Si on ne regarde que la pièce fabriquée, à première vue, il pourrait être facile de dire que le moulage des métaux n’a rien à envier à l’impression 3D métal, car les deux technologies peuvent fournir des pièces avec des trous internes et une rugosité de surface similaire. Seulement voilà, la rugosité de surface et les trous internes ne suffisent pas à faire pencher la balance en faveur d’une technologie ou d’une autre. Les propriétés mécaniques, la productivité et les coûts sont d’autres éléments qui pourraient aider à déterminer si les deux technologies peuvent être considérées comme des « ennemies » ou des « amies ».
Avez-vous déjà réalisé que presque tous les objets qui nous entourent intègrent des pièces de fonderie ? Le portail d’une maison, une clé à molette, un avion, un immeuble de bureaux, un camion, etc. Chacun de ces objets intègre des pièces en métal moulé. Avec un tel nombre d’applications couvertes par la technologie de moulage, et compte tenu des avantages bien connus de la fabrication additive, la logique voudrait que la combinaison de FA-moulage conduise automatiquement à un certain nombre d’applications plus performantes dans un large éventail d’industries, mais les choses ne sont pas toujours aussi simples dans la fabrication.
Il est logique d’explorer comment ces technologies peuvent progresser main dans la main quand on sait que l’industrie de la fonderie représente un pourcentage important de l’industrie manufacturière.
La technologie de moulage est l’une des plus anciennes technologies de production au monde. En fait, le processus de moulage était déjà utilisé en Égypte en 2800 avant Jésus-Christ. Pour ceux qui ne sont pas familiers avec ce processus, il pourrait être intéressant que vous gardiez cette description à l’esprit : généralement utilisé pour créer des formes creuses et complexes, le moulage consiste à verser un matériau liquide dans la cavité d’un moule spécialement conçu (la cavité faisant référence à la forme du produit à fabriquer). Une fois le matériau liquide refroidi, il se solidifie en une pièce appelée pièce moulée.
Les fabricants étant de plus en plus à la recherche de solutions susceptibles d’offrir les conditions les plus favorables en termes de prix, de temps et de qualité, comment ne pas imaginer que la fabrication additive, l’une des technologies de fabrication les plus récentes, puisse avoir son rôle à jouer dans un processus de fabrication impliquant un moulage ?
Ce dossier a pour ambition d’explorer les différentes voies où la FA & et le moulage peuvent être considérés comme des processus complémentaires, par opposition à celles où ils peuvent être considérés comme des processus concurrents. Pour ce faire, ce dossier exclusif abordera les points suivants :
- Les différents procédés de moulage existants, en mettant l’accent sur ceux qui correspondent le mieux à la FA ;
- Les points de vue des logiciels et des matériaux pour les approches de fabrication hybrides qui impliquent la FA et le moulage ;
- Les différentes attentes en termes de productivité et de coûts qui peuvent être suscitées.
