Les services de moulage d’inserts sont l’un des principaux services proposés par les plateformes de fabrication numérique. Un tel service permet d’accélérer le cycle de développement des produits dans les secteurs de la médecine, de l’automobile, des produits de consommation et des composants électroniques. Le fait est que, bien que les opérateurs ne remettent plus en question la capacité des technologies de fabrication additive à produire un résultat beaucoup plus rentable que l’outillage et la fabrication de moules conventionnels, ils se demandent encore quelle technologie de FA convient le mieux à la production d’inserts de moules prototypes.
L’essor de l’impression 3D a eu des répercussions non seulement sur la production de pièces d’usage final en tant que technologie de fabrication directe, mais aussi en tant que technologie de fabrication indirecte. Par exemple, la fabrication additive est parfois utilisée pour créer des moules en vue d’un moulage en uréthane ou en silicone. Dans d’autres circonstances, elle est utilisée pour créer des outils tels que des gabarits ou des montages qui améliorent les performances des cellules d’usinage. Cette capacité à créer des outils personnalisés pour les processus de fabrication traditionnels s’étend également au domaine du moulage par injection, où la technologie d’impression 3D est utilisée pour créer des inserts de moule d’injection personnalisés. Mais lorsqu’il s’agit de créer un insert de moule personnalisé, quelle technologie est la meilleure ? Nous nous sommes entretenus avec quelques experts en fabrication numérique pour en savoir plus sur deux des technologies d’impression 3D les plus populaires utilisées pour cette application, le jet de matière et la fusion laser sur lit de poudre.
L’utilisation des technologies de fabrication additive pour la production d’inserts de moules
Dans le but de répondre aux besoins de personnalisation de masse, les entreprises de FA ont exploré leurs processus de fabrication pour produire l’outillage utilisé dans le moulage par injection, avec des niveaux de réussite variés.
« Théoriquement, n’importe quelle technologie AM peut être utilisée. On pourrait immédiatement penser à l’impression 3D par extrusion qui est probablement la technologie la plus utilisée pour les prototypes, mais c’est probablement parce que c’est la technologie que les gens connaissent le mieux. Il n’y a aucune raison de ne pas utiliser le SLS, d’autres procédés à lit de poudre comme le faisceau d’électrons, ou même le jet de liant. Au bout du compte, ce sont les résultats obtenus qui comptent le plus », a déclaré d’emblée Cullen Hilkene, CEO de 3Diligent, à 3D ADEPT Media.
Jusqu’à présent, la plupart des applications qui ont été partagées par les entreprises ont été réalisées à l’aide des technologies DLP, SLA, Freeform Injection Moulding, SLS, DMLS / SLM, ainsi que PolyJet. Cependant, DMLS et PolyJet sont les technologies les plus largement mentionnées pour de telles applications, c’est pourquoi nous nous concentrerons uniquement sur ces deux technologies dans le cadre de ce dossier.
Cela dit, quelle que soit la technologie de FA utilisée, la perspective de fabrication révèle que « traditionnellement, le moulage avec des inserts métalliques est réalisé dans le but de renforcer les propriétés mécaniques des inserts, de réduire le temps de cycle et d’obtenir des articles moulés avec une meilleure qualité esthétique/dimensionnelle. »
Par ailleurs, toujours selon les experts de ZARE, un autre objectif de fabrication consisterait à intégrer un article aux propriétés thermiques spécifiques, dans un moule réalisé avec un matériau différent.
En outre, « une autre utilisation, plus critique, concerne la création de canaux de refroidissement particuliers et équidistants de la surface. Ces canaux de refroidissement permettent une plus grande dissipation de la chaleur dans l’unité de temps, avec pour conséquence une réduction de la durée du cycle de moulage et une réduction des déformations sur le produit fini, augmentant ainsi la qualité du produit final », ont-ils déclaré.
Brève description de la DMLS/fusion laser sur lit de poudre (LPBF).
