When Additive Manufacturing comes to composites fabrication, we did not expect this combination to work and lead to the development of some niche yet interesting applications for the industry. In their latest report, SmarTech Analysis announced this market segment would surpass $9 Billion in 2028. What explains the host of new opportunities for the composites industry? More importantly, what drives this market segment?
This article aims to give a state of the art of composites additive manufacturing and highlights key takeaways companies should keep in mind while taking their first steps into this market segment. To address this issue, we’ve invited two experts: Anisoprint and SABIC.
Anisoprint is one of the pioneers in Continuous fiber 3D printing. The Russian manufacturer develops composite fiber co-extrusion 3D printers that can fabricate high-strength reinforced parts. With a decade of academic and industrial experience in design and optimization of composite materials and structures, Fedor Antonov, the company’s founder and CEO, shared his thoughts on this niche technology.
Next to Anisoprint, is SABIC. This expert in the chemical industry delivers value by providing materials at various points throughout the global additive manufacturing value chain. Kim Ly, Lead Scientist, Application Technology at SABIC’s Specialties Business answered our questions as part of this feature.
Seven years ago, when we witnessed the launch of Markforged’s 3D printer that could process polymer structures with continuous carbon fiber reinforcement, any article on the topic would have taken one or two pages. Today, with the development of new materials and the entrance of new comers, this same topic can fill an entire magazine.
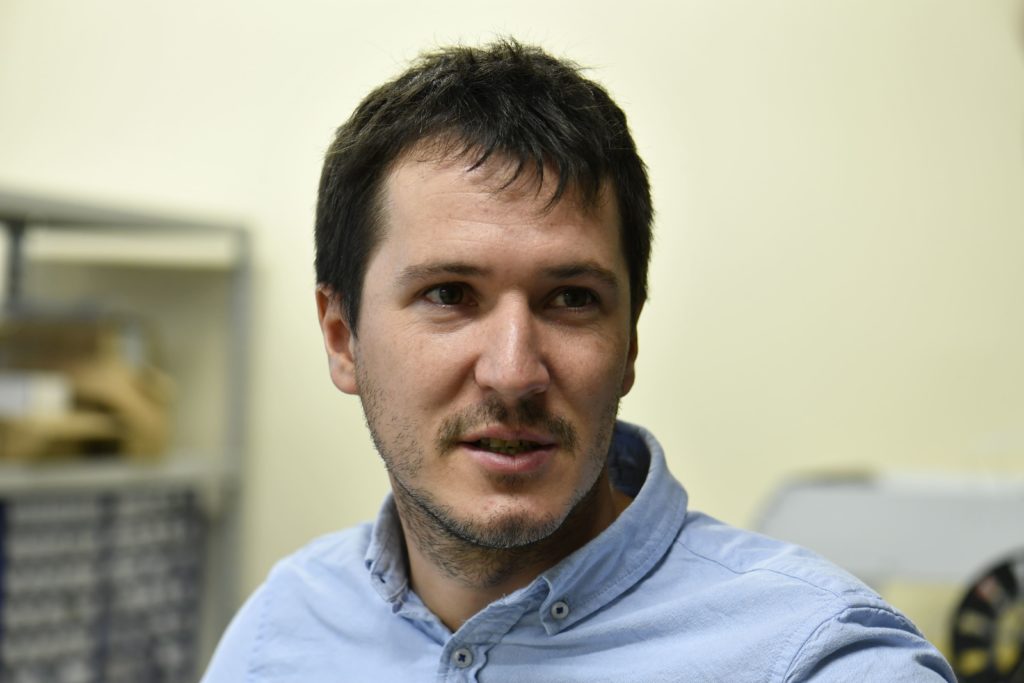
For Antonov, Composite 3D Printing is less widespread compared to other AM technologies because “it is one of the youngest branches of AM technologies. New players are entering the market every year and the number of applications and use cases is growing rapidly”. “I’m pretty sure that in 5-10 years composite 3D printing will be one of the biggest things in AM”, Antonov said.
Why does composites additive manufacturing make sense today ?
We tend to believe that the “virtuous cycle of the 3D Printing industry” drives this change. As per the words of Shane Fox, Founder of Link3D, “the more designers design products, the more applications we will have. The more applications there are, the more materials will be developed, and the more printers will evolve or be introduced to the market“.
