If one only looks at the manufactured part, at first glance, it could be easy to say that casting technology has nothing to envy to metal 3D printing as both technologies can deliver parts with internal holes and similar surface roughness. Here is the thing, surface roughness and internal holes are not enough to tilt the balance in favour of one technology or another. Mechanical properties, productivity and costs are other items that could help determine if both technologies can be seen as “enemies” or “friends”.
Â
Have you ever realized that almost every object that surrounds us integrates some casting parts? The gate of a house, a wrench, an aircraft, an office building, a truck, etc. Each of these objects integrates some metal cast parts. With such a high number of applications covered by casting technology, and given the well-known advantages of additive manufacturing, logic would have it then that combining AM and casting would automatically lead to a number of more performant applications in a wide range of industries, but things are not always that easy in manufacturing.
It makes sense to explore how these technologies can advance hand in hand when we know that the foundry industry represents a big percentage of the manufacturing industry.
Casting technology is one of the oldest production technologies in the world – as a matter of fact, the process of casting was used in Egypt by 2800 BC. For those who are not familiar with this process, it could be interesting for you to keep this description in mind: typically used to create hollow and intricate shapes, casting refers to a liquid material being poured into the cavity of a specifically designed mold (the cavity referring to the shape of the product to fabricate). Once the liquid material cools, it solidifies into a part called a casting.
As manufacturers are increasingly looking for solutions that could deliver the most favorable price-time-quality conditions, how can we not imagine that additive manufacturing, one of the recent manufacturing technologies, can have its part to play in a fabrication process that involves casting?
This dossier ambitions to explore the different roads where AM & Casting can be seen as complementary processes, as opposed to the ones where they can be seen as competitive processes. To do so, this exclusive feature will discuss:
- The various casting processes that exist while laying emphasis on the ones that are a great match for AM;
- The software & materials standpoints for hybrid manufacturing approaches that involve AM & Casting;
- The various expectations in terms of productivity and costs that may arouse.
Types of casting processesÂ
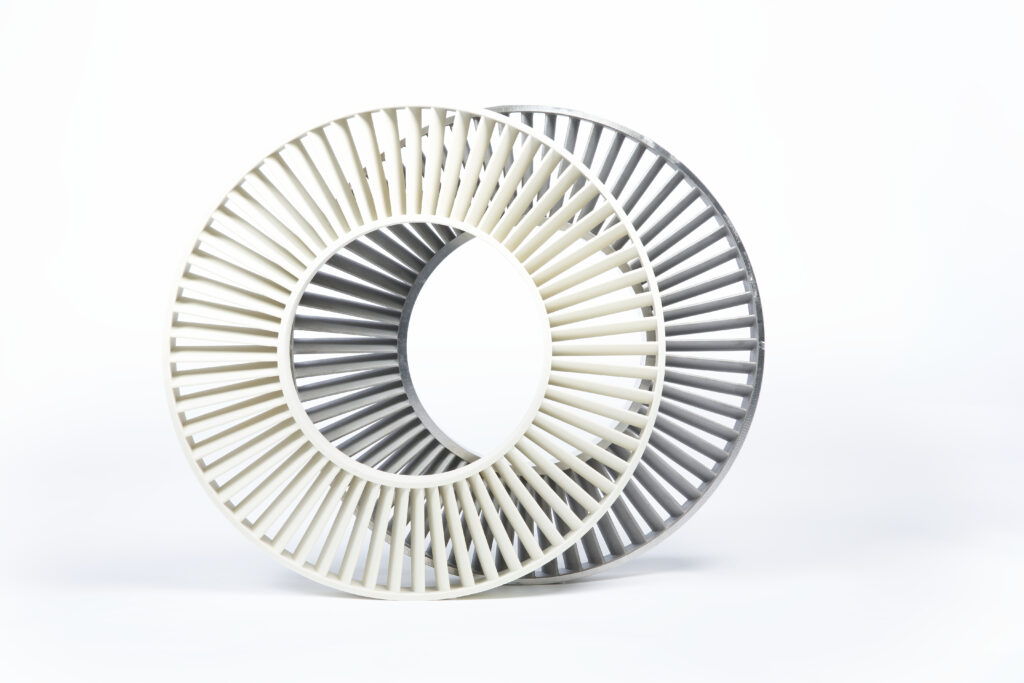
There are usually three different processes that immediately spring to mind when talking about casting: Die casting, Investment casting, and Sand casting. In reality, research shows that one can have up to 13 different types of casting processes. In addition to the three processes mentioned above, the other casting methods include: Shell mold casting, Plaster mold casting, Ceramic mold casting, Vacuum casting, Permanent mold casting, Slush casting, Pressure casting, Centrifugal casting, Continuous casting and Squeeze casting.
