A wide range of rules has been established to implement conventional manufacturing processes. AM breaks many of these rules since it introduces new capabilities that are not compatible with conventional manufacturing. One of these rules consists in determining if the fabrication of a part is suitable for AM. In the lines below, Julien Cohen, Application Engineer at 3DEO Inc., metal 3D Printer manufacturer and service bureau, answers 3 questions that are worth taking into consideration before selecting a metal AM production process for industrial production.
Let’s make things clear now: this topic could have been addressed from the polymer 3D Printing perspective, or from the liquid 3D Printing perspective. Fascination for AM also lies in its strangeness. Even though Julien Cohen makes it clear from the very beginning that “there are many ways to address this issue”, his answers are based on his experience at 3DEO Inc. and in large corporations with tens or hundreds of thousands of SKUs (stock-keeping unit). They will be combined with industry researches and application examples shared by companies.
Frameworks to define AM candidacy
We have outlined three different frameworks that can be assessed before going down the AM route for series production.
1- A database of components and assemblies
Despite the significant advantages of AM, all parts are not suited for AM processes. The most logical step would consist in listing the criteria that should be taken into account to define candidate products for AM applications.
In theory, conventional manufacturing metrics which are usually compared with AM metrics and related experience are first filtered by design engineers to determine the first criteria selection. Secondly, a database of components and assemblies is used to assess AM potential and label according to the pre-determined criteria. The same selection criteria are usually applied for every new part of assembly and result in a model decision for AM candidacy.
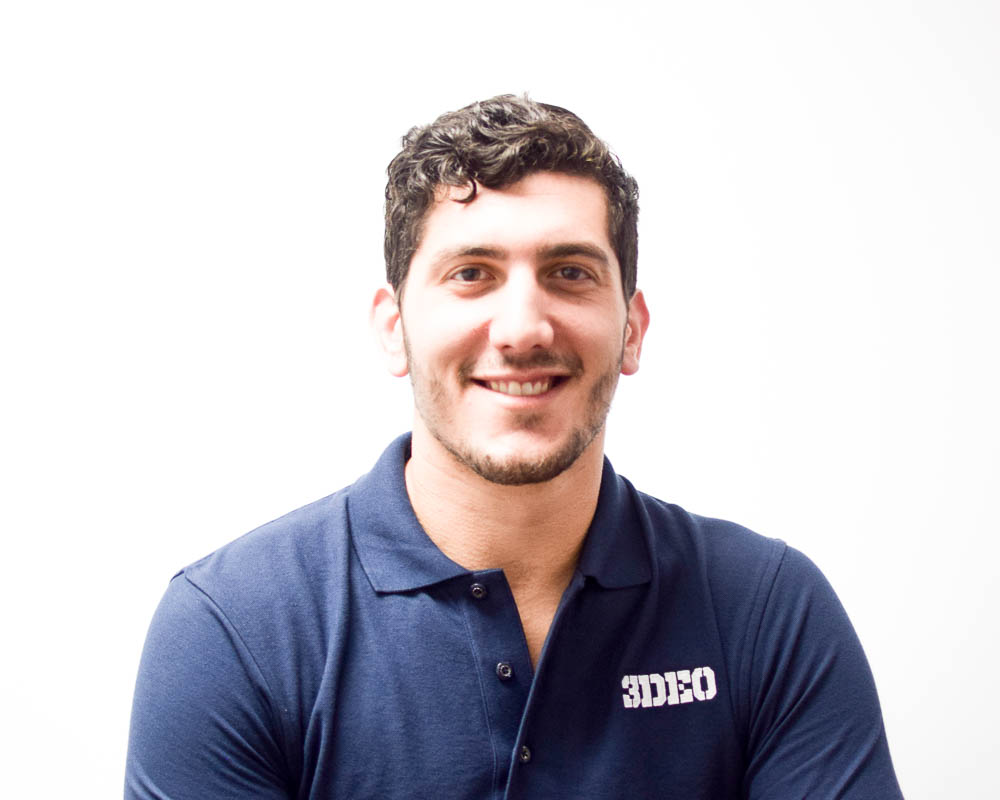
In practice, “there is no central library containing all the necessary data and metadata to make this decision. For example, how do I go search for parts in a specific size range, made via investment cast aluminum, at a certain annual quantity range? The first hurdle for many corporations is to make these data accessible in a searchable database.