This virtuous cycle is a first response to the evolution of composites additive manufacturing. If we dig a little bit deeper, we realize that this virtuous cycle also draws attention on the challenges of traditional composite-manufacturing processes and how additive manufacturing might be uniquely positioned to address them.
Indeed, traditional composite-manufacturing technologies often require hand lay-ups and post-processing stages such as autoclaving and vacuum-molding. Not only these stages are expensive with standard plastics or metals, but they should be performed by a higher-skilled workforce.
Furthermore, as designers need stronger materials that can be processed via AM, there is a need to explore other manufacturing opportunities. Composites materials might therefore become an interesting alternative where metals are not always sufficiently lightweight enough.
Speaking of the way the use of composites differs from conventional manufacturing processes & additive manufacturing processes, Antonov stated:
“There is not just one conventional composite manufacturing process. And most of them are also additive by definition (the materials is added to create an object, not removed). Moreover, Automated Fiber Placement (AFP) or Tape Laying (ATL) technologies, that are successfully used for decades to produce high performance composite parts, could be called 3D printing. Some of the new composite 3D-printing companies are offering technologies that are very similar to AFP or ATL, and some of the old AFP/ATL providers now start calling their machines 3D printers. There are other composite manufacturing technologies, such as hand layup, filament winding, pultrusion, resin transfer molding and many others, that are quite different one from another, but all of them are additive. What really makes the difference, is not the fact that these technologies are additive, but rather higher level of automation, digitalization and customization of the manufacturing process. Most of the conventional technologies are multi-stage processes that require lot of hand and paper work, and have many limitations. The ideal composite manufacturing technology of the future (anisoprinting) is a fully automated, single-stage, digital manufacturing process that imposes no limitations on the shape and internal structure of the part”.
This need for hand lay-ups, the expensive curing equipment and the need for stronger materials are a few areas where AM brings tangible solutions.
The use of composite materials in Additive Manufacturing
First, composite materials are the combination of two or more materials with different physical and chemical properties. To develop most composites, material experts usually take one material (the matrix) and surround it with fibres or fragments of a stronger material (the reinforcement).
Composite materials are meant to perform a certain job, for instance to deliver stronger or lighter parts, to deliver parts that can withstand electricity or to improve strength and stiffness. In a nutshell, they always improve the properties of their base materials and are leveraged in various applications.
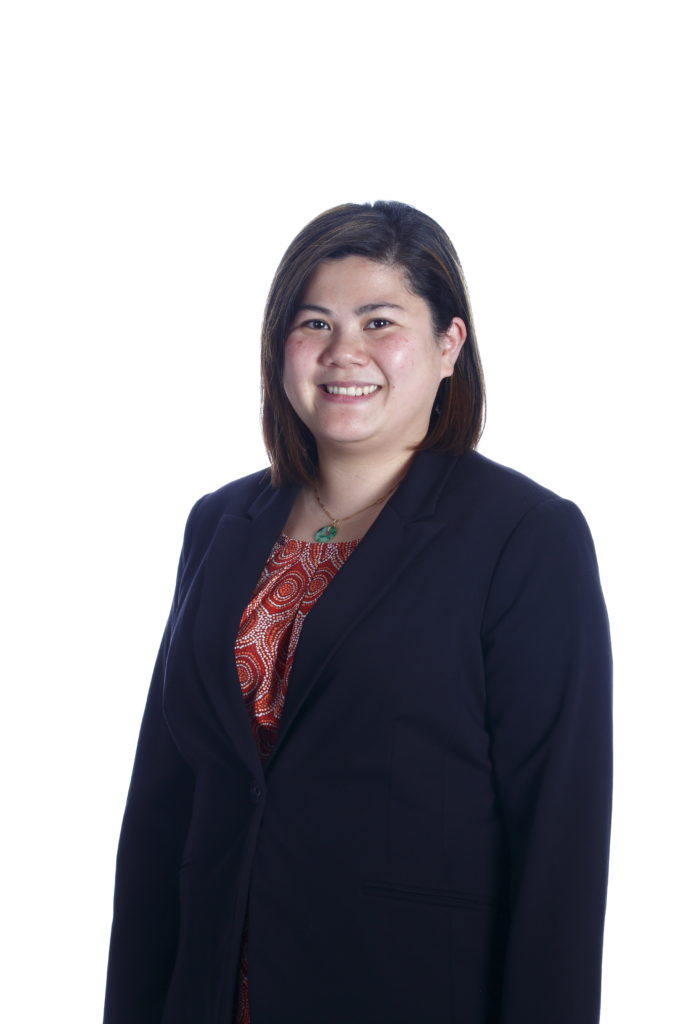
Composite materials can be found in various forms. Taking SABIC’s materials as an example, Kim Ly explained that “glass- and carbon-reinforced polymer pelletized compounds can be used in Large Format Additive Manufacturing (LFAM), also known as Fused Granular Fabrication or pellet extrusion Additive Manufacturing”. However, these materials can be found in many different forms as the way they are utilized also depends on the type of AM technology that processes them. Speaking of LFAM for instance, Ly explained that this technology is commonly associated with print envelopes of 1 cubic meter and larger and pellet feed rates ranging from 5-250 kg/hr.
