Un large éventail de règles a été établi pour tirer avantage des procédés de fabrication conventionnels. La FA enfreint nombre de ces règles car elle introduit de nouvelles capacités qui ne sont pas compatibles avec la fabrication conventionnelle. L’une de ces règles consiste à déterminer si la fabrication d’une pièce est adaptée à la FA. Dans les lignes ci-dessous, Julien Cohen, ingénieur d’application chez 3DEO Inc, fabricant d’imprimantes 3D métal et bureau de service, répond à 3 questions qui méritent d’être prises en considération avant de choisir un procédé de fabrication additive métallique pour la production industrielle.
Soyons clairs : ce sujet aurait pu être abordé sous l’angle de l’impression 3D polymère, ou encore l’impression 3D liquide. La fascination pour la FA réside également dans son étrangeté. En discutant de ce sujet, Julien Cohen l’annonce clairement : « il existe de nombreuses façons d’aborder cette question ». Ses réponses sont basées sur son expérience chez 3DEO Inc. et dans de grandes entreprises avec des dizaines ou des centaines de milliers de SKU (unité de gestion des stocks). Elles seront combinées avec des recherches industrielles et des exemples d’application partagés par les entreprises.
Eléments à prendre en compte pour définir la candidature de la FA en tant que méthode de production à utiliser
Nous avons défini trois cadres différents qui peuvent être évalués avant de passer à la production en série en utilisant la FA.
1- Une base de données de composants et d’assemblages
Malgré les avantages significatifs de la FA, toutes les parties ne sont pas adaptées aux processus de la FA. L’étape la plus logique consisterait à dresser la liste des critères à prendre en compte pour définir les produits candidats aux applications de la FA.
En théorie, les paramètres de fabrication conventionnels qui sont généralement comparés aux paramètres de la FA et à l’expérience connexe sont d’abord filtrés par les ingénieurs concepteurs pour déterminer la première sélection de critères. Ensuite, une base de données de composants et d’assemblages est utilisée pour évaluer le potentiel de la FA et l’étiqueter selon les critères prédéterminés. Les mêmes critères de sélection sont généralement appliqués pour chaque nouvelle pièce d’assemblage et aboutissent à une décision modèle pour la candidature à la FA.
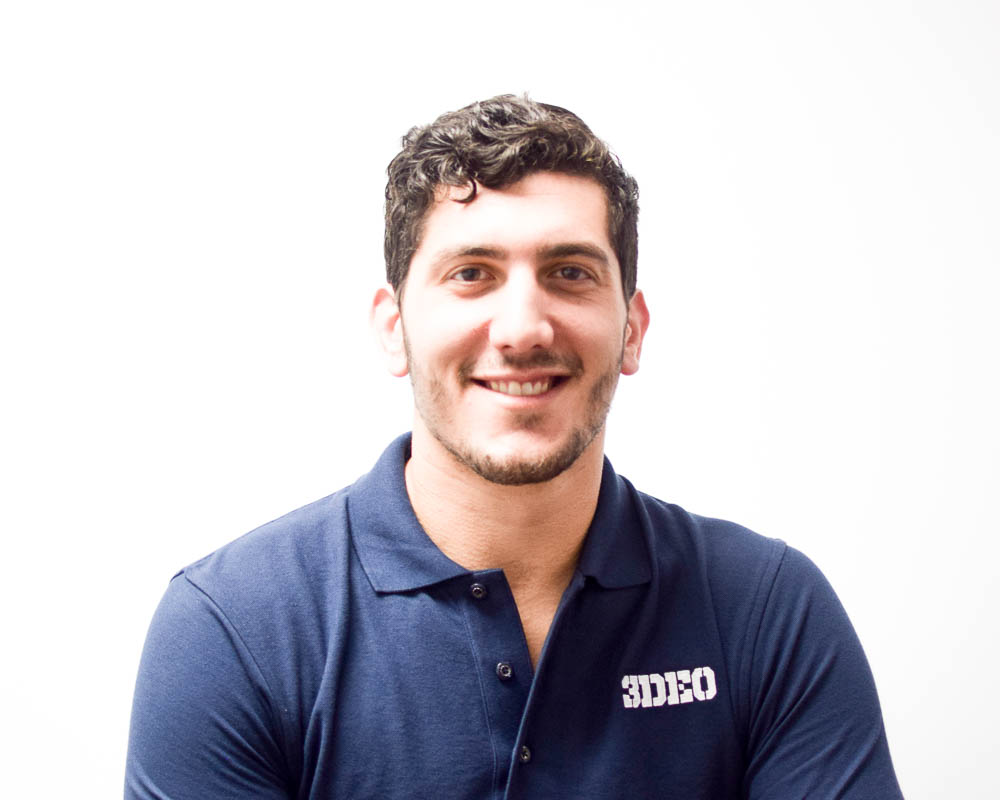
En pratique, « il n’existe pas de bibliothèque centrale contenant toutes les données et métadonnées nécessaires pour prendre cette décision. Par exemple, comment puis-je rechercher des pièces dans une gamme de taille spécifique, fabriquées en aluminium moulé à la cire perdue, dans une certaine fourchette de quantité annuelle ? Pour de nombreuses entreprises, le premier obstacle consiste à rendre ces données accessibles dans une base de données consultable.