Interestingly, “the main casting processes that are being combined with AM are sand and investment casting. Both casting processes can be addressed with Binder Jetting. Either to print sand molds and cores directly and without the need for tools, or by printing PMMA plastic to create models for investment casting applications. By combining sand or investment casting with AM the costs and delivery time, especially for prototypes and small volumes or large single components can be reduced by up to 75 % due to the needlessness of tools”, Christian Traeger, Director for Sales & Marketing at voxeljet states from the outset.
A sand casting method requires the production of castings in a sand mold, steel, iron and most non-ferrous alloy castings. It involves several stages in order to achieve a high-quality finish. However, a few of its advantages and disadvantages can be summarized as follows:
Advantages | Disadvantages |
Cheap production costs, especially in low-volume runs. | The process yields a lower degree of accuracy compared to other methods due to shrinking. |
Possibility to manufacture large parts. | It can be difficult to sand cast parts with predetermined size and weight specifications. |
Ability to cast both ferrous and non-ferrous materials. | Potential poor surface finishes may occur. |
The well-known investment casting method on the other hand, starts in the wax room and finishes with testing where castings are carefully fettled, blasted and heat treated. Traditionally, this process requires creating a mold into which a molten alloy can be poured: a wax pattern is coated with a refractory ceramic material; as the refractory material gets hardened, its internal geometry takes the shape of the wax pattern; during the third stage, the wax is melted out and the molten metal is poured into the mold cavity. This molten metal thereafter solidifies and the outer ceramic material is broken down to take the casting out.
As summarized above with the sand casting process, here are a few advantages and disadvantages of this process:
Advantages | Disadvantages |
Can achieve the casting of highly complex, extremely accurate parts with good surface finish right out of the mold; | Ideal for parts with small sizes. |
Can cast very thin (~0.015 in) sections with incredibly low tolerances (~0.003 in) | Parts with cores or holes smaller than 1.6 mm or holes deeper than 1.5 times the diameter of the part are difficult to investment cast. |
Possibility to automate the process, therefore to produce a large amount of parts; | May involve expensive equipment and resources |
Various types of parts can be manufactured using a wide range of materials: stainless steels, magnetic irons, brass and more. | |
Thorough testing carried out throughout the process. |
Â
Some of these advantages and limitations have been shared by Suraj Kathale from HCL Technologies.
While attention is often made on sand casting and investment casting when talking about AM & casting, it should be noted that AM can also be a response to die cast tooling in certain industries like automotive.
In a die casting process, the high-pressure metal liquid is pressed into a precision metal mold cavity at high speed and the metal liquid is cooled and solidified under pressure to form a casting.
Unlike other processes, this method involves the following advantages and disadvantages:
Advantages | Disadvantages |
High production efficiency and die casting molds can be used several times. | Long lead times |
Reduced requirements when it comes to post-casting machinery | Large parts cannot be cast |
Ideal for mass production |
Applications of AM in die casting can demonstrate how 3D printed conformal cooling channels close to the surface of these tools create a thermally balanced die, and how the benefits cascade into decreased cycle time, lower scrap rates and lower labor costs.
What AM process can be integrated to casting?
Sometimes, exploring routes where AM and casting are complementary, comes down to finding a faster (and somewhat affordable) way to create the mold before completing the manufacturing process. As you know, in this case, AM is often used to create the sand molds and cores that are thereafter used to fabricate parts by casting.
