Sometimes, our beliefs are so strong that they impact the choices we make on a daily basis. Depending on situations, they hide a common thread that results from various holistic experiences that we went through.
In a world where advanced technologies can drastically disrupt several industrial markets, Aaron Bent strongly believes that “an advanced material remains the enabler for a class of new products”. Aaron Bent is the CEO of 6K, formerly known as Amastan Technologies. He combines 25 years of experience in managing roles across markets as diverse as defense & aerospace, automotive and solar, to name a few of them. These experiences have shown him the ability of an advanced material to change the way products are made. 6K seems to be one of these companies that could create a real impact on several markets through advanced materials, and Aaron Bent will tell us why in this Opinion of the Week series.
6K: the key milestones
Bent was only employee number three when he joined 6K six years ago. Today the company has just under 100 employees. Be it as Amastan Technologies or 6K, its core business remains the same: the development, commercialization, and implementation of plasma technologies for the production and processing of nanomaterials, as well as homogenous and uniform nano powders.
However, the rebranding into 6K was necessary to reflect the uniqueness of its UniMelt process, seen through the company’s logo on the one hand, on the other hand, the vertical industries it targets.
“When we rebranded from Amastan to 6K, we wanted to ensure that the name and our brand identity really spoke to what we do, our technology and connecting that to the products we make. During our process 6K quickly rose to the top because it represents the operation of our UniMelt microwave plasma which runs at 6K (5778K to be more specific) degrees and, coincidently, is the temperature of the surface of the sun,” said Dr. Aaron Bent.
With the goal of synthesizing materials for various markets, the company quickly realized that their materials could serve a wide range of fields in the metallurgy industry including one of its fast growing segments: Additive Manufacturing.

They strive to demonstrate the platform’s capability to manufacture advanced materials for energy storage, phosphors for LED lighting, semiconductor materials, defense IR-transparent materials, and metal powders for AM.
“As we started to vet out which industry and applications we could have a profound effect upon, additive manufacturing powders was an obvious choice given the UniMelt microwave plasma process’ unique capabilities. Being able to offer the AM industry more choice of material opens up the application opportunities for our customers, while exceeding the quality performance of materials made AM powders a natural choice. Add to it, that we do it in a sustainable way compared to gas or plasma atomization, we began commercial operations for additive manufacturing,” explained the CEO.
However, the last five years have demonstrated the necessity to create a brand for the AM industry as the company’s technology could not only develop the most widely used materials such as In 718 and Ti 64 but could also customize new materials for this market in compliance with sustainability and quality requirements. That brand is 6K Additive.
What makes this production process outstanding?
“What separates the UniMelt process from others is the uniformity of the plasma and size of the production zone. The use of microwaves enables a three inch uniform plasma so that each particle that goes through the plasma sees exactly the same temperature, removing the possibilities of satellites and inconsistencies forming during production. We can also run the plasma as long as eight feet long allowing better control in the process and improving material quality compared to gas or plasma atomization,” said 6K Additive’s spokesperson.
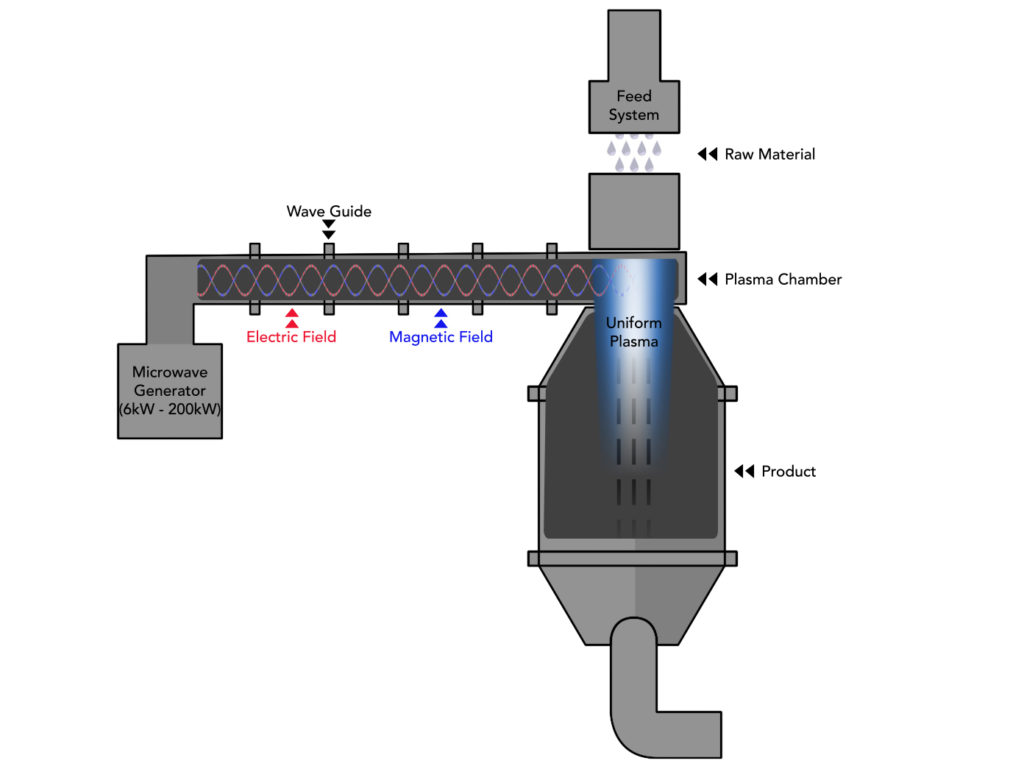
While the system must not be confused with Gas Atomization (GA) or Plasma Atomization (PA), it should be noted that it can process materials at 6000 degrees maximum.