Anyway, SABIC’s “primary base polymers include ABS (Acrylonitrile-Butadiene-Styrene), PC (general purpose and high-heat polycarbonate), PPE (NORYL™ polyphenylene ether resin), and PEI (ULTEM™ polyetherimide resin), as well as a new compound based on our FST PC for enhanced performance with respect to low flame, smoke and toxicity”.
Speaking of challenges operators can encounter at the materials level, Ly continued:
“We have learned that many early LFAM adopters have less experience processing polymers than our traditional customer base in injection moulding, particularly in the areas of material selection and Design for Additive Manufacturing. In addition, understanding best practices in material handling, drying, and processing are critical since there may be differences in the behaviour of grades, even within the same polymer family. For that reason, SABIC also provides support including fundamental polymer education when needed. Further, since we use our Large Format printer to screen compounds under development, we are very aware of the potential design and processing challenges that can arise, so we offer to review proposed print configurations and can be present either in person or online during first prints to help diagnose any issues. This can help accelerate the learning curve for our customers”.
Chopped vs Continuous fibres
As mentioned before, most composites are formed with one main material (the matrix) which is strengthened with fibres of fragments of a stronger material. It should be noted that two reinforcement types of fibre are compatible with AM technology: chopped and continuous.
With chopped fibre, small strands (< 1 mm in length) are embedded into the polymer material. The percentage of fibre used and the base thermoplastic will influence the strength of the final part.
Continuous fibre on the other hand, requires a mix of long strands of fibre and a thermoplastic during the printing process. This thermoplastic can be PLA, ABS, Nylon, PETG and PEEK. Such type of parts is usually very light and strong as metal.
It’s easy to appreciate the capabilities of those two types of fibres when they are processed on a specific AM technology.
“Printers built for LFAM utilize compounds based on chopped fibre to take advantage of the strength properties along with widespread availability and lower cost of pellets as compared to filaments. Use of chopped fibre provides distributed reinforcement throughout the matrix of the print. Printers that incorporate continuous fibre into a matrix of molten polymer have more recently been introduced and offer additional functional capabilities; however, use of continuous fibre may have some limitations on design and full incorporation into the matrix, particularly in gantry-based AM systems” SABIC’s speaker pointed out.
In the industry, additive manufacturing of chopped fibre composites would find more applications than continuous fibre due to this length of strands, which is less complex to process than AM of continuous fibre.
The key focus on Carbon fibre
Carbon fibre is one of the most widely used type of fibre used on the 3D printing market, alongside fibreglass and Kevlar. For the two experts, two main arguments explain this excessive and growing use of carbon fibre: performance and applications.
For Anisoprint’s CEO, it is a matter of performance. “As the main UVP (Unique Value Proposition) of composite 3D printing is high performance (high strength, stiffness and low weight) it is logical to use the most high performance components. When the price topics will become more important with the maturity of the technology, probably, other types of fibers (such as glass, basalt, aramid or natural fibers) will become more popular, but everyone will find its own niche”, Antonov notes.