Une fois que cet accès est disponible, le problème peut être abordé sous plusieurs angles. À mon avis, plutôt que de commencer par une liste de pièces et d’identifier quel processus de FA pourrait être utilisé pour chacune, il est plus efficace d’identifier un processus de FA potentiel et de filtrer ensuite les pièces en fonction des limites connues du processus. Ce flux de travail peut être divisé en quatre étapes :
- Choisir un processus de FA sur lequel se concentrer (L-PBF, 3DEO’s Intelligent Layering®, DED, Cold Spray, etc.)
- Disqualifier les pièces en utilisant les limitations absolues du processus (c’est-à-dire le volume de construction maximum, les matériaux disponibles, la capacité de taille des caractéristiques, la quantité annuelle)
- Classer les parties restantes en utilisant une sorte de mesure d’analyse de rentabilité (quelle application aurait le plus grand impact sur l’entreprise avec une réduction de 20% des coûts, une réduction de 20% du poids ou une mise sur le marché plus rapide ?)
- Réduire cette liste de classement à un nombre gérable d’opportunités de premier plan, et les examiner en profondeur pour déterminer celles qui méritent d’être poursuivies », explique Cohen
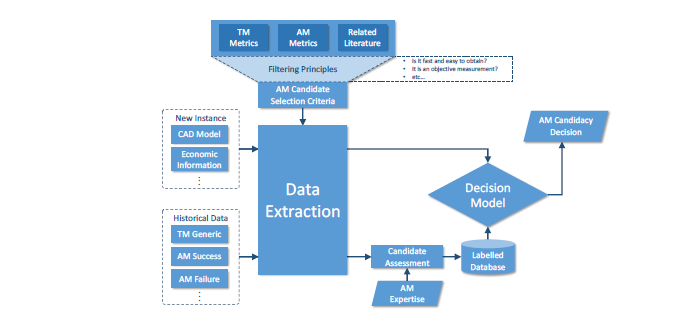
2- L’approche de l’analyse de la conception
Une autre méthodologie appliquée par les entreprises est l’analyse de la conception. Cette approche consiste à identifier les pièces où la FA pourrait être utilisée efficacement en tirant parti des capacités de la « conception pour la FA » (en anglais Design for AM = DfAM). Quatre critères sont souvent pris en considération dans ce processus : l’intégration des fonctions, la personnalisation, la légèreté de la conception ainsi que l’efficacité de l’exploitation.
L’intégration des fonctions peut être comprise comme la manière dont la conception sera intégrée dans l’ensemble de la structure. Ce critère vise à déterminer si un groupe de pièces peut être reconçu en une seule pièce, si la taille d’un produit peut être réduite tout en réalisant la même fonction, ou si sa production nécessitera moins de temps. Les ensembles complexes constitués de pièces à fonction unique répondent souvent à ce critère, car chacune d’entre elles peut être produite séparément pour réduire la complexité de la conception et de la fabrication.
D’un point de vue technologique, le critère de « personnalisation » implique de multiples variations de conception et des tailles de lot plus petites au niveau de la fabrication. Ce critère est l’avantage le plus reconnu de la FA : il permet de satisfaire les exigences des utilisateurs finaux des produits de consommation.