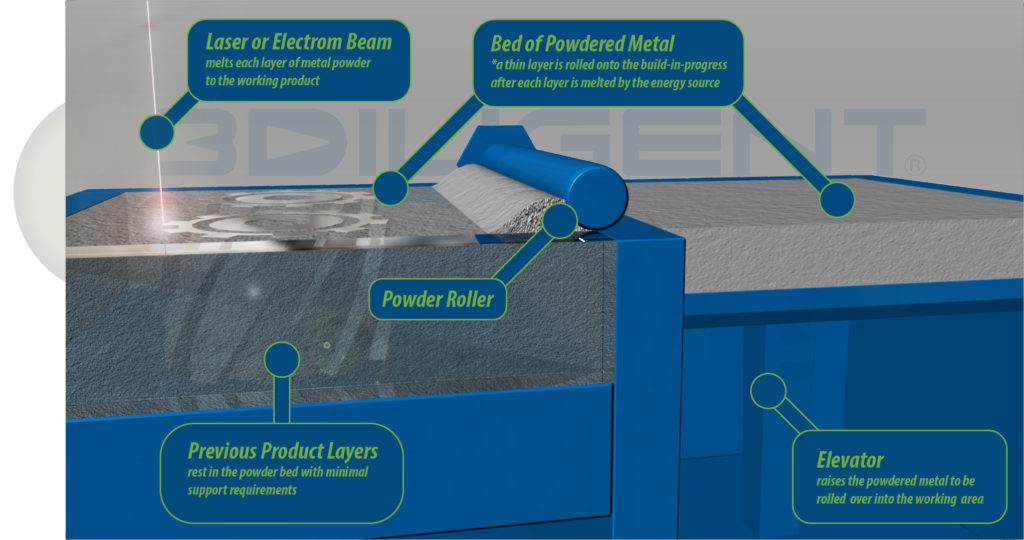
Tout d’abord, notons que, même si la technologie DMLS est souvent utilisée de manière interchangeable avec la technologie SLM ou LPBF, il convient de préciser que la technologie DMLS est une marque d’EOS, SLM, un terme introduit par l’Institut Fraunhofer en 1995, tandis que LPBF est le nom générique donné au processus de fabrication. C’est pourquoi l’appellation « fusion laser sur lit de poudre » sera celle utilisée dans ce dossier.
Effaçons toute confusion qui pourrait survenir ici : Le DMLS, qui signifie Direct Metal Laser Sintering, comporte le mot « Sintering » alors qu’en réalité, il fonctionne par fusion. Dans la même veine, le LPBF utilise le mot « Fusion » alors qu’on ne peut pas faire fondre un plastique, il faut le fritter.
Quoi qu’il en soit, pour ceux qui ne le connaissent pas, ce procédé de fabrication permet de produire des « pièces de forme nette et quasi nette directement à partir d’un fichier de dessin numérique avec des tolérances dimensionnelles inférieures à 0,1 mm » grâce à l’interaction entre un laser à haute énergie et une charge de poudre métallique.
Pendant le processus de fabrication, la machine remplit sa chambre de construction d’un gaz inerte, puis la chauffe à la température d’impression idéale. En fonction de l’épaisseur de la couche définie au préalable (généralement 0,1 mm d’épaisseur de matériau), une fine couche de poudre est appliquée sur la plate-forme de construction. Une fois que le laser à fibre optique (200/400 W) balaie la section transversale de la pièce, il permet la fusion des particules de métal entre elles. Une nouvelle couche de poudre est étalée sur la couche précédente à l’aide d’un rouleau. D’autres couches ou sections transversales sont fusionnées et ajoutées. Le processus est répété jusqu’à ce que la pièce imprimée en 3D soit complètement construite.