Types de procédés de coulée
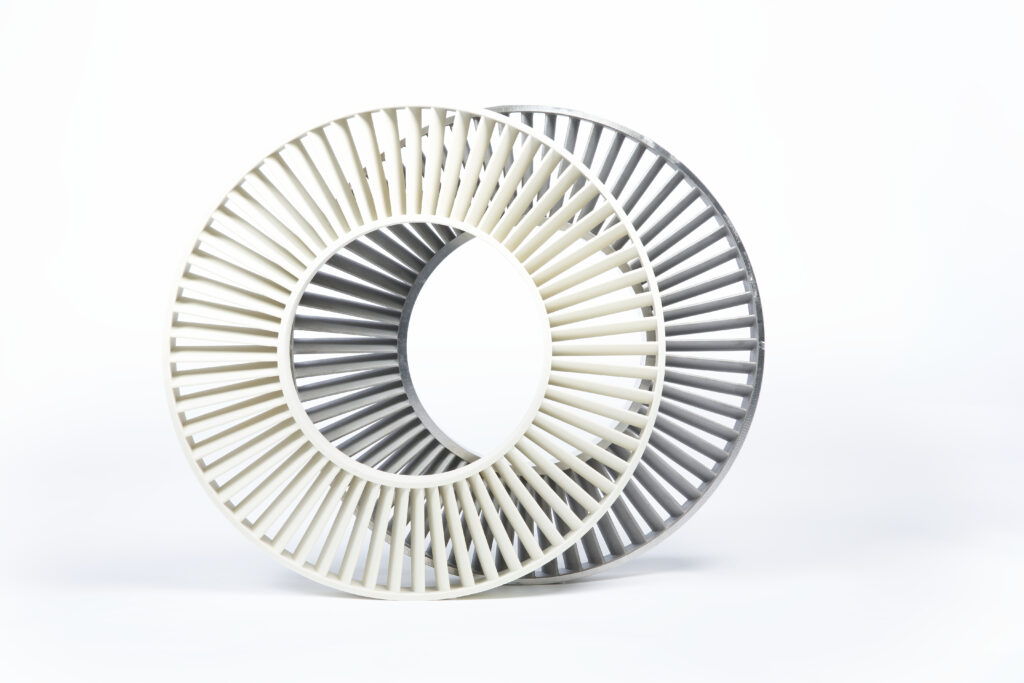
Trois procédés différents viennent immédiatement à l’esprit lorsqu’on parle de moulage : le moulage sous pression, le moulage à la cire perdue et le moulage en sable. En réalité, les recherches montrent qu’on peut avoir jusqu’à 13 types différents de procédés de moulage. En plus des trois procédés mentionnés ci-dessus, les autres méthodes de moulage comprennent : Le moulage en coquille, le moulage en plâtre, le moulage en céramique, le moulage sous vide, le moulage en moule permanent, le moulage en boue, le moulage sous pression, le moulage centrifuge, le moulage en continu et le moulage sous pression.
Il est intéressant de noter que « les principaux procédés de moulage combinés à la FA sont le moulage en sable et le moulage à la cire perdue. Ces deux procédés de moulage peuvent être traités par Binder Jetting (technologie de jet de liant). Soit pour imprimer des moules et des noyaux en sable directement et sans outils, soit en imprimant du plastique PMMA pour créer des modèles pour les applications de moulage à la cire perdue. En combinant le moulage en sable ou à la cire perdue avec la FA, les coûts et les délais de livraison, en particulier pour les prototypes et les petits volumes ou les grands composants individuels, peuvent être réduits jusqu’à 75 % grâce à l’absence d’outils », déclare d’emblée Christian Traeger, directeur des ventes et du marketing chez voxeljet.
La méthode de moulage en sable consiste à produire des pièces moulées dans un moule en sable, en acier, en fer et dans la plupart des alliages non ferreux. Elle implique plusieurs étapes afin d’obtenir une finition de haute qualité. Toutefois, quelques-uns de ses avantages et inconvénients peuvent être résumés comme suit :
Avantages | Inconvénients |
Coûts de production peu élevés, notamment pour les petites séries. | Le processus donne un degré de précision inférieur à celui des autres méthodes en raison du rétrécissement. |
Possibilité de fabriquer des pièces de grande taille. | Il peut être difficile de sabler des pièces moulées avec des spécifications de taille et de poids prédéterminées. |
Capacité à couler des matériaux ferreux et non ferreux. | De mauvaises finitions de surface peuvent se produire. |
La méthode bien connue du moulage à la cire perdue, quant à elle, commence dans la salle de cire et se termine par des essais où les pièces moulées sont soigneusement ébarbées, sablées et traitées thermiquement. Traditionnellement, ce procédé nécessite la création d’un moule dans lequel un alliage fondu peut être versé : un modèle en cire est recouvert d’un matériau céramique réfractaire ; à mesure que le matériau réfractaire durcit, sa géométrie interne prend la forme du modèle en cire ; au cours de la troisième étape, la cire est fondue et le métal fondu est versé dans la cavité du moule. Ce métal fondu se solidifie ensuite et le matériau céramique extérieur est brisé pour faire sortir la pièce moulée.