D’autre part, la conception légère va généralement de pair avec des économies de poids et de coûts de matériaux. Le défi de l’ingénieur concepteur consiste ici à améliorer les performances des pièces en réduisant leur poids et, au final, en diminuant les coûts et les matériaux. Pour y parvenir, les ingénieurs utilisent généralement des logiciels d’optimisation de la topologie, car ces outils augmentent la complexité géométrique de la pièce en plaçant le matériau aux endroits requis par la fonction.
Enfin, l’efficacité de l’opération consiste à explorer toutes les solutions innovantes qui peuvent améliorer l’efficacité de la pièce une fois qu’elle sera utilisée. Ce critère amène souvent les ingénieurs à explorer les moyens d’améliorer la durée de vie du produit, de réduire les coûts d’exploitation, d’améliorer la conversion d’énergie et bien d’autres choses encore.
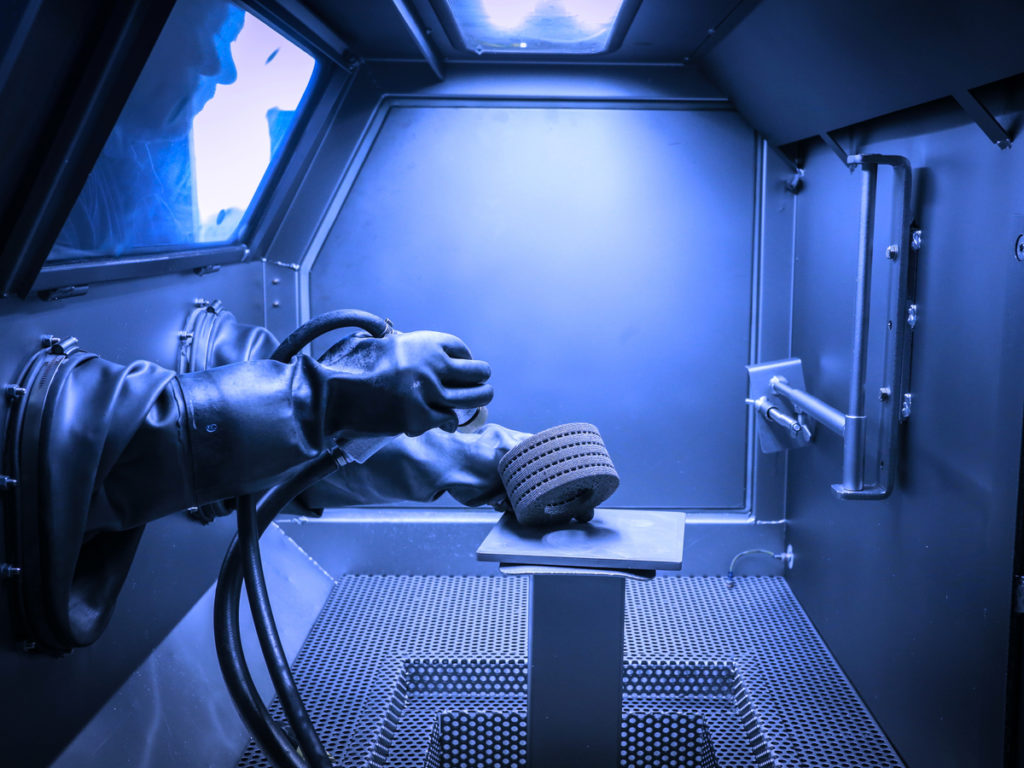
En général, cette approche examine les différents avantages technologiques et économiques de la FA. En outre, selon l’objectif final du fabricant, il n’est pas toujours nécessaire de revoir la conception de la pièce.
« Les gens qui travaillent dans l’industrie de la FA se font constamment demander « pouvons-nous imprimer cette pièce en 3D’’, et la réponse est presque toujours oui… mais ce n’est pas la bonne question. Ce qu’il faut demander, c’est « devrions-nous imprimer cette pièce en 3D ? »
Il est possible qu’une organisation puisse encore tirer des avantages du passage à un processus de FA sans avoir à revoir sa conception : délais plus courts, absence de coût d’outillage, diminution des risques, etc. Mais sans refonte, ils passeront à côté de l’incroyable potentiel d’optimisation qu’offre la liberté de conception pour la FA. Nous avons maintenant à portée de main un incroyable éventail d’outils logiciels de conception générative, de modélisation implicite et d’optimisation de la topologie, et il est dommage de laisser leurs capacités sur la table.