Brève description du procédé PolyJet/ Material Jetting
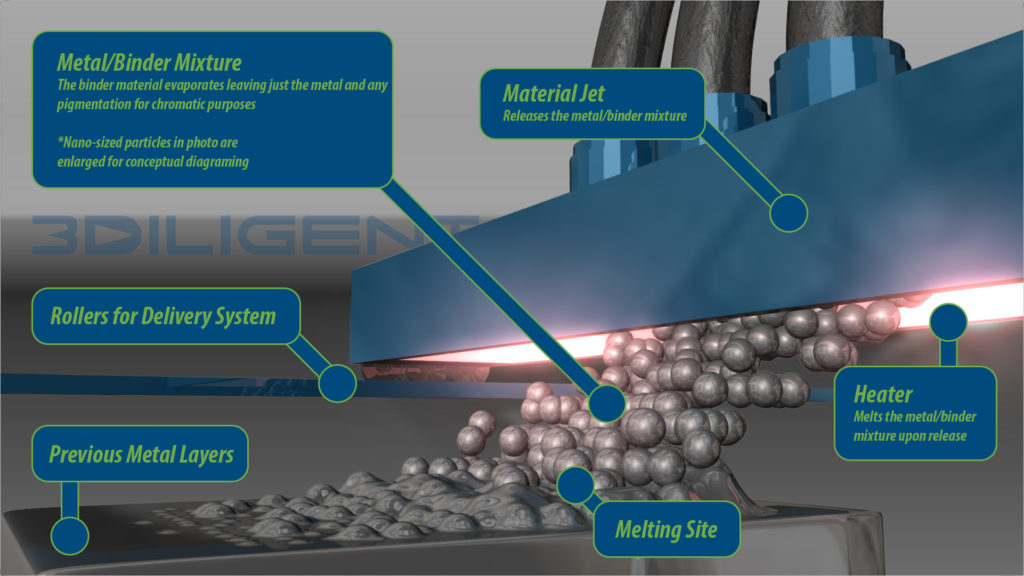
Le PolyJet est un procédé de fabrication qui fonctionne soit en continu, soit à la demande (DOD = Drop on Demand). Avec un processus similaire à celui d’une imprimante à jet d’encre bidimensionnelle, il fabrique des pièces en projetant des milliers de gouttelettes de photopolymère sur une plateforme de construction et en les solidifiant avec une lumière UV.
Dans les années 2000, Objet-Geometries a été la première entreprise à développer une imprimante 3D avec ce procédé, qu’elle a breveté sous le nom de PolyJet. Onze ans plus tard, en 2011, Stratasys a racheté Objet et, depuis lors, a élargi sa gamme de produits aux solutions de jet de matière (MJ = Material Jetting).
Aujourd’hui, le nom PolyJet reste associé aux imprimantes 3D de Stratasys. Cependant, Stratasys n’est pas la seule entreprise à développer des imprimantes 3D industrielles basées sur ce procédé, c’est pourquoi le terme « Material Jetting » sera utilisé dans cette démarche, car il désigne le nom général de ce procédé de fabrication.
Le processus d’impression commence par le versement de la résine photopolymère dans le conteneur de matériau. Cette résine doit être chauffée (entre 30 et 60 °C) afin d’atteindre la viscosité appropriée.
Lorsque le chariot de l’axe X commence à se déplacer sur la plaque de construction, les têtes d’impression commencent à projeter sélectivement des centaines de minuscules gouttelettes de résine. Les sources de lumière UV suivent la trajectoire des têtes d’impression et durcissent instantanément la résine pulvérisée. Une fois qu’une couche entière est terminée, la plateforme de construction descend d’une couche en hauteur et le processus est répété jusqu’à ce que la pièce soit entièrement formée.
Avec les progrès technologiques, les fabricants de machines ont développé des imprimantes 3D dotées de plusieurs têtes d’impression afin de réaliser une impression multi-matériaux. Selon la machine utilisée, les imprimantes 3D multi-matériaux peuvent permettre l’utilisation d’un matériau de support dissoluble ou de plusieurs variétés ou couleurs de matériau fonctionnel.
En outre, au fil du temps, plusieurs types de technologies de projection de matériaux ont été développés afin de répondre aux divers besoins des industries. Il s’agit par exemple de procédés de projection de matériaux qui fonctionnent avec de la résine et des cartouches, de procédés de projection de matériaux qui fonctionnent avec de l’encre, de procédés de projection de matériaux qui fonctionnent avec de la cire et des cartouches ou même de procédés de projection de matériaux qui fonctionnent avec du métal et des cartouches.
« S’il est important de faire la distinction entre le jet de matière avec les métaux et les plastiques, il convient de noter que les inserts de moule sont généralement fabriqués en métal », note Hilkene.
Toutefois, cela ne signifie pas qu’il est impossible de produire un insert de moule en plastique. En fait, les technologies de FA susmentionnées qui peuvent être utilisées pour produire des inserts de moule incluent la FFF qui traite les matériaux plastiques. Il s’agit ici de comprendre ce qui explique le passage des procédés de fabrication traditionnels aux procédés de fabrication additive, puis le choix d’une technologie de FA spécifique plutôt qu’une autre.
