Dans l’industrie automobile, une grande partie consiste à produire non seulement une pièce performante, mais aussi une pièce plus légère. Un système modulaire récemment lancé pour l’outillage automobile permet de résoudre ce problème. En effet, le mélange de poutres en fibre de carbone et d’éléments uniques imprimés en 3D permet d’obtenir des gabarits et des appareils d’inspection 90% plus légers que les outils traditionnels.
Lancé par Rapid Fit, un fabricant d’outils et une filiale de Materialise, la société a utilisé l’impression 3D pour fabriquer les formes montées, les points de montage ainsi que les connecteurs de cadre.
L’avantage de la légèreté
Grâce à la légèreté, il devient plus facile et plus rapide pour une personne de faire fonctionner et de déplacer les appareils sans utiliser d’équipement lourd.
Rappelez-vous les caractéristiques de la fibre de carbone présentées dans le numéro d’avril de 3D Adept Mag (Page 34). Elle intègre toutes les normes standards en termes de fonctionnalité, de précision, de stabilité et de rigidité. En outre, elle minimise la dilatation thermique ; par conséquent, est approprié dans les environnements de production ainsi que les chambres climatiques.
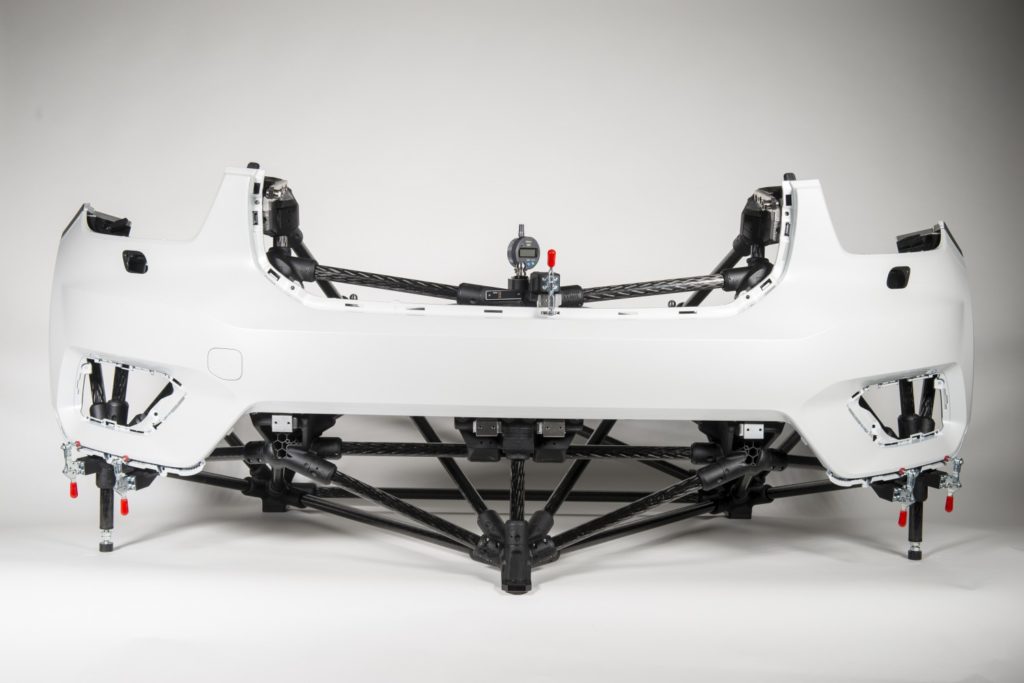
