The project’s goal was to develop a sustainable process that uses lunar resources and recycled scrap metals, eventually contaminated by lunar dust, to produce spare parts on-site which could help and enhance human settlement on the Moon.
Time flies when you’re having fun, they said. Eighteen months ago, Austrian manufacturers Incus and Lithoz GmbH embarked on an ESA-sponsored project to develop and test the potential of 3D printing in a micro-gravity environment.
The scientists’ team aimed to research the feasibility of processing lunar scrap metals (which might be recovered from debris from old missions or old satellites) to produce high-quality printed parts using additive manufacturing (AM), specifically Lithography-based Metal Manufacturing (LMM), all of this while taking into consideration potential in situ contamination by using lunar regolith simulant.
Challenges of AM in the lunar environment
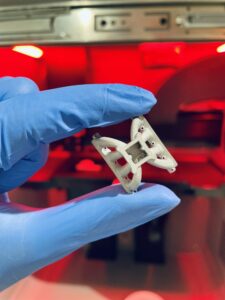
The biggest challenge for lunar additive manufacturing is the harsh lunar environment, including the atmosphere, gravity, temperature, radiation, and the potential contamination of moon dust. However, the Incus 3D printing solution, Hammer Lab35, was able to print recycled Titanium powder while maintaining proper part quality. The produced parts demonstrated a high level of strength, comparable to Metal Injection Molded Titanium parts standards (1000-1050 MPa).
The LMM technology used in the project can print from scrap metals using pre-mixed feedstock, without free and loose powder and the need for any support structures, offering a sustainable zero-waste workflow. The project also included the development of a green binder and the optimization of pre- and post-processing steps to print and test different demonstrators for future lunar applications.
“This project has proven that LMM technology is able to use recycled powder for the feedstock material and provide sustainable zero-waste workflow,” said Incus CEO Dr. Gerald Mitteramskogler. “We expect that further developments in metal recycling technologies will open the way to metal materials with more settled sintering processes for the lunar environment.”
The project’s results have important implications for the future of space exploration and the development of sustainable Moon bases. Remember that the creation of a sustainable Moon base requires the successful use of lunar resources.
“The use of local lunar resources, as well as the recycling of old spacecraft, are essential for a sustainable and Earth-independent Moon base. Through this project, it was proven that the LMM technology is able to use recycled powder sources as feedstock material. Furthermore, it was demonstrated that contaminations for the powder sources by using lunar regolith simulant are manageable, especially from the perspective of the printing process. With those aspects in mind, as well as the future challenges already foreseen and anticipated, upcoming research and development will be able to continue and open-up further the way towards a sustainable Moon settlement finally released from Earth dependency,” stated Francesco Caltavituro, System Engineer for the project at OHB.
Remember, you can post job opportunities in the AM Industry on 3D ADEPT Media free of charge or look for a job via our job board. Make sure to follow us on our social networks and subscribe to our weekly newsletter : Facebook, Twitter, LinkedIn & Instagram ! If you want to be featured in the next issue of our digital magazine or if you hear a story that needs to be heard, make sure to send it to contact@3dadept.com