There are some industries – like the energy sector – where the struggle to drive climate change is more challenging than others. Brede Lærum and Pantea Khanshaghaghi took 50 minutes of their Wednesday shift to discuss this topic with 3D ADEPT Media. Trust me, it’s quite complicated to address all the points of this vast topic in just 50 minutes, but they are enough to confirm that a company is on a right track to deliver on its climate ambitions. And Equinor is.
With over 2 1 ,000 employees committed to providing affordable energy for societies worldwide, th e N o r we gian state – own e d multinational energy company is on a journey to net zero emissions through the optimisation of its oil and gas portfolio as well as the development of growth in renewables and development of low-carbon value chain in carbon capture and hydrogen.
With political pressure and the level of regulations that are rising around climate change, the Stavanger headquartered company – just like fellow organizations in the field – is continuously integrating sustainability concepts to understand the effects of its own actions, but also to measure them in order to achieve its net zero emission goals.
“There are two main areas that energy companies look into, when it comes to climate change and sustainability. The first one is the CO2 emissions from producing oil and gas – and we are working hard to reduce that as much as possible – and the second one is reducing the footprint for the product that is being used around the world. This second challenge makes it crucial to address the ‘carbon removal project’. We are actually developing a solution to capture the carbon and send it back into a place where there will be no risk of seeing it again”, Lærum told 3D ADEPT Media.
For Equinor and all other organisations that can play a role in climate change, overcoming these challenges requires to take into account multiple fronts including manufacturing and that’s exactly why Brede Lærum and Pantea Khanshaghaghi were the right spokespersons for this topic.
Indeed, Lærum is Head of the Additive Manufacturing Centre of Excellence at Equinor, Chairman of the Fieldmade Digital Inventory Project and Chairman of the international network «AM Energy». Khanshaghaghi on the other hand, is the project leader in Business development, responsible for sustainability through Additive Manufacturing at Equinor.
From an additive manufacturing perspective, “we are looking into the CO2 emissions related to our procurement process, when we purchase equipment, goods and other products. This third area has a huge potential when it comes to reducing the consumption of raw materials and the corresponding energy consumption and CO2 emissions. Additive Manufacturing is perfectly fitted into a circular economy model” he adds.
“The oil and gas industry has several challenges to address but the whole world has a bigger challenge: the materials we are consuming. Hundreds of billions of tons of materials are consumed worldwide and we are not able to recycle them (We recycle less than 9% of them). This major concern raises several issues including pollution – because at least 1% of pollution comes from manufacturing (Manufacturing is responsible for 31% of global emission -which is the highest among different sectors)– and the security of supplies that the pandemic has highlighted, especially in Europe. Additive Manufacturing is uniquely positioned to play a role in these three main challenges. For example, when we say that we are going to achieve less waste and in all different phases of the manufacturing process, we can do so because the technology itself allows for less use of materials. Transitioning from conventional manufacturing processes to AM processes is just a first step in the actions that can be implemented.
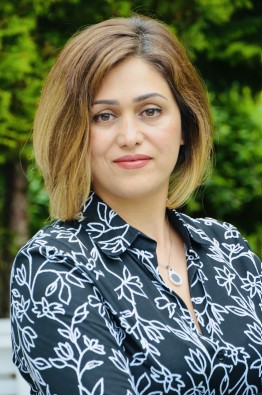
Indeed, mining those materials is another problem. This means that, each production usually requires us to manufacture a lot of products in order to be commercially visible. We have to send these products to subsidiaries or partners across the world but also keep some of these products in case we would need them later. All of this requires a lot of materials, transportation, and resources that could be saved for other purposes. That’s the reason why, at Equinor especially, we are looking to transit into a digital world where we will not need to produce a lot and transport a lot. We would avoid this “overuse” of materials and send the products just when and where we will need them. By doing so, we are already able to cut CO2 emissions at multiple levels. On top of that, we are saving lots of time and money as a producer and for the end-user”, Khanshaghaghi outlines, speaking of these three main areas and why AM is a pivotal manufacturing tool for each of them.
As Khanshaghaghi explained the importance of these three scopes/ areas for an energy company (production of emissions, products used around the world as well as purchase & consumption of goods), she laid emphasis on the importance of the latter for AM professionals.