That being said, binder jetting remains the most widely used process with casting – sand casting especially. In this process, a printhead deposits a liquid binding agent onto a thin layer of powder particles — foundry sand, ceramics, metal or composites –. In this case for example, sand is usually the 3D printable material, the binder is foundry-grade resin while the component manufactured is a sand mold or mold core. This form of AM is often referred to as sand 3D printing, and on the current market, only a few manufacturers have built solid expertise in this area. They include for instance voxeljet, ExOne and ETEC (formerly known as EnvisionTEC).
As far as investment casting is concerned, applications reveal that another technology that is a great fit for casting workflows is SLA (Stereolithography). The technology can enable the production of metal parts at a lower cost, with greater design freedom, and in less time than traditional methods. One of the objectives in investment casting is to use as little material as possible, while maintaining shape and accuracy. This objective can easily be met with SLA, where a UV laser cures and solidifies thin layers of resin in order to deliver internal structures, thin walls, surface finish and ideal resolution. The manufacturing steps that lead to the final product may often vary from one manufacturer to another, but ultimately, when using SLA patterns, it’s easy to modify the original design of the pattern mold and examine the results in just a few days.
Due to the fact that investment casting foundries cannot often produce prototype castings until the injection mold is completed, FDM 3D printing is often used as an another option for producing investment casting patterns that are a lot more efficient and cost-effective.
That being said, other items that are worth considering are the materials and software standpoints as well as the mechanical properties of the parts achieved.
The software standpoint
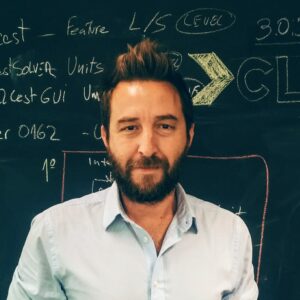
Very little credit is often given to the design software, yet it can play a crucial part in ensuring the success of the part. Every single manufacturing process starts with a design, and as always, operators will look to deliver the maximum performance of the part by making the most of the manufacturing process.
Needless to say that Sand Casting (3D printed Mold) and Investment Casting (3D printed pattern) have different manufacturing constraints, therefore imply many differences at the design level. As seen with some traditional AM processes, Martin Solina, ‪Vice President, Inspire Manufacturing Solutions, Altair recommends foundries to ask themselves some basic questions before going to production: ““Can I cast this shape?” This is key to have sound parts without defects and to minimize rejections. What will be the production cost? How does it compare with a traditional method? What are the benefits?”
Nevertheless, at the very beginning of the design stage, when AM and casting are explored in a hybrid manufacturing approach, one of the concerns that may arouse might be the right way to achieve the optimal geometry of the part. For Martin Solina, “this shouldn’t be a concern as this is a great advantage that can be obtained using a hybrid process.” “Hybrid casting has benefits from both worlds: additive manufacturing gives flexibility to design lightweight and optimal designs, while casting provides proven manufacturing method with good material properties. [This means that] by using 3D printing and casting, we are maximizing the design freedom while increasing performance and reducing weight of the parts”, he explains.