Even though she recognizes that the primary use cases to date, are seen with carbon-fibre and glass-fibre, Ly also lays emphasis on the expensive cost of carbon-fibre-reinforced compounds as compared to glass-fibre compounds. However, despite this expensive cost, operators are attracted by the high strength, modulus, thermal conductivity and the lower coefficient of thermal expansion that carbon fibre delivers, properties that are “all highly critical for tooling applications”. Not to mention that carbon fibre compounds are also less prone to warpage, a key advantage for robust manufacturing.
Distinct differences remain, between printing carbon fiber and printing carbon fiber-filled thermoplastics, as well as continuously laying carbon fiber as part of a 3D printed geometry. This brings us to our next question: what type of AM technologies can process composite materials?
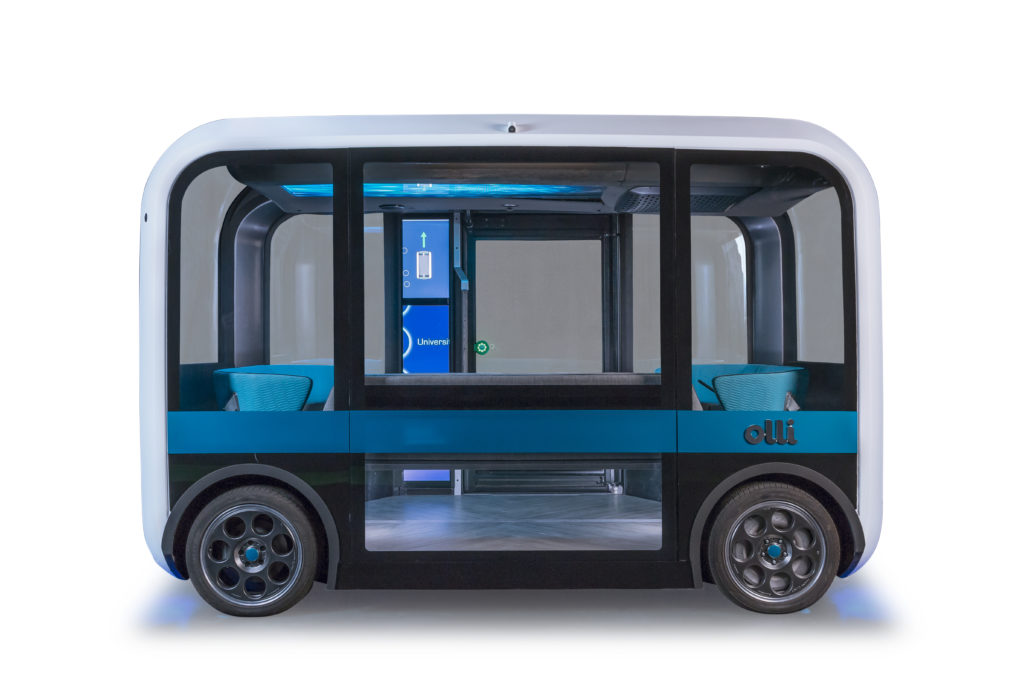
Materials vs AM technologies
A few number of manufacturers position themselves on the composites 3D printing market. Some of them have made this technology their core business while others provide this technology as part of a large production technologies portfolio. There are for instance:
Anisoprint, +Lab/moi composites, 3D Fortify, 3DXTech, Advanc3D Materials, Arevo Labs, CEAD Group, Cincinnati Inc., Continuous Composites 3D, CRP Group, EOS, Impossible Objects, Ingersoll, Markforged, Roboze, Ricoh, Stratasys, Thermwood, Desktop Metal and Fortify.
As composite materials are available in various forms, their AM technologies can be based on a liquid or filament process.
Furthermore, as composite materials require a dedicated approach, existing technologies that were not developed with the goal of processing composites, cannot process them. Antonov did not take into account short fibre reinforce composites here, as “they do not offer a different value proposition”.
Nevertheless, “most of the composite AM are material extrusion based, or lamination based. At the moment it’s quite hard to categorize them, as every vendor has its own process, each of which has its pros and cons” Anisoprint’s CEO completed.
