With the dozen players that entered the electron beam melting market during the past five years, the electron beam melting status has evolved from a “spare wheel” technology to a solution that could provide strong advantages that laser powder bed fusion (LPBF) does not. Among these newcomers, one that could potentially disrupt the current technology landscape is JEOL LTD, a company founded in 1949 and headquartered in Akishima, Japan, with seventeen overseas subsidiary companies located throughout the Americas, Europe, Asia, and Australia. We caught up with Bob Pohorenec, President of JEOL USA to understand why.
JEOL USA, Inc., located outside of Boston, was established in 1962. The company first appeared on our radar in 2021, with the launch of its JAM-5200EBM metal Additive Manufacturing machine but the company’s beginnings in the AM industry go back to 2014 when it joined the Japanese government’s Technology Research Association for Future Additive Manufacturing project, or TRAFAM. It collaborated with Dr. Akihiko Chiba of Tohoku University on a four-year project to build an EB-PBF machine based on JEOL’s advanced electron optics and automation that resulted in the development of a prototype machine installed at Tohoku University.
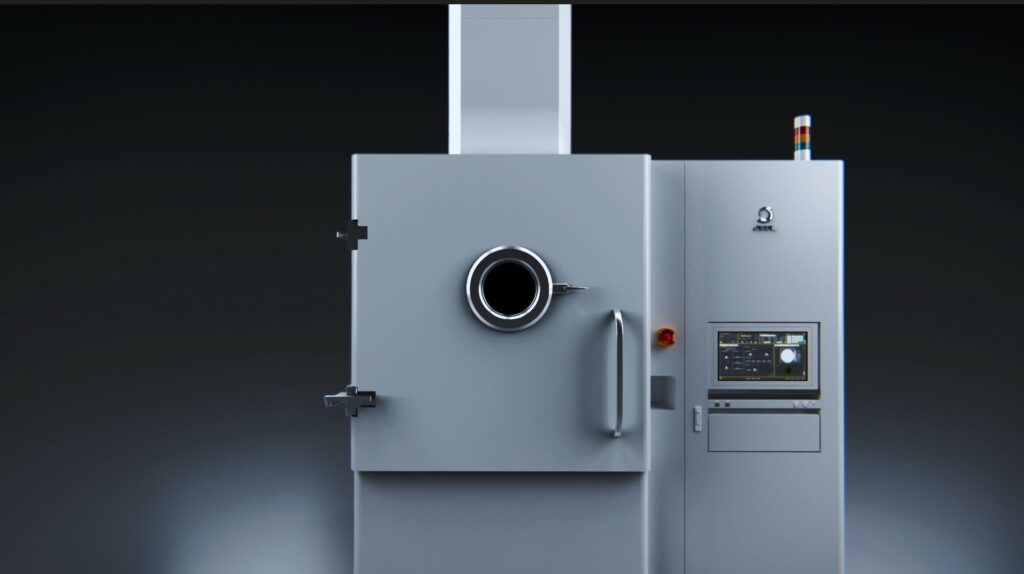
If the company’s Electron Beam Powder Bed Fusion (EB-PBF ) 3D printing technology is at the heart of this conversation, it’s important to keep in mind that AM users also use the company’s metrology and analytical instruments to support various research projects or manufacturing processes.
That being said, when a company brings over 7 decades of expertise in electron beam technology as a supplier of electron microscopy and e-beam lithography, one assumes that they will not face the same challenges as other OEMs when entering the AM market – challenges related to the novelty and maturity of the technology and how they can shape a specific business.
Nevertheless, the similarities between the AM market and the semiconductor equipment market have somehow helped JEOL position itself in the electron beam melting niche. As per Pohorenec’s words, similarities that are critical to both markets include “performance, cost of ownership, equipment up-time, spare part and technical support availability.”
“However, the semiconductor equipment market is very mature and has gone through a great deal of consolidation. The AM market is still developing which makes it very exciting for us,” he continues.
To date, looking back at the key milestones that have marked JEOL’s AM activities ever since the company launched its JAM-5200EBM metal 3D printer in 2021, Pohorenec mentions three key moments.