Comme nous l’avons résumé ci-dessus avec le procédé de moulage en sable, voici quelques avantages et inconvénients de ce procédé :
Avantages | Inconvénients |
Peut réaliser le moulage de pièces très complexes et extrêmement précises avec un bon état de surface dès le démoulage ; | Idéal pour les pièces de petite taille. |
Peut couler des sections très fines (~0.015 in) avec des tolérances incroyablement faibles (~0.003 in) | Les pièces comportant des noyaux ou des trous inférieurs à 1,6 mm ou des trous d’une profondeur supérieure à 1,5 fois le diamètre de la pièce sont difficiles à couler à la cire perdue. |
Possibilité d’automatiser le processus, donc de produire une grande quantité de pièces ; | Peut impliquer des équipements et des ressources financières élevées |
Différents types de pièces peuvent être fabriqués à partir d’un large éventail de matériaux : aciers inoxydables, fers magnétiques, laiton, etc. | |
Des tests approfondis sont effectués tout au long du processus. |
Certains de ces avantages et limites ont été partagés par Suraj Kathale de HCL Technologies.
Alors que l’attention est souvent portée sur le moulage en sable et le moulage à la cire perdue lorsqu’on parle de FA et de moulage, il convient de noter que la FA peut également être une réponse à l’outillage moulé sous pression dans certaines industries comme l’automobile.
Dans un processus de moulage sous pression, le liquide métallique à haute pression est pressé à grande vitesse dans la cavité d’un moule métallique de précision, puis le liquide métallique est refroidi et solidifié sous pression pour former une pièce moulée.
Contrairement aux autres procédés, cette méthode présente les avantages et les inconvénients suivants :
Avantages | Inconvénients |
L’efficacité de la production est élevée et les moules de coulée sous pression peuvent être utilisés plusieurs fois. | Longs délais d’exécution |
Des exigences réduites en matière de machines de post-coulée | Les grandes pièces ne peuvent pas être moulées |
Idéal pour la production en série |
Les applications de la FA dans le moulage sous pression peuvent démontrer comment des canaux de refroidissement conformes imprimés en 3D à proximité de la surface de ces outils créent une matrice thermiquement équilibrée, et comment les avantages se traduisent par une réduction du temps de cycle, des taux de rebut et des coûts de main-d’œuvre.
Quel processus de FA peut être intégré au moulage sous pression ?
Parfois, l’exploration des voies où la FA et le moulage sont complémentaires se résume à trouver un moyen plus rapide (et quelque peu abordable) de créer le moule avant de compléter le processus de fabrication. Comme vous le savez, dans ce cas, la FA est souvent utilisée pour créer les moules en sable et les noyaux qui sont ensuite utilisés pour fabriquer des pièces par moulage.
Cela dit, le jet de liant reste le procédé le plus largement utilisé avec le moulage – en particulier le moulage en sable. Dans ce procédé, une tête d’impression dépose un liant liquide sur une fine couche de particules de poudre – sable de fonderie, céramique, métal ou composites -. Dans ce cas par exemple, le sable est généralement le matériau d’impression 3D, le liant est une résine de qualité fonderie tandis que le composant fabriqué est un moule en sable ou un noyau de moule. Cette forme de FA est souvent appelée impression 3D de sable, et sur le marché actuel, seuls quelques fabricants ont acquis une solide expertise dans ce domaine. Il s’agit par exemple de voxeljet, ExOne et ETEC (anciennement connue sous le nom d’EnvisionTEC).
En ce qui concerne le moulage à la cire perdue, les applications révèlent que la SLA (stéréolithographie) est une autre technologie qui convient parfaitement aux flux de travail de moulage. Cette technologie permet de produire des pièces métalliques à moindre coût, avec une plus grande liberté de conception et en moins de temps que les méthodes traditionnelles. L’un des objectifs du moulage à la cire perdue est d’utiliser le moins de matériau possible, tout en conservant la forme et la précision. Cet objectif peut être facilement atteint avec la SLA, où un laser UV durcit et solidifie de fines couches de résine afin d’obtenir des structures internes, des parois fines, une finition de surface et une résolution idéale. Les étapes de fabrication qui mènent au produit final peuvent souvent varier d’un fabricant à l’autre, mais en fin de compte, lorsqu’on utilise des modèles SLA, il est facile de modifier la conception originale du moule à modèle et d’examiner les résultats en quelques jours seulement.
