Built off the best features of its predecessor, the Studio System 2 aims to provide the easiest way to 3D print complex, high-performance metal parts in low volumes for pre-production and end-use applications – in offices.
The new metal 3D printer is an upgraded version of the Studio System metal 3D printer. It distinguishes itself from the other by a two-step solution that does not require the need for a solvent debind phase anymore.
The removal of solvents has been made possible thanks to new material formulations that allow parts to be transferred directly from the printer into the furnace. According to the manufacturer, the two-step process delivers a nearly hands-free experience that also reduces consumables usage and overall system footprint.
Stick to its promise to deliver a wide range of complex geometries, Desktop Metal integrates a heated build chamber in the new 3D printer as well as print profiles that allows for enhanced surface finish right after the furnace process.
The manufacturer also ensures the production of strong parts due to new isotropic TMPS infill. Indeed, vacuum sintering in the Desktop Metal furnace can reach temperatures of up to 1400°C, which is interesting for the fabrication of parts with mechanical properties that are similar to castings- a perfect requirement for the Metal Powder Industries Federation (MPIF) standards.
As far as materials are concerned, the Studio System 2 processes 316L stainless steel, a corrosion resistant and general-purpose material used for the production of parts in various applications such as manifolds, nozzles, brackets, latches, and jewelry.
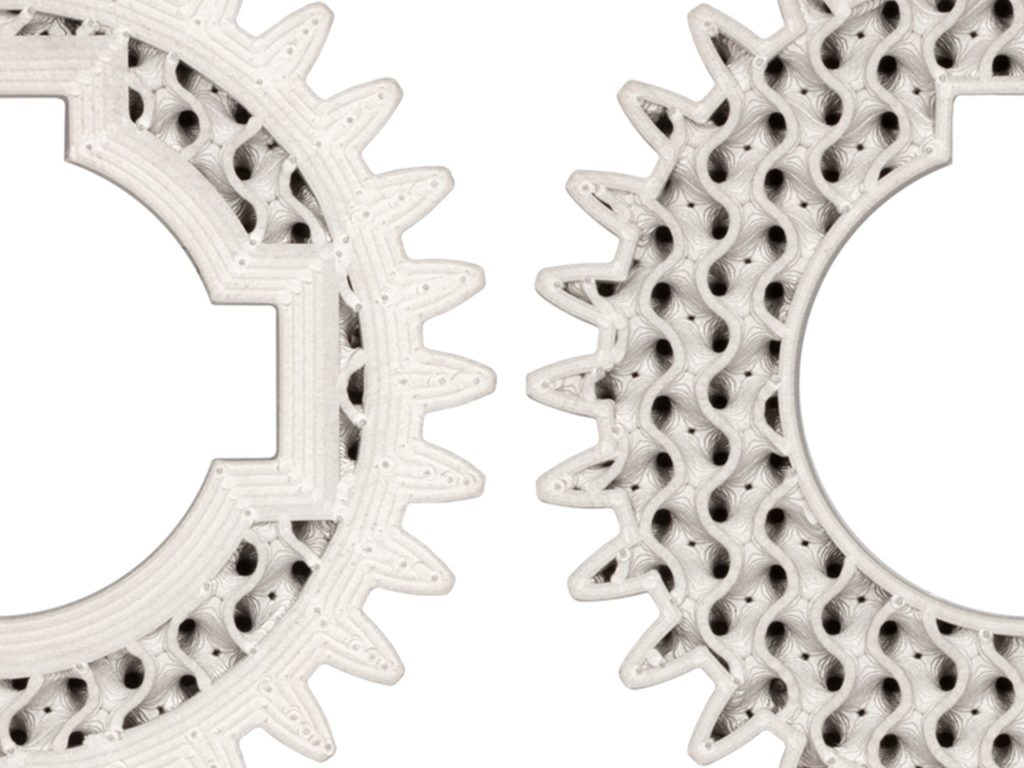
A wide range of materials are currently being developed by the manufacturer. They should be unveiled throughout 2021. In addition, the Studio System 2 will be backwards-compatible through the use of the debinder, with all materials previously supported by the Studio System, including 17-4PH stainless steel, 4140 low alloy steel, H13 tool steel, and Copper.
As for the software controlled workflow, the manufacturer’s Fabricate™ software features new, default print profiles tailored to the Studio System 2 process that simplify build preparation while still providing users access to more than 90 customizable print settings. Fabricate also generates Separable Support structures with strategic splits to avoid locking during post-processing and fully automates thermal debind and sintering cycles.
“As additive manufacturing adoption advances worldwide, Desktop Metal continues to drive innovations that enable the technology to more effectively compete with conventional manufacturing processes,” said Ric Fulop, CEO and co-founder of Desktop Metal. “Our next-generation Studio System 2 takes the best features of the original Studio System+ and significantly improves upon them, delivering higher quality end-use metal parts through a more streamlined and accessible process, and within an even smaller footprint.”
Remember, you can post job opportunities in the AM Industry on 3D ADEPT Media free of charge or look for a job via our job board. Make sure to follow us on our social networks and subscribe to our weekly newsletter : Facebook, Twitter, LinkedIn & Instagram ! If you want to be featured in the next issue of our digital magazine or if you hear a story that needs to be heard, make sure to send it to contact@3dadept.com