Once that access is available, the problem can be addressed from multiple angles. In my opinion, rather than starting with a list of parts and identifying which AM process could be used for each, it’s more effective to identify a potential AM process and then filter out parts based on the known process limitations. This workflow can be roughly split into four steps:
1) Choose an AM process to focus on (L-PBF, 3DEO’s Intelligent Layering®, DED, Cold Spray, etc.)
2) Disqualify parts using absolute process limitations (i.e. maximum build volume, available materials, feature size capability, annual quantity)
3) Rank the remaining parts using some kind of business case metric (which application would make the biggest impact to the business with a 20% cost reduction, 20% weight reduction, or faster time-to-market?)
4) Pare this ranked list down to a manageable number of top opportunities, and examine these in-depth to determine which is worth pursuing”, Cohen explains.
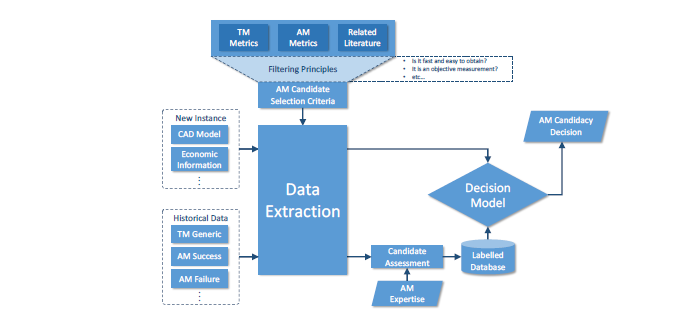
Figure 1. Framework to define AM candidacy (in theory) – Credit: McGill University – (Automated Candidate Detection for Additive Manufacturing).
2- The design analysis approach
Another methodology applied by companies is the design analysis. This approach consists in identifying parts where AM could be applied efficiently by leveraging DfAM capabilities. Four criteria are often taken into consideration in this process: functions integration, customization, lightweight design as well as operation efficiency.
Functions integration can be understood as the way the design will be integrated in the whole structure. This criterion aims to determine if a group of parts can be redesigned into one single part, if a product size can be reduced while achieving the same function, or if it will require less time for its production. Complex assemblies made of single-function parts often meet this criterion as each of them can be produced separately to reduce design and fabrication complexity.
From a technological perspective, the “customization” criterion involves multiple design variations and smaller lot sizes at the manufacturing level. This criterion is the most-acknowledged benefit of AM – it satisfies the requirements of consumer products end-users.
Lightweight design on the other hand, usually goes hand in hand with weight and materials costs savings. The challenge of the design engineer here is to improve parts performance with weight-reduction and ultimately less materials & costs savings. To tackle this issue, engineers usually leverage topology optimisation software, as such tools increase the part’s geometric complexity by placing the material in locations required by the function.
Lastly, the operation efficiency consists in exploring all the innovative solutions that can improve the part efficiency once it will be used. This criterion often leads the engineers to explore ways the product life expectancy can be improved, ways to lower operational costs, ways to improve energy conversion and many more.
