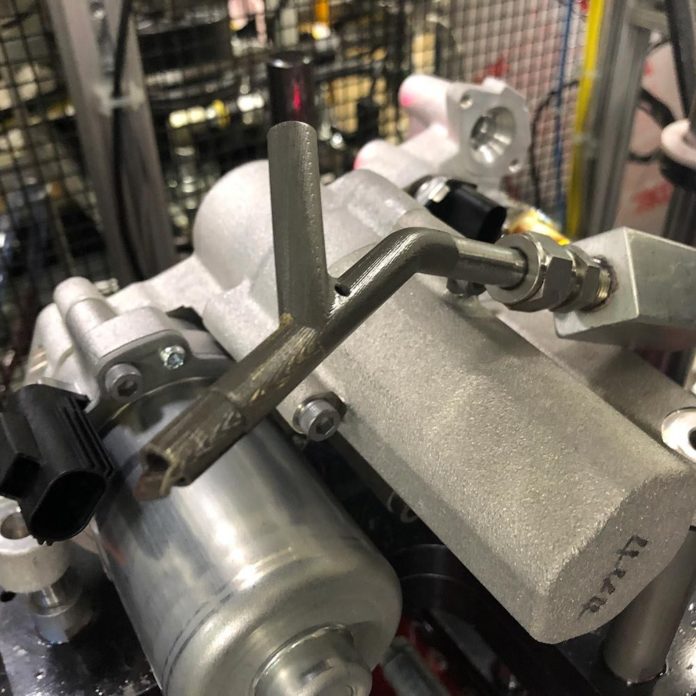
La société de gestion d’énergie Eaton a annoncé que son Vehicle Group lance un nouveau programme d’impression 3D métal dans le cadre de sa stratégie Industrie 4.0 visant à réduire le temps de développement et à gagner en efficacité.
Nous avons entendu parler d’Eaton pour la première fois il y a trois ans, lorsque la société a signé un accord commercial avec Bremen Castings, Inc. (BCI) afin d’accélérer le développement de nouveaux produits pour les clients du secteur de l’hydraulique. Au fil du temps, la société a amélioré son expertise en matière de FA et est devenue un fournisseur de pièces imprimées en 3D pour l’aérospatiale.
À ce jour, Eaton produit des montages de haute qualité, des dispositifs de sécurité, des pinces d’automatisation pour l’assemblage et la manutention, et des composants de maintenance nécessitant un remplacement. Le développement de prototypes suit la même stratégie pour permettre des essais de développement de produits plus rapides et améliorer l’efficacité.
Améliorer le rendement et l’efficacité
Pour accélérer le processus de conception, des scanners sont utilisés pour créer des modèles 3D des composants existants. Ce processus permet de rétroconcevoir les composants afin de mieux exploiter les capacités d’impression 3D, notamment en modifiant la conception des composants pour utiliser moins de matériaux, en ajoutant différents éléments de topographie ou en consolidant plusieurs composants en une seule pièce.
Alors qu’un nombre croissant d’imprimantes 3D sont déployées dans le monde entier, le Vehicle Group d’Eaton a réalisé d’autres améliorations opérationnelles, notamment une réduction des délais et des économies de coûts.
La technologie d’impression 3D n’ajoute du matériau que là où il est nécessaire et permet de développer des conceptions plus avancées. Ensemble, ces deux facteurs permettent de réduire le nombre d’opérations de post-traitement nécessaires tout en diminuant le coût des matériaux.
Un regard plus approfondi sur l’impression 3D
Le processus d’impression de pièces et de composants métalliques commence par l’utilisation de poudre de métal stockée dans une tige et maintenue par de la cire et un liant polymère. Comme pour l’extrusion, le métal est fondu, et l’imprimante 3D commence à ajouter couche après couche, en fonction de ses schémas programmés.
Une fois le processus d’impression terminé, la pièce ou le composant est passé dans un bain chimique pour éliminer la plus grande partie du liant polymère. La pièce passe ensuite dans un four pour enlever la cire et le polymère restants, et pour fusionner le matériau métallique dans une structure à haute densité. En fonction de l’usage auquel est destinée la pièce ou le composant imprimé et du matériau avec lequel il a été imprimé, un traitement thermique supplémentaire peut être effectué pour augmenter encore la résistance de la pièce.
Le délai total pour faire imprimer un composant dépend de plusieurs critères, dont la taille et la complexité de la pièce. Selon la conception de la pièce ou du composant et les tolérances requises, il peut également subir un post-traitement. L’opération de reliure et le traitement thermique sont effectués par lots, plusieurs composants différents passant ensemble par ces processus pendant que les composants suivants sont imprimés. Bien que l’imprimante, le décolletage et le four fonctionnent en boucle intégrée, il est possible d’augmenter le nombre d’imprimantes sans avoir à dupliquer le décolletage ou le four.
N’oubliez pas que vous pouvez poster gratuitement les offres d’emploi de l’industrie de la FA sur 3D ADEPT Media ou rechercher un emploi via notre tableau d’offres d’emploi. N’hésitez pas à nous suivre sur nos réseaux sociaux et à vous inscrire à notre newsletter hebdomadaire : Facebook, Twitter, LinkedIn & Instagram ! Si vous avez une innovation à partager pour le prochain numéro de notre magazine numérique ou si vous avez un article à faire connaître, n’hésitez pas à nous envoyer un email à contact@3dadept.com.