Je suis fermement convaincu que l’expérience de la FA devrait être injectée le plus en amont possible dans le processus de conception, et que la FA peut avoir un effet beaucoup plus important sur le développement de nouveaux produits et les projets de conception « clean sheet » que sur les produits existants qui sont déjà équipés et en production », souligne l’ingénieur d’application de 3DEO.
Malheureusement, cette méthode d’analyse des critères présente également ses limites, car elle se concentre uniquement sur les domaines où la FA réussira, et ne traite pas de ce qui fait de la FA un mauvais choix pour une pièce spécifique. En ce sens, elle ne rejette pas les pièces présentant des limites évidentes. En outre, elle ne tient pas compte de tous les facteurs opérationnels du processus de production qui inclut la chaîne d’approvisionnement.
3- Les scénarios de la chaîne d’approvisionnement
La chaîne d’approvisionnement est devenue une partie intégrante du processus de la FA. C’est pourquoi, Senvol, une société qui fournit des données pour aider les entreprises à mettre en œuvre la FA, a défini sept scénarios de chaîne d’approvisionnement où la FA peut être rentable. Ces scénarios prennent en compte les dépenses de fabrication, les délais, les coûts des stocks, l’approvisionnement, les opérations à distance, les coûts d’importation/exportation et les fonctionnalités.
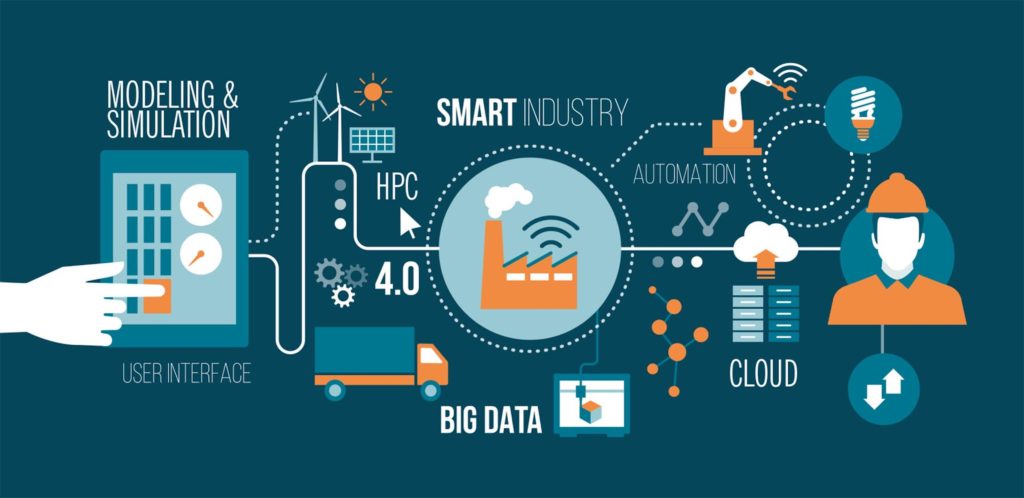
La vérification de la candidature de la FA par cette approche est assez simple : si un composant répond aux exigences d’un ou de plusieurs scénarios, alors la FA doit être explorée plus avant. Cependant, si aucun de ces scénarios n’est satisfait, la FA n’est probablement pas le processus technologique idéal à exploiter.