Dans ce cas, bon nombre des difficultés traditionnelles de la conception pour le moulage par injection en métal se sont présentées dans la conception de l’outillage en plastique. Cependant, la plupart de ces problèmes sont souvent amplifiés en raison de la moins bonne finition de surface d’un moule imprimé en 3D par rapport à un moule métallique similaire, d’où le choix d’un processus de FA métallique pour cette production.
En outre, les recherches montrent que les inserts de moule en plastique imprimés en 3D ont révolutionné la fabrication des moules dans le secteur de la transformation des plastiques. Le faible coût des moules ainsi que la mise en œuvre rapide des modifications de conception ont séduit les utilisateurs au début, jusqu’à ce qu’ils se rendent compte que les résultats n’étaient pas toujours durables. En outre, en raison des températures plus élevées des matériaux et des pressions d’injection élevées, les cycles de fonctionnement des moules en plastique imprimés en 3D diminuent souvent. La recherche de solutions plus stables pour les petites séries et les quantités moyennes a conduit de nombreux fabricants à envisager des alternatives de FA métal.
Pour la production d’inserts de moule, qu’est-ce qui fera pencher la balance en faveur de LPBF ou de MJ ?
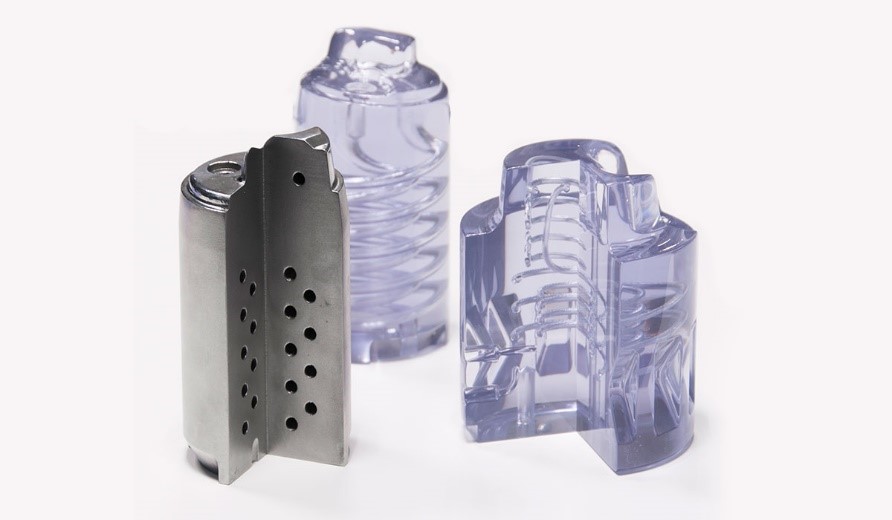
Afin d’évaluer quelle technologie convient le mieux à la production d’inserts de moules, nous avons comparé ces deux technologies sur la base de cinq critères principaux : la complexité de la géométrie, le post-traitement, le calendrier, le volume de production et les coûts.
Cette analyse est principalement basée sur notre entretien avec Cullen Hilkene, CEO de 3Diligent, une entreprise qui concrétise la fabrication numérique distribuée. Des contributions externes d’autres entreprises ainsi que des recherches ont également permis d’apporter l’évaluation la plus précise de ces processus.
Complexité de la géométrie
Il va sans dire que certains produits sont faciles à fabriquer par moulage par injection en raison de leur conception simple à cavité unique et de leur taille. Cependant, ce n’est un secret pour personne que la FA est attrayante en raison de sa capacité à produire des géométries complexes, notamment des canaux de refroidissement complexes.
Selon Hilkene, le procédé LPBF gagne un point ici, car la technologie convient au refroidissement de pièces aux formes complexes. Selon l’expert, le défi au niveau de la fabrication consiste à maintenir une température uniforme à la surface du moule pour refroidir la matière fondue chaude à l’intérieur de la cavité. Non seulement ce processus de refroidissement prend du temps, mais il entraîne souvent des coûts de production élevés. Pour dissiper la chaleur en un temps très court pendant le processus de fabrication, les ingénieurs doivent reconstruire le canal de refroidissement près de la surface de la pièce. Par rapport au fraisage traditionnel, le procédé LPBF apporte des améliorations significatives à ce niveau car il donne aux ingénieurs la possibilité de concevoir des géométries libres, en fondant couche sur couche des poudres métalliques, tout en assurant une dissipation régulière de la chaleur à travers la chambre.