Indeed, one can extend the lifetime of equipment either by using AM to repair, by getting obsolete parts using 3D printing or by avoiding replacing certain components. “In the latter case, we would not need to take our raw materials, we don’t have to consume more energy to produce those parts, and therefore no CO2 emissions will be produced. So, by reducing the consumption of goods, we can actually quite contribute to the reduction of CO2 emissions. But that remains a relatively new area”, she said.
Additive Manufacturing, a tool to translate net zero emission goals into practice
First signs of AM activities have been seen at Equinor in 2016. According to the head of AM at the Centre of Excellence, it all started as a research activity where the team ambitioned to discover if they can effectively trust AM and what would be the main benefits for Equinor. At present, the AM unit integrates about 34 polymer 3D printers (FDM & SLS) that serve an education purpose.
“We do not have an ambition to be a parts producer. We want the suppliers to continue producing parts, now using AM. That’s the reason why, although we keep a strong focus on metal AM technologies in our various activities, we do not invest in such technologies for our in-house activities. That being said, there are seven different and recognized AM technologies within this industry. Our activities and tangible examples of application explored so far, reveal a great potential for Powder bed fusion, DED aka LMD, and wire-arc AM”, the Head of AM emphasizes.
Although AM in its essence, is a sustainable method – since you build from nothing as opposed to starting with a large lump of metal and reduce it gradually; with AM you can optimize the parts through topology optimisation and reduce raw materials -, there are no confirmed data that may help state which metal AM process is more sustainable today. However, comparative analysis of how certain applications are produced can help appreciate the potential of a given AM technology and trust even better the sustainability strategy of a given company. To illustrate this statement, Lærum took the example of the comparative life cycle assessment (LCA)* of a cooling fan – produced using AM and via conventional manufacturing (CM) processes. In this specific case, the carbon footprint of the electric motor – of the cooling fan produced via the two types of manufacturing processes – has been assessed with regards to its Global Warning Potential (GWP)* over 100 years.
Lærum explained that the supplier told them to replace the whole electric motor (weighing 1 and half tons) because the (obsolete) fan was broken. They calculated CO2 emissions related to the replacement of a new part. The CO2 emissions for producing this fan locally were 3.8kg but replacing the whole pump – as initially indicated – would have caused them to produce 4 500 kg of CO2 emissions.
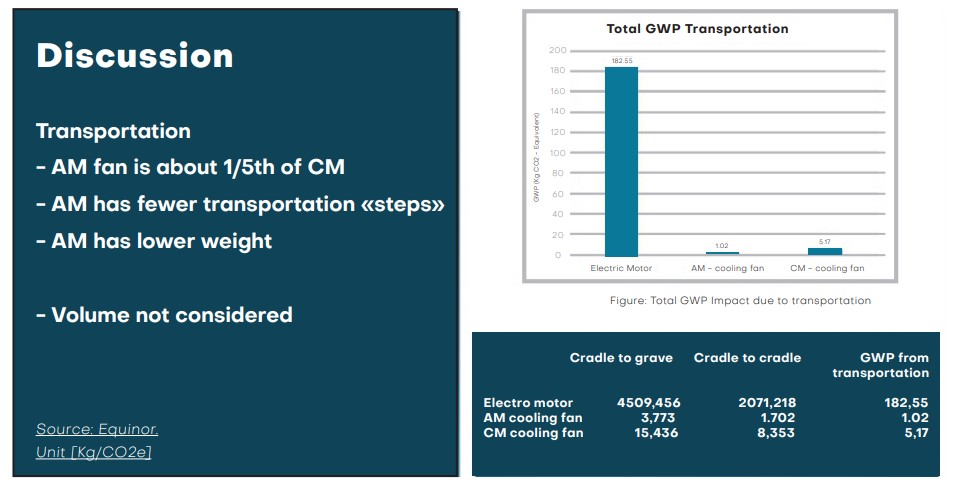
In addition, the expert points out that the use of recycling of raw material reduces the GWP from 45% to 54% in the three respective scenarios.
