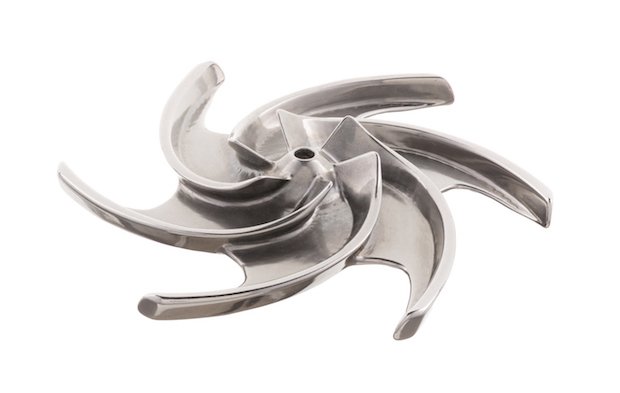
Desktop Metal a ajouté l’acier inoxydable 316L à sa gamme de matériaux d’impression 3D. Destiné au Studio System™, ce matériau peut être utilisé dans des environnements médicaux, à température extrême, hautement corrosifs et de qualité marine.
Reconnu pour sa résistance à la corrosion et ses excellentes propriétés mécaniques à des températures extrêmes, le matériau d’impression 3D en acier inoxydable possède de nombreuses variables et, au fil du temps, est de plus en plus utilisé par un large éventail de spécialistes de l’impression 3D métal. ExOne, par exemple, a ajouté l’acier inoxydable 304L à sa gamme et ITAMCO a fabriqué en plus des pièces fabriquées avec de la poudre métallique EOS 17-4 PH IndustryLine qui dépasse la résistance à la traction de l’acier inoxydable 17-4 PH. Les deux matériaux à base d’acier inoxydable ont été utilisés dans des environnements industriels exigeants.
Le spécialiste de l’impression 3D métal de Burlington reconnaît également le potentiel de ce matériau. Pour le CEO et cofondateur de Ric Fulop, « l’ajout du 316L permet aux ingénieurs d’imprimer des pièces métalliques pour un large éventail d’applications, y compris les pièces de moteur, l’équipement de laboratoire, la fabrication de pâtes et papiers, les dispositifs médicaux, le traitement chimique et pétrochimique, les appareils de cuisine, les bijoux et même les outils et équipements cryogéniques. Les équipes sont maintenant capables d’imprimer rapidement des prototypes 316L, des géométries complexes qui ne le sont plus pour les méthodes de fabrication et produisent les pièces utilisées au final de façon rentable. »
Quelques exemples d’applications réalisées avec leur produit phare, le système Studio System, comprennent une buse de carburant de combustion pour navires-citernes, une attelle annulaire personnalisée à usage médical ou une roue à aubes pour environnements difficiles.
Le Centre Médical Beth Israel Deaconess a utilisé le matériau de Desktop Metal pour leur attelle annulaire. Dédiée à l’industrie médicale, l’attelle annulaire permet de limiter l’amplitude des mouvements des membres blessés. Généralement fabriqué à base de plastique moulé par injection, la contrainte avec ce procédé est que les pièces ont tendance à se briser après quelques temps.
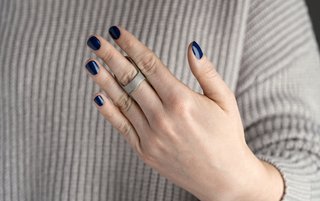
Le médical a donc décidé de le personnaliser par impression 3D en 316L et bénéficie d’une finition esthétique et d’une durabilité accrue.
« Le fait de pouvoir imprimer en 3D des pièces en acier de qualité médicale comme cette attelle de doigt, qui est adaptée à l’anatomie du patient, offre de nombreux avantages par rapport aux méthodes de fabrication précédentes qui prennent plus de temps et peuvent être moins efficaces », a déclaré Jim S. Wu, MD, chef de la radiologie musculosquelettique et des interventions au Beth Israel Deaconess Medical Center, et professeur associé à Harvard Medical School.
Pour des informations exclusives sur l’impression 3D, abonnez-vous à notre newsletter et suivez-nous sur les réseaux sociaux !
Vous souhaitez-vous abonner à 3D ADEPT Mag ? Ou vous voulez figurer dans le prochain numéro de notre magazine numérique ? Envoyez-nous un email à contact@3dadept.com
//pagead2.googlesyndication.com/pagead/js/adsbygoogle.js (adsbygoogle = window.adsbygoogle || []).push({});