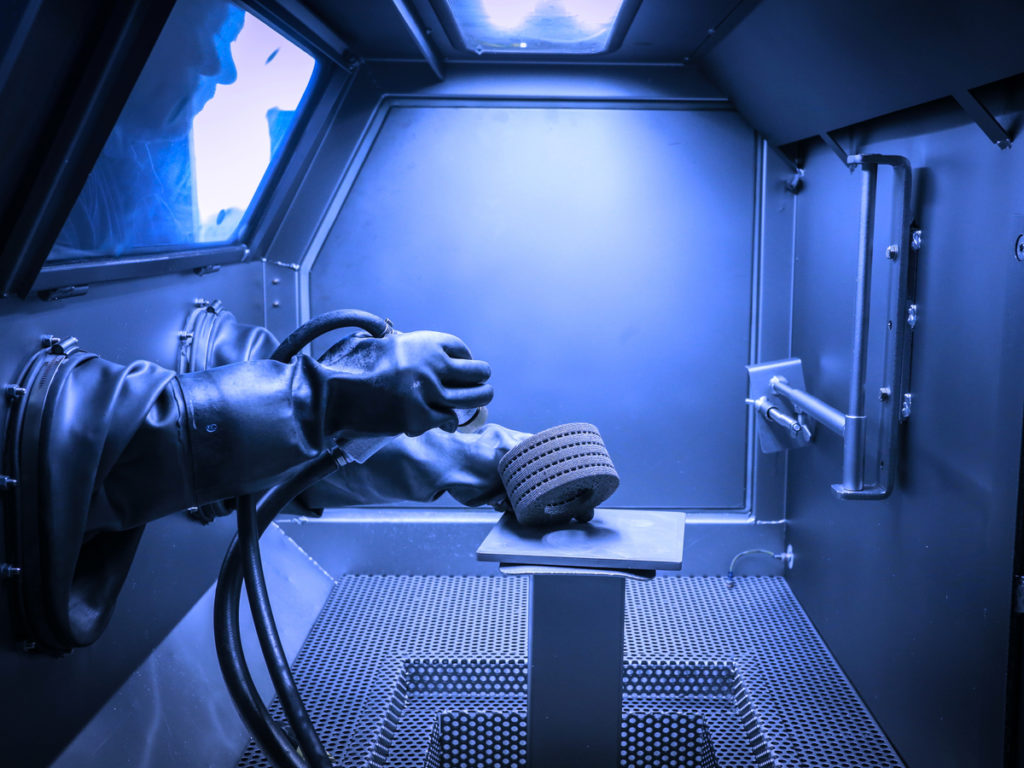
In general, this approach looks at the various technological and economic advantages of AM. Moreover, depending on the ultimate goal of the manufacturer, the part might not always need to be redesigned.
“People that work in the AM industry constantly get asked “can we 3D print this part?”, and the answer is almost always yes… but this is not the right question. What you need to ask is “should we 3D print this part?”
It’s possible that without redesign an organization can still reap benefits from switching to an AM process: shorter lead times, no tooling cost, decreased risk, etc. But without redesign, they will miss out on the incredible potential for optimization which AM design freedom offers. We have an incredible array of generative design, implicit modelling, and topology optimization software tools now at our fingertips, and it’s a shame to leave their capabilities on the table.
My strong opinion is that AM experience should be injected as far upstream in the design process as possible, and that AM can have a much greater effect on new product development and clean sheet design projects vs. existing products which are already tooled up and in production”, 3DEO’s application engineer points out.
Unfortunately, this method of criteria analysis also presents its limitations as it only focuses on areas where AM will succeed, and does not address what makes AM a bad choice for a specific part. In this sense, it does not reject parts with obvious limitations. Furthermore, it does not take into account all the operational factors of the production process which includes the supply chain.
3- “The supply chain scenarios”
Supply chain has become an integrated part of the AM process. That’s why, Senvol, a company that provides data to help companies implement AM, has defined seven supply chain scenarios where AM can be cost-effective. These scenarios take into account manufacturing expense, lead time, inventory costs, sourcing, remote operations, import/export costs, and functionality.
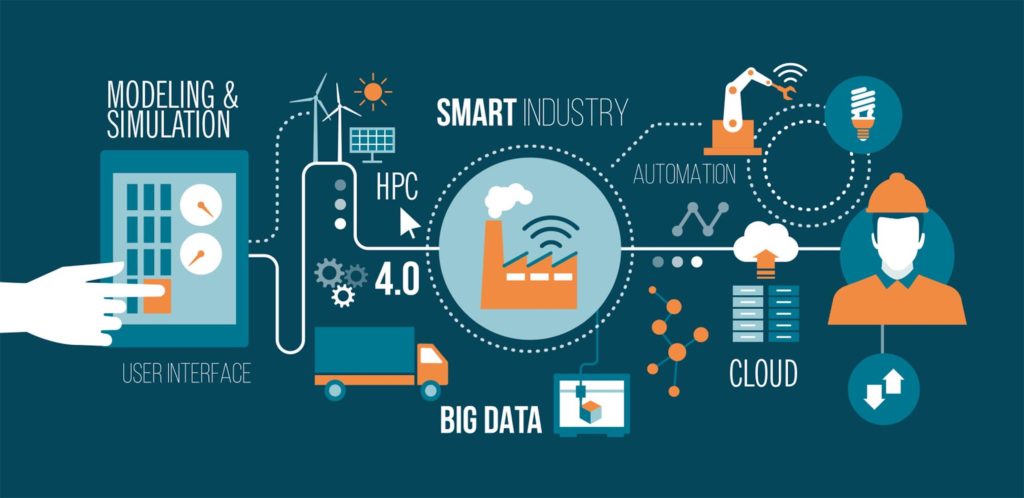
Checking AM candidacy through this approach is pretty simple: if a component meets the requirements of one or more scenarios, then AM should be explored further. However, if none of these scenarios is met, therefore AM is likely not the ideal technology process to leverage.