The technology capabilities allow for the design of a wide range of materials as any metal or alloy can become a feedstock for 6K’s premium powders. Rather than leveraging wire or ingot as feedstock, UniMelt® utilizes certified machining scrap as feedstock, a technique that enables AM powders to include any material that is usually produced using subtractive technologies such as CNC.
“The ability to use a multitude of feedstocks, like angular CNC turnings, used powder or even AM supports, ensures certified chemistry because we start with certified chemistry to begin with in the form of scrap or used powder, etc. Our vision is a zero-loss production capability where a super user from aerospace or medical as an example, can take their certified scrap material from subtractive manufacturing and turn it into AM premium powder, helping to drive the circular economy.”
Furthermore, despite the fact that AM is often said to be a sustainable technology, it should be noted that the production of AM powders does not reflect that sustainability.
“Until UniMelt, AM powder production has been very inefficient. GA and PA produce anywhere from 20% to 30% of the desired particle size distribution (PSD) for LPBF. The remaining 70% becomes scrap and often is sent to landfill. Because we control the size of the input feedstock with the UniMelt system, we get near 100% of the desired PSD, so all of the material in the case of LBPF as an example becomes usable powder. Add to it that UniMelt plasma uses a third of the gas during production in comparison to GA or PA, UniMelt is a much more sustainable production process with respect to its carbon footprint”, stated Dr. Bent.
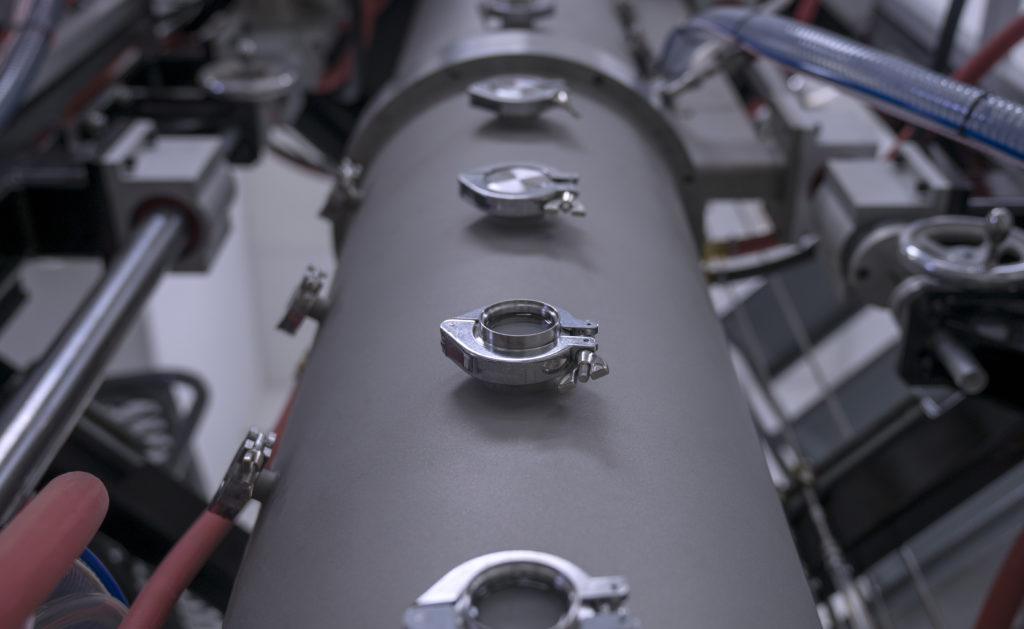
Challenges and next step for 6K Additive
6K seems to provide the market with a unique process that can benefit industries beyond the AM sector: one that develops powders from sustainable sources. Powders that can be used by various technologies including powder bed, EBM, Binder Jet, direct energy deposition as well as cold spray, and PM processes like MIM and HIP.
Its biggest strength today, which is the ability to produce the most-widely used & exotic materials, might also be its weakness tomorrow. The question is: are all these materials going to meet a real/big demand on the market?
Bent told us that for every material they have to produce, they continue to ask themselves: “is this a material customers are looking to put into production?” If the answer is no, this material is likely to be given second place in the commercialization process.
As the company is moving forward, it finds itself impacted by the Covid-19 pandemic. After debuting on the European market at Formnext 2019, the materials producer envisioned to set up a European office in 2020.
“Certainly, these have been trying times during the Covid-19 crisis and we are not immune to its impact. Our plans have slowed slightly, but we are still on target to create an EU office in Q4 this year. This will be followed by placing a UniMelt system in the EU either at a dedicated 6K production facility or at large AM production super user’s site who requires 100 tons of a specific material where the UniMelt would be feeding their production needs,” concluded the CEO.
Remember, you can post free of charge job opportunities in the AM Industry on 3D ADEPT Media or look for a job via our job board. Make sure to follow us on our social networks and subscribe to our weekly newsletter. : Facebook, Twitter, LinkedIn & Instagram ! If you want to be featured in the next issue of our digital magazine or if you hear a story that needs to be heard, make sure to send it to contact@3dadept.com.