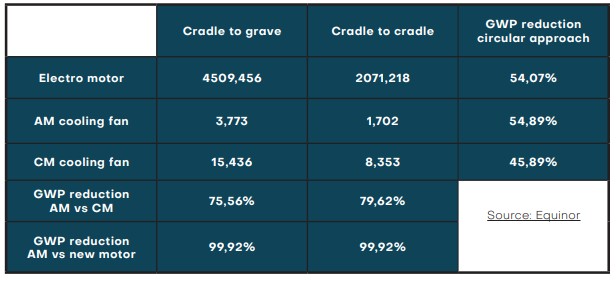
“It’s a completely new scale. By extending the lifetime of that motor, we avoided 4 500 kg of CO2 emissions related to the production of a new pump. If you add that to all the different equipment we are considering to replace, this will add to a rather large sum of CO2 every year. It’s a really new era to look into when it comes to CO2 emissions. The whole industry should look into this “scope n°3” of emissions”, Lærum adds. As the expert explains, taking the example of the broken fan, looking at this “scope n°3” requires to look at the country where the components are being produced and where the raw components are being taken out. Furthermore, this production using AM refocuses the debate on the importance of circular economy and its ultimate purpose which goes beyond recycling.
“The main purpose of circular economy is to design the waste out and that’s exactly what AM does. First of all, we are using less materials, and thereafter, when we design the new part, we do so in a way that it will be recycled – or at least have a longer lifetime”, Khanshaghaghi notes. “By changing our behaviour and our way of dealing with all the equipment, we can of course contribute to reduce CO2 emissions”, the Head of AM completes.
A fight that requires other partners
It’s one thing to know the process and identify the steps that one should take in this fight for climate change, it’s another one to have the right partners to do so.
The latest partnership where the company is involved alongside independent technology research institute SINTEF, and gas company Gassco , is a project from Kongsberg Ferrotech, a Norwegian robotics company, that designs and manufactures subsea robots for the oil and gas industry. Together, the three companies will develop 3D printing technologies for subsea equipment repair and maintenance. Inspection, maintenance and repair (IMR) robots are pivotal to the success of this project as they can achieve repairs and modifications in a dry environment while being completely submerged. So far, the teams have already completed deep water testing on the composite repair in the Trondheim Fjord in Norway.
According to the sustainability expert, the concept of circular economy will once more play a key role here since AM will be used to repair instead of replacing. “That’s kind of designing the waste out again”, she reminds us. “From a manufacturing standpoint for instance, they will look at the way they can recycle all the metals they have. Amid the companies that will help us in this process, there is f3nice that recycles metal scraps into atomized powder.”
While AM is another great tool that illustrates the circular economy process in production, Khanshaghaghi highlights the importance for organizations to think about a better energy mix for that. “For instance, it is not interesting to use fossil fuels heavily in a country that is already planning to use renewable energies”, she notes. In the same vein, Equinor’s collaborators also note the enriching experience they have through collaborations with startups.
In addition to f3nice mentioned above, Lærum mentioned Fieldmade, a tech startup that ambitions to change the linear supply chain into a network-based approach. The startup has partnered with Siemens Energy, TotalEnergies and to develop an on-demand 3D printing ecosystem for parts supply.
“Together, we are demonstrating that AM is contributing to sustainability throughout the whole circle of circular economy. In this specific case, the technology serves as a catalyst for the new digital ecosystem that we are building with Fieldmade and Siemens Energy. In the long-run, this platform will be a commercial product – promoted by Fieldmade – with two main functions: connect all operators and all suppliers in a huge digital network for spare parts. Secondly, all these suppliers could promote their own digital parts into the network so that the digital inventory will be driven by the ecosystem – not purchased by the operator-. Although AM is an important enabler for the digital inventory the main point is on-demand production of parts, using AM, CNC machining or any other fast, reliable and repeatable manufacturing method. The plan is to gradually reduce the physical inventory while building the content of the digital inventory”, Lærum explains.
