt possible. Son successeur, Clean Aviation, a été lancé en décembre 2021.
Le programme Clean Sky 2 est composé d’acteurs clés de l’industrie et d’experts en la matière ainsi que d’organismes de recherche universitaires de toute l’Europe. Le programme intègre, démontre et valide des technologies capables de réduire les émissions de CO2 ainsi que les émissions d’oxyde nitreux (NOx) et de bruit jusqu’à 30 % par rapport aux avions « de pointe » de 2014. Un autre objectif est de développer une industrie aéronautique et une chaîne d’approvisionnement fortes et compétitives au niveau mondial en Europe.
Basée à Munich, en Allemagne, l’équipe GE Aerospace Advanced Technology (GE AAT) Munich dirige trois partenariats principaux dans le programme Clean Sky 2 pour identifier le matériel du moteur, les avantages, la conception, le processus de fabrication et, en lien avec les objectifs du programme, collaborer étroitement avec les sites de GE Aerospace en Italie, en République tchèque, en Pologne et en Turquie, ainsi qu’avec des partenaires externes.
Changer la donne pour les grandes pièces métalliques additives
L’un des partenariats dirigés par GE AAT Munich est le projet de technologie des turbines (TURN), qui a été mis en place pour accélérer la maturation technologique des futurs moteurs d’avion.
Et en réponse à un appel à propositions de Clean Sky 2, en 2018, un consortium composé de l’Université de technologie de Hambourg (TUHH), de l’Université technique de Dresde (TUD) et de la société technologique Autodesk, a été sélectionné pour soutenir GE AAT Munich pour la conception et la fabrication d’un composant de fabrication additive métallique à grande échelle – le boîtier du cadre central de turbine (TCF) intégré par additif avancé – le projet MONACO. Ce projet comprenait également la conception et la production de coupons et de pièces critiques, la validation et la qualification, ainsi que la livraison finale de l’enveloppe métallique imprimée en 3D à taille réelle.
Après près de six ans de R&D et d’ingénierie, le consortium a récemment dévoilé la conception du boîtier TCF de grand format utilisant la technologie de fusion directe par laser métallique (DMLM) de GE Additive en alliage de nickel 718. Le boîtier du TCF est l’une des plus grandes pièces fabriquées de manière additive pour l’industrie aérospatiale.
Le carter TCF est conçu pour les moteurs à fuselage étroit, dont le diamètre est d’environ un mètre ou plus. Le fait de disposer de cette solution de conception monobloc pour produire ce type de matériel de moteur de grand format avec un coût, un poids et un délai de fabrication réduits donne un avantage commercial concurrentiel.
« Nous voulions réduire le poids de la pièce de 25 % mais aussi améliorer les pertes de pression du flux d’air secondaire ainsi qu’une forte réduction du nombre de pièces pour améliorer la maintenance« , a déclaré le Dr Günter Wilfert, responsable de la technologie et des opérations de GE AAT Munich.
Réduction de la dépendance à l’égard des pièces moulées et applications futures
En dehors des avantages de cette nouvelle pièce sur le plan de l’environnement, des performances, du poids, des coûts et de la réduction des déchets, l’impact le plus important sera peut-être la perturbation de la chaîne d’approvisionnement dans toutes les industries confrontées à des problèmes de moulage dans la fabrication conventionnelle.
Le cadre central de la turbine, un composant inhérent aux moteurs d’avion modernes à turbosoufflante, sert de conduit pour le gaz chaud qui passe de la turbine haute pression à la turbine basse pression. Traditionnellement, ils sont fabriqués par moulage et/ou forgeage, suivis d’étapes d’usinage supplémentaires.
En raison des exigences strictes en matière de matériel en état de navigabilité dans l’industrie aérospatiale hautement réglementée, le nombre de fournisseurs agréés pour les pièces moulées et forgées est très limité. Il en résulte des délais d’exécution longs et des coûts élevés. Ces défis, et le fait que le cadre central d’une turbine n’est pas une pièce rotative, en font un candidat idéal pour la fabrication additive.
Cette nouvelle solution de conception par fabrication additive pour les cadres de moteur ne se limite pas aux cadres centraux de turbine des futurs moteurs ; elle peut être appliquée aux cadres centraux de moteur existants et hérités. Les caractéristiques de conception proposées peuvent également être transférées et/ou mises à l’échelle pour les châssis arrière de turbine (TRF), les carters de turbine basse pression et les châssis intermédiaires de turbine (TMF).
« Les gens veulent déjà savoir comment cette pièce a été fabriquée et comment la conception et la technologie pourraient s’appliquer à leurs industries. Notre stratégie a toujours été de nous assurer que la conception du composant répondait aux exigences de l’ingénierie aérospatiale et aux objectifs de Clean Sky 2, mais qu’elle pouvait être facilement transposée à d’autres moteurs de segments similaires, ainsi qu’à des entreprises et secteurs adjacents« , a déclaré Ashish Sharma, ingénieur principal avancé de l’équipe GE AAT.
« Le programme Aviation propre, conformément à l’objectif du Green Deal de l’UE de neutralité carbone d’ici 2050, soutient le lancement de nouveaux produits disruptifs d’ici 2035, dans le but de remplacer 75 % de la flotte en exploitation d’ici 2050. Une mise sur le marché plus rapide et des taux de production accrus seront donc essentiels pour atteindre ces objectifs environnementaux ambitieux« , a déclaré Christina-Maria Margariti, responsable du projet d’avions à hydrogène pour Clean Aviation.