L’utilisation de la fabrication additive par Rapid Fit « permet, le cas échéant, de développer des solutions pour des formes très complexes et des fonctionnalités intégrées. Les ajustements instantanés et les clips qui peuvent être détachés à nouveau augmentent la répétabilité et améliorent la représentation de l’environnement de la pièce. L’utilisation de pièces normalisées réutilisables permet d’économiser des coûts à long terme. »
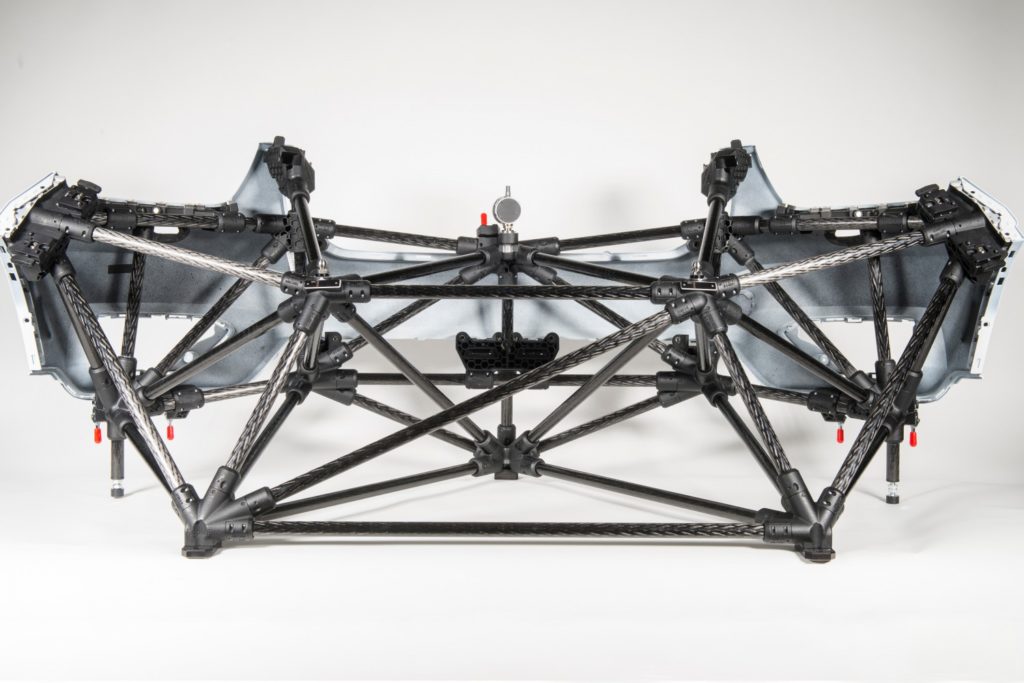
Appareil installé sur un pare-chocs de voiture
Enfin, techniquement parlant, l’équipe de Rapid Fit a utilisé des données CAO et une bibliothèque paramétrique pour fabriquer un gabarit. La bibliothèque paramétrique est un gros avantage en termes de personnalisation et d’économie de temps. Après la production des pièces par Materialise, elles sont montées sur le châssis et calibrées avec une machine de mesure de coordonnées haut de gamme (CMM – coordinate measuring machine).
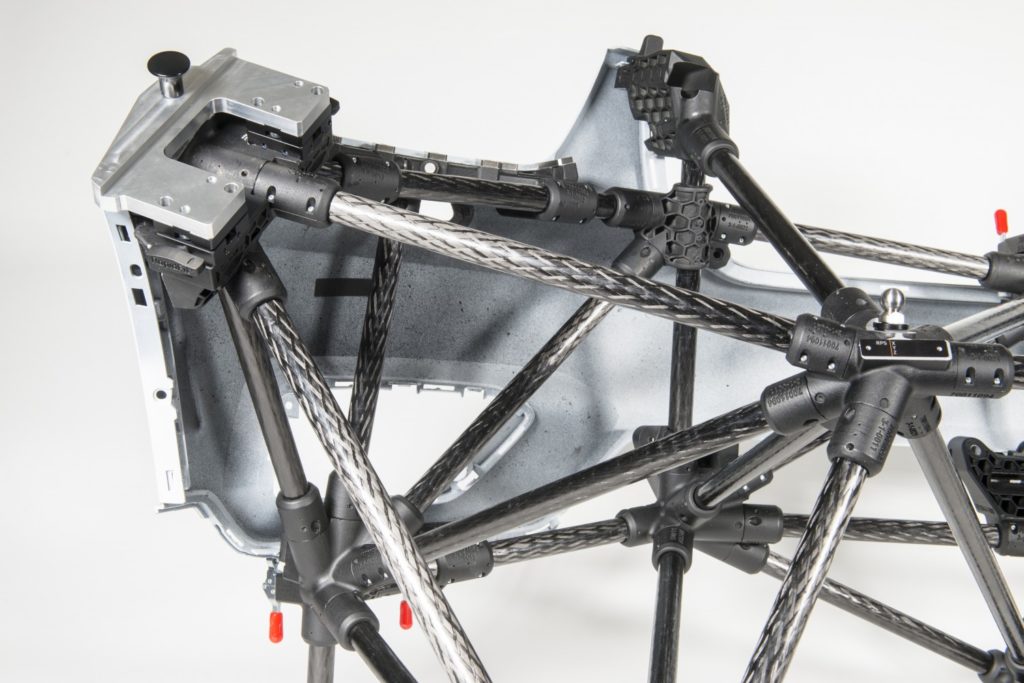
Vue détaillée des connecteurs imprimés en 3D et des poutres en fibre de carbone
Pour des informations exclusives sur l’impression 3D, abonnez-vous à notre newsletter et suivez-nous sur les réseaux sociaux !
Voulez-vous figurer dans le prochain numéro de notre magazine numérique ? Envoyez-nous un email à contact@3dadept.com
//pagead2.googlesyndication.com/pagead/js/adsbygoogle.js
(adsbygoogle = window.adsbygoogle || []).push({});