Nous avons entendu parler pour la première fois du projet ETHEC city l’année dernière. Il s’agit d’un projet étudiant suisse mené par une équipe d’ingénieurs en mécanique de l’ETH Zurich qui développe un prototype de moto électrique. Plusieurs entreprises, dont des fabricants de technologies d’impression 3D, soutiennent cette initiative et aident les étudiants à aborder la « durabilité dans la mobilité » en explorant les technologies de FA telles que la stéréolithographie (SLA), le frittage laser sélectif (SLS) et la fusion laser sélective (SLM).
En fin de compte, ces technologies sont également une excellente occasion pour les étudiants de découvrir des processus de fabrication qui peuvent être utilisés pour la production en série en dehors de la fabrication de prototypes.
Dans cette veine, une entreprise qui apporte également une contribution essentielle à ce projet est le fabricant allemand de machines voxeljet. Le fabricant d’imprimantes 3D soutient le développement d’un système de refroidissement qui vise à garantir une plus longue durée de vie aux cellules de la batterie.
Selon l’équipe d’ingénieurs de voxeljet, en raison de la capacité limitée de leurs batteries, les motos électriques existantes conviennent mieux à la circulation urbaine qu’aux longs voyages à travers le pays. Toutefois, avec la bonne approche technologique, il est possible de surmonter cette limitation.
La première idée de l’équipe a consisté à agrandir l’espace afin de permettre le refroidissement de la batterie. Pour ce faire, l’équipe suisse a procédé à des récupérations. Ils récupèrent par exemple l’énergie de freinage, en installant un moteur de moyeu de roue dans la roue avant du vélo mais il est vite devenu plus compliqué de stocker au mieux la puissance supplémentaire disponible pour augmenter l’autonomie.
En effet, voxeljet explique dans un rapport que créer une haute densité d’énergie dans un espace le plus réduit possible est une chose. Cependant, maintenir la chaleur générée par le fonctionnement de la batterie à un niveau constant est plus difficile sur une moto que dans un véhicule plus grand. Or, une gestion optimale de la température est cruciale pour la durée de vie de la batterie.
« Le refroidissement de la batterie dans les véhicules électriques est normalement réalisé à l’aide d’un liquide de refroidissement qui passe devant les cellules par un tuyau ou un tube« , explique le Dr Josef Mayr, Group Manager Thermal Simulation chez inspire AG et coordinateur du projet ethec – inspire AG est également un sponsor du projet -. « L’inconvénient de cette méthode est que seul un contact ponctuel ou linéaire est réalisé et que le contact direct avec les cellules n’est pas réellement atteint. » Compte tenu de l’espace limité au milieu du cadre de la moto, un seul concept était finalement possible : l’encastrement complet de toutes les cellules de la batterie dans un bain d’huile.
L’équipe d’ethec s’est inspirée du système de refroidissement des transformateurs dans les sous-stations des grands réseaux électriques. « Des étincelles volent lorsque l’équipement est mis en marche« , explique Mayr, « mais comme les unités nagent entièrement dans de l’huile de silicone et qu’il n’y a donc pas d’oxygène, il ne peut y avoir de court-circuit. »
La fabrication additive entre alors en jeu
Répartis sur deux modules, les étudiants de l’ETH ont assemblé un total de 1 269 cellules rondes lithium-ion d’une puissance totale de 15 kWh. Des simulations de flux assistées par ordinateur ont ensuite permis de créer la structure optimale du boîtier de la batterie, qui devait non seulement être absolument étanche, mais aussi assurer un contact parfait entre les différentes cellules et le flux d’huile de silicone. Cependant, un objet de la taille du boîtier de la batterie ethec dépassait les capacités de l’équipement de frittage direct par laser métallique (DMLS) disponible. Et afin de « montrer aux étudiants le chemin du prototype à la production en série« , selon Josef Mayr, le choix s’est porté sur le moulage métallique. Plus précisément, un moule en sable imprimé en 3D a été utilisé comme modèle pour le moulage d’un alliage aluminium-cuivre – en bref : le moulage imprimé.