Collaboration entre l’industrie et le monde universitaire
L’équipe du consortium considère son travail, et la pièce elle-même, comme pouvant changer la donne dans l’utilisation de la fabrication additive métallique pour la production future de grandes pièces pour les moteurs d’avions commerciaux.
La participation des universités a été essentielle à la réussite globale du projet, leur permettant de faire partie d’un vaste programme technologique européen en collaborant étroitement avec l’industrie, en utilisant leur infrastructure et en faisant mûrir différentes technologies.
Selon Sharma, chaque partie avait un rôle à jouer. « L’université technologique de Hambourg dispose d’une machine GE Additive M2 installée sur le campus, et son expertise en matière de prototypage a été précieuse, tandis que l’équipe de TU Dresden était chargée de la validation et de la construction d’un banc d’essai dédié. Autodesk a optimisé le processus de conception pour la fabrication additive, et enfin GE Additive nous a aidés en imprimant la pièce à l’aide de sa machine A.T.L.A.S. Le fait d’avoir une équipe aussi talentueuse et expérimentée en matière de FA a apporté beaucoup de nouvelles idées et de nouveaux concepts fondamentaux auxquels nous n’aurions pas nécessairement pensé si nous avions travaillé dans nos équipes individuelles. Il y a eu beaucoup d’ingéniosité« , a-t-il ajouté.
Le projet a fait appel à une boucle d’itération multidisciplinaire pour concevoir le matériel et s’est appuyé sur les concepts, processus et outils de fabrication allégée pour réduire le temps d’itération de la conception. De nombreuses caractéristiques et solutions de conception innovantes et créatives ont été envisagées et introduites pour réduire la pression, le gradient thermique et les contraintes.
Dirk Herzog, professeur intérimaire à l’Institut für Laser- und Anlagensystemtechnik de la TUHH, a déclaré : « En raison de la taille de la pièce, il était nécessaire d’évaluer les concepts de conception par segments de fabrication dans un premier temps, de valider leurs performances et d’apprendre ensuite comment les transférer à l’échelle réelle. Tous les membres de l’équipe ont déployé des efforts considérables au cours des trois dernières années et demie pour nous amener au point où nous étions pleinement confiants dans le fait que la conception et le processus DMLM étaient prêts pour l’impression finale. Voir enfin la pièce physique se construire avec succès est très gratifiant« .
Au début du programme TURN, GE AAT Munich a exploré l’espace de conception et réalisé de multiples études commerciales en s’appuyant sur des technologies avancées telles que la fabrication additive. L’équipe de GE AAT Munich a pu établir un plan de maturation technologique pour faire progresser l’art de la fabrication de boîtiers TCF.
Enfin, lorsque le consortium a commencé à soutenir le plan de maturation technologique, AutoDesk a apporté des outils avancés pour optimiser la conception additive, la TUHH a ajouté une machine additive pour les premiers essais d’impression et les experts de la TUD ont construit une installation aérothermique avec des dispositifs d’instrumentation de pointe pour la validation – qui se mélangent pour donner des résultats satisfaisants dès la toute première tentative pour livrer un boîtier TCF 3600 monobloc additif réussi.
Enfin, lorsque le consortium a commencé à soutenir le plan de maturation technologique, AutoDesk a apporté des outils avancés pour optimiser la conception additive, la TUHH a ajouté une machine additive pour les premiers essais d’impression et les experts de la TUD ont construit un banc aérothermique avec des dispositifs d’instrumentation de pointe pour la validation – qui se mélange pour donner des résultats satisfaisants dès la toute première tentative pour livrer un cas de TCF additif réussi de 3600 pièces uniques.
« Le plus grand défi de la validation d’un matériel fabriqué de manière additive est que nous ne sommes pas autorisés à augmenter ou à diminuer l’échelle, car cela modifie la finition de la surface, ce qui se reflète dans les données de mesure traduites en produit. Nous avons apporté notre expérience unique en matière de tests d’impression pour la résistance mécanique, l’émissivité thermique et la validation aérothermique« , ont déclaré Thomas IIzig, Eike Dohmen et Sarah Korb, de l’équipe de scientifiques du TUD.
« L’équipe a ensuite conçu et fabriqué une nouvelle sonde à trois trous pour mesurer la perte de pression sur le boîtier TCF additif, qui a démontré une réduction d’environ 90 % de la perte de pression par rapport à une conception conventionnelle. Le boîtier TCF a subi des tests aérothermiques et mécaniques approfondis pour répondre aux exigences techniques« , ajoutent-ils.
Le rôle d’Autodesk dans cette recherche était de développer un carter de turbine central léger et performant en optimisant les performances structurelles et fluidiques tout en contribuant à consolider plus de 150 pièces en un seul composant. L’équipe Autodesk a contribué à relever les défis de la conception du composant en utilisant ses outils logiciels pour répondre aux exigences du programme.
N’oubliez pas que vous pouvez poster gratuitement les offres d’emploi de l’industrie de la FA sur 3D ADEPT Media ou rechercher un emploi via notre tableau d’offres d’emploi. N’hésitez pas à nous suivre sur nos réseaux sociaux et à vous inscrire à notre newsletter hebdomadaire : Facebook, Twitter, LinkedIn & Instagram !