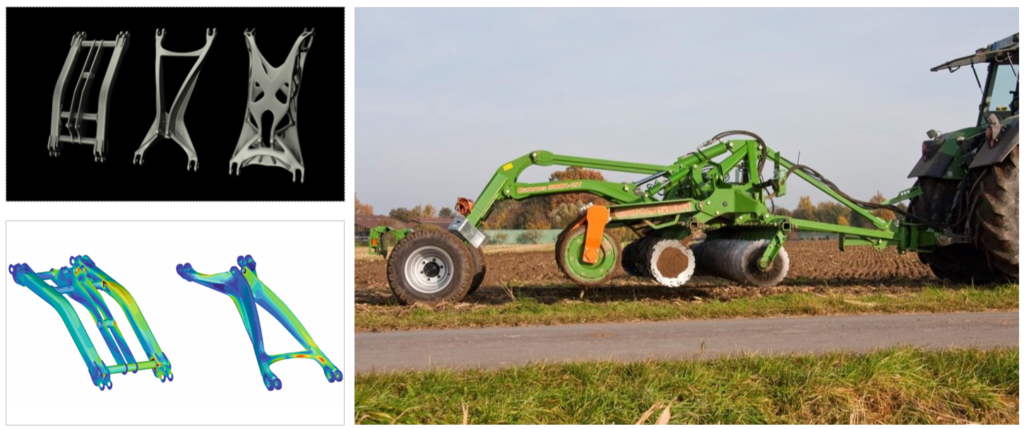
Furthermore, if in a solely traditional casting process, it’s possible to have a software tool that enables the investigation of the cast parameters and eliminates the possible failures of the casting process during the design phase, it makes sense to expect such dual function in this hybrid manufacturing approach. To make the business case for AM & Casting compelling, design software should allow users to do more than simply provide CAD tools. For Altair’s representative, this means that design engineers should – for example – be able to optimize the “performance of the part while defining manufacturing rules to ensure the manufacturability of the part for the particular manufacturing process. Design software must provide the freedom to the user to redefine the part and provide quick answers to questions regarding performance under different load cases, manufacturability, defect prediction or validation of the manufacturing process. Based on this, the role of a design software today has changed from a basic CAD tool to a simulation-driven design tool that provides feedback and information to improve and optimize the design of the part and processes integrating topology optimization and different type of analysis and simulation tools like structural, thermal or fluid analysis. Manufacturing simulation and many other tools help designers make decisions based on information, like:
- Create and Modify Designs with Ease: Create, modify and defeature solid models quickly, use PolyNURBS to create free-form smooth geometry and study multiple assembly configurations.
- Optimize for Manufacturability: Arrive at the ideal design direction extremely early in the process: topology optimization is based on physics and observes manufacturing process constraints.
- Simulate at the Speed of Design: Experience an interactive engineering design environment for rapid design exploration and product creation, without the need to invest in new computer hardware.”
Legend: Rocker arm Diet! The way to lighter agricultural machines through topology optimization and Manufacturing simulation – Altair, Amazone and Voxeljet have not only made a rocker arm unit lighter and durable but also with fewer stiffness variations. The rocker arm started as a 245kg welded part, with 16,5 m welded seams, which took very long to produce and was expensive. They ended up casting the part with 8% less weight, lower production costs and higher flexibility for customers in add-on modules. Images shared by Altair.
At a practical level, one should not forget that “designing” is very much dependent on the “human element”, which means that two engineers designing the same part will not always obtain the exact same “rendering” not to mention that, the complexity of the part – if not well handled, may lead to defects, low part performance, excessive weight, excessive time to market and even expensive operations of redesign and having to revisit process conditions.
“To meet today’s requirements of performance, weight reduction and especially costs, it is necessary to take advantage of new processes and design components for these processes require the combination of new software features, including:
- Parametric Geometry: provides the ability to perform geometry modifications and changes based on analysis and simulation.
- Structural and Motion or dynamic analysis to understand the working conditions of the analyzed part.
- Topology Optimization to improve the part performance and reduce weight based on the working conditions.
- Manufacturing simulation to predict the Mold filling and thermal analysis for different types of casting process such as investment casting or gravity sand casting considering the different types of AM molds too.
And most importantly, all these features should be linked to one another in a seamless way to be transparent for the user”, Martin Solina lays emphasis on.
The materials standpoint
One of the main concerns often raised by materials is the one of mechanical properties. Do we have satisfying results when assessing the tensile strength, hardness, surface roughness, and microstructure of the part?
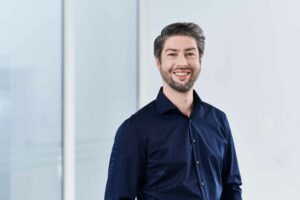
In a traditional sand casting process for instance, three materials/binding systems are often utilized and it’s easy to think that they can be directly transferred to AM production methods.
“When looking at sand casting the answer is a classic: it depends”, Christian Traeger brings a nuance. “Most of the materials used have been used in metal casting for centuries: sand and furanic resin. Other binder types, such as phenolic or inorganic binders are also capable with AM. Depending on the binder used, the system setup need to be adapted as well. Furanic direct binding requires the sand to be mixed with a promoter that reacts with the binder and glues the sand particles together. Both phenolic and inorganic binder work with unmixed sand. By irradiating the building platforms with temperature, the resins react and glue the sand particles together. Since unprinted sand is unmixed, it makes it a lot easier to recycle and reuse. In investment casting we see a great acceptance and growing market interest in the PMMA material set. The rapid production and flawless integration into existing process chains are the main benefits. The only way to optimize this material set further, is to further increase the surface quality.”