Étant donné que les fonderies de moulage à la cire perdue ne peuvent souvent pas produire de prototypes de moulage tant que le moule d’injection n’est pas terminé, l’impression 3D FDM est souvent utilisée comme une autre option pour produire des modèles de moulage à la cire perdue qui sont beaucoup plus efficaces et rentables.
Ceci étant dit, d’autres éléments qui méritent d’être pris en considération sont les points de vue des matériaux et des logiciels, ainsi que les propriétés mécaniques des pièces obtenues.
Perspective sur les logiciels
On accorde souvent très peu de crédit au logiciel de conception, alors qu’il peut jouer un rôle crucial dans la réussite de la pièce. Chaque processus de fabrication commence par une conception et, comme toujours, les opérateurs chercheront à obtenir les performances maximales de la pièce en tirant le meilleur parti du processus de fabrication.
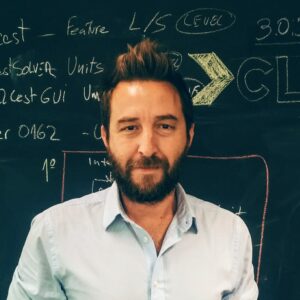
Il va sans dire que le moulage au sable (moule imprimé en 3D) et le moulage à la cire perdue (modèle imprimé en 3D) ont des contraintes de fabrication différentes, ce qui implique de nombreuses différences au niveau de la conception. Comme on le voit avec certains procédés traditionnels de FA, Martin Solina, vice-président d’Inspire Manufacturing Solutions, Altair, recommande aux fonderies de se poser quelques questions fondamentales avant de passer à la production : « Puis-je couler cette forme ? » C’est la clé pour avoir des pièces saines et sans défauts et pour minimiser les rejets. Quel sera le coût de production ? Comment cela se compare-t-il à une méthode traditionnelle ? Quels sont les avantages ? »
Néanmoins, au tout début de la phase de conception, lorsque la FA et le moulage sont explorés dans une approche de fabrication hybride, l’une des préoccupations qui peut surgir pourrait être la bonne façon d’obtenir la géométrie optimale de la pièce. Pour Martin Solina, « cela ne devrait pas être une préoccupation car c’est un grand avantage qui peut être obtenu en utilisant un processus hybride. Le moulage hybride présente les avantages des deux mondes : la fabrication additive donne de la flexibilité pour concevoir des modèles légers et optimaux, tandis que le moulage fournit une méthode de fabrication éprouvée avec de bonnes propriétés des matériaux. [Cela signifie qu’] en utilisant l’impression 3D et le moulage, nous maximisons la liberté de conception tout en augmentant les performances et en réduisant le poids des pièces », explique-t-il.
En outre, si dans un processus de moulage traditionnel, il est possible de disposer d’un outil logiciel qui permet d’étudier les paramètres de moulage et d’éliminer les défaillances possibles du processus de moulage pendant la phase de conception, il est logique d’attendre une telle double fonction dans cette approche de fabrication hybride. Pour que l’analyse de rentabilité de FA et du moulage soit convaincante, le logiciel de conception doit permettre aux utilisateurs de faire plus que simplement fournir des outils de CAO. Pour le représentant d’Altair, cela signifie que les ingénieurs de conception devraient – par exemple – être en mesure d’optimiser la « performance de la pièce tout en définissant des règles de fabrication pour assurer la fabricabilité de la pièce pour le processus de fabrication particulier. Les logiciels de conception doivent donner à l’utilisateur la liberté de redéfinir la pièce et de fournir des réponses rapides aux questions concernant les performances dans différents cas de charge, la fabricabilité, la prédiction des défauts ou la validation du processus de fabrication. Sur cette base, le rôle d’un logiciel de conception a aujourd’hui changé, passant d’un outil de CAO de base à un outil de conception axé sur la simulation qui fournit un retour d’information pour améliorer et optimiser la conception de la pièce et des processus en intégrant l’optimisation de la topologie et différents types d’outils d’analyse et de simulation comme l’analyse structurelle, thermique ou des fluides. La simulation de fabrication et de nombreux autres outils aident les concepteurs à prendre des décisions sur la base d’informations, comme par exemple :
- Créer et modifier des conceptions en toute simplicité : Créez, modifiez et défaites rapidement des modèles solides, utilisez PolyNURBS pour créer une géométrie lisse de forme libre et étudiez plusieurs configurations d’assemblage.