Scenario | Description |
Coûteux à fabriquer | Avez-vous des pièces qui sont coûteuses parce qu’elles sont complexes, ont des coûts fixes élevés (par exemple l’outillage) ou sont produites en faibles volumes ? La FA peut être plus rentable. |
Longs délais d’exécution | L’obtention de certaines pièces prend-elle trop de temps ? Vos coûts d’immobilisation sont-ils extrêmement élevés ? Voulez-vous accélérer la mise sur le marché ? Grâce à la FA, vous pouvez souvent obtenir des pièces plus rapidement. |
Coûts d’inventaire élevés | Vous surstockez ou sous-stockez ? Avez-vous des difficultés avec les pièces à longue queue ou obsolètes ? La FA peut permettre une production à la demande, réduisant ainsi les stocks. |
Fournisseurs exclusifs | Certaines de vos pièces essentielles sont-elles en exclusivité ? Cela pose un risque pour la chaîne d’approvisionnement. En qualifiant une pièce pour la FA, vous ne dépendez plus complètement d’un seul fournisseur. |
Lieux éloignés | Vous opérez dans des régions éloignées où il est difficile, long ou coûteux d’expédier des pièces détachées ? La FA peut vous permettre de fabriquer certaines pièces sur place. |
Coûts d’importation/exportation élevés | Payez-vous des frais d’importation/exportation importants sur des pièces simplement en raison de l’emplacement de votre unité commerciale et/ou de votre fournisseur ? La production sur place par FA peut éliminer ces coûts. |
Amélioration des fonctionnalités | Avec la FA, il est possible de reconcevoir une pièce pour améliorer les performances au-delà de ce qui était possible auparavant. |
Crédit: Senvol
Le principal avantage de cette approche est que les questions sont faciles à comprendre et peuvent être rapidement évaluées. Toutefois, elle n’est pas toujours considérée comme une méthode objective.
Ces critères diffèrent-ils d’une technologie de FA à l’autre ?
Parfois, chacune de ces méthodes est évaluée en tenant compte du type de production (production à faible volume ou production à haut volume) à réaliser. Cohen attire l’attention sur le fait que ces termes peuvent facilement prêter à confusion pour les industriels de diverses industries.
« Dans l’industrie aérospatiale, les pièces produites en grand volume peuvent signifier quelques centaines de pièces par an. La production en faible volume dans l’industrie industrielle et automobile peut représenter des dizaines de milliers de pièces par an », déclare l’expert.
En outre, toutes ces méthodes ont en commun le fait qu’elles ne tiennent pas compte du caractère unique de chaque technologie de FA.
« Par exemple, alors que les procédés de lit de poudre tels le L-PBF et l’EBM peuvent permettre une optimisation significative du rapport résistance/poids, de la capacité de transfert de chaleur et de l’efficacité du flux de fluide interne, le procédé est encore extrêmement coûteux et s’accompagne d’une longue liste de limitations et de considérations, en particulier dans la production en série. Ces procédés peuvent être des outils fantastiques pour les pièces à faible volume et à coût élevé, mais avec le bon support, la conception et le contrôle du processus peuvent également être rentables pour les petites pièces qui s’emboîtent efficacement sur la plaque de construction.
De même, le procédé Intelligent Layering® de 3DEO a été développé spécifiquement pour les applications à haut volume et à faible coût – je parle de quantités annuelles de plus de 100 000 pièces et de moins de 5 dollars par pièce. Notre procédé est unique dans l’espace de la FA métallique et surmonte de nombreuses limitations inhérentes aux procédés émergents comme le jet de liant, ainsi qu’aux procédés traditionnels comme le MIM et l’usinage CNC. Les types d’applications qui correspondent à notre procédé sont complètement différents de ceux qui correspondent à de nombreux autres procédés sur le marché.
En l’absence de normes industrielles répandues et de maturité technologique, faire le bon choix d’application nécessite une connaissance approfondie des procédés de FA disponibles, de leurs avantages et inconvénients, et une expérience de leur utilisation dans le passé. Chez 3DEO, nous entretenons des partenariats de production à long terme avec nos clients et offrons notre base de connaissances pour accélérer les décisions de ce type », commente le porte-parole de 3DEO.
En bref
Nous avons décrit trois méthodes de critères de sélection qui permettent de définir la FA comme méthode de production. Chacune de ces technologies de FA a ses avantages et ses inconvénients. Cependant, plus le marché progressera, plus les entreprises seront en mesure de standardiser un guide qui aidera à vérifier la candidature de la FA pour les applications de production.
Ce dossier a été initialement publié dans le numéro de Juillet/Août de 3D ADEPT Mag.
N’oubliez pas que vous pouvez poster gratuitement les offres d’emploi de l’industrie de la FA sur 3D ADEPT Media ou rechercher un emploi via notre tableau d’offres d’emploi. N’hésitez pas à nous suivre sur nos réseaux sociaux et à vous inscrire à notre newsletter hebdomadaire : Facebook, Twitter, LinkedIn & Instagram !