The installation of their first unit at Cumberland Additive Inc., in the Neighborhood 91 Additive Manufacturing Production Campus in Pittsburgh in September of 2023; the AMS7032 operational qualification (OQ) standards the company met while achieving the AMS7011 material requirements for Ti-6Al-4V alloy and a recent order received in December for the second unit to be installed in the United States from a top-tier research university that is working with a National Laboratory on AM using refractory metals.
“The next milestone will be the first installation of a JAM-5200EBM in Europe at the Technical University of Munich (TUM) which will happen in the next few months,” he enthuses.
Beyond these promising outlooks, what truly makes JEOL’s Electron Beam Powder Bed Fusion 3D printer outstanding?
First and foremost, for beginners in this space, electron beam powder bed fusion (EB PBF) relies on the use of a high-powered electron beam to melt conductive metal powders like copper and titanium together layer by layer.
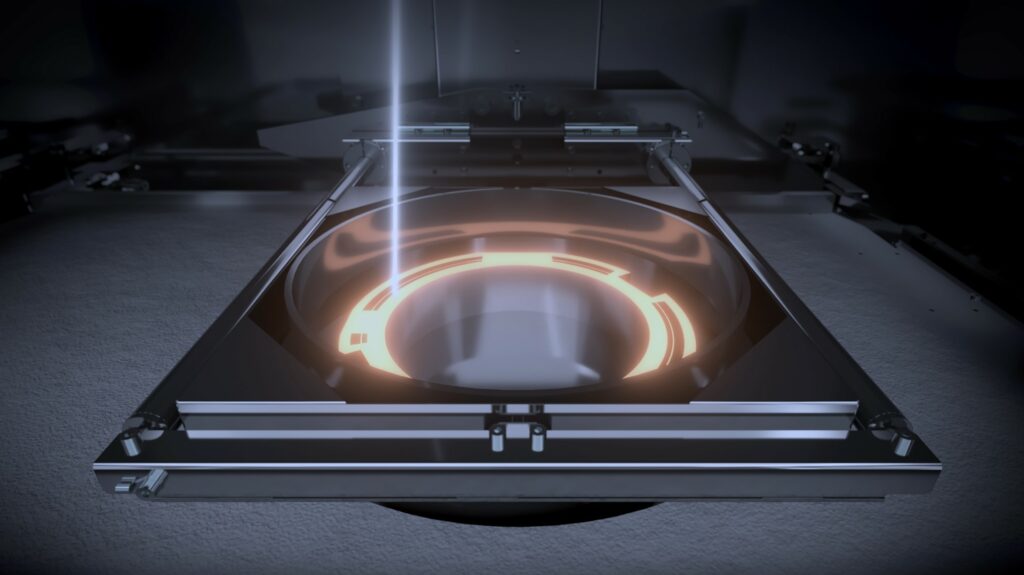
“In the case of the JAM-5200EBM we employed quite a bit of know-how and technology from our electron beam lithography systems which are used in semiconductor manufacturing environments. The result is an electron optical system that can allow user’s a high degree of adjustability in beam current without impacting the beam’s diameter. This system also delivers at least 1500 hours of electron emitter lifetime which is more than double that of other EB-PBF systems and translates into increased tool availability. Another major differentiator is our patented “e-shield” which eliminates the need of helium gas during the build process. We will be releasing several new features this year that will be very useful to machine owners,” JEOL USA President explains.
Regular readers of 3D ADEPT Media may remember that we recently discussed the reasons why Electron Beam Additive Manufacturing in general could be an ideal production candidate for large-scale parts, yet still lags far behind in adoption. Electron beam melting has found applications across the medical, aerospace and other industries.
If he didn’t mention exactly which ones, Pohorenec confirms there are applications where EB-PBF is not an appropriate fit. Speaking of applications where the technology can play a key role, he counts aerospace, defense, and medical device verticals because they “require metals such as Ti64, Inconel, copper, and tungsten and they need to meet stringent property requirements. Replacement of low-volume cast parts within a relatively short lead-time is also an area that EB-PBF can play a valuable role.”
