Que ce soit dans les foyers ou dans les milieux industriels, un four reste un appareil qui produit de la chaleur. En milieu industriel, ces appareils ont d’abord été utilisés en métallurgie pour chauffer et faire fondre le métal ou pour éliminer la gangue, principalement dans la production de fer et d’acier. Au fil du temps, l’utilisation des fours s’est tellement développée qu’il faut une presse spécialisée pour parler de tous ses tenants et aboutissants. Cependant, il s’avère qu’en ce qui concerne la fabrication additive, l’utilisation des fours reste assez limitée, mais elle est d’une importance capitale pour obtenir la pièce imprimée en 3D souhaitée.
Les fours industriels sont peut-être utilisés depuis le début de la révolution industrielle, mais le XXe siècle a apporté son lot d’innovations, et a étendu l’utilisation de ces technologies à de nouvelles applications qui n’étaient pas envisagées auparavant dans le domaine. L’histoire ne nous dit pas quand exactement ont eu lieu les premières utilisations de fours avec la fabrication additive. Cependant, elle révèle que la plupart des entreprises qui fournissent des fours aux fournisseurs ou utilisateurs de technologies de fabrication additive sont pour la plupart des entreprises qui ont une solide expertise dans le développement et la commercialisation de fours pour les processus de fabrication conventionnels et d’autres industries telles que la fonderie, le forgeage, la technologie des processus thermiques, pour n’en citer que quelques-unes.
Alors, pourquoi et avec quelles technologies de FA les fours sont-ils utilisés? Quels types de pièces imprimées en 3D nécessitent des fours ? Comment utilise-t-on les fours ? Et quelles sont les principales caractéristiques de ces machines ?
Cet article vise à donner un aperçu de l’utilisation des fours pour les pièces fabriquées de manière additive.
Pourquoi et où utilise-t-on les fours ?
Tout d’abord, étant donné leur nature primaire, les fours sont utilisés pour des applications qui nécessitent des températures de traitement élevées.
Dans l’industrie de la FA en particulier, même si les applications réalisées grâce aux technologies de FA métal nécessitent généralement l’utilisation de fours, il convient de noter que deux raisons principales peuvent expliquer l’utilisation de fours. Ces raisons permettent également de cataloguer les 2 principaux types de fours utilisés dans le domaine :
Les pièces qui nécessitent un frittage (et souvent un déliantage) et les pièces qui nécessitent un traitement thermique. À cet effet, « les céramiques et les pièces imprimées en 3D en composite peuvent nécessiter un traitement dans un four à vide, comme la plupart des pièces imprimées en 3D métal« , note d’emblée Andrea Cassani, directeur des ventes chez TAV VACUUM FURNACES SPA.
Cela signifie que, fondamentalement, tous les types de pièces imprimées en 3D peuvent nécessiter l’utilisation d’un four à un moment donné de la production.

Déliantage et frittage
Pour ceux qui ne sont pas familiers avec ces termes, veuillez noter que le déliantage et le frittage interviennent tous deux après le processus de fabrication.
Le déliantage est un processus qui consiste à retirer le matériau de liaison primaire en un temps très court et avec le moins de dommages possible.
Le frittage est souvent considéré comme l’étape finale de tous les procédés de métallurgie des poudres, y compris certains procédés d’impression 3D métal. Au cours de cette étape, les « pièces vertes » (une combinaison de poudre métallique et de liant) sont d’abord chauffées à une température à laquelle le liant évolue et est retiré des pièces. Le four monte ensuite en puissance jusqu’à la température de frittage du métal, qui est juste inférieure à la température de fusion du matériau, ce qui permet de fusionner les particules de métal. Une fois le frittage terminé, il n’y a que peu ou pas de traces des particules de poudre d’origine, le processus de fabrication et les pièces ayant une très faible porosité ».
Cependant, l’opérateur ne réalise pas toujours automatiquement les deux processus. Même s’il est plus rapide d’écroûter puis de fritter les pièces, l’opérateur peut aussi décider de (sauter l’étape d’écroûtage et) de fritter directement la pièce. D’un autre côté, il faut savoir que le processus de déliantage peut comporter plusieurs étapes, et plus d’un cycle avant que le matériau de liaison ne soit complètement éliminé, avant que la pièce ne soit frittée.
Quels que soient les cycles effectués, le frittage permet d’obtenir une meilleure densité de la pièce. Selon les experts de Desktop Metal, au cours de la dernière étape du frittage, les pores continuent de se rétrécir et la pièce se densifie davantage. Pour optimiser la densité de la pièce, les températures et le maintien du frittage sont étroitement surveillés pour contrôler et éviter la croissance des grains, qui peut se produire si les pièces sont laissées à des températures élevées.
