Un aperçu du prochain numéro de mai/juin de 3D ADEPT Mag qui présentera l’utilisation de la fabrication additive dans l’industrie du sport dans son segment « applications ».
C’est comme si c’était hier que COBRA Golf a dévoilé un putter en métal imprimé en 3D avec l’édition limitée KING SuperSport-35. Et pourtant, c’était l’année dernière et entre-temps, le fabricant de clubs et d’équipements de golf ne s’est pas reposé sur ses lauriers.
Dans le cadre de la préparation du prochain numéro de mai/juin de 3D ADEPT Mag, qui présentera l’utilisation de la FA dans l’industrie du sport dans son segment « applications », nous nous sommes entretenus avec Mike Yagley, vice-président de l’innovation et de l’IA chez COBRA Golf. Ensemble, nous avons discuté de l’utilisation de la FA dans l’industrie du golf, de leurs défis, des améliorations qu’ils attendent des fournisseurs de solutions de FA ainsi que de ce que nous pouvons attendre d’eux en termes de produits de golf fabriqués à l’aide des technologies de FA.
Notre conversation tombait à point nommé puisque COBRA Golf fait aujourd’hui officiellement son entrée sur le marché des putters, avec la série KING, sa première ligne complète de putters multi-matériaux imprimés en 3D.
COBRA Golf affirme que la série de putters imprimés en 3D KING est le résultat d’une collaboration de plusieurs années entre son équipe et HP, une collaboration qui a débuté avec le lancement du putter LE SuperSport-35. Dans le cadre de sa collaboration avec HP, l’équipe COBRA a d’abord utilisé l’impression 3D métal (Metal Jet) et a progressivement orienté les opérations de fabrication vers l’impression 3D nylon (Multi-Jet) afin de tirer le meilleur parti des avantages du nylon en termes de poids (qui représente environ la moitié de la masse d’aluminium).
Le choix de la FA a été déterminant dans le cycle de développement du produit.
Soyons honnêtes. À première vue, un club de golf est un objet relativement simple, composé d’une tête, d’un manche et d’un grip, mais son processus de fabrication est loin d’être aussi simple. En effet, la tête du club à elle seule nécessite environ 400 personnes pour être effectivement réalisée.
De plus, alors que le moulage et le forgeage sont les principaux procédés de fabrication conventionnels qui étaient autrefois envisagés pour la fabrication de ces produits, Yagley nous explique que le processus de fabrication exigeait beaucoup de travail : meulage, polissage, finition, découpe de rainures, travail manuel, parfois chromage ou peinture, pour ne citer que quelques-unes des tâches.
C’est pourquoi, afin de réduire le cycle de développement du produit (et pour d’autres raisons qui seront décrites dans le numéro de mai/juin de 3D ADEPT Mag), l’équipe COBRA a décidé de se tourner vers la FA. Tout en se concentrant sur la fabrication de la série KING imprimée en 3D, le vice-président de l’innovation et de l’IA a expliqué que toutes les pièces ne peuvent pas être fabriquées à l’aide de procédés traditionnels. Les cartouches en treillis complexes imprimées en 3D, par exemple, illustrent bien cet argument. Les cartouches sont essentielles pour créer un poids discrétionnaire et obtenir le meilleur « MOI » possible dans chaque modèle de putter.
(MOI signifie « moment d’inertie ». Cette mesure (grammes par centimètre carré) indique la résistance de la tête d’un club à la torsion).
Outre l’optimisation du poids, la cartouche en treillis sert également de structure de soutien au corps, amortit les vibrations et affine le son. La structure en treillis imprimée en 3D offre donc un MOI élevé pour une stabilité et des performances de roulement améliorées dans trois modèles distincts – le GrandSport-35 (OS Blade), le SuperNova (OS Fang) et l’Agera (OS Mallet). La société révèle que chaque modèle est doté d’un châssis en acier, d’une couronne en aluminium forgé, de poids en tungstène et d’un insert frontal SIK pour offrir une stabilité et une régularité de roulement inégalées sur chaque putt.