Moreover, research reveals that the production of casts by binder jetting requires several basic materials properties for the individual process steps. The particle material must be free flowing to fill the model form. The binder must have very low viscosity for metering and for the resulting molding material flow characteristics. Both properties are also a basis for processing of materials in machines within the binder jetting process. Therefore, the materials can be used in 3D printers without major modifications in their physical or chemical properties.
We then asked voxeljet’s Christian Traeger if parts produced with AM and a casting method possess the same mechanical properties as parts produced via casting as the only production method. He said they do.
“Reason for that is that, the casting process itself remains the exact same as it was before. By using typical foundry materials such as silica and special sands and complementary furanic, phenolic or inorganic binders, we only change the way molds, models and cores are built. Within the foundry, 3D printed parts can be integrated into existing process chains. Since the mechanical properties of castings depend mainly on the properties of the alloy used, additive manufacturing has no influence on these. Of course, there are some details that need to be kept in mind when designing to mold or the model such as cleaning of the printed parts. Also, the surface quality depends on the material used and can show differences compared to the materials used in conventional manufacturing, but when all these details are accounted for, and the metal is casted, the parts show the exact same mechanical properties as conventional manufactured cast parts.”
What about productivity and costs?
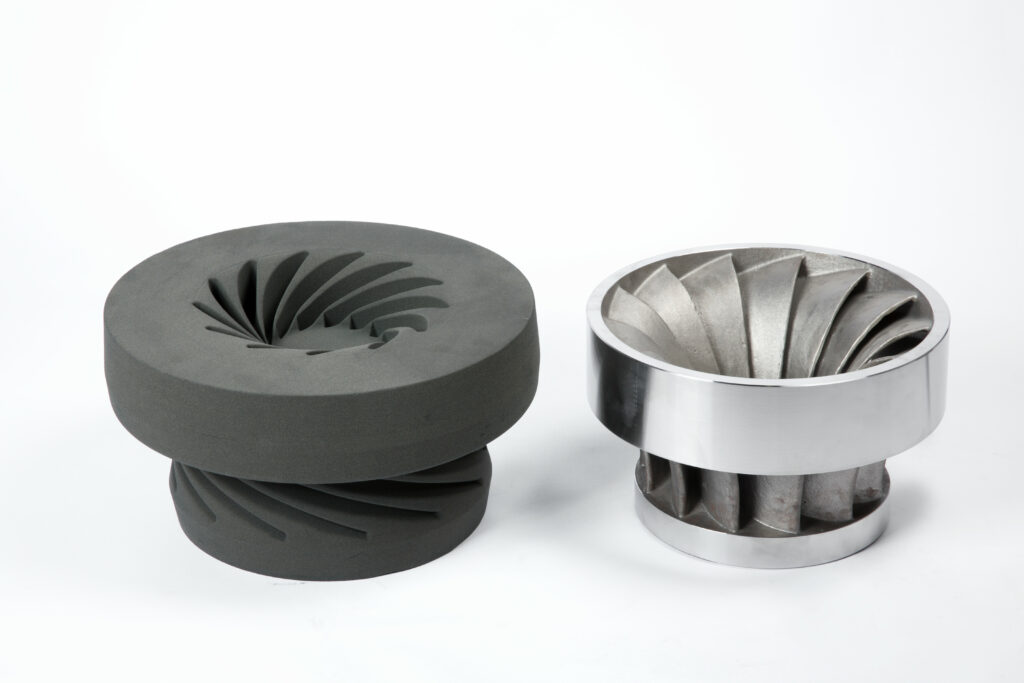
Calculation is in general easy when you compare production time with AM with production time of the same part achieved via a conventional manufacturing process: AM usually wins no matter what happens. What’s interesting here is to discover the steps that are removed in an AM process, but still required in a casting process.