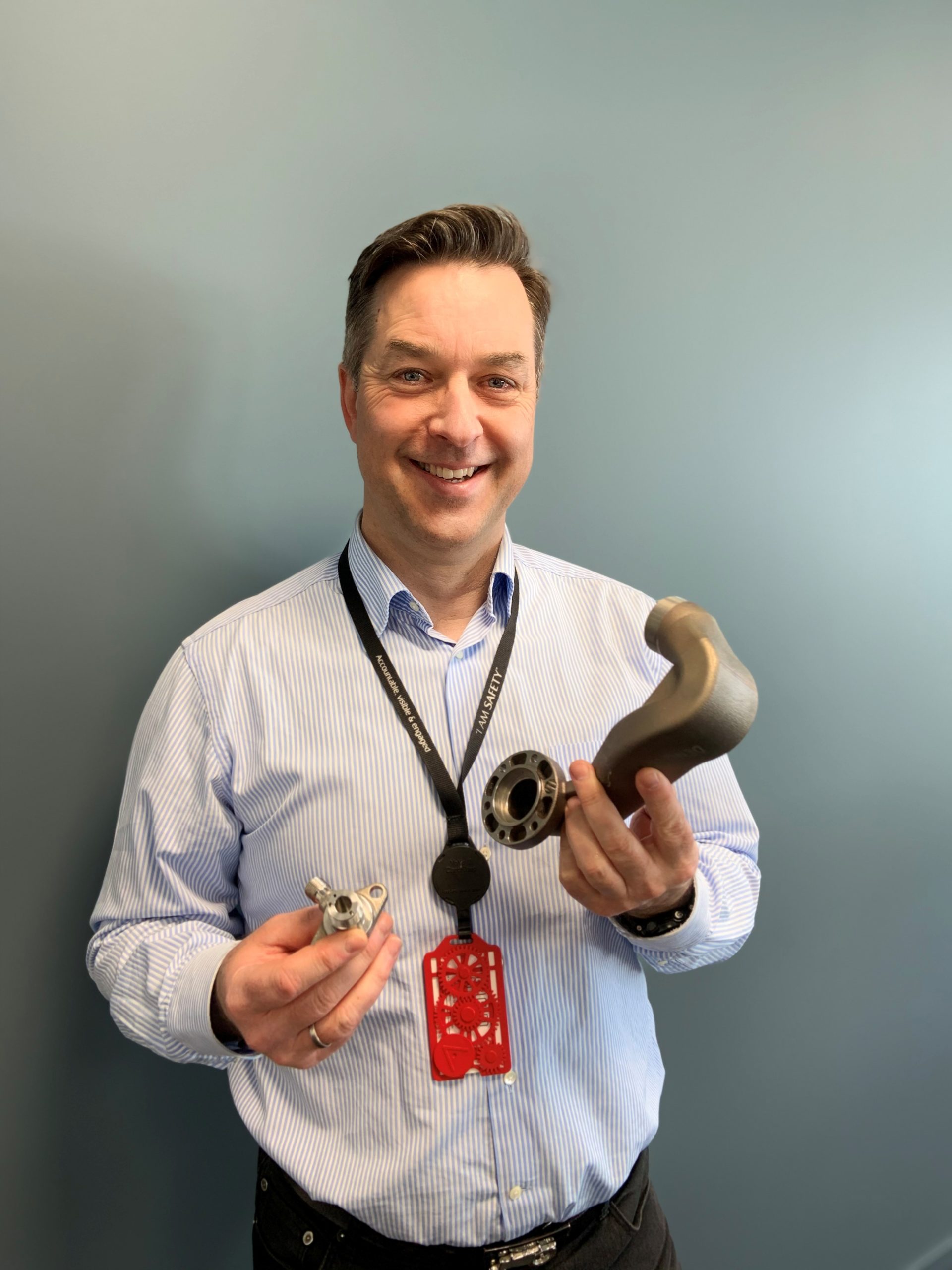
And now…?
Most energy companies that are challenged on carbon topics used to reflect on how they should grow in renewables, develop carbon capture and storage solutions or even produce less oil and gas over time. All of this is totally understandable when we look at how the society wants them to address this issue.
From a practical standpoint, this conversation with Equinor reveals that organizations should no longer only look at AM as the beautiful technology that will produce complex parts. It is possible to get tangible results regarding sustainability if we explore the use of Additive Manufacturing when developing digital solutions across the whole value chain, such as maintenance, production optimization and supply chain management. Now, imagine how far they can go if they add to 3D printing, data science and artificial intelligence.
With the goal of scaling digital solutions across its global portfolio faster than expected, and thus contributing to increased production as well as reducing maintenance, drilling and facility cost, Equinor recently increased its 2025 improvement ambition by 50%, from 2 to 3 billion USD. Added to that the aforementioned examples and the partners by its side? Their efforts to become a net-zero energy company will definitely pay off by 2050.
This exclusive feature has first been published in the 2021 September/October edition of 3D ADEPT Mag (PP 22-25). Remember, you can post free of charge job opportunities in the AM Industry on 3D ADEPT Media or look for a job via our job board. Make sure to follow us on our social networks and subscribe to our weekly newsletter : Facebook, Twitter, LinkedIn & Instagram ! If you want to be featured in the next issue of our digital magazine or if you hear a story that needs to be heard, make sure to send it to contact@3dadept.com