The everlasting comparison with PBF technologies
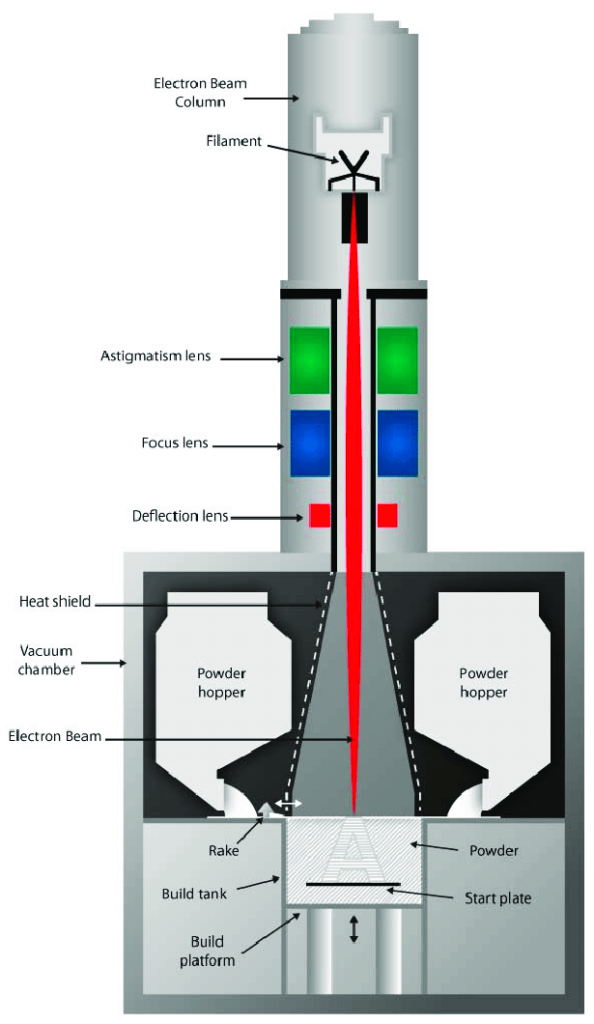
Electron beam powder bed fusion has always been described and seen as the fiercest competitor of LPBF. If I believe they shouldn’t be labelled as competitors, one needs to recognize a few advantages this process has over LPBF. For instance, the ability to process very pure metals with no porosity or oxidation, the processing of materials at highly elevated temperatures, the minimized need for heat treatment or even the possibility of reusing up to 98% unused powder.
On another note, EPBF has often been criticized for its lack of material selection and multi-material options, as well as the long time the vacuum may take to build up and less detailed resolution compared to PBF.
Needless to say, these benefits and drawbacks may vary from one machine to another. Speaking of a few advantages that could be associated with aerospace parts production and more, Pohorenec said: “EB-PBF’s ability to build free-standing or support-free structures inside a large volume is a major time and cost advantage compared to other PBF technologies. Additionally, this allows for a variety of parts to be built within the volume which allows the design engineers to maximize the productivity of the machine.”
Among the wide range of aerospace applications that could be achieved through EPBF, one that Pohorenec highlights is the jet engine turbine blade whose designs can be improved for higher efficiency engines. For the president, “the ability to stack those blades without supports and obtaining the same metallurgical properties as traditionally manufactured blades has real value.”
And now?
If I do not doubt there are exciting times ahead for companies that specialize in EPBF, I strongly believe those who could make a difference in the market are the ones who will focus on improving customer support. That’s anyway, what JEOL intends to do.
“Some of the industries we support require service level agreements with guaranteed response times, meaning a service engineer on-site within a specified number of hours or days, and quick delivery of spare parts. Over the years we have developed a large and expanding customer service infrastructure to support our equipment owners. We locate field service engineers throughout the geographies where our equipment is installed to shorten response times. In North America alone we have over 180 engineers in the field. We take customer service very seriously and treat it as a key component of our value proposition,” Pohorenec concludes.
This article has first been published in the January/February edition of 3D ADEPT Mag.