Putter AGERA
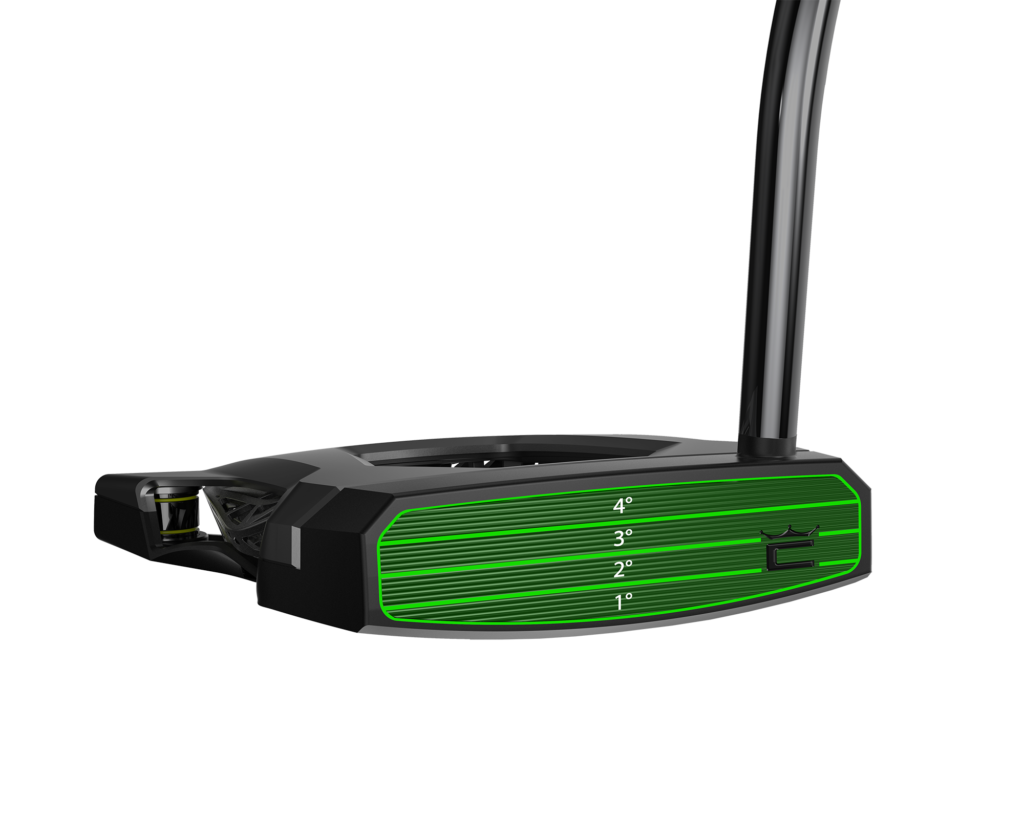
En ce qui concerne les technologies de fabrication, les putters multimatériaux imprimés en 3D ont nécessité la combinaison de la technologie d’impression 3D brevetée de HP et de la technologie brevetée Descending Loft (DLT) de SIK Golf. Cette dernière intègre quatre lofts descendants sur la face afin de fabriquer un angle de lancement et un roulement cohérents pour différents styles de putts et de coups. En d’autres termes, la DLT de SIK permet d’économiser du poids et d’obtenir des sensations douces mais nettes à l’impact.
« Nous sommes extrêmement enthousiastes à l’idée de lancer notre nouvelle famille de putters imprimés en 3D, poursuivant notre partenariat avec HP, utilisant leur Metal Jet Technology pour innover et transformer la façon dont les équipements de golf sont fabriqués grâce à l’impression 3D, un processus extrêmement efficace dans la conception et le développement de notre nouvelle ligne de putters », a déclaré Jose, VP Marketing & Product Architecture, Cobra Golf. « Nous sommes extrêmement enthousiastes à l’idée que les golfeurs puissent essayer nos nouveaux putters imprimés en 3D, bien que chacun soit unique, ils offrent tous une stabilité, une tolérance et des performances de roulement avancées qui faciliteront le putting pour les golfeurs de tous niveaux. »
Restez connectés pour en savoir plus sur les KPI (indicateurs clés de performance) qui sont analysés pour mesurer la performance d’un putter de golf imprimé en 3D, les principaux domaines d’amélioration en ce qui concerne les technologies de FA et d’autres détails sur la série imprimée en 3D KING.
Tout cela sera présenté dans le segment « applications » du prochain numéro de mai/juin de 3D ADEPT Mag, ainsi que des informations clés provenant de fabricants d’imprimantes 3D et d’ingénieurs qui ont consacré leur travail à l’amélioration des performances de course grâce à la conception de treillis imprimés en 3D.
N’oubliez pas que vous pouvez poster gratuitement les offres d’emploi de l’industrie de la FA sur 3D ADEPT Media ou rechercher un emploi via notre tableau d’offres d’emploi. N’hésitez pas à nous suivre sur nos réseaux sociaux et à vous inscrire à notre newsletter hebdomadaire : Facebook, Twitter, LinkedIn & Instagram ! Si vous avez une innovation à partager pour le prochain numéro de notre magazine numérique ou si vous avez un article à faire connaître, n’hésitez pas à nous envoyer un email à contact@3dadept.com.