- Optimiser pour la fabrication : Arrivez à la direction idéale de la conception extrêmement tôt dans le processus : l’optimisation de la topologie est basée sur la physique et observe les contraintes du processus de fabrication.
- Simulez à la vitesse de la conception : Découvrez un environnement de conception technique interactif pour une exploration rapide de la conception et la création de produits, sans avoir à investir dans un nouveau matériel informatique. »
Légende : Le bras culbuteur! La voie vers des machines agricoles plus légères grâce à l’optimisation de la topologie et à la simulation de fabrication – Altair, Amazone et Voxeljet ont non seulement rendu un bras oscillant plus léger et plus durable, mais aussi avec moins de variations de rigidité. Le culbuteur était au départ une pièce soudée de 245 kg, avec des soudures de 16,5 m, dont la production était très longue et coûteuse. Ils ont fini par couler la pièce avec un poids inférieur de 8%, des coûts de production plus bas et une plus grande flexibilité pour les clients en matière de modules complémentaires.
Sur le plan pratique, il ne faut pas oublier que la « conception » dépend beaucoup de « l’élément humain« , ce qui signifie que deux ingénieurs concevant la même pièce n’obtiendront pas toujours exactement le même « rendu« , sans compter que la complexité de la pièce – si elle n’est pas bien gérée – peut entraîner des défauts, une faible performance de la pièce, un poids excessif, un délai de commercialisation trop long et même des opérations coûteuses de reconception et de révision des conditions du processus.
Pour répondre aux exigences actuelles de performance, de réduction de poids et surtout de coûts, il est nécessaire de tirer parti de nouveaux processus et de composants de conception pour que ces processus nécessitent la combinaison de nouvelles fonctionnalités logicielles, notamment :
- La géométrie paramétrique qui offre la possibilité d’effectuer des modifications et des changements de géométrie en fonction de l’analyse et de la simulation.
- L’analyse structurelle et de mouvement ou dynamique pour comprendre les conditions de travail de la pièce analysée.
- L’optimisation de la topologie pour améliorer les performances de la pièce et réduire son poids en fonction des conditions de travail.
- La simulation de fabrication pour prédire le remplissage du moule et l’analyse thermique pour différents types de processus de moulage tels que le moulage à la cire perdue ou le moulage en sable par gravité, en tenant compte des différents types de moules imprimés 3D.
- Et surtout, toutes ces fonctionnalités qui doivent être liées les unes aux autres de manière transparente pour l’utilisateur », souligne Martin Solina.
Perspective sur les matériaux
L’une des principales préoccupations souvent soulevées par les matériaux est celle des propriétés mécaniques. Avons-nous des résultats satisfaisants lorsque nous évaluons la résistance à la traction, la dureté, la rugosité de surface et la microstructure de la pièce ?
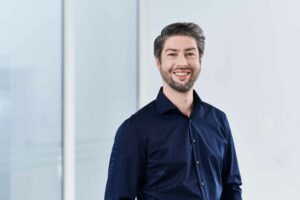
Dans un processus de moulage en sable traditionnel, par exemple, trois matériaux/systèmes de liaison sont souvent utilisés et il est facile de penser qu’ils peuvent être directement transférés aux méthodes de production par FA.