En général, les trois étapes suivantes sont souvent observées :
- Élimination du liant – soit par dégradation (interaction chimique avec le gaz du four) et/ou évaporation (liant vaporisé).
- La densification et l’élimination des pores ont lieu lorsque les particules métalliques migrent et fusionnent.
- Refroidissement du four pour que les pièces puissent être retirées en toute sécurité.
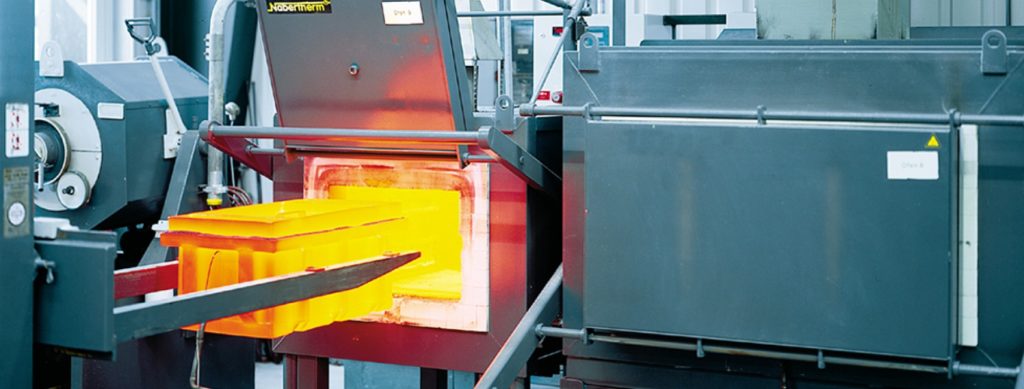
Traitement thermique
Comme son nom l’indique, le traitement thermique consiste à chauffer un matériau à une température spécifique, puis à le refroidir pour améliorer ses propriétés mécaniques. Ce matériau est généralement un métal ou un alliage. Dans certains processus de fabrication, cette partie est d’une importance capitale car elle permet à la pièce fabriquée de mieux résister à l’usure.
Pour y parvenir, quoi de mieux que d’utiliser un four qui peut maintenir la chaleur à une température souhaitée pendant une durée définie, avant de refroidir.
« Lorsqu’il est chaud, la structure physique du métal, également appelée microstructure, se modifie, ce qui entraîne finalement une modification de ses propriétés physiques. Le temps pendant lequel le métal est chauffé est appelé « temps de trempage ». Il est extrêmement compliqué de savoir à quelles températures chauffer et refroidir les métaux, ainsi que de connaître la durée de chaque étape du processus pour un métal ou un alliage spécifique. C’est pourquoi les spécialistes des matériaux, connus sous le nom de métallurgistes, étudient les effets de la chaleur sur le métal et les alliages et fournissent des informations précises sur la manière d’exécuter correctement ces processus« , explique un expert de General Kinematics.
Prenant l’exemple des pièces fabriquées à l’aide de la technologie SLM, TAV VACUUM FURNACES SPA explique que la plupart des matériaux imprimés à l’aide de la technologie SLM nécessitent un traitement thermique.
« Ce traitement thermique peut permettre de ‘détendre’ (pour libérer la plupart des tensions internes accumulées dans le matériau pendant la phase d’impression) ou d’un autre type (pour tenter d’optimiser les propriétés mécaniques de la pièce en fonction de son application spécifique). Généralement, ces traitements sont effectués à l’air ou en atmosphère contrôlée« , souligne l’expert. En outre, des matériaux tels que l’acier inoxydable, les superalliages de titane, les superalliages de nickel et les alliages de CoCr, pourraient nécessiter l’utilisation du vide.
Quels types de pièces imprimées en 3D nécessitent des fours ?
Comme mentionné précédemment, tous les types de pièces imprimées en 3D peuvent nécessiter l’utilisation de fours à un moment donné de leur production. Le fait est qu’il existe tellement de fours qu’une pièce imprimée en 3D métal ne nécessitera pas le même four qu’une pièce imprimée en 3D céramique ou en polymère. Dans le même ordre d’idées, elles ne passeront pas nécessairement par les mêmes étapes après les phases de déliantage ou de frittage.
Métaux | Céramiques, verre, composites, sable | Plastiques |
Décollement
Frittage Soulagement des contraintes Recuit de mise en solution Durcissement |
Décollement
Frittage Séchage Polymérisation |
Polymérisation
Trempe Séchage |
Sous gaz de protection, réaction
Gaz ou sous vide |
A Air | A Air |
Fours à chambre avec boîtes à gaz de protection | Décrochage dans un four à cendres
Décorticage dans des fours à chambre avec circulation d’air Frittage dans des fours à chambre Déliantage et frittage dans des fours combinés Fours de déparaffinage |
Fours
Séchoirs à chambre Fours à chambre à convection forcée |
Fours à cornue à parois chaudes | Voir aussi les concepts de séchage, de déliantage, de nettoyage thermique et de brûlage | Voir aussi les concepts de séchage, de déliantage, de nettoyage thermique et de brûlage |
Fours à cornue à parois froides |
Source : Nabertherm – Traitement thermique des pièces de fabrication additive
Veuillez noter que les pièces imprimées en 3D produites en céramique, en verre, en matériaux composites ou en sable peuvent être traitées dans des fours à vide ou à l’air.