Anisoprint’s continuous fibre 3D printing technology stands out from the crowd thanks to two inputs: the first one is designed for reinforcing material (fibre) and the other one is meant for the matrix material (plastic). The two materials are mixed inside the print head and are extruded through a single nozzle.
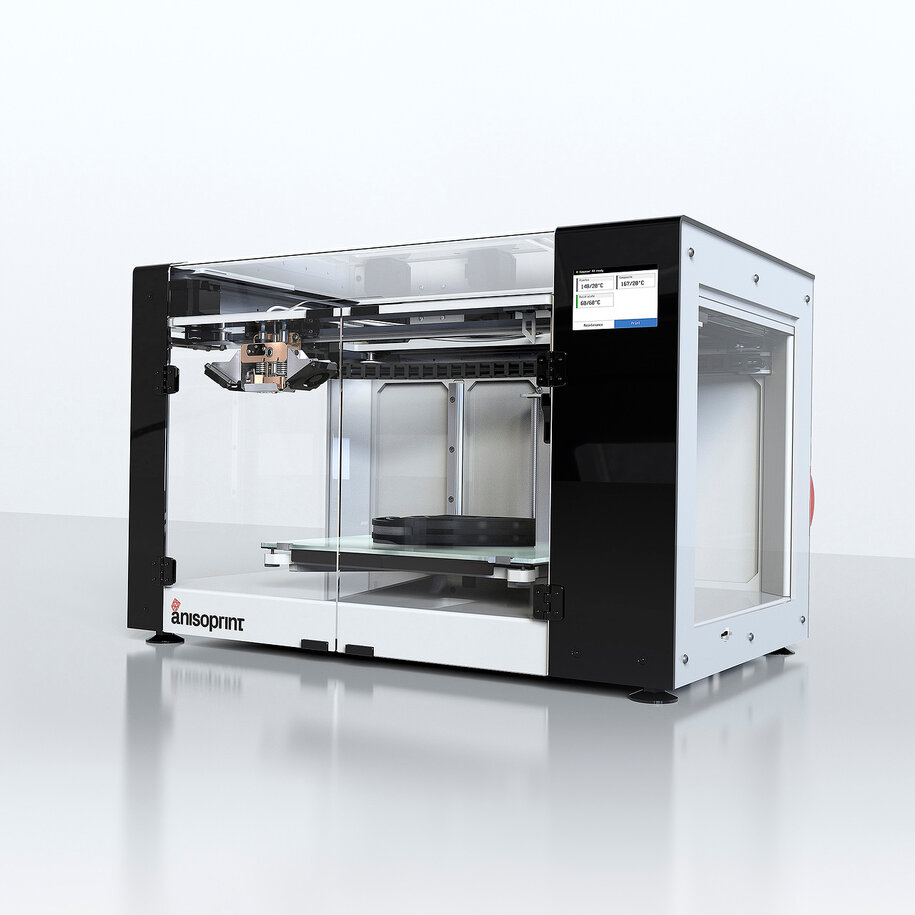
To comment on what makes their technology outstanding, Antonov states: “in most of the other extrusion-based continuous fiber 3D printing processes, the fiber is preliminary impregnated with plastic, and the print head has one input (for fiber, impregnated with plastic) and one output (for the same, but plastic molten inside). The co-extrusion approach allows us to use different types of plastics as a matrix (binder) material, and this choice is made at the customer side, which is not possible with the pre-impregnation approach. And more important, with co-extrusion you can locally change the volume fraction of the fiber that allows for printing more complex structures such as lattices or using layers with variable thicknesses”.
Concluding Thoughts
As the AM market shifts away from the stereotype of rapid prototyping, an increasing focus is made on functionality and materials are not exempt from such scrutiny. As far as composites 3D printing is concerned, this niche technology enables a multitude of applications in every field that requires high performance and lightweight parts.
The value proposition in creating large parts and tools in days rather than months includes speed-to-market, reduced development costs, and often increased revenue from faster sales.
“However, from the perspective of the material supplier, improvements in material quality and consistency continue to be a primary focus. Because prints can span hours or even days of run time, errors that may occur well into the printing cycle can result in material waste and highlights the need to minimize process fluctuation”. This is therefore the next area for improvement of AM specialists.
This dossier has first been published in the September-October issue of 3D ADEPT Mag.