En regardant le moulage au sable, la réponse classique est « ça dépend », Christian Traeger apporte une nuance : « La plupart des matériaux utilisés le sont depuis des siècles dans le moulage des métaux : sable et résine furanique. D’autres types de liants, comme les liants phénoliques ou inorganiques sont également traitables par la FA. En fonction du liant utilisé, la configuration du système doit également être adaptée. La liaison directe furanique nécessite de mélanger le sable avec un promoteur qui réagit avec le liant et colle les particules de sable ensemble. Les liants phénoliques et inorganiques fonctionnent tous deux avec du sable non mélangé. En irradiant les plates-formes de construction par la température, les résines réagissent et collent les particules de sable ensemble. Comme le sable non imprimé n’est pas mélangé, il est beaucoup plus facile à recycler et à réutiliser. Dans le domaine du moulage à la cire perdue, nous constatons une grande acceptation et un intérêt croissant du marché pour l’ensemble des matériaux PMMA. La production rapide et l’intégration parfaite dans les chaînes de processus existantes sont les principaux avantages. La seule façon d’optimiser davantage ce matériau est d’améliorer encore la qualité de la surface ».
En outre, la recherche révèle que la production de moules par jet de liant requiert plusieurs propriétés de base des matériaux pour les différentes étapes du processus. Le matériau des particules doit s’écouler librement pour remplir la forme du modèle. Le liant doit avoir une très faible viscosité pour le dosage et pour les caractéristiques d’écoulement du matériau de moulage qui en résulte. Ces deux propriétés constituent également une base pour le traitement des matériaux dans les machines dans le cadre du processus de projection de liant. Par conséquent, les matériaux peuvent être utilisés dans les imprimantes 3D sans modification majeure de leurs propriétés physiques ou chimiques.
Nous avons ensuite demandé à Christian Traeger de voxeljet si les pièces produites par FA et une méthode de moulage possèdent les mêmes propriétés mécaniques que les pièces produites par moulage comme seule méthode de production. Il a répondu par l’affirmative.
« La raison en est que le processus de moulage lui-même reste exactement le même qu’auparavant. En utilisant des matériaux de fonderie typiques tels que la silice et les sables spéciaux et des liants furaniques, phénoliques ou inorganiques complémentaires, nous ne changeons que la façon dont les moules, les modèles et les noyaux sont construits. Au sein de la fonderie, les pièces imprimées en 3D peuvent être intégrées dans les chaînes de processus existantes. Comme les propriétés mécaniques des pièces moulées dépendent principalement des propriétés de l’alliage utilisé, la fabrication additive n’a aucune influence sur celles-ci. Bien sûr, il faut garder à l’esprit certains détails lors de la conception du moule ou du modèle, comme le nettoyage des pièces imprimées. De même, la qualité de la surface dépend du matériau utilisé et peut présenter des différences par rapport aux matériaux utilisés dans la fabrication conventionnelle, mais lorsque tous ces détails sont pris en compte, et que le métal est coulé, les pièces présentent exactement les mêmes propriétés mécaniques que les pièces coulées fabriquées de manière conventionnelle. »
Qu’en est-il de la productivité et des coûts ?