Let’s say for instance that the production time is calculated as from when the parts’ producer receives the 3D CAD geometry from a customer. The casting process of a part with an average complexity might require two additional core boxes for pattern equipment. The operators would need 3 days to redesign a 3D model with all necessary draft angles and prepare the 3D pattern geometries. Two additional weeks will be necessary to move from 3D geometries to a ready pattern: this includes CNC machining for negatives, CNC machining for core boxes and copying epoxy models and making the gating system. Not to mention that extra time is necessary for the main production and forming.
AM as you may know does not need all these steps. For the same part, the operator will need a couple of hours to prepare a program to start producing the part. Most time is dedicated to the printing process here which might take up to 3 days – depending on the speed of the machine. Thereafter, the operator can spend a couple of hours on the various post-processing steps that need to be conducted.
Nevertheless, one advantage that remains worth mentioning is that in a casting process, in one mold there is more than one part, which means that in one casting process it is possible to produce 10 parts. This number is likely to vary – and may not always be reached – with a 3D printer. While casting remains an attractive process for series production, AM is a great fit for very complex parts and for productions where time is a limiting factor.
“AM works with digital CAD data and does not require any form of tooling. Conventional tooling can take up to 12 weeks to be produced and only then the casting process for this specific part can begin. Binder Jetting can create molds and models within hours or days, reducing the time needed to create e.g. a prototype by up to 75%. Binder Jetting is a quite easily scalable process technology, meaning that build volumes and productivity can be increased, making the technology not only suitable for prototype production but also for small to medium large batch sizes”, Christian Traeger comments.
However, when asked if the combination of AM & casting is the most cost-effective way to produce parts – when looking at other metal AM processes, he said:
“This depends on the material and the required batch size. For prototypes and small series, AM supported casting process is much more cost-effective than e.g., Direct Metal Laser Sintering. Reason for that are the printing materials as well as the casting alloys. 1 kg of aluminum costs around 6,50 EUR when casting. Special Steel alloys can cost up to 38 EUR. The same materials but for AM technologies can cost something between 78-133 EUR per kilogram.
When it comes to batch sizes, binder jetting molds, cores and models is cost effective for prototypes and small to medium batch sizes. Binder Jetting is on one of the most productive AM technologies around and can also be scaled quite easily in order to meet larger batch size needs. Also, it offers build volumes beyond the capabilities of any existing metal printers. While metal binder jetting is of course a technology on the rise, the build volumes still lack the volume that sand printers offer. To say Binder Jetting supported metal casting is the most cost-effective way to produce metal parts is a strong statement and a little far-fetched. In certain scenarios, as described above, the cost effectiveness of Binder Jetting is very hard to beat, but those scenarios have to be identified and carefully evaluated to find the best fit and solution.”
Concluding thoughts
The casting industry may not be known for its speed, but the economics and opportunities are just too good to be left apart. This industry is responsible for parts that fuel everyday life, the economy and many other industries, yet when we look at manufacturing, the sector remains one of the biggest losers with production declines of around 30% due to crisis and other ongoing transformation across industries. Price and production time make AM an appealing and competitive production candidate to address part of this problem, especially when we look at the production of small parts and for small quantity (up to 5 parts).
Furthermore, as mentioned by voxeljet, despite the high cost of AM equipment, one notes that machine manufacturers continue to invest time and resources to develop a portfolio that can easily enable industries to scale their production for larger batch size needs. Lastly, beyond these investments, it’s crucial to keep in mind that when looking at this hybrid manufacturing approach that involves AM & Casting, sometimes, the right design software and utilization of this software can make a whole difference, not only in casting the “un-castable”, but also in delivering the ideal benefits in terms of time, costs and performance.
This exclusive dossier has first been published in the July/August edition of 3D ADEPT Mag. All resources and contributions can be found in page 13.
Remember, you can post your job opportunities in the AM Industry on 3D ADEPT Media or look for a job via our job board. Make sure to follow us on our social networks and subscribe to our weekly newsletter : Facebook, Twitter, LinkedIn & Instagram ! If you want to be featured in the next issue of our digital magazine or if you hear a story that needs to be heard, make sure you send it to contact@3dadept.com