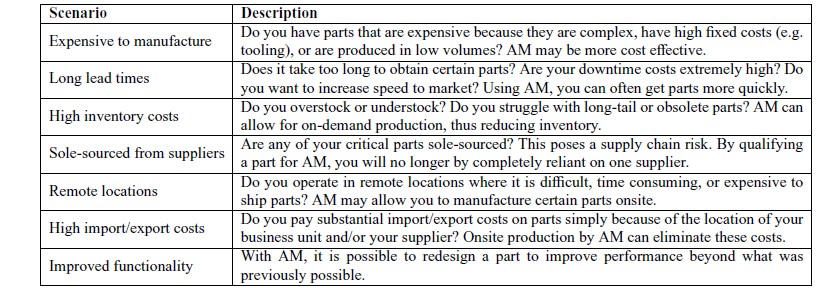
The main advantage of this approach is that the questions are easy to understand and can be quickly assessed. However, it is not always considered as an objective method.
Do these criteria differ from one AM technology to another?
Sometimes, each of these methods is assessed with the type of production (low-volume production or high-volume production) to achieve in mind. Cohen draws attention to the fact that these terms can easily raise confusion among industrials from various industries.
“High-volume production parts in the aerospace industry might mean a few hundred parts annually. Low-volume production in the industrial and automotive industries might mean tens of thousands of parts annually” the expert states.
Furthermore, one common limitation all these methods share is the fact that they do not take into account the uniqueness of each AM technology.
“For example— while powder bed processes like L-PBF and EBM can enable significant optimization of strength-to-weight ratio, heat transfer capability, and internal fluid flow efficiency, the process is still extremely expensive and comes with a laundry list of limitations and considerations, especially in serial production (I’ve given conference talks specifically on the difficulty of using L-PBF in production). These processes can be fantastic tools for low-volume, high-cost parts, but with the right support design and process control can also be cost-effective for small parts which nest efficiently on the build plate.
Similarly, 3DEO’s Intelligent Layering® process was developed specifically for high-volume, low-cost applications— I’m talking 100k+ annual quantities and <$5 per part. Our process is unique in the metal AM space and overcomes many limitations inherent to emergent processes like binder jetting, as well as traditional processes like MIM and CNC machining. The types of applications that fit our process are completely different than those which fit many of the other processes on the market.
In the absence of widespread industry standards and technology maturity, making the correct choice of application requires deep knowledge of available AM processes, their pros and cons, and experience using them in the past. At 3DEO we maintain long-term production partnerships with our customers and offer our knowledge base to accelerate these types decisions” 3DEO’s spokesperson comments.
In a nutshell
We have described three AM candidate selection criteria methods that are often utilized within organizations. Each of these AM technologies has its pros and cons. However, the more the market advances, the more companies will be able to standardize a guide that will help verify AM candidacy for production applications.
This feature has initially been published in the July-August Issue of 3D ADEPT Mag.
Remember, you can post job opportunities in the AM Industry on 3D ADEPT Media free of charge or look for a job via our job board. Make sure to follow us on our social networks and subscribe to our weekly newsletter : Facebook, Twitter, LinkedIn & Instagram ! If you want to be featured in the next issue of our digital magazine or if you hear a story that needs to be heard, make sure to send it to contact@3dadept.com