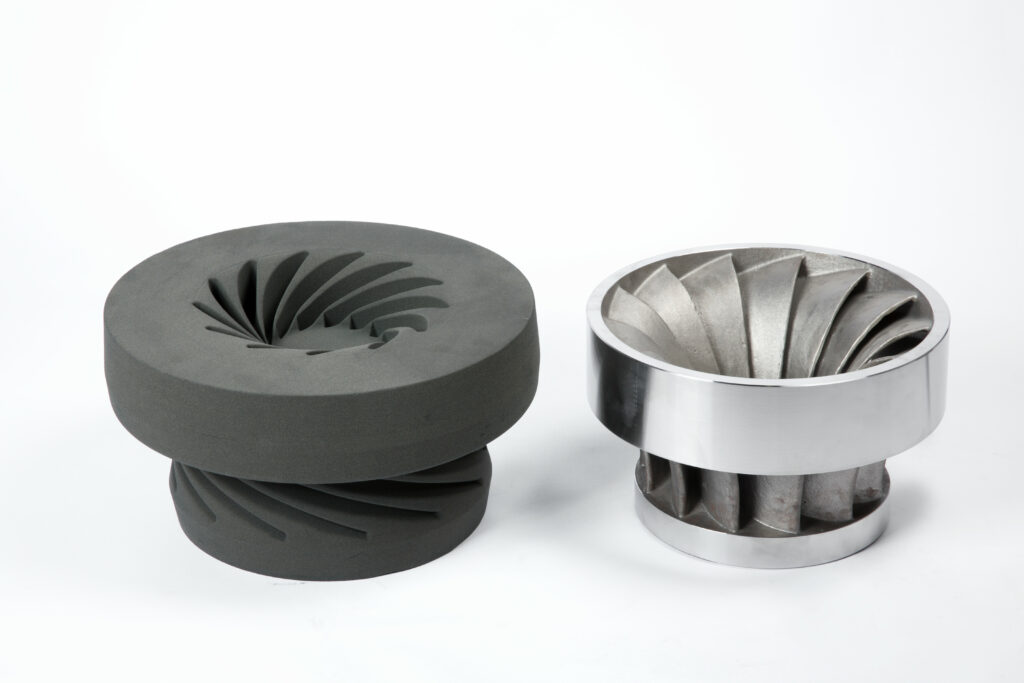
Le calcul est en général rapide lorsqu’on compare le temps de production avec la FA avec le temps de production de la même pièce obtenue par un procédé de fabrication conventionnel : la FA l’emporte généralement, quoi qu’il arrive. Ce qui est intéressant ici, c’est de découvrir les étapes qui sont supprimées dans un processus de FA, mais qui restent nécessaires dans un processus de moulage.
Disons par exemple que le temps de production est calculé à partir du moment où le fabricant de pièces reçoit la géométrie CAO 3D d’un client. Le processus de moulage d’une pièce de complexité moyenne peut nécessiter deux boîtes à noyaux supplémentaires pour l’équipement de moulage. Les opérateurs auront besoin de trois jours pour redessiner un modèle 3D avec tous les angles de dépouille nécessaires et préparer les géométries de modèle 3D. Deux semaines supplémentaires seront nécessaires pour passer des géométries 3D à un modèle prêt à l’emploi : cela comprend l’usinage CNC pour les négatifs, l’usinage CNC pour les boîtes à noyaux, la copie des modèles en époxy et la fabrication du système de porte. Sans compter le temps supplémentaire nécessaire pour la production principale et le formage.
La FA, comme vous le savez peut-être, ne nécessite pas toutes ces étapes. Pour la même pièce, l’opérateur aura besoin de quelques heures pour préparer un programme et commencer à produire la pièce. La majeure partie du temps est consacrée au processus d’impression, qui peut prendre jusqu’à trois jours, en fonction de la vitesse de la machine. Ensuite, l’opérateur peut consacrer quelques heures aux différentes étapes de post-traitement qui doivent être réalisées.
Néanmoins, un avantage qui mérite d’être mentionné est que dans un processus de coulée, un moule contient plus d’une pièce, ce qui signifie que dans un processus de coulée, il est possible de produire 10 pièces. Ce nombre est susceptible de varier – et n’est pas toujours atteint – avec une imprimante 3D. Si le moulage reste un procédé intéressant pour la production en série, la FA convient parfaitement aux pièces très complexes et aux productions pour lesquelles le temps est un facteur limitant.