Les données CAO numériques du boîtier de la batterie fournies par l’équipe d’ethec ont servi de base à voxeljet pour produire un moule en sable par impression 3D à jet de liant. Dans ce processus, une couche de sable de quartz de quelques micromètres d’épaisseur et un liant projeté sur celle-ci sont alternativement superposés jusqu’à ce que la géométrie spécifiée du futur composant soit imprimée avec la plus grande précision. Le boîtier de la batterie ETHEC a finalement été coulé dans la fonderie d’aluminium de Kupral Spa, basée à Brescia, en Italie.
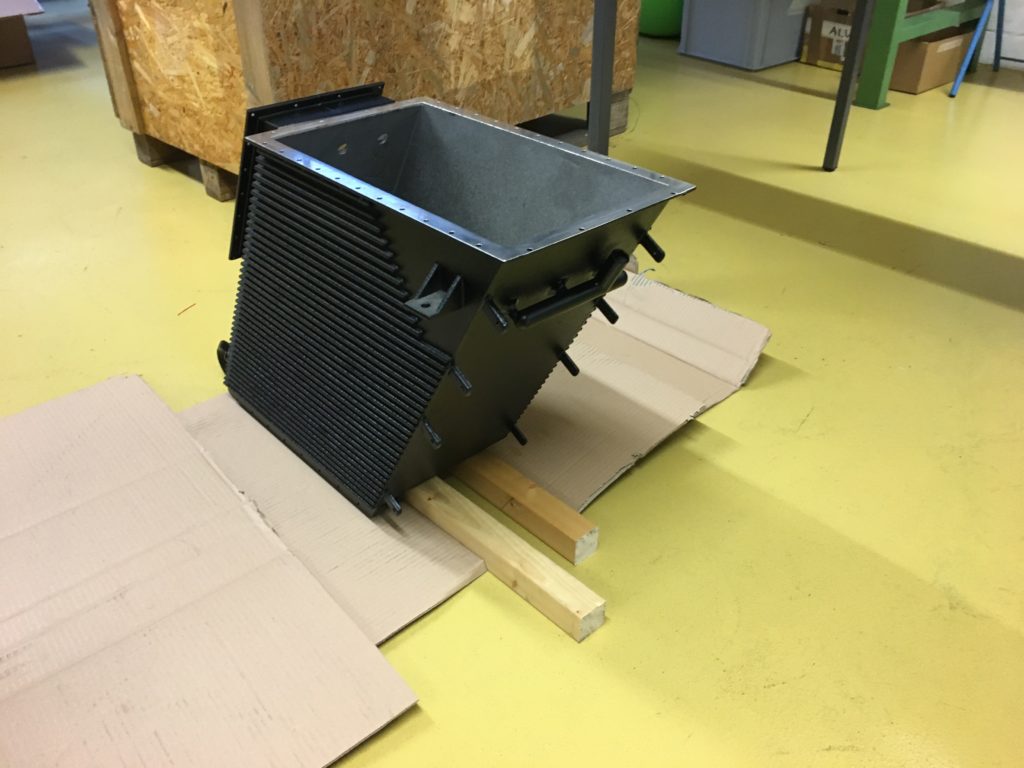
Le prototype ETHEC n’a pas encore été soumis à des tests pratiques à grande échelle. Mais le concept d’une moto électrique économe en énergie conçu par les étudiants présente un potentiel impressionnant : La vitesse de pointe devrait atteindre un maximum de 160 km/h, et grâce à la récupération et au nouveau concept de batterie, ethec city pourrait atteindre une autonomie d’environ 400 km. La question de savoir si le concept convaincra également les acheteurs potentiels reste ouverte pour le moment – la recherche d’un partenaire pour la production industrielle en série d’ethec city est toujours en cours.
N’oubliez pas que vous pouvez poster gratuitement les offres d’emploi de l’industrie de la FA sur 3D ADEPT Media ou rechercher un emploi via notre tableau d’offres d’emploi. N’hésitez pas à nous suivre sur nos réseaux sociaux et à vous inscrire à notre newsletter hebdomadaire : Facebook, Twitter, LinkedIn & Instagram ! Si vous avez une innovation à partager pour le prochain numéro de notre magazine numérique ou si vous avez un article à faire connaître, n’hésitez pas à nous envoyer un email à contact@3dadept.com