Post-traitement
Certaines technologies de FA ne nécessitent pas de post-traitement une fois l’étape de fabrication terminée. Dans ce cas précis, le procédé LPBF perd un point car la technologie « n’imprime pas toujours de manière aussi lisse que les autres procédés de fabrication, d’où la nécessité d’une étape de post-traitement à la fin du processus d’impression« , note le CEO de 3Diligent.
En revanche, pour les applications où la résistance à l’usure n’est plus le facteur le plus critique, le Material Jetting est reconnu pour fournir des pièces imprimées en 3D avec une grande précision et un excellent état de surface.
Temps, coûts et production en volume
Par rapport aux procédés de fabrication conventionnels qui prennent souvent plusieurs semaines, les deux procédés de FA permettent aux opérateurs de gagner du temps. Néanmoins, en comparant ces procédés LPBF et MJ, on constate que le LPBF est plus coûteux et nécessite plus de temps de production que le MJ.
Non seulement le processus de fabrication avec le procédé LPBF nécessite une étape supplémentaire de post-traitement – qui est déjà considérée comme l’étape la plus coûteuse du processus de production global -, mais parfois, la production d’inserts de moule doit répondre à des solutions spécifiques au client qui ne peuvent être définies à l’avance.
En ce qui concerne le volume, l’une des premières étapes au niveau de la production consiste généralement à déterminer si un moule va être utilisé pour fabriquer 30 ou 30 000 pièces. Une fois les prototypes approuvés, les procédés de fabrication conventionnels deviennent généralement l’option idéale pour la production en série. Néanmoins, entre les deux procédés de fabrication que nous analysons aujourd’hui, on constate que le Material Jetting convient mieux à la production de moules à faible tirage.
Alors, que devons-nous garder à l’esprit ?
Le tableau ci-dessous donne un aperçu des éléments qui ont été évalués pour comparer le LPBF et le MJ pour la production d’inserts de moule.
Technologies/Critères d’analyse | Principaux processus concurrentiels dans la gamme traditionnelle | Complexité de la géométrie | Post-traitement | Temps | Coûts | Production de volume |
Fusion laser sur lit de poudre |
Fraisage traditionnel |
Idéal pour les formes complexes | Étape supplémentaire de post-traitement | Plus de temps de production | Coûteux par rapport au procédé MJ | Production en gros volume |
Jet de matière | Excellents résultats précis | Pas d’étape de post-traitement intensif | Réduction du temps de production par rapport au LPBF | Moins cher que le LPBF | Idéal pour les moulages à faible tirage |
Et maintenant ?
Nous ne pouvons pas dire avec certitude que les défis entourant la conception des outils dans les industries de moulage par injection seront tous relevés dans un avenir proche. Cependant, on peut témoigner des différents procédés de fabrication qui permettent aujourd’hui de produire un outil aux géométries complexes, « avec des dimensions précises, une alimentation en matière dans la cavité, des canaux de refroidissement et une éjection facile de la pièce solidifiée ».
Deux de ces technologies ont été évaluées aujourd’hui. Ce que nous retiendrons, c’est que les inserts de moule imprimés en 3D peuvent être produits dans des délais rapides (1 à 2 semaines, contre 5+ semaines avec le fraisage traditionnel). Plus important encore, les technologies de FA sont idéales pour les conceptions de moules où des changements ou des itérations sont probables, pour les pièces relativement petites (moins de 150 mm) et pour les faibles quantités produites.
Malgré ces avancées au niveau de la production, il faut noter que nous ne savons pas toujours si, oui ou non, ces pièces imprimées en 3D sont mises sur le marché en tant que produit autonome ou en tant que partie d’une structure plus importante. Sans compter qu’il n’existe aucune indication claire du cycle de vie d’un moule imprimé en 3D.
Ce contenu a d’abord été publié dans le numéro de Juillet/Août 2021 de 3D ADEPT Mag. – Image de Une: 3D Hubs.