« La FA fonctionne avec des données CAO numériques et ne nécessite aucune forme d’outillage. La production d’un outillage conventionnel peut prendre jusqu’à 12 semaines et ce n’est qu’ensuite que le processus de moulage pour cette pièce spécifique peut commencer. Le procédé de jet de liant peut créer des moules et des modèles en quelques heures ou quelques jours, réduisant ainsi jusqu’à 75 % le temps nécessaire à la création d’un prototype, par exemple. Le procédé de jet de liant est une technologie de processus relativement extensible, ce qui veut dire que les volumes de construction et la productivité peuvent être augmentés, ce qui rend la technologie non seulement adaptée à la production de prototypes, mais aussi à des lots de petite et moyenne taille », commente Christian Traeger.
Toutefois, lorsqu’on lui demande si la combinaison de FA-moulage est le moyen le plus rentable de produire des pièces – si on compare avec les autres procédés de FA métal il répond :
« Cela dépend du matériau et de la taille de lot requise. Pour les prototypes et les petites séries, le processus de moulage assisté par FA est beaucoup plus rentable que le frittage laser direct des métaux, par exemple. Cela s’explique par les matériaux d’impression et les alliages de moulage. Un kilo d’aluminium coûte environ 6,50 EUR lors du moulage. Les alliages d’acier spéciaux peuvent coûter jusqu’à 38 EUR. Les mêmes matériaux, mais pour les technologies de FA, peuvent coûter entre 78 et 133 euros par kilogramme.
En ce qui concerne la taille des lots, l’injection de liant dans les moules, les noyaux et les modèles est rentable pour les prototypes et les lots de petite et moyenne taille. Le jet de liant est l’une des technologies de FA les plus productives et peut être facilement adapté pour répondre aux besoins de lots plus importants. Elle permet également de construire des volumes supérieurs aux capacités des imprimantes à métaux existantes. Si le jet de liant métallique est bien sûr une technologie en plein essor, les volumes de fabrication ne sont toujours pas à la hauteur de ceux offerts par les imprimantes à sable. Dire que la coulée de métal assistée par jet de liant est le moyen le plus rentable de produire des pièces métalliques est une affirmation forte et un peu tirée par les cheveux. Dans certains scénarios, comme ceux décrits ci-dessus, la rentabilité du jet de liant est très difficile à battre, mais ces scénarios doivent être identifiés et soigneusement évalués pour trouver la meilleure solution. »
Réflexions finales
L’industrie de la fonderie n’est peut-être pas connue pour sa rapidité, mais l’économie et les opportunités sont tout simplement trop bonnes pour être laissées de côté. Cette industrie est responsable des pièces qui alimentent la vie quotidienne, l’économie et de nombreuses autres industries. Pourtant, lorsque nous regardons la fabrication, le secteur reste l’un des plus grands perdants avec des baisses de production d’environ 30% en raison de la crise et d’autres transformations en cours dans les industries. Le prix et le temps de production font de la FA un candidat attrayant et compétitif pour résoudre une partie de ce problème, surtout si l’on considère la production de petites pièces et de petites quantités (jusqu’à 5 pièces).
De plus, comme le mentionne voxeljet, malgré le coût élevé des équipements de FA, on constate que les fabricants de machines continuent d’investir du temps et des ressources pour développer un portefeuille qui peut facilement permettre à ces industries de faire évoluer leur production pour des besoins de taille de lot plus importante. Enfin, au-delà de ces investissements, il est essentiel de garder à l’esprit que, dans le cadre de cette approche de fabrication hybride impliquant la FA et le moulage, le bon logiciel de conception et l’utilisation de ce logiciel peuvent parfois faire toute la différence, non seulement pour mouler l' »impossible à mouler« , mais aussi pour obtenir les avantages idéaux en termes de temps, de coûts et de performances.
Ce dossier exclusif a été initialement publié dans l’édition de juillet/août de 3D ADEPT Mag. Toutes les ressources et contributions se trouvent en page 13.
N’oubliez pas que vous pouvez poster gratuitement les offres d’emploi de l’industrie de la FA sur 3D ADEPT Media ou rechercher un emploi via notre tableau d’offres d’emploi. N’hésitez pas à nous suivre sur nos réseaux sociaux et à vous inscrire à notre newsletter hebdomadaire : Facebook, Twitter, LinkedIn & Instagram !