Comment utilise-t-on les fours ? Et quelles sont les principales caractéristiques de ces machines ?

Nous avons commencé cet article en supposant que nous pourrions dresser une utilisation générale des fours pour les pièces imprimées en 3D. Nous nous sommes trompés. Les contributeurs et les ressources sur lesquels nous nous sommes appuyés pour écrire cet article révèlent qu’avec les nombreux types de fours qui existent, il ne serait pas possible de cataloguer les principales caractéristiques des fours – du moins pas ici.
Alors, comment aider les utilisateurs de la FA à prendre une décision ? Cassani tente d’apporter une réponse utile :
« Nous ne pouvons pas faire une déclaration générique valable pour tous les types de fours à vide. Nous pouvons dire qu’aujourd’hui, la plage de température requise pour l’impression 3D des pièces se situe approximativement entre 500 et 1400°C pour le frittage et le traitement thermique ou en dessous de 900°C pour le déliantage/’présintering’. Dans le cas où une pièce doit être frittée souvent, nous divisons le processus et les fours en 2 étapes : première étape, un four de déliantage pour retirer les pièces du liant et deuxième étape (à température plus élevée), un four de frittage.
Dans le cas de pièces devant être traitées thermiquement, le four est très proche d’un four de traitement thermique sous vide classique, avec quelques caractéristiques spécifiques. Il faut souvent considérer que celui qui achète un four pour le traitement thermique de pièces imprimées en 3D n’utilise le four que pour ces pièces, donc [une conception optimisée est généralement justifiée]. »
Dans le même ordre d’idées, on peut prendre note des recommandations suivantes de TAV VACUUM FURNACES SPA & SECO/WARWICK S.A. aux entreprises à la recherche d’un nouveau four :
- Habituellement, lorsqu’on utilise la même technologie pour les processus et les matériaux d’impression 3D, il n’est pas nécessaire d’adapter/changer le four.
- Cependant, la taille du four doit être ajustée pour correspondre à la capacité de production estimée.
- Après l’utilisation des fours, la pièce nécessite souvent une finition et, dans certains cas, un petit usinage.
- Si le four est correctement personnalisé, le four lui-même ne représente qu’un faible pourcentage de l’investissement requis pour les imprimantes 3D et il peut généralement fonctionner avec 4 à 16 imprimantes.
- Une technologie peut nécessiter un frittage, tandis qu’une autre aura besoin d’une relaxation des contraintes. Ainsi, prendre en considération les objectifs futurs du fabricant – tels que la standardisation d’un four, la production de masse ou un flux constant de commandes – permet d’investir dans le bon four industriel et aide les entreprises à éviter la plupart des obstacles avant même qu’ils ne surviennent.
Pour aller de l’avant…
La vérité est qu’à mesure que la FA se développe, le besoin de meilleures capacités technologiques continue d’augmenter et ce n’est que récemment que les processus de traitement thermique ont commencé à occuper une place plus importante dans le paysage de la FA.
Disposer d’une imprimante 3D industrielle (métal/polymère) n’est plus une grande réussite. En fait, plusieurs rapports, dont l’enquête de PostProcess sur la post-impression additive, révèlent que plus de 50 % des utilisateurs d’imprimantes 3D disposent de deux ou trois types de technologies différentes dans leurs installations.
Cela signifie que les inconvénients d’un procédé de fabrication seront en fin de compte compensés par les avantages des autres et, dans ce schéma de production, les fours devront accueillir les deux.
C’est la raison pour laquelle les collaborations entre les développeurs de fours et les fabricants d’imprimantes 3D ou les centres de recherche/universités privés et publics sont également répandues ici. Comme c’est le cas pour TAV VACUUM FURNACES SPA, ces collaborations aident les producteurs d’imprimantes 3D et les centres de recherche/universités à définir des normes de post-traitement et à améliorer constamment les caractéristiques du four en termes de performance, de productivité et de qualité sur les pièces imprimées en 3D.
Sources:
Principale contribution: Interview avec Andrea Cassani, Sales Director à TAV VACUUM FURNACES SPA.
Contributions externes: SECO/WARWICK S.A. – Desktop Metal – Nabertherm – General Kinematics
Ce contenu a d’abord été publié dans le numéro de Juillet/Août 2021 de 3D ADEPT Mag. – Image de Une: 3D Hubs.